टर्निंगद्वारा निर्माण केलेल्या यंत्रभागांचे लहान किंवा मोठ्या प्रमाणात उत्पादन करण्यासाठी सी.एन.सी. लेथचा वापर केला जातो. काही मूलभूत उपसाधनांनी सज्ज असलेला दोन अक्षांचा सी.एन.सी. लेथ हे विविध प्रकारचे उत्पादन घेण्याचे एक अष्टपैलू साधन आहे. यंत्रभागांच्या निर्मितीमध्ये कास्टिंग आणि फोर्जिंगनंतर सामान्यतः पुढची पायरी टर्निंग ही असते. बारच्या आकाराची कार्यवस्तू चकमध्ये पकडून दोन सेंटर्समध्ये टर्निंग करण्याच्या कामात स्टँडर्ड सी.एन.सी. लेथचा वापर करता येतो.
सी.एन.सी.मधील कंट्रोलमुळे प्रोग्रॅम करण्याची सोय प्राप्त होते आणि आठ-दहा दिवसांच्या मूलभूत प्रशिक्षणानंतर कोणताही टर्नर काही साधे-सोपे यंत्रभाग यशस्वीपणे बनवू शकतो. तथापि, विविध प्रकारच्या यंत्रभागांचे यशस्वीपणे मशिनिंग करण्यासाठी प्रोग्रॅमिंग, कार्यवस्तू कशी पकडावी आणि कोणती टूल्स केव्हा आणि कशी वापरावी (ॲप्लिकेशन इंजिनिअरिंग) या विषयातील सखोल अभियांत्रिकी ज्ञान असणे आवश्यक आहे. सामान्यत: सी.एन.सी. लेथ मशिन उत्पादकाजवळ हे ज्ञान असते आणि ते वापरूनच तो कोणताही विशिष्ट यंत्रभाग मोठ्या प्रमाणात अचूकपणे बनवण्यासाठी मशिनमध्ये हवी तशी टूल्सची सोय करून देत असतो. अभियांत्रिकी कौशल्य अनेक वर्षांच्या मेहनतीने आणि अनुभवातून प्राप्त होत असते. त्यामुळे विशिष्ट यंत्रभाग बनवण्यासाठी तयार केलेली मशिन्स, त्या मशिन्सकडून काय कामगिरी अपेक्षित आहे, त्यानुसार स्वस्त किंवा महाग असू शकतात. बरेचदा मशिन उत्पादकाला काही सब ॲसेम्ब्ली विशिष्ट बाह्य स्रोतांकडून घ्याव्या लागतात.
आता आपण स्टँडर्ड दोन अक्षीय सी.एन.सी. लेथमध्ये साधारणपणे काय सोयी उपलब्ध असतात, ते पाहूया.
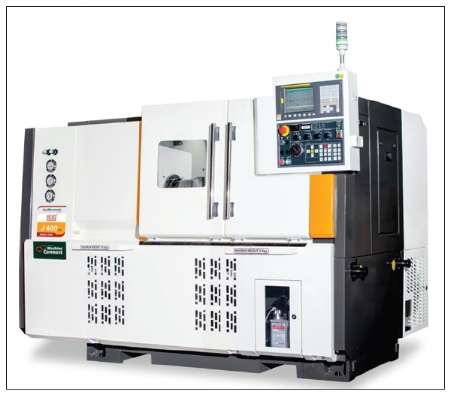
मंचकावर X आणि Z या दोन अक्षांच्या सरकणीची (स्लाईड) व्यवस्था असते. याला एका विशेष स्पिंडल मोटरने (एकाहून अधिक व्ही-बेल्ट्सद्वारे) चाल दिली जाते. स्पिंडलची गती सी.एन.सी. कंट्रोलरद्वारा नियंत्रित केली जाते. स्पिंडलमध्ये एक 3 जबड्यांचा पॉवर चक असतो. पाट्यावर एक दोन अक्षीय सरकण (स्लाईड) व्यवस्था असते. त्यातील X सरकणीवर टूल टरेट बसवलेले असते. या टरेटमध्ये सामान्यतः 8 अथवा 12 टूल्स असतात. सरकणींना बॉल स्क्रू आणि नट यंत्रणेच्या साहाय्याने सर्व्हो मोटर्सतर्फे चाल देऊन बॉक्स प्रकारच्या अथवा LM प्रकारच्या सरक मार्गावर सरकवले जाते. कार्यवस्तूंना आधार देण्यासाठी एक हायड्रॉलिक शक्तीने चालणारा टेलस्टॉक दिलेला असतो. हायड्रॉलिक पॉवर युनिट एका रोटरी सिलिंडरमार्फत चक, टेलस्टॉक क्विल आणि (डिझाईनमध्ये असल्यास) कधी कधी टरेटलाही चालना देते. मशिन चालणाऱ्या कंट्रोलरला समजणारी एक सांकेतिक भाषा वापरून मशिनचा प्रोग्रॅम बनवावा लागतो. सामान्यतः मशिन चालवण्यासाठी पुरेशा क्षमतेचा स्थिर विद्युत पुरवठा आवश्यक असतो. यामध्ये कंटूर टर्निंग, ड्रिलिंग, थ्रेड कटिंग, बोअरिंग वगैरे कामे करता येतात. क्वचित रीमिंग, बर्निशिंग आणि नर्लिंग अशी कामेही योग्य टूल्स वापरून करणे शक्य असते. एका शीतक (कुलंट) युनिटमधून पाण्यात एकजीव होऊ शकणाऱ्या तेलापासून बनवलेल्या शीतकाचा पुरवठा केला जातो आणि कचरा गोळा करण्यासाठी एक चिप ट्रे दिलेला असतो. शीतक आणि कचरा यांच्यापासून ऑपरेटरचे संरक्षण करण्यासाठी एक पत्र्याचे बंदिस्त झाकण दिलेले असते. संवेदनशील इलेक्ट्रॉनिक घटकांचे आयुष्य वाढण्यासाठी तापमान नियंत्रित करणे गरजेचे असते. त्यामुळे इलेक्ट्रिकल कॅबिनेटसाठी एक कूलर दिलेला असतो.
विविध आकाराचे यंत्रभाग बनवण्यासाठी स्वतःचे विशेष कौशल्य वापरणाऱ्या विविध ग्राहकांच्या गरजा पूर्ण करण्याच्या उद्देशाने वर वर्णन केलेले मशिन वेगवेगळ्या क्षमतेत आणि आकारात उपलब्ध असते.
वाहन उद्योगामध्ये यंत्रभागांची खूपच मोठ्या संख्येत आवश्यकता असते. त्यामुळे बरेच ग्राहक त्यांच्या यंत्रभागांसाठी टूल्सची विशिष्ट मांडणी असलेल्या मशिन्सची मागणी करतात. ज्या यंत्रभागाची मोजमापे अतिशय अचूक असावी लागतात, अशा यंत्रभागांवरील एक किंवा दोन महत्त्वाच्या ऑपरेशन्ससाठी अशा मशिनची सहसा मागणी केली जाते. यातील कामाचे मूल्यांकन संख्याशास्त्राच्या (स्टॅटिस्टिक्सच्या) साहाय्याने केले जाते.(दहा लाखांपैकी अतिशय थोडे यंत्रभाग नापसंत झाले तरच चालते). कच्चा यंत्रभाग आणि मशिनमधून बाहेर पडणारा तयार यंत्रभाग, हे यंत्रचित्रांद्वारे पूर्वीपासून निश्चित केलेले असल्यामुळे कामात कोणतीही संदिग्धता नसते. मशिन उत्पादकाने एक यंत्रभाग बनायला लागणारा वेळ, किती दिवसात मशिन मिळू शकेल आणि किंमत या बाबींची हमी द्यायची असते. या प्रकारच्या कामात अभियांत्रिकी क्षेत्रातला डिझाइनिंग, ॲप्लिकेशन इंजिनिअरिंग, चाचण्या आणि अंमलबजावणी यांचा पुरेसा अनुभव लागतो. या सर्व कारणांमुळे विविक्षित कामासाठी खास बनवलेले मशिन मिळायला लागणारा वेळ अधिक असतो आणि त्यातील कामानुसार त्याची किंमतही पुष्कळ जास्त असते.
आता आपण विशिष्ट कामासाठी बनवलेल्या मशिनमधील विशेष उपसाधनांची माहिती घेऊ या. (यातील काही पर्याय स्टँडर्ड मशिनबरोबर देता येणे शक्य आहे.)
कार्यवस्तू पकड
संतुलित (सेंट्रिफ्युगली कॉम्पेन्सेटेड) कार्यवस्तू पकडण्यासाठी 3 जबड्यांचा पॉवर चक हे एक मान्यताप्राप्त आणि अष्टपैलू साधन आहे. तरीही 3 जबड्यांचा चक वापरून सर्व यंत्रभाग पकडता येतीलच असे नाही. मशिनमध्ये भरड कर्तन (रफिंग) करताना अधिक शक्ती लागते आणि फिनिशिंगच्या वेळी कर्तनाची (कटिंगची) गती जास्त असते. दोन्ही कामात कार्यवस्तूमध्ये कोणताही वेडेवाकडेपणा न होता, ती घट्ट आणि सुरक्षितपणे पकडणे अतिशय महत्त्वाचे आहे. मशिनची गती जास्त असली की, कार्यवस्तूवर केंद्रोत्सारी बल कार्यान्वित होते. चकचे पकडण्याचे स्थिर बल टिकवून ठेवण्यासाठी जबड्यांचा आकार आणि मशिनची गती हे दोन घटक महत्त्वाचे असतात. त्यामुळे काही चक्सच्या डिझाइनमध्ये (चित्र क्र. 3) केंद्रोत्सारी बल संतुलित करण्याची योजना केलेली असते. चकमधून कार्यवस्तू निसटल्यास मशिनचे गंभीर नुकसान होऊ शकते. कार्यवस्तू पकडण्याकडे जर पुरेसे लक्ष दिले नसले, तर कधी कधी काम करणाऱ्या ऑपरेटरलाही इजा होण्याची शक्यता असते. सर्व्हिस विभागाच्या माणसांना कारखान्यांमध्ये बोलावण्याचे हे एक प्रमुख कारण असते. या बाबतीत केलेली तडजोड सुरक्षेच्या आणि उत्पादकतेच्या दृष्टीने महागात पडू शकते. सर्वसामान्यपणे या कामात मशिन उत्पादक अथवा कार्यवस्तू पकडण्याची उपकरणे बनवणारे विशेष तज्ज्ञ यांची मदत घेतली जाते. ही उपकरणे ग्राहकाच्या मागणीनुसार निरनिराळी बनवावी लागत असल्यामुळे ती महाग असतात आणि उपलब्ध होण्यासाठी बराच वेळही लागतो. त्यामुळे काही उपकरणे स्पेअर ठेवावी लागतात. क्वचित काही प्रकारचे कॉलेट्स आणि मँड्रेल्स लगेच उपलब्ध होऊ शकतात.
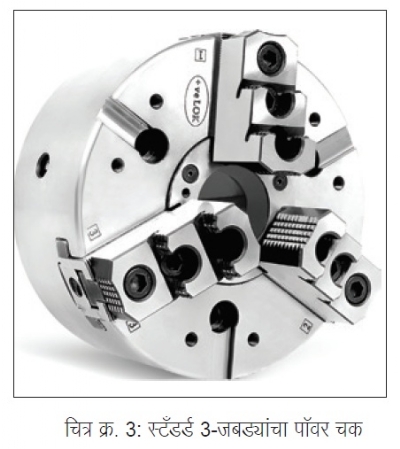
युनिव्हर्सल बॉल लॉक चक
1. यूबीएल चक (यूबीएल चकची संरचना) कॉम्पेन्सेटिंग प्रकार सेटरायझिंग प्रकार
ओतकाम (कास्टिंग) किंवा घडाई (फोर्जिंग) केलेल्या कार्यवस्तूंना त्यांच्यावर केल्या जाणाऱ्या पहिल्या ऑपरेशनसाठी लेथमध्ये पकडण्यासाठी याचा प्रामुख्याने उपयोग केला जातो. यात 15° पर्यंतचा उतार असलेली ओतीव कार्यवस्तू पकडता येते आणि तिला तिच्या बटिंग पृष्ठभागापर्यंत मागेही खेचता येते. फेसिंग केलेल्या किंवा सेंटर केलेल्या कार्यवस्तूंवर काम करण्यासाठी एक्सेन्ट्रिक कॉम्पेन्सेटिंग (यात कार्यवस्तूचे केंद्र व चकचे केंद्र वेगळी असतात आणि केंद्रोत्सारी बलाला संतुलित केलेले असते.) प्रकारचा चक वापरता येतो. सामान्यतः असे चक महाग असतात आणि ते प्रमाणाने मोठ्या उत्पादनासाठी वापरले जातात.
कॉलेट्स आणि मँड्रेल्स
विविध प्रकारच्या कामात उपयुक्त पडावे या हेतूने हे चक्स निरनिराळ्या शैली आणि डिझाइन्समध्ये बनवलेले असतात. जिथे चौकोनी बटिंग पृष्ठभाग उपलब्ध असतो, तेथे पुल प्रकारचे कॉलेटस् आणि मँड्रेल्स वापरले जातात. अन्य जागी डेड लेंग्थ प्रकार वापरला जातो. अगदी 30 सेकंदात कॉलेटस् बदलता येईल असे तात्काळ बदलता येणारे (क्विक चेंज) प्रकारही असतात.
दोन जबड्यांचा/चार जबड्यांचा चक
हे चक्स 3 जबड्यांच्या वेज बार पॉवर चकसारखेच असतात, परंतु त्यांतील जबड्यांमध्ये विशेष बदल करून घ्यावे लागतात. दोन जबड्यांचे चक साधारणपणे वेड्यावाकड्या आकाराच्या कार्यवस्तू पकडण्यासाठी वापरले जातात आणि त्यांच्या जबड्यांचे डिझाइन विशेष प्रकारे केलेले असते. ज्या कार्यवस्तूंची बाहेरची बाजू अतिशय पातळ प्रतलातून बनलेली असते, त्यांना पकडताना त्यात वेडेवाकडेपणा येऊ नये, म्हणून त्यांच्यावर केल्या जाणाऱ्या नंतरच्या ऑपरेशन्ससाठी 4 जबड्यांचे पॉवर चक प्रामुख्याने वापरले जातात. यात एक 2+2 जबड्यांचा प्रकारसुद्धा असतो. यात जबड्यांची एक जोडी पॉवरवर चालणारी असते, तर दुसरी जोडी स्प्रिंग अथवा पॉवरवर चालणारी असते व त्यात दुहेरी सिलिंडर वापरला जातो. वेड्यावाकड्या आकाराच्या कार्यवस्तू अगदी पहिल्या ऑपरेशनमध्ये पकडण्यासाठीसुद्धा यांचा उपयोग करता येतो.
पिन आर्बर/पुल बॅक चक
याचा वापर सर्वसाधारणपणे दुसऱ्या ऑपरेशनमध्ये कार्यवस्तू समकेंद्री पकडण्यासाठी आणि बटिंग पृष्ठभागावर मागे खेचण्यासाठी केला जातो. 3 जबड्यांच्या चकमधून मिळते त्यापेक्षा चांगल्या दर्जाची समांतरता आणि समकेंद्रीयता यातून प्राप्त होते. 3 जबड्यांच्या चकमध्ये जबडे वर उचलले जाण्याकडे कल असतो, ज्यामुळे बटिंग पृष्ठभागाला समांतर यंत्रण करणे अवघड जाते.
डायफ्राम अथवा पिच लाईन चक
यांसारख्या दाते असणाऱ्या कार्यवस्तू पकडून त्यांच्यामध्ये दात्यांना समकेंद्री फिनिशिंग ऑपरेशन करण्यासाठी हा चक सामान्यतः वापरला जातो. यांचा उपयोग अनेकदा टर्निंगच्या कठीण ॲप्लिकेशन्समध्ये केला जातो.
फींगर चक
जेव्हा कार्यवस्तू अतिशय नाजूक असते आणि चकचे त्रिज्य (रेडियल) बल पडल्यावर ती वेडीवाकडी होण्याचे भय असते, तेव्हा याचा उपयोग केला जातो. जसे काम असेल त्यानुसार याचे डिझाइन करावे लागते.
वरील प्रकारांचे मिश्रण
काही विशेष ॲप्लिकेशन्समध्ये वरील पद्धतींचे मिश्रण वापरले जाते. उदाहरणार्थ, डायफ्राम चकबरोबर फिंगर (फेस) क्लँपिंग, कॉलेटस्बरोबर एक्सेन्ट्रिक कॉम्पेन्सेटिंग यूबीएल चक इ.
इंडेक्सिंग चक
यूजे क्रॉस, ट्रायपॉड्स, फिटिंग्ज वगैरे तिरक्या अक्षांच्या कार्यवस्तूंचे मशिनिंग करण्यासाठी लागणाऱ्या विशेष ॲप्लिकेशन्सची भरपूर डिझाइन्स उपलब्ध आहेत. इंडेक्सिंग चकमध्ये मॅन्युअल, सेमीऑटोमॅटिक आणि पूर्णपणे ऑटोमॅटिक असे प्रकार उपलब्ध आहेत.
मॅग्नेटिक चक
मॅन्युअल ऑपरेशन असलेले छोट्या प्रकारचे आणि विजेवर चालणारे मोठ्या प्रकारचे चुंबकीय (मॅग्नेटिक) चक उपलब्ध असतात. यांचा उपयोग सामान्यतः बेअरिंग रिंगच्या कठिण टर्निंग कामासाठी केला जातो
अन्य वैशिष्ट्ये
अक्षांना जोडलेल्या इलेक्ट्रॉनिक मापन पट्ट्या
लेथवर होणाऱ्या हालचालींचे अंतर मोजण्यासाठी बहुतेक लेथमध्ये सामान्यतः मोटरवर स्थापित एनकोडर दिलेला असतो. मापन करण्यासाठी वापरलेले बॉल स्क्रू पुरेसे काटेकोर आहेत, असे येथे गृहित धरले जाते. बॉल स्क्रूचे एक परिभ्रमण साधारण 10 लाख पल्सेस समान असते. त्याला इलेक्ट्रॉनिक पद्धतीने गुणले जाते आणि बॉल स्क्रूच्या पिचला पल्सेसच्या संख्येने भागले असता हालचालीचे लघुत्तम माप (लीस्ट काउंट) मिळते. सामान्यतः कमीत कमी 1 मायक्रॉन इतके माप अचूकपणे मोजता येणे अपेक्षित असते. हे मापन बॉल स्क्रूच्या परिपूर्णतेवर, अचूकतेवर अवलंबून असते. परंतु बॉल स्क्रूची झीज होऊ शकते, त्यात धूळ जाऊ शकते, वेगवेगळ्या तापमानात त्याच्या आकारात सूक्ष्म बदल होतात आणि या सर्वाचा परिणाम मापनाच्या दर्जावर होतो. यातील त्रुटी कमी करण्यासाठी आणि मापनाची विेशासार्हता वाढवण्यासाठी इलेक्ट्रॉनिक पट्ट्या वापरल्या जातात. या पट्ट्यांचे डिझाइन अत्याधुनिक असते आणि त्यांची उभारणी करताना काळजी घेणे आवश्यक असते. त्यात धूळ जाऊ नये याची खबरदारी घेणेही महत्त्वाचे असते. व्यवहारात विविध प्रकारच्या आधुनिक पट्ट्या वापरल्या जातात आणि त्यांचा आकार आणि अचूकता यांच्यानुसार मशिनची किंमत काही लाखांनी वाढू शकते.
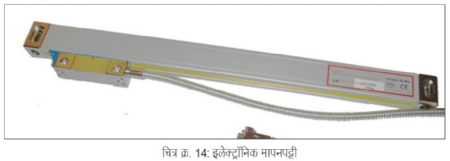
सीट चेक
जेव्हा आधी मशिनिंग केलेल्या पृष्ठभागाबरोबर कार्यवस्तूची समांतरता ठेवणे आवश्यक असते, तेव्हा क्लॅम्पिंगच्या नंतर आणि मशिनिंग सुरू करायच्या आधी बटिंग पृष्ठभागाचा संदर्भ घेणे महत्त्वाचे असते. या वैशिष्ट्यामुळे स्क्रॅपची निर्मिती टाळली जाते आणि ऑपरेटरची जबाबदारी कमी होते. हा संदर्भ बॅक प्रेशर मोजून घेतला जातो. कार्यवस्तूच्या बटिंगमुळे एअर व्हेन्टस् बंद होतात. सगळीकडील बॅकप्रेशर एकसारखे असले की, कार्यवस्तूची समांतरता सुनिश्चित होते. यासाठी चकिंग सिलिंडरच्या टोकाला एक खास रोटरी जॉइंट बसवावा लागतो तसेच, या वैशिष्ट्याचा उपयोग करण्यासाठी कार्यवस्तू पकडण्याचे वेगळे डिझाइन करावे लागते. ज्या मशिनमध्ये स्वयंचलितपणे गँट्री लोडिंग केले जाते, त्यात अपघात टाळण्यासाठी हे वैशिष्ट्य असणे अनिवार्य आहे.
टरेटचे प्रकार
उत्पादकता वाढवायची असेल, तर निष्क्रिय वेळ कमी करायला हवा. टूल इंडेक्सिंग हे वेळखाऊ असते, त्यामुळे टरेट इंडेक्सिंगसाठी सर्व्हो ड्राइव्ह वापरून वेळ वाचवण्याचा प्रयत्न केला जातो. त्यामुळे सध्या सर्व्हो टरेट्सची चलती आहे. पारंपरिक इलेक्ट्रो-मेकॅनिकल टरेट्सपेक्षा हे अधिक विेशासार्ह असतात, कारण यात झीज होणारे यंत्रभाग कमी असतात.
उच्च दाबाचे शीतक
स्टँडर्ड शीतक पंप्स हे कमी दाबाचे पंप्स असतात. (अधिकतम दाब - साधारण 1 बार). कार्बाईड इन्सर्ट वापरून करण्यात येणाऱ्या ड्रिलिंग ॲप्लिकेशनमध्ये कचरा बाहेर काढण्यासाठी उच्च दाबाचे शीतक (5~20 बार) आवश्यक असते. ज्यात गँट्री किंवा रोबोद्वारा लोडिंग केले जाते, अशा काही विशिष्ट ॲप्लिकेशन्समध्ये ऑपरेशनची विेशासार्हता वाढवण्यासाठी कार्यवस्तूमधून कचऱ्याचे निस्सारण करावे लागते. त्यासाठी 130~200 बार दाबही आवश्यक असतो.
स्पिंडलमधून शीतक
जेथे छिद्र पाडतानाच फिनिशिंगही केले जाते, अशा ड्रिलिंगच्या वेळी कार्यवस्तूच्या पकड साधनात (उदाहरणार्थ, कॉलेटस्) कचरा प्रवेश करण्याची शक्यता असते. अशा कामाच्यावेळी स्पिंडलमधून शीतक पोहोचवले जाते. येथे सिलिंडरच्या टोकावर असलेल्या रोटरी जॉइंटचे नुकसान टाळण्यासाठी शीतक फिल्टर करणे आवश्यक असते.
शीतक चिलर्स
जेव्हा सामान्य वातावरणात मशिन्स वापरली जातात, तेव्हा दिवस-रात्रीच्या तापमानातील फरकामुळे औष्णिक त्रुटी निर्माण होतात. या त्रुटी कमी करण्यासाठी शीतकाचे तापमान +/-10 मध्ये स्थिर ठेवले जाते, ज्यामुळे कामामध्ये सातत्य येते.
चिप कन्व्हेअर्स
या कन्व्हेअर्सचा वापर करून मशिन्सद्वारे निर्माण होणारा कचरा सतत एका डब्यामध्ये टाकला जातो. वेगवेगळ्या प्रकारच्या चिप्स आणि पदार्थांसाठी वेगवगेळ्या प्रकारचे कन्व्हेअर्स उपलब्ध असतात. उदाहरणार्थ, स्लॅट (स्टील बेल्ट), स्क्रेपर, ड्रम फिल्टरसहित स्क्रेपर, स्लॅट आणि स्क्रेपरचे मिश्रण, स्क्रू/कॉइल आणि मॅग्नेटिक असे विविध प्रकार असतात.
स्वयंचलित दरवाजा
ऑपरेटरच्या श्रमाची बचत व्हावी आणि एकाहून अधिक मशिनवर काम करणे शक्य व्हावे, यासाठी स्वयंचलित दरवाजांचा उपयोग केला जातो. हे साधारणतः न्युमॅटिक सिलिंडर्सद्वारा चालवले जातात. मशिनिंगच्या प्रत्येक आवर्तनाच्या सुरुवातीला दरवाजा आपोआप बंद होतो आणि आवर्तन समाप्त झाले की, तो आपोआप उघडतो.
कार्यवस्तू अनलोड करण्याची उपकरणे
कार्यक्षम प्रणालीमध्ये (टोयोटा उत्पादन प्रणाली) एका ऑपरेटरने आवर्तन काळानुसार एकाहून अधिक मशिन्स हाताळायची असतात. अशा वेळी कार्यवस्तू अनलोडिंग करणारे उपकरण तर उपयुक्त असतेच, त्याचबरोबर कमीत कमी रुंदीच्या मशिन्सची मागणी केली जाते. या सुविधेमुळे ऑपरेटरने प्रत्येक मशिनवर व्यतीत केलेला वेळ कमी होतो आणि तो बरीच मशिन्स एकावेळी हाताळू शकतो. उदाहरणार्थ, या प्रणालीमध्ये 90 सेकंदांचा प्रक्रिया आवर्तन काळ असणारी सहा मशिन्स एक ऑपरेटर सामान्यतः हाताळतो.
ब्लॉक टूलिंग प्रणाली
मशिन्सचा निष्क्रिय वेळ कमी करण्यासाठी (इन्सर्टस् बदलणे आणि ऑफसेटस् घेणे) ब्लॉक टूलिंग प्रणाली वापरली जाते. टूलच्या वेगवेगळ्या उत्पादकांनी स्वतःच्या मालकी हक्काच्या आणि पेटंट घेतलेल्या प्रणाली विकसित केल्या आहेत. (त्यातील काही प्रणाली प्रमाणित झालेल्या आहेत, उदाहरणार्थ, व्हीडीआय टूलिंग, कॅप्टो, एच.एस.के. वगैरे) ही टूल्स आधीपासून सेट करता येतात आणि त्यांना जलदपणे बदलताना ऑफसेट घ्यायची गरज पडत नाही.
टूल टच प्रोब
टूलची झीज झाल्यामुळे किंवा इन्सर्टस् बदलल्यानंतर ऑफसेटमध्ये काही बदल करावे लागतात. त्यासाठी जलद ऑफसेट घेणे या प्रोबमुळे शक्य होते. ज्या प्रकारचा प्रोब असेल, त्याप्रमाणे हाताने किंवा स्वयंचलितपणे त्याला त्याच्या पार्किंग केलेल्या स्थानावरून कार्यन्वित करता येते. ‘मारपॉस’ अथवा ‘रेनिशॉ’ मेकचे प्रोब प्रचलित आहेत. या वैशिष्ट्यामुळे कार्यक्षमतेत वाढ होते.
स्टेडी रेस्ट
दोन केंद्राच्यामध्ये पकडून मशिनिंग करताना लांब आणि निमुळत्या कार्यवस्तूंना अतिरिक्त आधाराची गरज असते. लांब कार्यवस्तूंच्या टोकावर काम करतानाही आधाराची गरज असतेच. हा आधार देण्यासाठी सामान्यतः तीन बिंदूंच्या आधाराची वर्क स्टेडी उपयोगात आणली जाते. हायड्रॉलिक प्रणालीवर चालणारी स्वकेंद्री (सेल्फ सेंटरिंग) 3 बिंदू स्टेडी बहुप्रचलित आहे. क्वचित हाताने चालवण्याची स्टेडीसुद्धा वापरली जातात. काही कामामध्ये स्टेडीने टूल्सबरोबर पुढे किंवा त्याच्या पाठोपाठ चालणे आवश्यक असते. अशा परिस्थितीत मशिनवर विशेष व्यवस्था केली जाते.
विशेष टूलिंग
जेव्हा एकाच वस्तूचे उत्पादन प्रचंड प्रमाणात करायचे असते आणि एकंदर ऑपरेशन्सची संख्या कमी करायची असते, तेव्हा विशेष टूलिंग आवश्यक असते. फॉर्म टूल्स, अनेक धारा असणारी टूल्स (टूल्सची संख्या कमी करण्यासाठी), बॅक बोअरिंग टूल्स, लांब बोअर्ससाठी आवाज कमी करणारे (डॅम्प केलेले) बोअरिंग बार ही काही उदाहरणे आहेत.
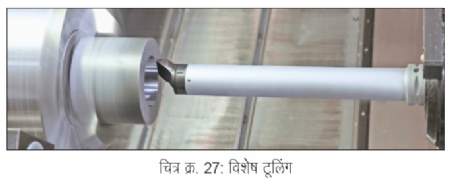
सब स्पिंडल्स
यात प्रमुख स्पिंडलबरोबर सिंक्रोनाइझ केलेल्या एका हलवता येण्याजोग्या अतिरिक्त स्पिंडलची योजना केलेली असते. यामुळे कार्यवस्तू पहिल्या ऑपरेशननंतर मुख्य स्पिंडलकडून अतिरिक्त स्पिंडलला सुपूर्द केली जाते आणि दुसरे ऑपरेशन ऑपरेटरच्या हस्तक्षेपाशिवाय केले जाऊ शकते. अर्थातच वेळेची बचत होते.
लेथवरचे मिलिंग
उच्च दर्जाचे नियंत्रण ठेऊन आणि चलित हत्यार (ड्रिव्हन टूल) टरेटचा वापर करून टर्निंग आणि मिलिंग एकाच मशिनवर एकत्र करता येते. अशा मशिनच्या रचनेत एकच स्पिंडल अथवा सब-स्पिंडल्स असू शकतात. त्यात मोठ्या संख्येने टरेट्स असतात आणि तिसरा (Y) अक्ष त्यात टाकल्यावर बहुविध यंत्रभाग एकाच मशिनवर बनवणे शक्य होते. ज्यात टर्निंग आणि मिलिंग दोन्ही ॲप्लिकेशन्स आहेत अशा यंत्रभागांचे लहान प्रमाणातील उत्पादन घेण्यासाठी ही मशिन्स उपयुक्त असतात.
स्वयंचलित हत्यार परिवर्तक (टूल चेंजर)
बार आणि चकच्या कामात टूल्स लावण्याची क्षमता वाढवण्यासाठी सी.एन.सी. टर्न मिल सेंटर्समध्ये बहुविध टरेट्स आणि सब-स्पिंडल्सचे संयोजन केलेले असते. हल्ली असेही निदर्शनास आले आहे की, बी-अक्ष असणाऱ्या मशिन्समध्ये टूल्स लावण्याची क्षमता वाढवण्यासाठी टूल परिवर्तक दिले जातात. ही मशिन्स उच्च वर्गात मोडतात आणि बहुधा पुष्कळ महागडी असतात.
स्वयंचलित वर्क लोडिंग
मोठ्या प्रमाणात करण्याच्या कामाची अचूकता आणि जटिलता यांच्यानुसार स्वयंचलित वर्क लोडिंग साध्या न्युमॅटिक साधनांनी तसेच गँट्री अथवा रोबोमार्फत केले जाते. हे बॅच उत्पादनासाठी सोयीचे नाही.
स्वयंचलित गेजिंग आणि फीडबॅक
गँट्री अथवा रोबो वापरणाऱ्या मशिन्सना संपूर्ण स्वयंचलन देण्यासाठी याचा वापर केला जातो. मशिनवर अथवा मशिनबाहेर मापन करून, मिळालेला डेटा कंट्रोलरला दिला जातो आणि बनवण्यात येणाऱ्या यंत्रभागांची मोजमापे अचूकपणे नियंत्रित करण्यासाठी आवश्यक ते फेरबदल मानवी हस्तक्षेपाशिवाय केले जातात. उत्पादन प्रणालीमध्ये फेरबदल करण्यातील मानवी हस्तक्षेप टाळण्यासाठी स्वयंचलित गेजिंगचा उपयोग साध्या मशिनमध्येही करता येतो.
बार फीडर्स
बारवर काम करताना बार फीडर्सचा वापर केला जातो. यात लांब (3 मी) अथवा आखूड (1.5 मी) बार फीडर्स, एकल अथवा बहुल व्यासाचे बार फीडर्स - हायड्रॉलिकली ऑपरेटेड, बार मॅगॅझिनसहितचे सर्व्हो बार फीडर्स वगैरे अनेक प्रकार आहेत. यामुळे मानवी हस्तक्षेपाशिवाय बराच काळ मशिन चालू शकते आणि ऑपरेटर एकाच वेळी अधिक मशिन्स सांभाळू शकतो.
कार्यवस्तू कॅचर
बारवरच्या कामात कार्यवस्तू तयार झाल्यानंतर त्यांना एका ठिकाणी गोळा करण्यासाठी कॅचरचा उपयोग केला जातो. कार्यवस्तू एका परडीत किंवा करंडीत गोळा होतात आणि ऑपरेटर वेळोवेळी त्यांना तिथून हलवतो. या वैशिष्ट्यामुळे ऑपरेटर एकावेळी अधिक मशिन्स सांभाळू शकतो.
हत्यार स्थिती संनियंत्रण (मॉनिटरिंग)
सामान्यतः हे ऑपरेटरचे काम असते. कोणत्याही दिलेल्या ॲप्लिकेशनसाठी कर्तन हत्यारांची (कटिंग टूल्स) काही विशिष्ट आयुष्य मर्यादा असते, कारण त्यांची सतत झीज होत असते. ऑपरेटरने निर्माण होणारे यंत्रभाग वेळोवेळी तपासावे लागतात आणि टूल्सच्या ऑफसेटमध्ये योग्य बदल करून त्यांची मोजमापे नियंत्रणात ठेवावी लागतात. जर एका प्रमाणाबाहेर कर्तन हत्याराची झीज झाली, तर ते बदलावे लागते. जर ते योग्य वेळेत बदलले नाही, तर ते तुटण्याची शक्यता असते आणि त्यातून होणाऱ्या अपघातात मशिन्सचे नुकसान अथवा ऑपरेटरला दुखापत होऊ शकते. महत्त्वाच्या ॲप्लिकेशन्समध्ये हे काम हत्यार स्थिती संनियंत्रकासारख्या अत्याधुनिक उपकरणाद्वारे केले जाते.
यामध्ये टरेट बेसवर एक 3 अक्षीय पिझोइलेक्ट्रिक फोर्स डायनॅमोमीटर लावलेला असतो. एका मॉनिटरच्या साहाय्याने कर्तन क्रियेतील बलाच्या आलेखाचा मागोवा घेतला जातो. जसजशी टूल्सची झीज होते, तसतसा हा आलेख वाढत जातो. बऱ्यापैकी झिजलेल्या परंतु तरीही वापरता येण्याजोग्या टूल्ससाठी आलेखातील बलाची मर्यादा सुनिश्चित असते. नंतर जेव्हा मशिन पूर्ण झिजलेल्या टूल्सच्या बल मर्यादेवर पोहोचते, तेव्हा एक धोक्याचा इशारा दिला जातो, ज्याद्वारे टूल बदलण्याची सूचना मिळते. ही साधने महागडी असतात आणि जिथे टूलचे नुकसान झाल्यास गंभीर परिणाम होतील अशा ठिकाणीच ती वापरण्यात येतात. अशी उपकरणे पुरवणाऱ्या काही कंपन्यांची नावे पुढीलप्रमाणे आहेत. - आर्टिस, प्रोमथेक आणि मॉनट्रॉनिक्स.
अंगभूत मोटर्स असलेली स्पिंडल्स
सुरुवातीला यांचा वापर ग्राईंडिंग ॲप्लिकेशन्समध्ये वापरल्या जाणाऱ्या टूल्समध्ये केला जात असे आणि आता ते टर्निंग आणि मिलिंग ॲप्लिकेशन्समध्येही प्रचलित आहेत. मशिनच्या स्पिंडलमध्येच स्पिंडल मोटरचा स्टेटर आणि रोटर अंतर्भूत असतात. मशिनच्या ड्राईव्ह प्रणालीतील यंत्रभागांची संख्या कमी करण्याच्या हेतूने असे केले जाते. यात ड्राइव्ह बेल्ट नसतात, त्यामुळे कंपनाचा एक स्रोत नाहीसा होतो. टूलचे आयुष्य थोडेसे वाढते आणि पृष्ठभागाचा दर्जाही सुधारतो. अंगभूत मोटर्स असलेली स्पिंडल्स बेल्ट ड्राइव्ह असलेल्या स्पिंडल्सपेक्षा महाग असतात. बेल्ट ड्राइव्ह असलेली स्पिंडल्स अधिक मजबूत असतात आणि त्यांची देखभाल करणे सोपे असते. त्यामुळे ती उच्च टॉर्कच्या ॲप्लिकेशन्समध्ये वापरली जातात.
स्पिंडल ड्राइव्हसाठी बाह्य गिअर बॉक्सेस
इंजिन लेथप्रमाणे सी.एन.सी. लेथ्समध्येही दोन किंवा चार प्रकारच्या गतीबदलासाठी सुयोग्य असे गिअर बॉक्सेस देणे शक्य असते. अखंडपणे गतीबदल करण्याची स्पिंडल मोटरची क्षमता जमेस घेता मशिनची स्थिर टॉर्कची व्याप्ती वाढवता येते. परंतु स्पिंडल गती उच्च असल्यावर गिअर बॉक्सेसमधून अतिशय मोठा आवाज येतो. त्यामुळे बऱ्याच ॲप्लिकेशन्समध्ये अंगभूत गिअर बॉक्सेस ठेवण्याचे टाळले जाते. परंतु मोठ्या आकाराच्या मशिन्समध्ये अतिशय कमी गतीवर उच्च कर्तन टॉर्क प्राप्त करण्यासाठी मोटरवर स्वतंत्र गिअर बॉक्स बसवण्याची उदाहरणे आहेत. यामुळे दाते असलेल्या बेल्टद्वारा स्पिंडल ड्राइव्हमधून उच्च टॉर्कचे ट्रान्समिशन शक्य होते. झेडएफ, बारुफाल्डि अशा कंपन्या विविध स्टँडर्ड आकारामध्ये टूल्सच्या ॲप्लिकेशन्ससाठी तयार गिअर बॉक्सेस देऊ करतात.
प्रकाश पडदा/ सुरक्षा धार
ऑपरेटरची सुरक्षितता वाढवण्यासाठी मशिनच्या दरवाज्यात या गोष्टी समाविष्ट केल्या जातात. औद्योगिक कायद्यांमधील दंडात्मक तरतुदींमुळे कॉर्पोरेट कंपन्यांमध्ये ऑपरेटर्सच्या सुरक्षिततेवर अधिकाधिक लक्ष केंद्रित केले जात आहे.
सी.एन.सी. टर्निंग मशिन्समध्ये वर नमूद केलेल्या गोष्टी वापरण्यात येतात. सी. एन. सी लेथ्स विविध आकार आणि प्रकारात उपलब्ध असल्यामुळे यातील सर्व पर्यायांची यादी देणे अशक्य आहे. या लेखातून मशिन्सची उत्पादकता आणि सुरक्षितता कशी वाढवता येईल (अर्थात त्याची काही किंमत मोजून), या संबंधात काही कल्पना, काही विचार वाचकांसमोर मांडण्याचा प्रयत्न केला आहे. याद्वारे वाचकांच्या सी.एन.सी. लेथ विषयीच्या ज्ञानात थोडीफार भर पडली, तर या लेखाचे उद्दिष्ट सफल झाले असे म्हणायला हरकत नाही.
बी मचाडो एस डिझाइनर्स लि. कंपनीचे व्यवस्थापकीय संचालक आहेत. त्यांनी 1970 साली अभियांत्रिकी पदवी घेतल्यानंतर डिझाइन अभियंता म्हणून CMTI मध्ये काम सुरू केले. 1979 मध्ये CMTI मधून बाहेर पडून त्यांनी भागीदारीत एस डिझाइनर्स लि. कंपनी सुरू केली.