साध्या लेथ मशिनवर जॉब वर्क करण्यापासून सुरुवात केलेल्या लघु उद्योगाचे, आज आयात होणाऱ्या वंगण विरहित बुशला सक्षम भारतीय पर्याय देणाऱ्या कंपनीत रुपांतर झाले आहे.
मशिनिंगच्या कामापासून सुरुवात झालेल्या आमच्या ‘एव्हीआय ऑईललेस’ (AVI OILLESS) कंपनीला मशिनिंगची कामे सुरू असतानाच ‘बजाज ऑटो’साठी यंत्रभाग (पार्टस्) बनविण्याची संधी मिळाली. ‘बजाज ऑटो’ कंपनीला आम्ही प्रेस टूल डाईज आणि प्रेशर डाय कास्टिंग्जच्या पार्टस्चा पुरवठा करीत होतो. त्याचबरोबर टूल रुमला आवश्यक असणाऱ्या टर्निंग, मिलिंग केलेल्या भागांचा (पार्टस्) पुरवठा करायला कंपनीने सुरुवात केली.
गाईड एलिमेंटचे तंत्र
गाईड एलिमेंटमध्ये दोन प्रकार आहेत. एक प्लेटच्या आकाराचे तर दुसरे बुश आकाराचे असते. हे दोन्ही प्रकार प्रेस टूलमध्ये वापरले जातात. पूर्वी हार्डन्ड स्टील मटेरिअलमधील म्हणजे, केस हार्डन्ड किंवा हाय कार्बन, हाय क्रोमिअम EN-31 मटेरिअल हार्डनिंग आणि ग्राईंडिंग केलेली बुश वापरली जायची. वंगणन (ल्युब्रिकेशन) होण्यासाठी पूर्वीच्या तंत्रज्ञानामध्ये ऑईल किंवा ग्रीस दिले जायचे. नवीन तंत्रज्ञानात वंगणनासाठी ग्रॅफाईट वापरले जाते. ग्रॅफाईटची सूक्ष्म संरचना (मायक्रो स्ट्रक्चर) थरांनी बनलेली (लेयर टाईप) असून, त्याची रचना षट्कोनी आहे. घर्षण झाल्यावर त्याचे थर सुटत जातात आणि फिल्म बनते. (चित्र क्र.1) ग्रॅफाईट मटेरिअल, मॉलेब्डेनम डाय सल्फाईड (MOS2) आणि पॉली टेट्रा फ्लोरो इथिलीन (PTFE) या तीन मटेरिअलमध्ये वंगणाचे गुणधर्म आहेत. (चित्र क्र.2)
वंगण विरहित बुश
ग्रॅफाईट हे घन स्वरुपातील वंगण (सॉलिड ल्युब्रिकंट) आहे. नवीन तंत्रज्ञानात ग्रॅफाईटच्या वंगणन गुणधर्माचा उपयोग प्रेस टूलमध्ये करण्यात आला. मँगेनिज ब्राँझ हे त्याचे मूळ (बेस) मटेरिअल असून, त्यास हाय टेन्साईल ब्राँझ असेही म्हणतात. यामध्ये ग्रॅफाईट मटेरिअल बसवले (एम्बेड) जाते. ग्रॅफाईट मटेरिअल बसवण्यासाठी मँगेनिज ब्राँझच्या प्लेटवर भोके पाडून, स्लाईडिंगची जी दिशा असेल, (लांबीच्या बाजूने किंवा रुंदीच्या बाजूने) ती दिशा विचारात घेऊन ग्रॅफाईटच्या जागांची रचना करावी लागते. स्लाईडिंग होणार्या भागाचा प्रत्येक बिंदू ग्रॅफाईटच्या संपर्कात आला पाहिजे, हा यामागील मुख्य उद्देश असतो. ग्रॅफाईट घट्ट बसण्यासाठी त्याला एक इपॉक्सी रेझिन हे विशेष ॲडेजिव्ह वापरले जाते. हे इपॉक्सी रेझिन साधारण 3000 ते 4000 सेंटीग्रेड या तापमानापर्यंत टिकते. म्हणजे इतक्या उच्च तापमानालादेखील ग्रॅफाईटचा बसविलेला प्लग बाहेर येत नाही. यानंतर त्यावर फिनिश टर्निंग आणि ग्राईंडिंग प्रक्रिया करण्यात येते.
उत्पादन विकास प्रक्रिया
सुरवातीला हे उत्पादन पाहिल्यानंतर त्याचे मटेरिअल कोणते इथपासून, त्या मटेरिअलचे केमिकल कंपोझिशन, मेकॅनिकल प्रॉपर्टीज आम्हाला तपासाव्या लागल्या. ते मटेरिअल भारतात उपलब्ध आहे की नाही, याचीदेखील आम्हाला कल्पना नव्हती. संशोधन करून आम्ही हाय टेन्साईल ब्राँझ (मूळ मटेरिअल मँगेनिज ब्राँझ) या मटेरिअलचा स्रोतदेखील मिळवला, मात्र त्यावेळी आम्हाला ते कमी प्रमाणात सहजपणे उपलब्ध झाले नाही. चाचणीसाठी कमीत कमी 1 टन मटेरिअल घ्यावे लागेल असे त्या उत्पादकाकडून सांगण्यात आले. हे आर्थिक आव्हान स्वीकारून आम्ही मटेरिअल खरेदी केले. त्याचे कास्टिंग करतानाही आम्हाला अनेक अडचणी आल्या. बुश कास्टिंग करण्यासाठी आम्ही काही फाऊंड्रीशी संपर्क साधून त्यांच्याकडे बुश किंवा प्लेट कास्ट करण्याचे प्रयत्न केले. परंतु या मटेरिअलची द्रव ते घन ही जी फ्रिझिंग रेंज आहे, ती फक्त 300 सेंटीग्रेडची आहे. या 300 सेंटीग्रेडमध्येच ते वितळलेले मटेरिअल साच्यामध्ये ओतायला लागायचे. यावेळी वितळलेले मटेरिअल भट्टीपासून साच्यापर्यंत नेण्यासाठी लागणारा वेळ, त्यात कमी होणारे तापमान यामुळे कास्टिंगमध्ये अनेक दोष निर्माण होत होते. हेदेखील आमच्यासमोरील मोठे आव्हान होते. आम्ही हार न मानता प्रयोग करत गेलो. राईजर काय मापाचा (साईज) ठेवायला पाहिजे, त्याची आकुंचन क्षमता तपासायची, तापमान कमी जास्त करून काही फरक पडतोय का? अशा सर्व बाजूंनी विचार करत प्रयोग केले. बर्याच अभ्यासानंतर आणि प्रयोगानंतर असे लक्षात आले की, क्लोज मोल्डऐवजी ओपन मोल्डमध्ये कास्टिंग यशस्वीपणे होते. त्यानुसार आम्ही ओपन मोल्डमध्ये कास्टिंग केले. (चित्र क्र.3)
अपेक्षित दिशेने घनीभवन (डायरेक्शनल सॉलिडिफिकेशन) होण्यासाठी असलेली मोल्डिंगची पेटी ही थोडीशी तिरकी ठेवावी लागते. अशाप्रकारे टप्प्याटप्प्याने सुधारणा करत गेल्यानंतर साधारणतः 5 ते 6 महिन्यांनी आम्हाला सकारात्मक परिणाम मिळाले. कास्टिंग यशस्वी झाल्यामुळे मशिनिंगला काही अडचण आली नाही, मात्र त्यात ग्रॅफाईट कसे बसवायचे (जास्त क्लिअरन्स दिला तर ग्रॅफाईट बाहेर येते.) यासाठी ग्रॅफाईट आणि छिद्रामधील क्लिअरन्स किती पाहिजे, या गोष्टींचा आम्हाला अभ्यास करावा लागला. ॲडेजिव्ह कोणते वापरायचे यासाठीदेखील आम्ही बरेच संशोधन केले. ग्रॅफाईट आणि कामाच्या वेळी असणारे तापमान या दोन्हीला योग्य असणारे , तसेच नुसत्या हवेमध्ये सेट होणारे असे ॲडेजिव्ह आम्ही वापरले. सुरुवातीला ग्रॅफाईटला ॲडेजिव्ह लावल्यानंतर ते हवेत सेट करण्यासाठी ठेवायचे. त्यानंतर ही पद्धत बदलून आम्ही विशेष इपॉक्सी ॲडेजिव्ह वापरायला सुरुवात केली. अनेक प्रयत्न करून हा यंत्रभाग विकसित केल्यानंतर आम्ही 4-5 प्लेटस बनवून बजाजमध्ये दाखवल्या. या उत्पादनाच्या त्यांनी जवळपास 2 वर्षे चाचण्या (ट्रायल) घेतल्या. या चाचण्यांनंतर आयात केलेल्या प्लेट्स आणि आमच्या प्लेट्स यांचे रिझल्ट्स एकसारखे मिळाल्याचा अभिप्राय त्यांनी आम्हाला दिला. आपल्याच देशात हे उत्पादन मिळत असल्याने त्यांनी या उत्पादनाची आयात करणे पूर्णपणे बंद केले. यामध्ये त्यांची जवळपास 50% हून अधिक आर्थिक बचत (कॉस्ट सेव्हिंग) झाली.
फोर्जिंग आणि एक्सट्रूजन करून मटेरिअल आणले असते तर ते खर्चिक होत होते.छोट्या प्रमाणातील उत्पादनासाठी कमी संख्येने कच्चा माल देणारेही त्यावेळी कोणी नव्हते. त्यामुळे सुरुवातीला लागणारा कच्चा माल आम्ही इनगॉट फॉर्ममध्ये आणला होता. प्लेट आणून त्यातून मशिनिंग करणे असा आम्ही विचार केला, मात्र प्लेट पाहिजे त्या मटेरिअलमध्ये मिळत नसल्यामुळे, कास्टिंगशिवाय आमच्याकडे पर्याय नव्हता. बाजारपेठेत उपलब्ध असलेल्या या एक्सट्रूडेड प्लेटस् या फॉस्फरस आणि ब्राँझ मटेरिअलमध्ये मिळायच्या. हाय टेन्साईल ब्राँझ या मटेरिअलचे गुणधर्म (प्रॉपर्टीज) वेगळे असल्यामुळे आम्हाला कास्टिंगकडे जाणे भाग पडले. अनेक वर्षे आम्ही हे काम सँड कास्टिंगमध्ये केले. त्यानंतर सेंट्रिफ्युगल कास्टिंगमध्ये आणि आता आम्ही ते कंटिन्युअस कास्टिंगमध्येदेखील करत आहोत. मोठ्या आकारासाठी आपण सेंट्रिफ्युगल कास्टिंग करू शकतो, तर छोट्या आकारासाठी कंटिन्युअस कास्टिंग करतो. खर्चाचीही बचत होते. सँड कास्टिंगमध्ये आम्हाला 5 ते 6 मिमी मशिनिंग अलाउन्सेस ठेवावे लागायचे. प्रक्रिया बदलल्यानंतर अलाउन्सेस कमी होऊन आता आम्ही 2 मिमी अलाउन्सेसमध्ये काम करतो.
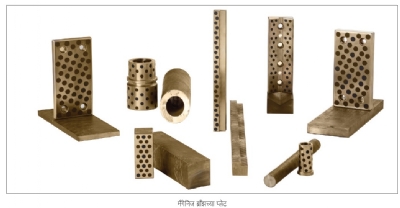
सेल्फ ल्युब्रिकेटिंग बुशचे फायदे
वर्कशॉपमध्ये किंवा मशिन फ्लोअरवर जी धूळ असते, त्याचा कोरड्या वंगणनामुळे (ड्राय ल्युब्रिकेशन्स) बनलेल्या या फिल्मवर काहीही परिणाम होत नाही. त्यामुळे फोर्ज इंडस्ट्री, सिमेंट इंडस्ट्रीमध्ये हे बुश मोठ्या प्रमाणात वापरले जातात. तसेच फार्मास्युटिकल उद्योगांत जिथे वंगणनासाठी ऑईल किंवा ग्रीस वापरू शकत नाही. याठिकाणी हे गाईड एलिमेंट वापरले जातात. हायड्रोपॉवर क्षेत्रात जिथे टर्बाईनमध्ये वारंवार वंगणन करणे शक्य नसते अशा ठिकाणी ही सेल्फ ल्युब्रिकेटिंग एलिमेंट/बुश वापरली जातात. मशिन शॉप किंवा मशिन टूल उद्योगात, हायड्रोपॉवर ॲप्लिकेशनसाठी आणि प्रेस टूल डाईजमध्ये ही बुश वापरली जातात. प्रेस टूल डाईजमध्ये खूप जास्त भार (लोड) असतो. त्या तुलनेने त्याचा वेग कमी असतो. अशा कामाला ही बुश अधिक योग्य ठरतात. त्याठिकाणी पारंपरिक स्टील आणि ऑईल/ग्रीजची बुश वापरली जायची. मात्र, त्यापेक्षा या बुशची कामगिरी चांगली आहे. स्टीलचे हार्डन केलेले बुश वापरले तर त्याठिकाणी सातत्याने ऑईल किंवा ग्रीस टाकावे लागते. ते टाकत असताना काही चूक झाली तर वंगणन छिद्रे (ल्युब्रिकेशन पॉईंटस) बंद (ब्लॉक) होतात. त्यामुळे वंगणनाची प्रक्रिया व्यवस्थित होत नाही. या परिस्थितीमध्ये डाय अडकण्याची शक्यता अधिक असते. नवीन तंत्राच्या बुशचा वापर केला तर, बाहेरून अतिरिक्त वंगणनाची गरज भासत नाही. तसेच सातत्याने ग्रॅफाईटची सेल्फ ल्युब्रिकेटिंग फिल्म तयार होत असल्याने जॅमिंग आणि लॉकिंग होत नाही. ज्यावेळी डाय दुरुस्तीसाठी किंवा साफ करायला घेतला जाईल त्यावेळी ते बुश आतून स्वच्छ करावे लागतात. जेव्हा डाय स्वच्छ केला जातो, तेव्हा जुनी फिल्म तिथून निघून जाते आणि पुन्हा नव्याने तशी फिल्म तयार होते. जोपर्यंत ल्युब्रिकेशन फिल्म आहे तोपर्यंत बाहेरून वंगणनाची आवश्यकता लागत नाही.
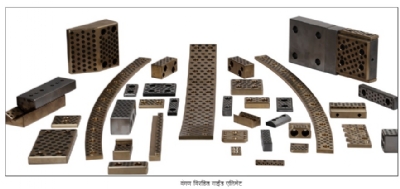
वंगण विरहित स्लाईड प्लेटचा प्रेस टूल डायमधील उपयोग
अनेक मशिन टूलमध्ये हे बुश वापरले जातात. सी.एन.सी, व्ही.एम.सी.मध्ये बऱ्याचठिकाणी काही पॅलेट चेंजर्स असतात. त्या पॅलेट चेंजर्सच्या यंत्रणामध्ये ही बुश वापरण्यात येतात. जिग्ज आणि फिक्श्चर्समध्ये ज्या ठिकाणी पिवोट वापरले जाते त्या लिंकमध्ये ही बुश वापरली जातात. स्टील प्लँटमधील कन्व्हेअर्समध्ये सातत्याने वंगणन करता येत नाही. कारण तेथील परिस्थिती एकतर उष्ण असते आणि त्यात असणारे रोलर्स थंड ठेवण्यासाठी त्यावर सतत पाणी मारले जाते. म्हणजे उष्ण आणि थंड अशी दुहेरी परिस्थिती त्या ठिकाणी असते. त्या ठिकाणी ही बुश उपयोगात आणली जातात. परंतु ज्या ठिकाणी फिरण्याचा वेग जास्त असतो त्या ठिकाणी हे योग्यपणे काम करत नाहीत. कारण उच्च आरपीएमला ग्रॅफाईट मटेरिअल वेगाने झिजते. कमी वेग आणि वजनाला अधिक असलेल्या या कामामध्ये ते जास्त फायदेशीर ठरतात. जेसीबीसारख्या अर्थ मुव्हिंग मशिनमध्येही ही बुशेश वापरली जातात. व्होल्टासला, काही स्टॅकर्समध्ये तर, काही मटेरिअल वाहतुकीच्या साधनांमध्ये लिफ्टिंग मेकॅनिझममध्येदेखील ही बुश वापरली जातात.
फोर्कलिफ्ट आणि मटेरिअल हँडलिंग याठिकाणी बुशचा वापर होतो. उदाहरणार्थ, मटेरिअल हँडलिंग आणि सीझर लिफ्टमध्ये असलेले बेअरिंग काढून बुश लावता येते. तसेच प्लॅस्टिक इंजेक्शन मोल्डिंग मशिनमध्ये ही बुश वापरली जातात. प्रेस टूल, प्लॅस्टिक मोल्ड्स आणि वेल्डिंग फिक्श्चर्स यातील महत्त्वाच्या गाईडिंग एलिमेंटससाठीसुद्धा यांचा वापर होतो. पेंटिंग लाईनच्या कन्व्हेअर्समध्येदेखील हे बुश दिलेले आहेत.
स्टँडर्ड बुशचे आयुष्य कमी असून, त्याला ठराविक काळाने मेंटेनन्स करावा लागतो. त्याउलट ऑईललेस बुशची किंमत थोडीशी जास्त असली तरी, त्याचे आयुष्य जास्त आहे आणि मेंटेनन्स कमी आहे. बुशचे आयुष्य हे ॲप्लिकेशनवर अवलंबून आहे. प्रेस टूल्समध्ये जी बुश दिली जातात त्याचे साधारण आयुष्य हे 10 लाख स्ट्रोक्सपेक्षा अधिक मिळते. स्टँडर्ड बुशमध्ये तुलना केल्यास याचे साधारण आयुष्य हे 2 ते 3 पटीने अधिक मिळते.
भारतातील अनेक प्रेस टूल डाईज उत्पादकांना आम्ही या बुशचा पुरवठा करतो. भारतात वंगण विरहित बुश व्यवसायातील असलेल्या मोठ्या संधीचा फायदा ओळखत काही बहुराष्ट्रीय कंपन्यांनी येथे व्यवसाय सुरू केला आहे. हा व्यवसाय करणारी ‘एव्हीआय ऑईललेस’ (AVI OILLESS) ही भारतातील पहिली कंपनी असून, 1997-98 साली आम्ही या व्यवसायाला सुरुवात केली. आमचा बाजारपेठेतील हिस्सा हा अंदाजे 25 ते 30% आहे.
प्रशांत हेंद्रे यांनी पुण्याच्या अभियांत्रिकी महाविद्यालयातून 1995 साली अभियांत्रिकीची पदवी घेऊन नंतर त्यांनी एम.ई. (मेटलर्जी) पूर्ण केले.
गेली 16 वर्षे विविध कंपन्यांमध्ये विविध विभागात काम करून सध्या ते ए.व्ही.आय. ऑइललेस कंपनीचे संचालक आहेत.