मोजमाप उपकरणे (Measuring Instruments) हे एक आव्हानात्मक क्षेत्र आहे. कारखान्यामध्ये (मशिनिंगच्या प्रक्रियेमध्ये) ज्या अचूकतेने काम केले जाते, त्या अचूकतेची तपासणी करणारी उपकरणे आपल्याला तयार करायची असतात, हे या क्षेत्रामधील सर्वात मोठे आव्हान आहे. त्यामुळे मोजमाप उपकरणांची निर्मिती इतर उत्पादांपेक्षा अधिक अवघड आणि किचकट असते. आम्ही जेव्हा सुरुवात केली, तेव्हा भारतामध्ये यासाठी लागणारे कुशल कामगार घडवले जात नव्हते. महाविद्यालयांमध्येदेखील या गोष्टी शिकविल्या जात नव्हत्या. त्यामुळे हा व्यवसाय सुरू करताना आम्हाला नवीन लोक घडवावे लागले, तयार करावे लागले.
गेज निर्मितीसाठी लागणाऱ्या ज्या काही प्रक्रिया असतात, त्या प्रक्रिया त्या उत्पादनाकडे पाहून, त्याच्यातील किचकट गोष्टी लक्षात घेऊन डिझाईन कराव्या लागतात. अगदी साधा प्लग गेज तयार करायचा, तर प्लग गेजची अचूकता ही साधारण 1 ते 2 मायक्रॉन असते. त्यासाठी मग ग्राईंडिंग मशिन्सच्या मर्यादेमध्ये 10-15 मायक्रॉनपर्यंत पोहोचता येते. त्यानंतर मात्र कुशल कामगाराकडून लॅपिंग प्रक्रियेद्वारे 15 मायक्रॉनपासून 2 मायक्रॉनपर्यंत अचूकता आणावी लागते. हे करण्यासाठी ती लॅपिंग मशिन्ससुद्धा आम्हाला तयार करावी लागली. तसेच गेज ग्राईंडिंग आणि लॅपिंगसाठी एकाच सेटअपमध्ये ग्राईंडिंग आणि लॅपिंग एकत्र होणारे मशिन गरजेचे होते. ते मशिन आम्हाला परवडू शकत नव्हते. आमची गेज तयार करणारी कंपनी असल्यामुळे आम्हाला जास्त मशिन्सची आवश्यकता होती. माझ्या वडिलांनी (विलासराव साळुंखे) ते मशिन ज्यांनी बनवले होते, त्या ’स्टूडर’ कंपनीशी चर्चा करून त्याचे डिझाईन घेतले व त्यावरून आम्ही स्वतः ते मशिन तयार केले.
या प्रक्रियेतील आव्हान
उत्पादनाच्या दृष्टीने लागणाऱ्या प्रक्रियांची कौशल्ये विकसित करणे, त्याला लागणारी सर्व हत्यारे आणि उपकरणे तयार करणे हे यातील मुख्य आव्हान होते. तसेच ते मोजण्यासाठी लागणारी उपकरणेदेखील तशीच अवघड होती. उदाहरणार्थ, आम्ही थ्रेड गेजेस करायला सुरुवात केली, तेव्हा थ्रेड गेज मोजण्यासाठी फ्लोटिंग कॅरिएज मायक्रोमीटर नावाचे उपकरण असते, तिथेही आव्हान होते. कुठल्याही गोष्टी आयात करण्यासाठी परवाना आवश्यक होता आणि त्यात अधिक वेळ खर्ची व्हायचा. त्यामुळे आम्ही ’मॅट्रिक्स’ कंपनीशी बोलून त्यांची डिझाईन्स घेतली. युरोपिअन उद्योगजगताने या सर्व गोष्टी 30-40 वर्षांपूर्वीपासून केल्या असल्यामुळे आता त्यांना त्याची गरज नव्हती. त्यामुळे आम्हाला त्यांच्याकडून डिझाईन्स मिळत गेले. त्यावरून मग आम्ही फ्लोटिंग कॅरिएज मायक्रोमीटर यंत्र तयार केले. अशी वेगवेगळी उत्पादने, मोजमाप उपकरणेसुद्धा आमच्या व्यवसायाचा भाग म्हणून इथे तयार होत गेली. अशा प्रकारे 1972 सालापासून ’ॲक्युरेट’चा प्रवास सुरू झाला. प्रत्येक वेळी नवीन उत्पादन म्हटले की, त्याला लागणारी मशिनरी, सर्व प्रक्रिया, त्याला लागणारी मोजमाप उपकरणे असे सर्व तयार होत गेले. यात प्रॉडक्ट डेव्हलपमेंट सायकल खूप मोठ्या होत्या. 1991 नंतर धोरणांमध्ये बदल झाले. त्यामुळे आम्हाला कच्च्या मालाचा पुरवठा सहज होऊ लागला. उत्पादनांची उप-उत्पादने आम्हाला उपलब्ध होत गेली. त्यामुळे यंत्रे तयार करणे अजून सोपे झाले.
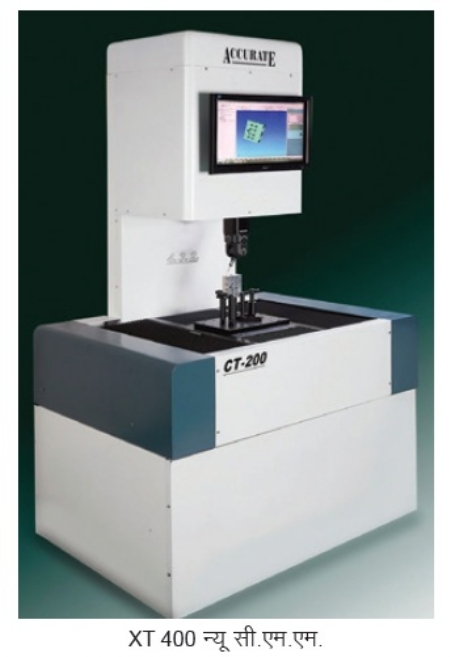
सी.एम.एम.चा प्रवास (को-ऑर्डीनेट मेजरिंग मशिन)
सी.एम.एम.ची रचना अतिशय स्थिर आणि भक्कम लागते. त्याला गंज चढता कामा नये. त्याचे आयुष्य भरपूर पाहिजे आणि तापमानाचा कमीत कमी परिणाम त्याच्यावर झाला पाहिजे. सी.एम.एम.मध्ये ’एअर बेअरिंग तंत्र’ आणि ग्रॅनाईट या दोन बाबी महत्त्वाच्या असतात, कारण सी.एम.एम.चे सगळे हालचाल करणारे गाईड्स असतात ते दाबयुक्त हवेच्या बेअरिंगवर चालतात. त्यामुळे त्याला अमर्याद आयुष्य मिळते. आम्हाला थोडे गेजिंगचे ज्ञान होते. त्याआधारे आम्ही भारतामध्ये एअर बेअरिंगचे तंत्रज्ञान विकसित केले. ग्रॅनाईटची प्रक्रियाही आम्ही विकसित केली. तिसरी महत्त्वाची गोष्ट होती, ती म्हणजे त्याला लागणाऱ्या डिजिटल स्केल्स, ऑप्टिकल स्केल्स. आम्ही सुरुवातीला 80 च्या दशकात मशिन टूलच्या रेट्रोफिटिंगमध्ये एका जपानी कंपनीसोबत काम करायचो. त्यांचे जे इलेक्ट्रॉनिक स्केल्स, डिजिटल स्केल्स मशिन टूलमध्ये वापरले जात होते, ते पाहिल्यानंतर हेच तंत्रज्ञान सी.एम.एम.मध्ये थोड्या वेगळ्या प्रकारे वापरले जात असल्याचे लक्षात आले. हे तीनही तंत्रज्ञान एकत्र करून त्यासाठीलागणारे सॉफ्टवेअर विकसित करून 1988 मध्ये सी.एम.एम.चे काम सुरू झाले. 1991 साली झालेल्या ’इम्टेक्स’ प्रदर्शनात पहिल्यांदा हे मशिन दाखवले गेले. त्यानंतर आम्हाला पहिली मागणी मिळाली.
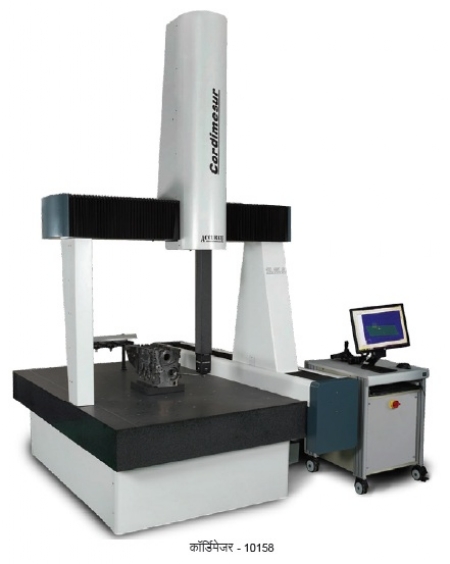
सी.एम.एम.ची प्रक्रिया सुरू झाली, त्यावेळी आम्ही एका युरोपिअन कंपनीसोबत काम करत होतो. मशिन भारतात विकणे, हा त्या कंपनीचा उद्देश होता. त्यामुळे आम्हाला अशा प्रकारच्या अत्याधुनिक मशिनसाठी इतर कोणत्या गोष्टींची आवश्यकता लागते हे समजले. उदाहरणार्थ, त्यासाठी सी.एन.सी. कंट्रोलर लागतात, प्रोब यंत्रणा लागतात, तसेच त्याची इको सिस्टिम, जी भारताबाहेर होती, त्याची ओळख झाली. सी.एम.एम.मध्ये ग्रॅनाईट हा एक महत्त्वाचा भाग होता. मी स्वतः भारतामध्ये आमचे जे महत्त्वाचे ग्रॅनाईट डेव्हलपमेंट सप्लायर होते, त्यांच्याशी बोललो. त्यावेळी आमच्या असे लक्षात आले, की हे पुरवठादार पारंपरिक पद्धतीने काम करत आहेत. परदेशामध्ये ग्रॅनाईटसारख्या गोष्टीचे मशिनिंग हे कन्व्हेंशनल मशिनवर होत असल्याचे मी पाहिले होते. सी.एम.एम. मशिनचे सर्व गाईडवे ग्रॅनाईटचे असतात. मशिन टूलचे जे स्लाईड वे ग्राइंडर असते, त्याच्यावर ग्रॅनाईटचे मशिनिंग होते. अर्थात त्याला लागणारी टूल्स वेगळी असतात. साधारण 1995-96 मध्ये एका कंपनीचे स्लाईड वे ग्राईंडिंग मशिन, लिलावात आम्हाला अतिशय कमी किंमतीत मिळाले. ती आमची सर्वात मोठी गुंतवणूक होती. ते मशिन आणले, बसवले आणि ग्रॅनाईटची सर्व डेव्हलपमेंट आम्ही सुरू केली.
एकत्र मशिनिंग त्याची लॅपिंग प्रक्रिया असा सर्व सेटअप आम्ही सुरू केला. पुढे 2002 मध्ये दुसरी एक चांगली संधी आम्हाला मिळाली. इटलीमध्ये आमच्याच क्षेत्रातील एक कंपनी होती. 50 वर्षे काम केलेल्या कंपनीचा काही कारणास्तव लिलाव झाला. त्यामध्ये त्या कंपनीची सर्व मशिन्स आम्हाला मिळाली. 2002 मध्ये आम्ही ती सर्व मशिन्स भारतामध्ये आणली. दरम्यान, तिथल्या काही डिझायनर लोकांना नोकरीची आवश्यकता होती. मग ते लोक व आमची माणसे यांचा एक कार्यगट बनवला गेला. त्यांचा अनुभव व आमच्या लोकांची ऊर्जा अशा गोष्टी एकत्र आल्या व तिथून खऱ्या अर्थाने सी.एम.एम.चा प्रवास सुरू झाला. आता आम्ही छोट्या मशिनपासून मोठ्या मशिनपर्यंत, जास्त अचूकता असलेले मशिन ते बॉडी इन्व्हाईट ॲप्लिकेशनपर्यंत वर्षाला जवळजवळ 125 मशिन्स तयार करतो. आज जर्मनी, अमेरिका, मेक्सिको, थायलंड, चीन अशा ठिकाणी मशिन्स पाठविली जातात. जवळजवळ 1 हजार मशिन्स आम्ही आपल्याच देशात दिल्या आहेत, मात्र अजूनही ही मशिन्स भारतात कमी प्रमाणात बनतात. ’ॲक्युरेट’ व हाताच्या बोटावर मोजण्याइतपत काही कंपन्या सोडल्या तर या क्षेत्रात फार कमी लोक आहेत. त्याला दोन गोष्टी कारणीभूत आहेत. एक म्हणजे आपले जे पूर्वीचे वातावरण होते, त्यामध्ये अशा प्रकारच्या कुठल्याही उत्पादाला योग्य त्या संख्येत (व्हॉल्युम) उत्पादन करणे हे एक प्रमुख आव्हान होते. दुसरे असे की, उद्योगांच्या दृष्टीनेसुद्धा मोजमाप उपकरणे ही कुठल्याही कारखान्यात अतिशय कमी संख्येने लागणारी वस्तू आहे. एकच उपकरण घ्यायचे आहे तर मग परदेशी ब्रँडचेच का घेऊ नये?, असा विचार अनेकदा व्हायचा. कारण इम्पोर्टेड मशिन असले की, ग्राहकांना सांगायला सोपे पडते, की तुम्ही जे वापरता तेच मशिन माझ्याकडे आहे.
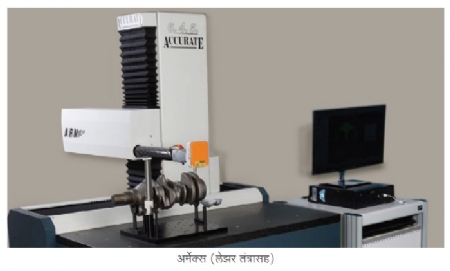
उपकरणे तयार करताना आलेल्या अडचणी
व्हर्निअरसारखी उपकरणे बनविण्यातल्या अडचणी अजूनच वेगळ्या आहेत. खरे तर भारतात कॅलिपर बनविणारे आम्ही पहिले होतो. त्यावेळची आव्हानेही खूप होती. यामध्ये एका वेगळ्या आव्हानाला आम्हाला तोंड द्यावे लागले. आम्हाला या कॅलिपरसाठी अचुंबकीय पोलाद (नॉन मॅग्नेटिक स्टील) आयात करावे लागत असे. त्यासाठी 410 आणि 420 ग्रेडचे स्टेनलेस स्टील लागत असे. मात्र त्यावेळी लघु उद्योगांमध्ये मोडत असलेल्या भांडीकामाला(स्टेनलेस स्टीलची भांडी) धोका आहे, असे भारत सरकारला वाटले. म्हणून सरकारने ती भांडी तयार करणाऱ्या लोकांच्या संरक्षणार्थ त्या स्टीलवर 300% आयात कर लावला. या वादात आम्ही अडकलो. या भांड्यांना जे स्टील लागत होते तेच 410, 420 ग्रेडचे स्टील आमच्या टूलला लागायचे. त्यावर उपाय म्हणून आम्ही इतर स्टील कंपन्यांकडून ते तयार करून घेतले, मात्र त्याचा जास्त काही फायदा होऊ शकला नाही. पुढे चीनमध्ये स्टीलचे मोठ्या प्रमाणावर उत्पादन घेतले जाऊ लागले आणि तिथल्या विशिष्ट उत्पादन पद्धतीमुळे त्यांनी प्रचंड संख्येत या उपकरणांचे उत्पादन सुरू केले आणि तो स्वस्त पर्याय खुला झाला. त्यामुळे या कंपन्यांनी सर्व जगाला मागे टाकले. पुढे लेझर तंत्राचा वापर इंडस्ट्रीमध्ये सुरू झाला आणि व्हर्निअरसारख्या उत्पादनाच्या मार्किंगच्या ज्या पद्धती होत्या त्याऐवजी लेझर पद्धती वापरायला सुरुवात झाली. (पूर्वी फोटोमार्किंग पद्धत वापरायचे.) हे लेझर मशिन चीनमधील प्रत्येक राज्याने विकत घेऊन ते तंत्रज्ञान अंमलात आणले. त्यामुळे संपूर्ण प्रक्रिया बदलली, उत्पादन खर्चदेखील बदलला. ते जगाच्या बाजारात पुढे निघून गेले. त्यामुळे आताची परिस्थिती अशी आहे की, ज्या उत्पादनांना विक्रीनंतर सेवा लागत नाही अशा उत्पादनांसाठी, भारतच काय पण आज जगातील कुठल्याच देशाला चीनसोबत स्पर्धा करणे हे खरेच अवघड आहे. या क्षेत्रातील ज्या कंपन्या स्वत:चे असे एखादे विशेष उत्पादन घेऊन त्यात विकास करत गेल्या त्याच टिकल्या आहेत. आम्हाला अभिमान वाटतो की ’ॲक्युरेट’ त्यातील एक कंपनी आहे.
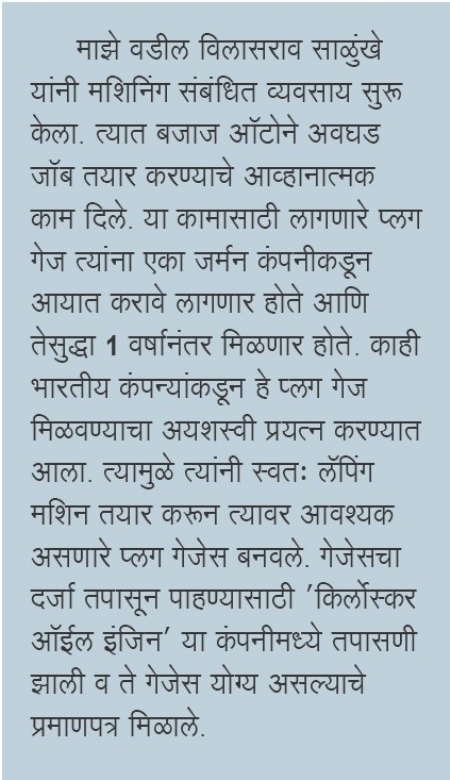
या सर्वांमध्ये इलेक्ट्रॉनिक्सचादेखील खूप मोठा सहभाग आहे. आता ’इंडस्ट्री 4.0’ नावाचे औद्योगिक स्टँडर्ड प्रस्थापित होत आहे, ज्यामध्ये स्वयंचलित कॉम्पेन्सेशन किंवा काम चालू असतानाच प्रोसेस करेक्शन कसे करता येईल यावर भर असेल. जिथे वेगवेगळ्या उपकरणांना एकमेकांशी संवाद साधावा लागणार आहे आणि त्याची नवीन कार्यपद्धती आता सर्वत्र स्थापन होत आहे, तिथे इलेक्ट्रॉनिक्स फार महत्त्वाचे असेल. दुर्दैवाने अशा प्रकारचे इलेक्ट्रॉनिक्स (हार्डवेअर) भारतामध्ये होत नाही, कारण इलेक्ट्रॉनिक्समध्ये जे वेगवेगळ्या प्रकारचे सेन्सर्स आहेत, त्याचे उत्पादन भारतामध्ये होत नाही. युरोप आणि चीनमध्ये असे उत्पादन घेतले जाते.
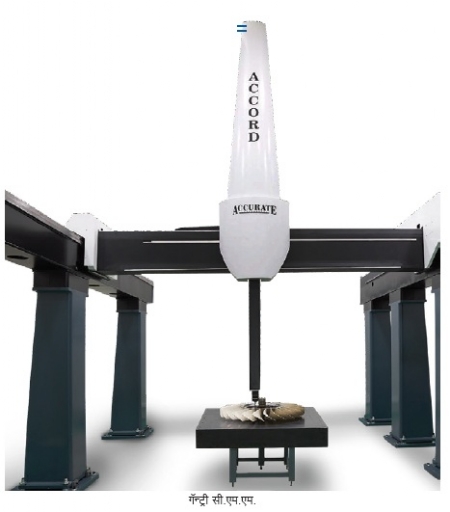
विक्री आणि विपणन यासाठी आमची काही धोरणे होती. आम्ही असे ठरवले होते, की या उद्योगासाठी जितका माल आम्ही आयात करत आहोत, तितका तरी निर्यात व्हायला हवा. या वर्षी आमच्या कंपनीचा 25% माल निर्यात करत आहोत आणि तो वाढत जाऊन 40% व्हावा अशी इच्छा आहे. अर्थातच भारतातली बाजारपेठ आमच्यासाठी व्यवसायाच्या दृष्टीने सर्वात मोठी बाजारपेठ आहे. सध्या भारतामध्ये ’ॲक्युरेट’चे मार्केट हे जवळजवळ 40% आहे व उरलेले 60% इतर कंपन्यांमध्ये विभागले आहे. त्यामुळे आता आमची मशिन्स भारताबाहेर कशी विकता येतील यावर आम्ही लक्ष केंद्रित केले आहे. सी.एम.एम.सोबतच आम्ही इतरही मोजमाप उपकरणे निर्यात करतो.
संशोधन आणि विकास परिस्थिती
संशोधन आणि विकासामध्ये आमच्यासारख्या कंपन्यांनी योग्य समतोल साधला आहे. आपले अभियंते आणि बाहेरून मिळणारे मार्गदर्शन यांच्यातील परस्पर सामंजस्याने आम्ही हे करू शकतो. अशा प्रकारच्या क्षेत्रात काम करताना अचूकतेच्या दृष्टीने काही गोष्टी महत्त्वाच्या आहेत. तुम्ही वापरणारे उपकरण आणि ते उपकरण वापरताना असलेले वातावरण (तापमान, आर्द्रता इत्यादी) हा मुद्दा फार महत्त्वाचा आहे. म्हणजे योग्य त्या तापमानाला ते उपकरण वापरता येणे महत्त्वाचे आहे. उपकरण बनवण्यासाठी योग्य ऑपरेटर, त्याचे कौशल्य, अवघड आणि किचकट प्रक्रियेची संपूर्ण आणि योग्य माहिती असणे गरजेचे आहे. ’ॲक्युरेट’मध्ये या तीनही गोष्टींचा समन्वय साधण्याचा प्रयत्न केला आहे. ’अॅक्युरेट’ ही फक्त एक कंपनी नसून, ती एक ’इंस्टिट्युशन’ आहे, जिथे आमचे सर्व कामगार हे ’कुशल कामगार’ बनतील यावर आमचे लक्ष असते. प्रत्येक कामगाराला सर्व प्रकारची माहिती असायला हवी, तसेच त्याला सर्व प्रकारचे काम करता यायला हवे, हे सुद्धा आम्ही पाहतो. यांत्रिक, इलेक्ट्रॉनिक्स, सॉफ्टवेअर अशा सर्वच क्षेत्रात आम्ही सक्षम होण्याचा प्रयत्न करत असतो.
संशोधनासाठीचे अभियंतेही आम्हालाच तयार करावे लागतात. त्यामुळे आम्ही अननुभवी अभियंते घेऊन त्यांना उत्पादन क्षेत्रात आधी काम करायला लावून तयार करतो. मगच ते डिझाईनमध्ये येतात. पूर्वी एखादे उत्पादन विकसित करायला, ते स्थिर व्हायला जो वेळ लागायचा तो आता आमच्याकडे खूप कमी झाला आहे. नव-नवीन प्रक्रिया त्याच्या खाचाखोचा, समस्या निराकरण तंत्रे समजली आहेत आणि त्यामुळे सर्व प्रक्रिया सुलभ झाल्या आहेत.
[email protected]
विक्रम साळुंखे यांचे वडील विलासराव साळुंखे यांनी 1963 साली अक्युरेट गेजिंग अँड इन्स्टुमेंट्स प्रा. लि. कंपनीची स्थापना केली. विक्रम साळुंखे यांनी अभियांत्रिकीचे शिक्षण पूर्ण केल्यानंतर मागील 29 वर्षांपासून ते कंपनीचे व्यवस्थापकीय संचालक म्हणून काम पाहत आहेत.