अलीकडे भारतामध्ये शॉप फ्लोअर स्वयंचलनावर अधिक भर दिला जात आहे. सुरुवातीला 3 अक्षांच्या हालचाली संगणक नियंत्रित करण्यापासून आजपर्यंत यामध्ये मोठी प्रगती केली आहे. लघु- मध्यम उद्योगांत (SME) 4-5 अक्ष नियंत्रित करणाऱ्या मशिन्स वापरल्या जातात. त्याबरोबरच कार्यवस्तूचे लोडिंगदेखील यंत्रमानवाद्वारे केले जाते. ऑटो पॅलेट चेंजर, ऑटो गेजिंग हे प्रकारदेखील आता लघु-मध्यम उद्योग क्षेत्रात वाढले असून भविष्यातही ते वाढत जातील, यात शंका नाही. ज्या प्रमाणात आपण यांत्रिकीकरण वाढवून त्यातील मानवी हस्तक्षेप टाळण्याचे प्रयत्न करू तसतसे आपणास खात्रीशीर उत्पादन मिळण्यास मदत होणार आहे. अचूक आणि खात्रीशीर उत्पादन मिळावे हा उद्देश समोर ठेवून याकडे अधिकाधिक लक्ष देणे गरजेचे आहे. ज्यावेळी मानवी संवेदनशीलतेवर आधारित काम होते, त्यावेळी काही गोष्टी तपासत कामाची प्रगती होत असते. मात्र, यांत्रिकीकरणाकडे आपण वळत असताना एखादी गोष्ट एकसारखी आणि एकाच पद्धतीने होणार याची खात्री होणे गरजेचे असते.
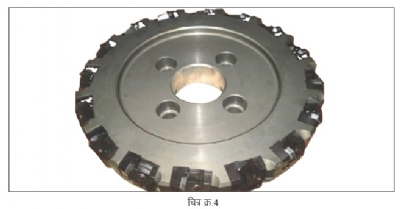
फिक्श्चर्स, टूल्स, गेजेस याबाबतीत बोलायचे झाले तर, फिक्श्चर्सवर कार्यवस्तू नीट बसते का? त्याच्या लोकेशन पिनमध्ये व्यवस्थित प्रवेश होतो का? क्लॅम्प झाल्यावर कुठे अंतर राहत नाही ना? विशेषतः जिथे रेफरन्स फेस आहे त्याचा आधार व्यवस्थित आहे की नाही, या सगळ्याची खात्री काम सुरू होण्यापूर्वी करून घेणे गरजेचे आहे. त्याबरोबरच अशा मशिन्सवर जे टूल्स वापरण्यात येणार आहेत, त्या टूल्सबाबतही सतर्क असणे आवश्यक आहे.
सर्वप्रथम टूलचे आयुष्य किती आहे हे ठरविले पाहिजे. टूल उत्पादकाच्या सल्ल्याने स्पीड, फीड अशा गोष्टी ठरवून घ्याव्यात. त्यानंतर उत्पादकाने ठरवून दिल्याप्रमाणे त्याच्या आसपास जे टूल लाईफ मिळेल त्याची नोंद करून ठेवावी. आपल्या सेटवर जे टूलचे आयुष्य मिळेल तोच आपला मानदंड ठरवावा. त्याआधारे त्या मापाच्या 90% ते 95% वर आपली टूल बदलण्याची वेळ ठरवावी. त्यामुळे टूल तुटण्याची किंवा जॉब चुकण्याची शक्यता नसते.
आज बाजारपेठेत टूल तयार करणाऱ्या अनेक देशी आणि परदेशी कंपन्या आहेत. त्यामुळे 2-3 कंपन्यांची टूल्स प्रत्यक्ष वापरून मगच ती खरेदी करण्याचा निर्णय घ्यावा. प्रत्येक वेळी वेगवेगळ्या कंपनीच्या टूल्सचा वापर केल्यास टूल बदलाचा आपला मानदंड ठरवण्यास अवघड जाते.
परदेशातील मशिन्सवर ब्रेकेज संवेदक, अतिभार संवेदक वगैरे असतात, मात्र बहुतेक मशिनसाठी आज तरी तो परवडणारा पर्याय नाही. काही महागड्या मशिनसाठी विशेषकरून अंतर्गत काम असलेल्या मशिनवर असे संवेदक दिसतात. पिझ्झो इलेक्ट्रिक सेन्सॉर्स, मशिनच्या स्लाईडखाली लावून त्याद्वारे कटिंगचा दाब मोजला जातो. त्यानंतर ते मशिनच्या संगणक प्रणालीशी जोडून कुठपर्यंत दाब वाढल्यास मशिन बंद करायची ते ठरवले जाते.
टूलचे अंगभूत गुण व लेपन प्रक्रियेने (कोटिंग) यामध्ये योग्य ती वाढ करणे अत्यावश्यक आहे. कारण यांत्रिकीकरणाच्या कार्यप्रणालीमध्ये मशिनची मूळ किंमत वाढते. त्यामुळे जर कार्यवस्तू परवडणाऱ्या दरात करायची असेल तर ती कमीत-कमी वेळेत झाली पाहिजे.
मशिनच्या वेळातील सर्वाधिक वेळ घेणाऱ्या कामाचा व्यवस्थित अभ्यास करून त्यामध्ये योग्य तो बदल करून वेळ वाचवला पाहिजे. तर काही क्रियांचे (ऑपरेशन) एकत्रीकरण केले पाहिजे.
केस स्टडी 1
येथे चित्र क्र. 1 मध्ये दाखविल्याप्रमाणे कंपोनंटचा एक कान 35 - 0.036 मिमीमध्ये हवा होता. दोन्ही बाजूच्या त्रिज्यांमध्ये फरक होता. एका बाजूस कड त्रिज्या (कॉर्नर रेडियस) आवश्यक होती. त्याकरिता वर वेगळा व खाली वेगळा असे 2 कटर वापरले जात होते. कटरची स्वतःची व मशिनची ट्रॅव्हल ॲक्युरसी एकत्र घेता, हव्या त्या मर्यादेमध्ये कार्यवस्तू येत नव्हती. व्ही.एम. सी.वर सातत्याने कार्यवस्तूचे उत्पादन घ्यायचे असल्याने मध्ये तपासणे शक्य नव्हते. यासाठी विविध पायऱ्यांवर त्या टूल सेटमध्ये बदल घडवून आणले.
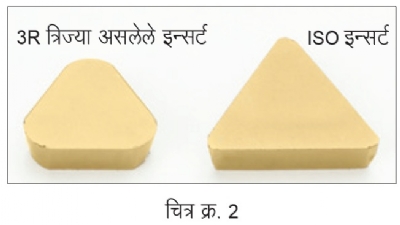
प्रथम एका बाजूस जेथे 1 मिमी त्रिज्या होती. ती मिलिंग इन्सर्टच्या अंगीभूत कोनामुळे होणार हे ठरवले. तेथे कापायच्या बाजूस जास्तीत जास्त 5 मिमी इतकेच मटेरियल असल्याने तेथे 16 मिमीची इन्सर्ट वापरली. दुसऱ्या बाजूस कोपरा त्रिज्या (कॉर्नर रेडियस) 3R होती. त्या बाजूस मटेरियलही जास्त होते. त्या बाजूसाठी 22 मिमीची इन्सर्ट वापरून त्यास 3R ग्राईंड करून घेतले (चित्र क्र. 2) आणि तेदेखील 0.005 ते 0.007 या मर्यादेमध्ये व त्यांच्या सातत्यासाठी तपासणीची व्यवस्था केली. तसे पाहता 3Rच्या काही इन्सर्ट बाजारात मिळतात. पण किंमतीचा विचार करता ISO इन्सर्टस् वापरणे भाग होते. आम्ही सहज मिळणारे ISO इन्सर्टस् घेवून ग्राईंड करताना त्याच्या ग्राईंडिंगची गुणवत्ता बदलली व विेशसनीयता वाढविली व कटरमध्ये अक्षीय समायोजन (ॲक्सियल ॲडजस्टमेंट) दिले. तरीही त्या मर्यादेमध्ये कार्यवस्तू येण्यास त्रास होत होता व जास्त वेळ लागत होता. यावर उपाय म्हणून चित्र क्र. 3 मध्ये दाखविल्याप्रमाणे दोन कटर, वरचा Ø 180 मिमी खालचा, Ø 201.2 मिमी एकत्रित केले. त्यामुळे दोन्ही बाजूचे अंतर (डेप्थ) एकदम करणे शक्य झाले. मध्ये असलेल्या जागेचा वापर करून 35-0.036 मिमी या मर्यादेपेक्षा कमी कटरवरच आणून ठेवले. त्यामुळे एका पासमध्येच हे साईज करणे जमले. अशाप्रकारे प्रत्येक पायरीवर विेशासकता वाढवत, दोन कामांचा संयोग केल्याने अडचण दूर झाली. तसेच वेळेतही 32% बचत झाली तो फायदा वेगळाच.
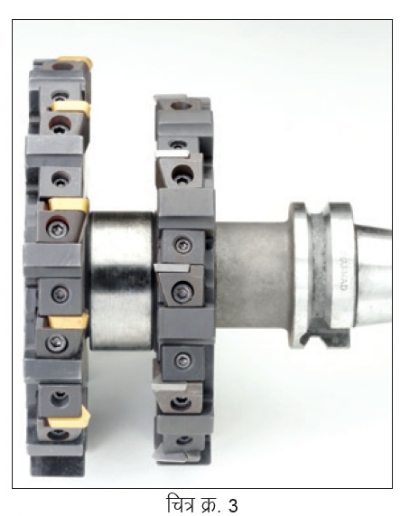
अशाप्रकारे 2 किंवा त्यापेक्षा अधिक कामे एका पासमध्ये करण्याची असंख्य उदाहरणे देता येतील. सूत्राप्रमाणे विचार केल्यास रफिंग + स्टेप्स + चँफर्स एकत्र करून फिनिशिंगचे काम स्वतंत्रपणे करणे. या साध्या व सोप्या सूत्राचा वापर केल्यास वेळेची बचत होते आणि मशिन किंमत जास्त असतानाही जॉब माफक खर्चात करता येतो.
मशिनिंग करताना चिप व्यवस्थापन अत्यंत महत्त्वाचे असते. कारण फाईन बोअरिंग करतेवेळी चिप तुटतात, याबाबत खात्री हवी. चिप टुलभोवती गुंडाळून त्याचे फिनिशिंग बिघडते. त्यासाठी योग्य प्रकारचे चिप ब्रेकर प्रोफाईल शोधून त्यावर स्पीड आणि फीड ठेवावा.
केस स्टडी 2
एका एच.एम.सी. मशिनवर खूप मटेरिअल एका छिद्रात आतमध्ये काढायचे होते. त्यात एवढ्या चिप जमा होत्या, की त्या बाहेर काढणे मोठे जिकिरीचे काम होते. निम्म्या आवर्तनानंतर (सायकल) एका पाईपमधून जोरदार शीतक फिरवता येईल अशी सोय करून त्याद्वारे चिप बाहेर फेकली गेल्यावर ही अडचण आटोक्यात आली. ड्रिलिंगबाबतीतही चिप बाहेर येईल याची काळजी घ्यावी लागते.
केस स्टडी 3
अनेकदा बोअरिंगबरोबर त्यास लागून असलेल्या फेसचे काटकोनाचे प्रमाण दिलेले असते. ज्यावेळी फेस फारसा मोठा नसतो त्या ठिकाणी बोअरिंगनंतर लहान कटर फिरवून हे साधता येते. मोठ्या फेसची काटकोन मिती अडचणीची ठरते, कारण एच.एम.सी.च्या स्पिंडल आणि एटीसीची वजन धरण्याची क्षमता मर्यादित असू शकते.
एका मोठ्या ISO 50 टेपर असलेल्या एच.एम.सी.साठी Ø 70 मिमी बोअरच्या बाजूचा फेस असाच काटकोनात पाहिजे होता आणि फेस Ø 263 मिमी पर्यंत करून हवा होता. बोअर करून झाल्यावर Ø 276 मिमीचा कटर फिरवणे आवश्यक होते. याठिकाणी कटरची बॉडी ॲल्युमिनिअममध्ये बनवून आम्ही ते साध्य केले. (चित्र क्र. 4) अर्थात कटर एटीसीमध्ये बसणे शक्य नव्हते. त्यामुळे तो स्पिंडलमध्ये परस्पर बसवावा लागला.
अलीकडे ॲल्युमिनिअमच्या कार्यवस्तूचा वापर वाढला आहे. ते करत असताना कर्तन वेग (कटिंग स्पीड) जास्त वापरावा लागतो. बरेचदा डायमंड (पीसीडी) वापरणे रास्त ठरते. अशा ठिकाणी हलक्या वजनाचे कटर वापरून जास्त वेग मिळवता येतो.
मशिन, वर्क मटेरिअल, कार्यवस्तूची रचना या सगळ्यांचा विचार करून वरीलप्रमाणे उपाय योजल्यास व टूलद्वारे मशिनच्या क्षमतेचा कमाल वापर करून यांत्रिकीकरणाची जी जास्तीची किंमत आहे, त्यावर मात करून आपण किफायतशीर उत्पादन घेऊ शकतो.
दत्ता घोलबा ‘मानस इंजिनिअरिंग’ कंपनीचे संस्थापक संचालक असून, 44 वर्षांपासून कटिंग टूल्स या विषयाशी निगडित कार्य करत आहेत.