फाउंड्रीमध्ये वितळलेल्या धातूच्या रसाचे तापमान मोजण्यासाठी थर्मोकपल वापरले जातात. हे एकदा वापरून फेकावे लागत असल्याने त्याचे उत्पादनही मोठ्या प्रमाणात करावे लागण्याची गरज असते. याचे उत्पादन करणाऱ्या कंपनीने हे उत्पादन वाढविण्याचे ठरविले पण त्यासाठी चालू पद्धतीमध्ये दर्जा, वेळ आणि लागणारे श्रम या सर्व बाबी सुधारणे आवश्यक होते.त्यामुळे याचा सर्वांगीण विचार करून उपाय शोधला गेला.
थर्मोकपल जोडणी
जुनी पद्धत
पूर्वीच्या पद्धतीमध्ये ऑपरेटर लोखंडी कॅप एका खड्ड्यामध्ये ठेवत होता. त्याच्यावर थर्मोकपलचे टिप ठेवून त्यावर एक टूल हातोडीच्या सहाय्याने मारून पंच करण्यात येत होते. ही सगळी प्रक्रिया मॅन्युअली होत होती. त्यामुळे अंतिम उत्पादन फार कमी मिळत होते.
ऑपरेटरला येणाऱ्या अडचणी
• हाताच्या साहाय्याने मारून पंच केल्यामुळे ऑपरेटरचे हात दुखायचे.
• कमी काम व्हायचे आणि तिथे ऑपरेटर काम करायला नाराज असायचे. तर काही वेळेला त्याच्याकडून चुकीचे काम केले जायचे.
या अडचणींवर अभ्यास करण्यात आला. त्यात असे आढळून आले की, ऑपरेटरला होणारा त्रास कमी करायचा असेल, तर हे पंचिंग हायड्रॉलिकली किंवा न्युमॅटिकली प्रेस केल्यास फायदेशीर ठरेल. मात्र दाबाचा (प्रेशर) अभ्यास करता, हे पंचिंग न्युमॅटिकली शक्य आहे, असे लक्षात आले. त्यानुसार या प्रक्रियेसाठी न्युमॅटिक प्रेस डिझाईन करण्यात आले.
नवीन पद्धत
कंपनीची गरज दिवसेंदिवस वाढत होती. त्यामुळे उत्पादन क्षमता दुप्पट करण्यात यावी असा निर्णय घेण्यात आला. त्यासाठी एकूण आवर्तन काल (सायकल टाईम) किती लागेल याचा अभ्यास करण्यात आला. त्यानुसार 2 सेकंद हा आवर्तन काल निश्चित करण्यात आला. मात्र या 2 सेकंदाच्या काळात प्रेसिंग, टेस्टिंग, लोडिंग आणि अनलोडिंग होणे गरजेचे होते. या सर्व प्रक्रियेसाठी हे चारही ऑपरेशन्स समांतर करण्याचे ठरले. मग हे 4 ऑपरेशन्स समांतर करण्यासाठी इंडेक्सिंगची मदत घेण्यात आली. त्यासाठी 16 स्टेशनचे इंडेक्सिंग डिव्हाईस डिझाईन करण्यात आले. यामुळे आता असे होते की, ऑपरेटर एका वेळी एका खड्ड्यात एक कॅप ठेवतो. त्याच्यावर एक थर्मोकपल ठेवण्यात येते. त्याला मिनिटाला 30 जॉब लोडिंग करावे लागतात. नवीन पद्धतीमुळे ते आता सहजपणे शक्य होत आहे. ॲसेम्ब्ली पुढे गेल्यानंतर टेस्टिंगचे टूल वरील बाजूने खाली येते आणि जॉबला स्पर्श करून त्याची विद्युत सलगता (कंटिन्युटी) तपासत असते. त्याची सलगता बरोबर असेल, तर त्याच्या पुढच्या प्रेसला सिग्नल दिला जातो आणि त्याच्या पुढच्या स्टेशनला ते ऑटोमॅटिकली प्रेस होते. सलगता जर बरोबर नसेल तर त्याठिकाणी प्रेस होत नाही. त्याठिकाणी ते सोडून देण्यात येते. त्याच्यापुढे ’रिजेक्ट स्टेशन’ असते. ’रिजेक्ट स्टेशन’मध्ये इजेक्टरच्या रॉड खालून एक न्युमॅटिक सिलेंडर दिला आहे जो रॉडची हालचाल करून जॉबला उडवून बाहेर काढतो. हा जॉब प्रेस झालेला नसल्यामुळे त्याला काही ऑपरेशन करायचे असेल किंवा त्यावर काही ’रीवर्क’करायचे असेल तर ते शक्य होते. पुढच्या स्टेशनमध्ये योग्य जॉब बाहेर काढला जातो. जर टेस्टिंग स्टेशनला जॉब बरोबर झालेला असेल, त्याचे प्रेसिंग पण झालेले असेल तर या इजेक्टर स्टेशनवर जॉब बाहेर येतो. त्याला पुढे उतार करून त्याच्यासमोर एक ट्रे ठेवलेला असतो. हे सर्व जॉब ट्रेमध्ये भरले जातात. असे 500 जॉब झाले की, एक दिवा पेटतो आणि तो पेटलेलाच राहतो. दुसरा ऑपरेटर येवून तो ट्रे काढतो आणि दुसरा ट्रे लावतो. पहिला ऑपरेटर मात्र मिनिटाला 30 च्या हिशोबाने कॅप्स आणि थर्मोकपल हे दोन्ही एकमेकांत ठेवत असतो. एका मिनिटाला 30 जॉब या हिशोबाने अतिशय सुसंगत उत्पादन मिळायला लागले. नाकारले गेलेले जॉब जागच्या जागीच बाजूला व्हायला लागले. त्यामुळे ऑपरेटरचे ते काम कमी झाले आणि ग्राहकाकडे फक्त चांगलाच जॉब जाऊ लागला.
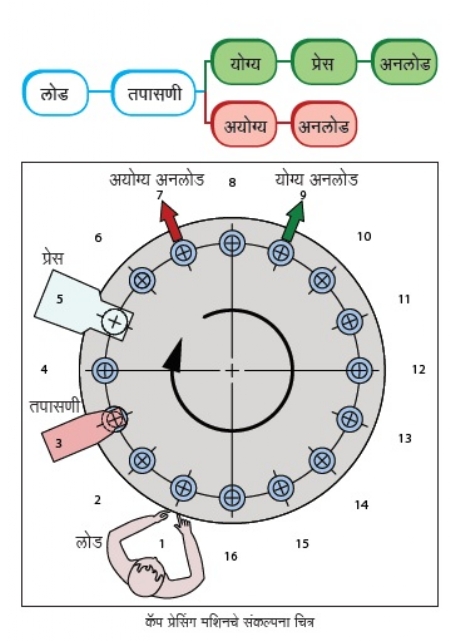
न्युमॅटिक प्रेस असल्यामुळे एका ठराविक दाबाखालीच प्रेसिंग होते आणि मेकॅनिकल टूल असल्यामुळे प्रेसिंगचे सातत्य मिळायला मदत झाली. सर्व जॉब एकसारखे प्रेस व्हायला लागल्यामुळे प्रेसिंगसाठी जॉब नाकारला जाण्याचे प्रमा़ण पूर्णपणे नाहीसे झाले. एका ट्रेमध्ये 500 जॉब ऑटोमॅटिकली मोजलेदेखील जाऊ लागले. ऑपरेटरचे तेही एक काम वाचले. या एका ऑटोमेशनमुळे हे सर्व फायदे झाले.
प्रसन्न अक्कलकोटकर यांत्रिकी अभियंता असून त्यांना या क्षेत्रातील 25 वर्षांहून अधिक अनुभव आहे.