आधुनिक उत्पादनासाठी यंत्रणामधील अचूकता, छोट्या आकारांच्या जॉबवर काम करण्याची क्षमता वाढविण्याबरोबरच अनियमित आकाराचे यंत्रण सुलभपणे करण्याची गरजही सतत पुढे येत आहे. ही गरज पुरविण्यासाठी मशिनमध्येही नवीन तंत्र विकसित होत आले आहे. तुलनेने नवीन असलेल्या इ.डि.एम. (इलेक्ट्रिक डिस्चार्ज मशिन) तंत्राविषयी या लेखात माहिती दिली आहे.
इ.डि.एम. तंत्रज्ञान
इ.डि.एम.ने ड्रिलिंग करण्याच्या पद्धतीमुळे छोटी तसेच खोल (डीप) ड्रिल्स अतिशय वेगाने तसेच अचूकपणे करता येतात. यामुळेच साचे आणि इतर भाग बनविण्याच्या प्रक्रियेमध्ये या तंत्रज्ञानाचा वापर वाढला आहे. पारंपरिक पद्धतीने ड्रिलिंग करताना 1 मिमीपेक्षा कमी व्यासाच्या ड्रिलिंगमध्ये अडचणी येतात. 0.1 ते 3.0. मिमी व्यासापर्यंत इ.डि.एम.चा पर्याय सर्वोत्कृष्ट ठरतो. कधीकधी 10 मिमीपर्यंतही ही पद्धत वापरता येते. ड्रिल तुटणे, बोथट होणे आणि ड्रिल बिटला परत ग्राईंडिंग करणे या सर्व गोष्टी कराव्या लागत नाहीत. त्यामुळे मोठ्या प्रमाणावर वेळेची आणि खर्चाची बचत होते. इ.डि.एम. ने तयार झालेल्या छिद्राचा व्यास, व्हर्टिकॅलिटी आणि सिलिंड्रिसिटी वरपासून खालपर्यंत अतिशय अचूक आणि तंतोतंत मिळते. या तंत्रामुळे कठीण धातूवर ड्रिलिंग करता येते. पारंपरिक पद्धतीने ड्रिल करून हार्डनिंग केलेल्या शीट्समध्ये छिद्रांचा आकार बदलतो. हा दोष इ.डि.एम. यंत्रणेत टाळता येतो. टंग्स्टन, टायटन, इन्कोनेल, पोलाद मिश्रधातू, मॉलिब्डेनम यासारख्या कठीण धातूंचे यंत्रण या पद्धतीने करता येते. यापूर्वी पारंपरिक यंत्रांचा वापर करून कमी आकाराची छिद्रे पाडणे शक्य नव्हते ते आता सहज शक्य झाले आहे. कोणत्याही वहनक्षमता (कंडक्टिव्हिटी) असलेल्या मटेरिअलमध्ये छिद्रे पाडण्यासाठी या तंत्रज्ञानाचा वापर सतत वाढत चालला आहे.
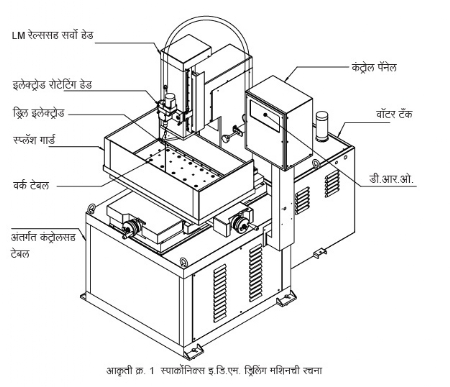
इ.डि.एम.होल ड्रिलरचे प्रमुख भाग
• स्टेनलेस स्टीलचे वर्क टेबल
• फिरणारा स्पिंडल
• इलेक्ट्रोड पकडण्यासाठी ड्रिल चक
• सिरॅमिक किंवा रुबी गाईड्स
• पॉवर सप्लाय सहित कंट्रोल पॅनेल
• डाय इलेक्ट्रिक फ्लुईड पंप
इलेक्ट्रोडचे प्रकार
एक छिद्र (सिंगल होल) किंवा अनेक छिद्र (मल्टी होल) चॅनेल - ज्या आकाराचे छिद्र पाडायचे असेल त्यानुसार इलेक्ट्रोडचा प्रकार निवडला जातो. 1 मिमीपेक्षा कमी आकाराच्या छिद्रासाठी एक छिद्र इलेक्ट्रोड वापरावा आणि 1 मिमीपेक्षा मोठ्या आकाराच्या छिद्रासाठी अनेक छिद्र असलेला इलेक्ट्रोड वापरावा. कार्यवस्तूमधून इ.डि.एम.ने यशस्वीपणे छिद्र पाडण्यासाठी आणखी दुसरा महत्त्वाचा घटक म्हणजे पितळेच्या किंवा तांब्याच्या इलेक्ट्रोड नळीच्या आंतरव्यासातून जाणाऱ्या वाहिन्यांची संख्या. मुळात, इलेक्ट्रोडकडून अपेक्षित असलेली कामगिरी त्याच्या केंद्रातून कुठल्या प्रकारचे छिद्र जात आहे, यावर अवलंबून असते. कारण वेगवेगळ्या गरजांसाठी वेगवेगळ्या प्रकारच्या अंतर्गत वाहिन्या बनविल्या जातात. पहिली गरज असते ती इलेक्ट्रोडच्या केंद्रातून पाणी किंवा कूलंटचे वहन करणे ज्यामुळे पितळेची किंवा तांब्याची नळी जास्त तापत नाही आणि जळत नाही. जर इलेक्ट्रोड खूप तापला तर तो मऊ होऊन वेडावाकडा होऊ शकतो आणि त्यातून सरळ रेषेतील ‘ड्रिल’ किंवा अचूक सातत्याचे ड्रिलिंग होऊ शकत नाही. इ.डि.एम. इलेक्ट्रोड ट्यूब एक किंवा अधिक वाहिन्यांची असावी हा देखील यातील महत्त्वाचा मुद्दा आहे. ‘ड्रिल’ करत असताना पडणारे छिद्र आरपार आहे की एका बाजूने बंद (ब्लाईंड होल) आहे, ते निश्चित करावे. कारण एका बाजूने बंद असलेल्या छिद्रामधून ड्रिल आरपार जात नसल्यामुळे स्पर्श न झालेला मटेरिअलचा तुकडा शिल्लक राहतो.
ड्रिल ट्यूब इलेक्ट्रोड्स
ब्रास किंवा कॉपर ट्युब्युलर इलेक्ट्रोड्स इ.डि.एम. ड्रिलिंगच्या प्रक्रियेसाठी गरजेचे असतात. हे इलेक्ट्रोड्स 0.1 मिमीच्या फरकाने उपलब्ध असतात. (उदाहरणार्थ, 0.2, 0.3, 0.4 मिमी ... 3.0 मिमी व्यासापर्यंत) स्टँडर्ड इलेक्ट्रोड्सची उपलब्ध लांबी 400 मिमी असते. असे इलेक्ट्रोड्स आयात करावे लागतात. 1.00 मिमीपर्यंतच्या छिद्राच्या व्यासासाठी एकच छिद्र असलेल्या इलेक्ट्रोडची शिफारस करण्यात आलेली आहे आणि दोन चॅनेल किंवा अनेक छिद्र असलेली इलेक्ट्रोड 1.0 मिमी आणि त्यापेक्षा जास्त व्यासाच्या छिद्रासाठी योग्य आहे. ड्रिलिंग करतेवेळी जी तार येते ती बहुछिद्र रचनेमुळे येत नाही, म्हणून बहुछिद्र रचना असलेले इलेक्ट्रोड्स वापरले जातात.
इ.डि.एम. ड्रिलिंग प्रक्रिया
यामध्ये तांब्याच्या किंवा पितळेच्या अचूक आकाराच्या नळीचा इलेक्ट्रोड म्हणून वापर केला जातो. हा इलेक्ट्रोड ‘Z’ अक्षावर असलेल्या ड्रिल चकमध्ये बसविला जातो आणि कार्यवस्तूच्या वरती एका सिरॅमिक किंवा रुबी गाईडच्या साहाय्याने धरला जातो. कार्यवस्तूच्या वरच्या पृष्ठभागाचे माप घेऊन किती खोलवर ड्रिल करायचे ते ठरविले जाते. इलेक्ट्रोड कार्यवस्तूच्या वरच्या पृष्ठभागावर टेकला की ‘Z’ अक्षाचे रिडिंग ’0’ सेट केले जाते. ड्रिलिंगची सुरुवात होण्याचा हा बिंदू असतो. इलेक्ट्रोड फिरवायला सुरुवात केली जाते. नळी आकाराच्या इलेक्ट्रोडमधून निचरा करण्यासाठी 50 ते 100 कि.ग्रॅ./ स्क्वेअर सेमी दाबाने पाण्याचे द्रावण सोडले जाते. पॉवर सप्लायमधले ऑन टाइम, ऑफ टाइम, पीक करंट आणि कपॅसिटन्सचे प्रमाण असे पॅरामीटर्स सेट केलेले असतात. डिस्चार्ज सुरू करून ड्रिलिंग सायकल सुरू केली जाते. ड्रिलिंग सायकल संपविताना डिस्चार्ज बंद केला जातो आणि ‘Z’ अक्ष कार्यवस्तूवरून वर उचलला जातो.
• ऑनटाईममुळे इलेक्ट्रोड आणि कार्यवस्तू यांच्यामधील विद्युत दाबाची (व्होल्टेज पल्स) वेळ ठरविली जाते. त्यामुळे अपेक्षित कार्यक्षमता देणारा ड्रिलिंगचा वेग मिळू शकतो.
• योग्य पद्धतीने ऑफ टाईमची निवड केली असल्यास पुढची ऑन टाईम पल्स कार्यान्वित करण्यास कटिंग करण्याचा भाग तयार होतो.
• सर्वोच्च विद्युत प्रवाह (पीक करंट) योग्यप्रकारे निवडल्यास सगळ्यात चांगले मटेरिअल, रिमूव्हल रेट आणि पृष्ठभागाचे उत्तम फिनिश मिळते.
• कमी वाहनक्षमता असलेल्या मटेरिअलमध्ये ड्रिलिंग करताना कपॅसिटन्स वापरला की कटिंग व्होल्टेजच्या पल्सला आवश्यक असलेली अतिरिक्त शक्ती (पॉवर बूस्ट) मिळते. या तंत्रामुळे मटेरिअल हीट ट्रीटमेंटला पाठविण्याची गरज भासत नाही. पारंपरिक पद्धतीने ड्रिलिंग करताना प्रथम ड्रिलिंग करून त्यानंतर ते हार्डनिंगसाठी हीट ट्रिटमेंटला पाठवले जाते.
ही प्रक्रिया सगळ्यांना माहिती होऊ लागल्यावर कठीण टूल स्टील, टंग्स्टन कार्बाईड, ॲल्युमिनिअम, ब्रास आणि इनकोनेल व्यतिरिक्त मटेरिअलमध्ये चाचणी करायला सुरुवात झाली. उच्च वेगाच्या या ड्रिलिंगचा वापर साचे आणि इतर उत्पादनात वाढत गेला. उदा. एअर व्हेंट होल्स, इंजेक्शन नॉझल्स, ऑईल ड्रेन होल्स, हायड्रॉलिक सिलिंडर्स, कोअर पिन्स, टर्बाईन ब्लेडस, बॉल बेअरिंग्ज आणि षट्कोनी (हेक्स) नट्समध्ये सेफ्टी वायर होल्स.
ड्रिलिंगसाठी लागणारा वेळ
छिद्राचा आकार आणि मटेरिअलचा प्रकार यानुसार ड्रिलिंगला लागणारा वेळ बदलत जातो. तक्ता क्र. 1 मध्ये संदर्भासाठी काही उदाहरणे दिली आहेत. साच्यांचे उत्पादन करताना पारंपरिक यंत्रणांऐवजी अति वेगवान इ.डि.एम. होल ड्रिलिंगचा वापर का केला जातो, हे तक्ता क्र. 1 मध्ये दिलेल्या वेळेवरून लक्षात येईल. दुसरी कोणतीही ड्रिलिंग प्रक्रिया वापरून कठीण मटेरिअलमध्ये कमी व्यासाचे ड्रिल मारणे अवघड असते. या ड्रिल प्रक्रियेमुळे कन्झ्युमेबलचा कमी खर्च होतो आणि हत्यार तुटण्याची शक्यता नसते. त्यामुळे इ.डि.एम. ड्रिल प्रक्रिया नक्कीच चांगला पर्याय आहे. या तंत्रामुळे केलेल्या छिद्रांना बर नसते. त्यामुळे नंतर पुन्हा डीबरिंग करण्याची गरज भासत नाही. मोठ्या आकाराच्या ड्रिल चक्समुळे स्टँडर्ड ड्रिल छिद्राची रेंज 0.3 मिमी ते 10 मिमी एवढी वाढली आहे. आता इ.डि.एम. ड्रिलिंग मॅन्युअल किंवा CNC मशिनवर करता येते. या तंत्रज्ञानात दिवसेंदिवस सातत्याने सुधारणा होत असल्यामुळे अधिकाधिक कामांसाठी याचा वापर होईल असे लक्षात येऊ लागले आहे. साचे आणि भाग बनविण्याची ही पूर्णपणे नवीन पद्धत आहे.
इ.डि.एम. ड्रिलिंग पद्धत निवडीसाठी खालील निकष लागू केले जातात.
• कार्यवस्तूचे मटेरिअल : इन्कोनेल, निमॉनिक, टिटॅनिअम, स्टील, कॉपर, टंग्स्टन, कठीण स्टील, कार्बाईडस, ॲल्युमिनिअम अलॉईज यांसारखे विद्युत वाहक धातू.
• कार्यवस्तूचा आकार : वर्क टेबलची रचना बंदिस्त नसल्यामुळे, नेहमीचे यंत्र जास्तीत जास्त 600 किग्रॅ वजनाच्या आणि 310 मिमीपेक्षा कमी उंची असलेल्या कार्यवस्तूवर काम करू शकते.
• छिद्राचा आकार/व्यास : स्पार्कोनिक्स स्टँडर्ड इ.डि.एम. ड्रिल मशिनवर कमीत कमी 0.3 मिमी व्यासाचे ड्रिल करता येते.
• छिद्राची लांबी/खोली : 1.5 मिमीपर्यंत व्यास असलेल्या इलेक्ट्रोडसाठी, जास्त अचूकतेसाठी व्यास आणि खोली यांचे गुणोत्तर 1:100 ठेवण्याची शिफारस करण्यात आली आहे. 1.6 मिमीपेक्षा जास्त आकारासाठी 300 मिमीची ड्रिलिंग खोली मिळवता येते. यासाठी 1:200 गुणोत्तर असावे.
इ.डि.एम. ड्रिलिंगचे फायदे
• इ.डि.एम.मध्ये पारंपरिक ड्रिलिंगमध्ये मिळणाऱ्या A11 टॉलरन्स च्याजागी 0.3 ते 1 मिमी पर्यंत D9 तर 1 मिमी ते 3 मिमी पर्यंत C11 टॉलरन्स मध्ये काम करता येते. मटेरिअलच्या कठीणपणाचा प्रक्रियेवर काही परिणाम होत नाही.
• टंग्स्टन कार्बाईड, निमॉनिक, इन्कोनेल या सर्व मटेरिअलचे इ.डि.एम.ने यशस्वीपणे यंत्रण करता येते.
• गुंतागुंतीचे आकार आणि पातळ वॉल थिकनेस असलेली कॉन्फिगरेशन आकार बिघडू न देता कापता येतात.
• इ.डि.एम. ही जॉबशी हत्याराचा प्रत्यक्ष संपर्क न येता आणि बल न वापरता काम करणारी प्रक्रिया असल्यामुळे पारंपरिक यंत्रणाचा ताण घेऊ शकत नसलेल्या नाजूक किंवा फुटणाऱ्या भागांसाठी अतिशय उपयुक्त आहे.
• यात कोणतीही बर मागे राहत नाही.
• या पद्धतीने फक्त विद्युत वाहक मटेरिअलचेच यंत्रण करता येते, ही या प्रक्रियेची मर्यादा आहे.
इ.डि.एम. ड्रिलिंग प्रक्रियेतील वेग आणि फीड रेट
80-100 किग्रॅ/सेमी2 गतीने उच्च दाबाखाली वाहणारे पाणी ही इ.डि.एम.मधील लक्ष ठेवण्यासाठीची महत्त्वाची प्रक्रिया आहे. ड्रिलिंग मटेरिअल आणि ड्रिल करण्याच्या छिद्राचा व्यास त्याप्रमाणे मोटर फीड आणि गती बदलण्याची गरज आहे.
सिरॅमिक/ रुबी गाईड यांचे काम आणि महत्त्व
इलेक्ट्रोड धारण करणारा चक (chuck) आणि वर्क टेबल यामधील अंतर 350 मिमीपेक्षा जास्त असते. इलेक्ट्रोडचा व्यास कमी असल्यामुळे इलेक्ट्रोड रन आऊट होतो आणि इलेक्ट्रोड रन आऊट कमीत कमी ठेवण्यासाठी खास रुबी गाईड किंवा सिरॅमिक गाईडसारख्या विद्युतरोधकाची गरज असते. त्यामुळे ड्रिल केलेल्या छिद्राच्या व्यासाची अचूकता जास्त चांगली राहते.
ऑपरेटरने घ्यावयाची खबरदारी
1. वर्कटेबल पृष्ठभाग स्वच्छ आणि गंज विरहित राहील याची काळजी घेणे.
2. ड्रिल ऑपरेशनमध्ये वापरलेले पाणी किंवा तेल योग्य पद्धतीने गाळलेले असावे. ते स्वच्छ असेल याची काळजी घेतली पाहिजे. जर गाळणी (फिल्टरेशन) व्यवस्था नसेल तर डाय इलेक्ट्रिक पाणी पुन्हा वापरू नये.
3. गाईड होल्डर आणि गाईड यांची योग्य अलाईनमेंट असणे आवश्यक आहे. दाब आणि बल न लावता रुबी गाईड, गाईड होल्डिंग विभागात घातले पाहिजे. गाईड होल्डरच्या आतील लंबगोलाकारपणा दर पंधरा दिवसांनी तपासला पाहिजे.
4. वाकलेले किंवा ब्लॉक असलेले इलेक्ट्रोड वापरू नयेत, कारण त्यामुळे नळीतून वाहणाऱ्या पाण्याच्या प्रवाहावर परिणाम होऊ शकतो.
shaileshsparkonix.com
शैलेश पटवर्धन स्पार्कोनिक्स (इंडिया) प्रा. लि. या कंपनीचे संचालक आहेत.