मेट्रॉलॉजी कंपनीने गेजिंग उत्पादन व्यवसायाला 1998 मध्ये सुरुवात केली. प्रथम या कंपनीने लिमिट गेजेसने व्यवसायाला सुरुवात केली. त्यानंतर एअर गेजेस, फिक्श्चरिंग आणि मल्टीपॅरामीटर्स असा विस्तार केला. गेजिंग व्यवसायातील एक नामांकित कंपनी म्हणून आज या कंपनीची ओळख आहे. गेजिंग म्हणजे काय, त्यात काळानुसार झालेले बदल, बाजारपेठ याविषयीची माहिती या लेखात देण्यात आलेली आहे.
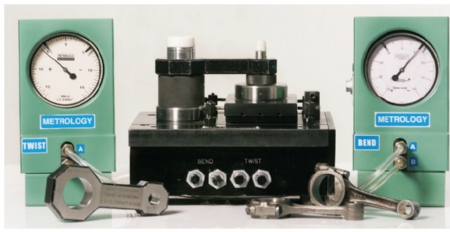
गेजिंग : मोजमापाची एक पद्धती
गेजिंग ही कार्यवस्तूचे अंतर तसेच इतर गुणवैशिष्ट्ये मोजण्याची पद्धती आहे. मेकॅनिकल गेजिंगमध्ये साधारणतः गो/नो-गो प्रकारचे प्लग गेजेस किंवा रिंग गेजेस येतात. यामध्ये तपासली जाणारी वस्तू अपेक्षित मापात आहे किंवा नाही ते समजते. दुसरी एक सूचक प्रणाली (इंडिकेटिव्ह सिस्टिम) असते, ज्यामध्ये प्रत्यक्ष मोजमाप मिळते याला आपण चल (व्हेरीएबल) असे म्हणतो. एअर गेजेस (नॉन काँटॅक्ट टाईप) आणि काँटॅक्ट टाईप गेजेस या सूचक प्रणालीमध्ये येतात. ’मेट्रॉलॉजी’ ही कंपनी प्रामुख्याने एअर गेजेस बनविते, मात्र आता ही कंपनी काँटॅक्ट टाईपकडेदेखील वळलेली आहे. एअर गेजेस आणि काँटॅक्ट टाईप गेजेसमध्ये अचूक मोजमाप मिळते, हा या प्रणालीचा मुख्य फायदा आहे. जेव्हा गो/नो-गो प्रकारचा प्लग गेज तपासला जातो तेव्हा तो जॉब चूक आहे की बरोबर आहे हे कळते. व्हेरिएबल गेजिंगमध्ये अचूक माप मिळाल्यामुळे नेमका फरक कुठे आहे ते कळण्यास मदत होते.
गेजिंगमध्ये अचूक रिडिंग मिळते, मग मोजमापाची साधने (इंस्ट्रुमेंट्स) आणि गेजिंग यातील नेमका फरक काय असा प्रश्न पडणे साहजिक आहे. मोजमापाची साधने ही सर्व प्रकारच्या उत्पादांना चालतात. व्हर्निअर, मायक्रोमीटर, टू डी, थ्री डी, सी.एम.एम. ही मोजमापाची साधने झाली. व्हर्निअरने आपण कोणतीही लांबी (लेंथ) मोजू शकतो, कोणताही व्यास मोजू शकतो. गेजिंगमध्ये मात्र तसे नसते. गेजिंग हे उपकरण फक्त त्या विशिष्ट भाग/उत्पादासाठीच बनविण्यात आलेले असते. मास प्रॉडक्शनसाठी गेजिंग हे उपकरण फायदेशीर ठरते. उदाहरणार्थ, जेव्हा कनेक्टिंग रॉड या कंपोनंटसाठी फिक्श्चर्स बनविण्यात येतात तेव्हा ते केवळ त्याच कनेक्टिंग रॉडच्या विशिष्ट मॉडेलसाठी बनविण्यात आलेले असतात. त्यामध्ये थोडा जरी बदल झाला तरी गेजिंग बदलावे लागते.
गेजिंग तंत्रज्ञानात काळानुसार झालेले बदल
पूर्वी गेजिंगमध्ये डायल टाईप इंडिकेटिंग युनिट असायचे. या युनिटवर ॲनालॉग माहिती (डाटा) मिळते. या माहितीवरून जॉबची मापे कळतात, मात्र ही माहिती (डाटा) तुलनात्मक असते. मूळ माप ’0’ असेल तर त्याच्या तुलनेत मोजले जाणारे माप कसे आहे ते समजते. सध्या तंत्रज्ञानात बदल झाला आहे. गेजिंगमध्ये इलेक्ट्रॉनिक्स उपकरणे वापरली जात आहेत. यामध्ये लाल, हिरवा आणि पिवळा अशा तीन रंगांची दर्शक प्रणाली वापरण्यात येते.
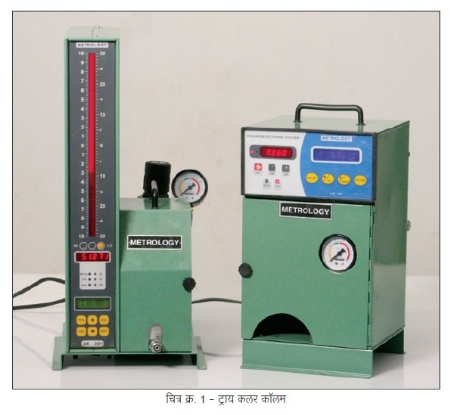
यात कंपोनंट जर ’रिजेक्ट’ असेल तर लाल रंग, कंपोनंट ’ओके’ असेल तर हिरवा रंग आणि जर ’रिवर्क’ करायचे असेल तर पिवळा रंग अशा पद्धतीने व्यवस्था करण्यात आलेली असते. या प्रणालीमुळे साध्या अकुशल कामगारालाही ती हाताळणे सोपे जाते आणि कंपोनंट अचूक तपासला जातो. त्यानंतर या प्रणालीमध्ये ’मेट्रॉलॉजी’ कंपनीने अशी रचना केली की, या दर्शकांऐवजी या तीन रंगांचे बार ग्राफ वापरले. उदाहरणार्थ, एखाद्या कंपोनंटचा अंतर्गत व्यास मोजताना जर व्यास बरोबर असेल तर, संपूर्ण बार ग्राफ हिरव्या रंगाचा होतो. व्यास मोठा असेल, तर बार ग्राफ लाल रंगाचा आणि व्यास कमी असेल, तर बार ग्राफ पिवळ्या रंगाचा होतो. या रचनेमुळे कंपोनंटमध्ये काही चूक असेल तर तात्काळ समजते. म्हणजेच या रचनेमध्ये दृष्य गुणवत्ता वाढविली. या रचनेला ’ट्राय कलर कॉलम’ असे नाव दिले. एक मायक्रॉनचा फरक आला तरी संपूर्ण बार ग्राफचा रंग बदलतो. त्यानंतर डाटा कलेक्शन ही पद्धत वापरण्यात येऊ लागली. यामध्ये तारीख, वेळ, शिफ्ट, कंपोनंटचे नाव आणि इतर तपशील नोंद करता येतो. या पद्धतीने त्या कंपोनंटचे सर्व पॅरामीटर, त्याची मापे आणि अंतिम परिणाम नोंदले जातात. म्हणजे जर तुम्हाला काही काळानंतर एखाद्या कंपोनंटची मूळ मापे पाहायची असतील तर ती सहजपणे पाहता येतात. यामध्येच आता संगणकीकृत यंत्रणा (पीसी बेस्ड सिस्टिम्स) आली. या यंत्रणेमुळे एकाचवेळी अनेक घटक (मल्टीपॅरामीटर) मोजता येऊ लागले हा मुख्य फायदा झाला. पूर्वी एका वेळी एकच घटक तपासला जात होता. जर 4 घटक मोजायचे असतील तर 1, 2, 3, 4 असे 4 वेगवेगळे स्टेशन्स आणि 4 वेगवेगळे यंत्रचालक (ऑपरेटर) यांची आवश्यकता भासायची. मात्र आता परिस्थिती बदलली आहे. एक यंत्रचालक जशा 3 मशिन हाताळतो, तसेच एक यंत्रचालक 2 किंवा 3 फिक्श्चर्स हाताळतो. एका फिक्श्चरमध्ये अंदाजे 2 ते 3 पॅरामीटर तपासले जातात. काही वेळेला 8-8 पॅरामीटरही तपासता येतात. आम्ही तयार केलेल्या एका फिक्श्चरवर 26 पॅरामीटर तपासता येतात. म्हणजेच एक ऑपरेटर 26 पॅरामीटर तपासतो.
फिक्श्चर्स
एक पॅरामीटर तपासणाऱ्या गेजला ’नॉर्मल गेज’ म्हटले जाते. फिक्श्चर हा अनेक पॅरामीटर तपासणारा एक पूर्ण सेट असतो. उदाहरणार्थ, सी.एम.एम.सारख्या यंत्रावर एका कंपोनंटला तपासण्यासाठी 4-5 मिनिटे लागत होती. त्याच्या तुलनेत आम्ही केलेल्या फिक्श्चरमध्ये टेबल ते टेबल फक्त 3 सेकंदामध्ये हे सर्व पॅरामीटर तपासले जातात. गेजिंगचा असाही फायदा आहे की, ही यंत्रणा मशिनच्या शेजारी लावण्यात आलेली आहे. यामुळे तात्काळ परिणामही मिळतात. जर काही चूक झाली असेल, तर या यंत्रणेमुळे तिथल्या तिथे मशिनवरच ती दुरुस्त करता येते. यापूर्वी एके ठिकाणी जॉब तपासण्यात येत होता. जर त्यात काही चूक असेल तर, शॉप फ्लोअरकडे किंवा उत्पादकाकडे प्रत्यक्ष जाऊन सांगावे लागत होते की, तो जॉब ओव्हरसाईज आहे किंवा अंडरसाईज आहे. त्याप्रमाणे त्यात दुरुस्ती केली जायची. तो तपासला जायचा आणि मग त्यानंतर त्या जॉबचे उत्पादन सुरू व्हायचे. यामध्ये खूप वेळ जायचा. आता मात्र तसे नाही. या कंपनीने यावर उपाय शोधून काढला. या प्रक्रियेत जॉब तपासला की, सॉफ्टवेअरद्वारे मशिनला प्रतिक्रिया देण्यात ये ते. पुढील आवर्तन चालू होण्यापूर्वी जॉब जर अंडरसाईज किंवा ओव्हरसाईज असेल, तर त्याप्रमाणे मशिनला सूचना दिलेली असते. मशिन त्यानुसार काम करते. या सूचनांद्वारे जो कंपोनंट बनतो, तो बरोबरच बनतो.
एअर प्लग गेजेस
एअर प्लग गेजेसमध्ये व्यास (डायमीटर) कसा तपासायचा आणि कुठे तपासायचा या दोन्ही गोष्टी येतात. बऱ्याचदा एअर गेजिंग वापरताना ते 2 जेटेड वापरायचे, 3 जेटेड वापरायचे की, 4 जेटेड वापरायचे हे समजत नाही. अनेकदा व्यास तपासताना त्याठिकाणी तो लंबगोल असू शकतो. त्याचप्रमाणे 3 लोब असण्याची शक्यता असते. त्यामुळे अशा प्रकारच्या तपासणीत व्यासाबरोबरच लोबही तपासणारा, आवश्यक तेवढा जेटेड गेज वापरणे गरजेचे ठरते.
प्रतिदाब (बॅक प्रेशर) हे एअर गेजचे मूळ तत्त्व आहे, ज्याला ’नल बॅलन्स प्रिंसिपल’ असे देखील म्हणतात. याचा अर्थ असा आहे की, आत जाणारी हवा आणि जेट्समधून बाहेर पडणारी हवा या दोन्ही समान पाहिजेत. ज्यावेळेला एअर गेजिंग वापरले जाते, तेव्हा पाहिजे तितके बॅक प्रेशर मिळाल्यामुळे दोन्ही म्हणजे आतमध्ये जाणारी हवा आणि बाहेर पडणारी हवा या दोन्ही सारख्या असतात. या नल बॅलन्समुळे अचूक रिडिंग मिळते.
बॅक प्रेशर आणि बाहेर जाणारी हवा यांचे सेन्सिंग होते. बॅक प्रेशरमुळे नीडल उचलली जाते आणि त्यामुळे रिडिंग दिसते. मुळात एअर गेजिंग ही तुलनात्मक पद्धत (कंपॅरिटीव्ह मेथड) आहे. यामध्ये ’हाय’ आणि ’लो’ अशा पातळ्या सेट केल्या जातात. कसे ते उदाहरणाद्वारे (आकृती क्र. 1 ) समजून घेऊ.
समजा प्लस 20 किंवा मायनस 20 मायक्रॉन्स अशा ’हाय’ आणि ’लो’ पातळ्या सेट केल्या, ’हाय’मध्ये म्हणजे प्लस 20 ला 3 किलोग्रॅम हे बॅक प्रेशर मिळत असेल आणि मायनस 20 ला 2 किलोग्रॅम बॅक प्रेशर मिळत असेल, तर जेव्हा 2.5 किलो ग्रॅम बॅक प्रेशर मिळते, म्हणजे ते 0 फरकाचे माप असते.
स्पेशल मल्टी गेज सिस्टिम
विशिष्ट जॉबसाठी एकाचवेळी अनेक मापे तपासणारी ही प्रणाली आहे. वाहन उद्योगासाठी लागणाऱ्या विविध भागांसाठी ही प्रणाली कशी काम करते ते आपण थोडक्यात पाहू.
पिस्टन
एका वाहने तयार करणाऱ्या कंपनीतील पिस्टन तपासणीसाठी आम्ही ही प्रणाली बनविली. पिस्टन बोअरमध्ये दोन भाग असतात. ते सलग नसून त्यांच्यामध्ये काही जागा असते. त्यामध्ये मँड्रिल घातले जाते, ज्याच्यामुळे तो समकेंद्री आहे, याची खात्री करण्यास मदत होते. त्याच वेळेला त्याचा 4 टप्प्यांमध्ये व्यास तपासला जातो. (आकृती क्र. 2) यामुळे व्यास आणि त्याची ओव्हॅलिटी कळते. कारण गजन पिन बोअरवर सगळी अचूकता अवलंबून असते. गजन पिनला साधारणतः +5 मायक्रॉनचा टॉलरन्स असतो. अशा अवघड परिस्थितीमध्ये काम करायचे असेल, तर त्यासाठी मल्टी जेट्सची आवश्यकता भासते. यामध्ये एकापेक्षा अधिक जेट्स एकापेक्षा अधिक व्यास एकाच वेळेला तपासतात.
• पिस्टनमध्ये 12-15 अवघड पॅरामीटर्स असतात. त्यामुळे हा गुंतागुंतीचा कंपोनंट आहे.
• पिस्टनचा अंतर्गत व्यास आणि बाह्य व्यास (तो पॅराबोलिक आकाराचा असून टॉप, मिडल आणि बॉटम हे तीन व्यास)
• पिस्टनचा प्रत्येक ग्रूव्ह (जेवढ्या पिस्टनच्या रिंग बसणार असतात त्या प्रत्येक रिंगचा ग्रूव्ह व्यास), ग्रूव्ह रुंदी, गजन पिन बोअर (गजन पिनच्या संदर्भाने त्याची उंची, ज्याला काँप्रेशन हाईट म्हणतात.) हे पॅरामीटर्स असतात.
सिलिंडर ब्लॉक
यात ब्लॉकच्या सिलिंडर बोअरची लांबी ही साधारणतः 100 ते 125 मिमी असते. यात 4 जेट्स लावलेले असतात. त्यानुसार 1, 2, 3, 4 असे 4 दर्शकदेखील असतात. म्हणजे एकावेळेला 4 टप्प्यांवर व्यास तपासले जातात. यामुळे कंपोनटची प्रोफाईल मिळते. म्हणजे तो अंतर्वक्र आहे, बहिर्वक्र आहे, एका बाजूला टेपर आहे, दुसऱ्या बाजूला टेपर आहे (आकृती क्र. 3) या गोष्टी कळतात. हे केवळ मल्टीजेट्समुळे साध्य होते. एअर गेजिंगने कोणताही भौमितिक घटक तपासता येतो. कधी कधी स्क्वेअरनेस, कॉन्सेन्ट्रिसिटी, रनआऊट हे पॅरामीटर तपासले जाऊ शकतात.
कनेक्टिंग रॉड मोजणी
’मेट्रॉलॉजी’ कंपनीने हा ’हिरो मोटोकॉर्प’साठी केलेला प्रकल्प आहे. त्यांच्या कनेक्टिंग रॉडसाठी आधी वापरली जाणारी गेज अंदाजे 35 लाख रुपयांची होती. मार्किंग मशिन धरून त्याची किंमत अंदाजे 50 लाख रुपयांच्या आसपास होती.
बिग एंड बोअरचा संदर्भ घेऊन या कंपनीने ही मशिन विकसित केली. कनेक्टिंग रॉडमध्ये बिग एंड बोअरच्या आतमध्ये केज बेअरिंग बसते. त्या केज बेअरिंगमध्ये क्रँकशाफ्टची क्रॅँक पिन बसलेली असते आणि स्मॉल एंड खाली पिस्टनच्या बाजूला असतो. बिग एंड बोअरचे मोजमाप करणे ही अत्यावश्यक बाब बनते. त्यासाठी जी वास्तविक साईझ आहे ती मोजावी लागते. याचबरोबर या मल्टीगेजिंग प्रणालीमध्ये ऑटोग्रेडिंग होते. कनेक्टिंग रॉडमध्ये बेअरिंग फिटमेंट असल्यामुळे तो 360 अंशामध्ये फिरवला की त्याचा राऊंडनेस कळतो. एका ठिकाणी व्यास तपासला तर कदाचित त्याठिकाणी मापे अचूक असतील. मात्र त्याच्या 90 अंशामध्ये मापे मर्यादेच्या बाहेर असण्याची शक्यता असते. इंजिनच्या आवश्यक मोजमापावर +14 मायक्रॉनचा टॉलरन्स आहे. या ऑटोग्रेडिंग सिस्टिमवर जॉब 360 अंशामध्ये फिरतो. पूर्ण एक आवर्तन (सायकल) झाल्यानंतर ग्रेडिंग होते. ग्रेड मार्किंग ही व्यासाच्या आधारे होते. मिनिमम आणि मेजर व्यासावरून त्याची ओव्हॅलिटी मोजली जाते. कमीत कमी व्यासाच्या आधारे त्याची ग्रेडिंग ठरते. बिग एंड डायाला ग्रेडिंग होते. स्मॉल एंडमध्ये गजन पिन बसते आणि तो कंपोनंट पिस्टनमध्ये जातो. ग्रेड कनेक्टिंग रॉडवर छापली जाते. या यंत्रणेमध्ये 2 मायक्रॉनची ग्रेड आहे, 0.1 मायक्रॉन लीस्ट काऊंट आहे, 0.2 मायक्रॉन अचूकता आहे. हे मार्किंग कायमस्वरुपी असून 0.1 मायक्रॉन जरी पुढे गेला तरी ग्रेड बदलते. जेव्हा हे इंजिन बिघडते आणि दुरुस्तीसाठी येते तेव्हा नेमकी कोणती ग्रेड आहे हे सांगणे अनेकदा कठीण जाते. जर कायमस्वरुपी मार्किंग केलेले असेल तर दुरुस्तीच्यावेळी काही अडचण आली तर ती ग्रेडिंगमुळे सहजपणे कळते.
यात a,A,B,C,D,E,F अशा ग्रेड्स आणि 14 मायक्रॉन टोटल टॉलरन्स आहे. त्यामुळे 2 मायक्रॉनची एक ग्रेड होते. ग्रेडिंगनुसार बेअरिंग फिटमेंट होते. त्यानुसार क्रॅँक पिनची निवड होते. म्हणून यामध्ये ग्रेडिंग महत्त्वाचे आहे.
या यंत्रणेमध्ये मानवावरचे अवलंबित्व आणि तपासण्याची वारंवारिता (रिपिटेशन ऑफ चेकिंग) पूर्णतः काढून टाकली. कारण 1 कंपोनंट 10 वेळा तपासला तर त्यामध्ये 10 वेगवेगळे रिडिंग येण्याची शक्यता असते. तसेच ’मेट्रॉलॉजी’ने तयार केलेल्या यंत्रणेमध्ये जॉब कसा फिरविला जातो हे महत्त्वाचे ठरते. जर वर्तुळ 360 अंशांमध्ये विभागले तर, एका अंशाला एक रिडिंग घेतले तर 360 रिडिंग मिळणार आहेत. तेवढे रिडिंग स्कॅन करून ’मिनिमम’ आणि ’मॅक्सिमम’ रिडिंग काढण्यात येते. सर्वात कमी व्यासाच्या आधारावर ग्रेड काढली जाते. फ्लोअर ते फ्लोअर 9 सेकंदाचा वेळ आहे. एका शिफ्टमध्ये 1800 ते 1900 कंपोनंट बनविले जातात. यानुसार अंदाजे 4 कंपोनंट मिनिटाला तपासले पाहिजे, अशी ग्राहकाची मागणी होती. त्यामुळे 6 सेकंद हा वेळ मार्किंगसाठी आणि बाकीच्या गोष्टींसाठी 3 सेकंद असा 9 सेकंदांचा वेळ फ्लोअर ते फ्लोअर ठरविण्यात आला.
या यंत्रणेमुळे झालेले फायदे
• कमी खर्चात कंपोनंट तपासला जातो.
• रिजेक्ट झालेला एकही कंपोनंट अॅसेम्ब्ली लाईनधून जात नाही.
• अचूक मोजमाप होते.
• कायमस्वरुपाचे मार्किंग होते.
• माहितीची नोंद होते.
• एकच फिक्श्चर 8 मॉडेलसाठी वापरता आले.
गेजिंग व्यवसायामध्ये मागील 28 वर्षांपासून असलेली ही कंपनी मागील 10 वर्षांपासून इलेक्ट्रॉनिक्स आणि सॉफ्टवेअर प्ऱणाली वापरून 0.1 मायक्रॉन लीस्ट काऊंटवरदेखील काम करत आहे. थेट ग्राहकाच्या गरजा समजून घेऊन त्याप्रमाणे गेज तयार करणे, हे या कंपनीचे वैशिष्ट्य आहे.
विशाल पवार हे अभियांत्रिकीचे पदवीधर असून त्यांनी व्यवस्थापन क्षेत्रामध्येदेखील पदव्युत्तर पदवी पूर्ण केली आहे. सध्या ते मेट्रॉलॉजी या कंपनीची धुरा सांभाळत आहेत.