कार्यवस्तूवर यंत्रण करताना ते उत्तम प्रकारे होण्यासाठी काही आवश्यक साधने वापरली जातात. उदाहरणार्थ, शीतक (कुलंट), कटिंग ऑईल, होनिंग ऑईल इत्यादींमुळे फिनिशिंग चांगले होण्यासाठीही मदत होते. शीतक कार्यवस्तूवरून पुढे जाताना, त्यात काही प्रमाणात ऑईलही मिसळले जाते. औद्योगिक क्षेत्रामध्ये वस्तूंचा सर्वोत्कृष्ट वापर करण्यावर अधिक भर दिला जात असल्यामुळे एकदा वापरलेले शीतक पुन्हा वापरण्यास प्राधान्य दिले जाते, मात्र त्यामध्ये मिसळल्या गेलेल्या ऑईलमुळे कामात अडचणी येऊ शकतात. उदाहरणार्थ,
1) सरफेस फिनिशिंग यथायोग्य नसणे.
2) शीतकाच्या टाकीत होणाऱ्या बॅक्टेरियाच्या निर्मितीमुळे पसरणारी दुर्गंधी; परिणामी अनुत्साही वातावरण.
3) शीतकाच्या उष्णतावहन क्षमतेमध्ये होणारी घट.
4) अशा शीतकाच्या सतत संपर्कात असणाऱ्या ऑपरेटरच्या तब्येतीवर होणारा दुष्परिणाम.
अशा सर्व गोष्टी टाळण्यासाठी ऑईल व शीतक हे वेगळे करूनच शीतक पुन्हा मशिनमध्ये वापरावे लागते. ऑईल व शीतक वेगळी करणारी अनेक उपकरणे उपलब्ध आहेत जसे, ऑईल स्किमर, डिस्क स्किमर इत्यादी.
स्किमरमध्ये एक पट्टा/चक्र असते. ते शीतक-ऑईलच्या टाकीमध्ये सतत फिरते ठेवले जाते. शीतकामध्ये मिसळलेले ऑईल, चक्र/पट्ट्याला लागून बाहेर येते. टाकीच्या ज्या भागामध्ये चक्र/पट्टा फिरते त्या भागातीलच ऑईल वेगळे होते. त्यामुळे शीतकामधून सर्व ऑईल बाहेर निघण्याची खात्री नसते. या समस्येवर उपाय शोधून ऑईल व शीतकाच्या विलगीकरणासाठी 2003-04 साली आम्ही ’ऑइल कोअलायजर’ हे प्रभावी उपकरण शोधले.
कोअलायजरचे प्रकार
1) स्टँडर्ड कोअलायजर (सर्वसाधारणपणे 500 लिटरपर्यंतच्या मिश्रणासाठी)
2) सुपर कोअलायजर (सर्वसाधारणपणे 500 - 2500 लिटरच्या मिश्रणासाठी)
3) 2500 लिटरच्या पुढेदेखील कोअलायजर उपलब्ध असून 20,000 लिटरसाठी ’पजो’ कंपनीमध्ये कोअलायजर बसवला गेला आहे.
4) थर्मल कोअलायजर (वरील दोन प्रकारांपैकीच; पण मिश्रणाची उष्णता कमी होऊ नये यासाठी यावर एक आवरण असते.)
कोअलायजरची वैशिष्ट्ये
1. स्किमरमध्ये ऑईल - शीतकाचे मिश्रण स्थिर असून, स्किमरचा भाग हलता असतो, तर कोअलायजरमध्ये मिश्रण हलते ठेवले जाते. हा स्किमर व कोअलायजरमध्ये महत्त्वाचा फरक आहे.
2. कोणतेही ऑईल हे शीतकापासून वेगळे करण्याची क्षमता.
3. एका ठिकाणाहून दुसरीकडे नेणे सहज शक्य.
4. कोणताही वारंवार बदलावा/भरावा लागणारा पदार्थ नाही.
5. पंपाशिवाय कोणताही चल भाग नसल्यामुळे देखभालीची गरज नाही.
6. वापरानुसार विविध आकारमानात उपलब्ध.
7. मिश्रणाचे तापमान कायम ठेवण्याची सोय करता येणे शक्य.
कोअलेसेन्स प्रक्रिया
कोअलेसेन्स (Coalescence) ही एक प्रक्रिया आहे. दोन किंवा अधिक ऑईलचे कण एकत्र आल्यामुळे एक मोठा कण तयार होतो. असा कण शीतकावर कमी घनता (लो डेन्सिटी) असल्यामुळे तरंगतो. त्यामुळे शीतकावर तरंगणारे ऑईल वेगळे करणे सहज शक्य असते. याच तत्त्वावर कोअलायजर कार्य करते.
कोअलायजरमध्ये एकूण 4 महत्त्वाचे घटक असतात.
1फ्लोट ॲसेम्ब्ली
ऑईल - शीतक विलगीकरणाची प्रक्रिया फ्लोट ॲसेम्ब्लीपासून सुरू होते. ज्या ठिकाणी ऑईल - शीतकाचे मिश्रण येते अशा टाकीमध्ये ही ॲसेम्ब्ली बसवली जाते. टाकीतील मिश्रणाच्या पातळीनुसार फ्लोटची उंची कमी-जास्त होते. फ्लोटची रचना विशिष्ट पद्धतीने केलेली असते, जेणेकरून शीतकावर तरंगणारे ऑईल, काही प्रमाणात शीतक आणि हवा फ्लोटमधील पाईपमध्ये जाऊ शकेल. त्यामुळे फ्लोटमधून ऑईल - शीतकाचे मिश्रण व हवा अशा दोन्ही गोष्टी पंपामार्फत कोअलायजरकडे जातात. टाकीच्या संरचनेनुसार फ्लोट बसवला जातो. फ्लोटला जोडला गेलेला होज पाईप पंपाच्या सक्शनला जोडला जातो. त्यामुळे फ्लोटच्या आसपास असणारे ऑईल अगदी सहजपणे ओढले जाते. फ्लोटमध्ये दोन प्रकार असतात.
अ) पारंपरिक फ्लोट (कन्व्हेन्शनल फ्लोट)
पारंपरिक फ्लोटमध्ये स्टेनलेस स्टीलचे दोन गोळे (फ्लोट बॉल्स) असून, ते टाकीतील मिश्रणाच्या समपातळीत राहतात. या प्रकारामध्ये फ्लोट 170 मिमी इतक्या अंतरापर्यंत वर-खाली हलू शकतात.
ब) थाळी फ्लोट (डिस्क टाईप फ्लोट)
थाळी फ्लोट प्रकारामध्ये स्टेनलेस स्टीलची एक थाळी असून, त्यावर 4 चेंडू बसवले जातात. फ्लोटची हालचाल जास्तीत जास्त 70 मिमी इतकीच होऊ शकते. या प्रकारचा फ्लोट विशेषकरून सी.एन.सी. मशिनच्या ट्रॅम्प ऑईल टाकीसाठी बनवला गेला आहे. दोन्ही प्रकारांमध्ये एकच कार्य होते, परंतु टाकीवर असणाऱ्या जागेनुसार फ्लोटची निवड केली जाते. फ्लोटचा तळ सामान्यपणे बोल्टिंग पद्धतीने बसवण्यात येतो. फ्लोटचा तळ मॅग्नेटचादेखील उपलब्ध असतो. फ्लोटच्या आऊटलेटला हायड्रॉलिक होज पाईप बसवण्यात येतो व तो पंपच्या इनलेटला मिश्रण पुरवतो.
2) पंप
फ्लोट-ॲसेम्ब्लीकडून येणारे सोल्युशन पंपामार्फत कोअलायजरपर्यंत पोहोचवले जाते. सर्वसाधारणपणे कोअलायजरसाठी अपकेंद्री (सेंट्रिफ्युगल) पंप वापरला जातो, मात्र ज्या ठिकाणी मिश्रण अल्कलाईन असते तिथे फेसनिर्मिती (फोम फॉर्मेशन) टाळण्यासाठी हवेच्या दाबावर चालणारा पंप (एअर ऑपरेटेड डायफ्राम पंप) वापरण्यात येतो. अशा पंपाला 4 Kg/cm2 इतका हवेचा दाब पुरवावा लागतो. अपकेंद्री पंप हा कोअलायजरच्या प्रकारानुसार 1/2 किंवा 1 एशशक्ती (HP) इतक्या ताकदीचा वापरला जातो.
3) कॅबिनेट
पंप व कोअलायजरला आधार देण्यासाठी कॅबिनेटचा उपयोग केला जातो. तसेच ऑईल साठवणारी टाकीसुद्धा कॅबिनेटवरच बसवली जाते. ने-आण करणे सुलभ होण्यासाठी कॅबिनेटच्या पायांना चाके बसवलेली असतात.
4) कोअलायजर बॉडी
हा या प्रक्रियेतील महत्त्वाच्या भागांपैकी एक आहे. पंपाच्या डिलिव्हरी लाईनमधून येणारे मिश्रण कोअलायजर बॉडीमध्ये येते. यामध्ये एकूण चार चेंबर्स असतात. पहिल्या चेंबरमध्ये ’संयोग द्रव्य’ (कोअलायजिंग मटेरिअल) (चित्र क्र. 6) असते, ज्यामधून ऑईल -शीतकाचे मिश्रण जाते. या मटेरिअलचा एक विशेष गुणधर्म असतो. मटेरिअलमधून मिश्रण जाताना ऑईलचे कण मटेरिअलवर धरून ठेवले जातात व अशा कणांचे प्रमाण वाढल्यावर ऑईल तवंगरूपाने पुढे सरकते. हे मटेरिअल बदलण्याची आवश्यकता नसते. या हे मटेरिअलमधून ऑईल - शीतकाचे मिश्रण पुढे जाते व दुसऱ्या चेंबरमध्ये साठते. ही प्रक्रिया होत असतानाच ऑईलचे कणतवंग स्वरुपात शीतकावर तरंगतात. फ्लोट ॲसेम्ब्लीमधून शोषली गेलेली हवा याच प्रक्रियेमध्ये बुडबुड्यांच्या स्वरुपात बाहेर येते. हे बुडबुडे तरंगणाऱ्या ऑईलच्या कणांना तिसऱ्या चेंबरच्या दिशेने ढकलतात. दुसरे चेंबर व तिसऱ्या चेंबरच्यामध्ये एक विभाजन (पार्टिशन) असून, त्याला एक पार्ट लावला जातो ज्याला ’ओव्हरफ्लो वेअर’ असे म्हणतात. या ओव्हरफ्लो वेअरमधून तरंगणारे ऑईल व अल्प प्रमाणात शीतक तिसऱ्या चेंबरमध्ये येते. हीच प्रक्रिया पुन्हा तिसऱ्या चेंबरकडून चौथ्या चेंबरच्या बाबतीत होते. जसजशी ओव्हरफ्लोची प्रक्रिया होत जाते, तसतशी पुढे सरकणाऱ्या ऑईलची घनता वाढत जाते. म्हणजेच चौथ्या चेंबरमध्ये जास्तीत जास्त प्रमाणात ऑईल असते. चौथ्या चेंबरमधून ते काढून घेण्यासाठी व्हॉल्व्ह, ऑईल संग्राहक (ऑईल कलेक्शन बिन) पुरवली जाते. दुसऱ्या बाजूला एक ओपनिंग असते त्याला ’ऑईल फ्री आऊटलेट’ असे म्हणतात. यामधून फक्त शीतक येते व ते परत टाकीमध्ये सोडले जाते. ही प्रक्रिया जोपर्यंत टाकीमध्ये ऑईल आहे तोपर्यंत सुरू असते.
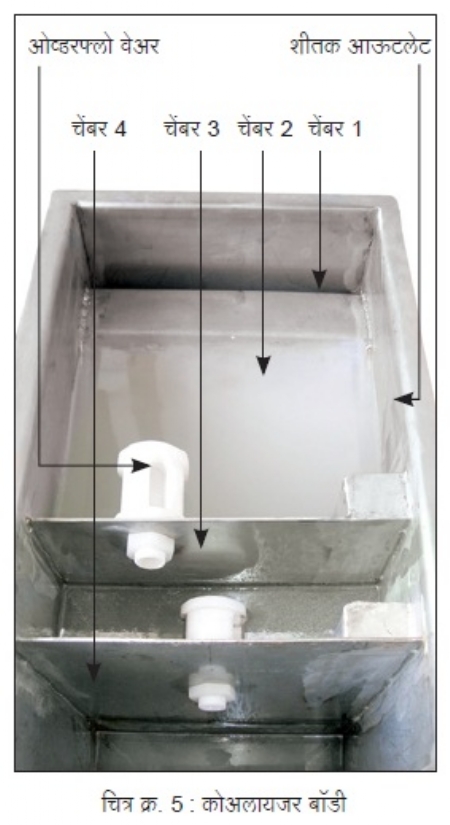
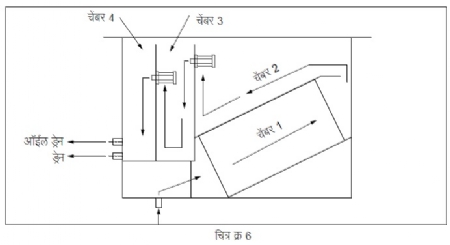
प्रत्यक्ष कामाचे उदाहरण
’बजाज ऑटो प्रा. लि.’ चाकण, पुणे येथे ऑटोमोबाईल क्षेत्रातील पार्टस् बनवणाऱ्या विभागामध्ये पार्टस्वर साचलेल्या ऑईलचा थर काढून टाकण्यासाठी ’वॉशिंग मशिन’ वापरण्यात येते. या मशिनच्या टाकीमध्ये वापरले गेलेले शीतक आणि यंत्रभागांवरून निघालेल्या ऑईलचे मिश्रण येते. ऑईलसह वापरल्या गेलेल्या शीतकामुळे सरफेस फिनिशिंग यथायोग्य नसणे, शीतकाच्या उष्णतावहन क्षमतेमध्ये झालेली घट व परिणामी गुणवत्तेमधील लक्षणीय घट इत्यादी अडचणी येत असत. त्या मशिनबरोबर शीतकामधील ऑईल काढून टाकण्यासाठी कोअलायजर बसवले गेले. कोअलायजरच्या वापरामुळे त्या जॉबवर ऑईलमुळे होणारे दुष्परिणाम नाहीसे झाले. चित्रामध्ये दर्शविल्याप्रमाणे बदल दिसून आला व गुणवत्ता वाढली. चित्र क्र. 7 मध्ये दाखवल्याप्रमाणे काळ्या रंगाचे माध्यम हे ऑईल असून ते शीतकावर साठून राह असे. पण चित्र क्र. 8 मध्ये कोअलायजर वापरल्यानंतर हे ऑईल वेगळे होऊन टाकीमध्ये शीतक स्पष्ट दिसू लागले.
फायदे
• शीतकाचे आयुर्मान तिपटीने वाढले.
• कंपोनंट रिजेक्शन 10% नी कमी झाले.
• शीतकाच्या विल्हेवाटीसाठी लागणारा खर्च 20% नी कमी झाला.
काही दिवसांमध्येच त्याच विभागातील आणखी वॉशिंग मशिन्ससाठी कोअलायजर मागविले गेले. आजतागायत बजाज ऑटो कंपनीमध्ये एकूण पाच कोअलायजर उत्कृष्टपणे कार्यरत आहेत. बजाज ऑटोप्रमाणेच आम्ही म्हणजे, ’इनोव्हेशन फिल्टर सिस्टिम प्रा. लि.’चे काही सन्माननीय ग्राहक उदाहरणार्थ, सँडविक एशिया प्रा. लि., सिको टूल्स लि., पजो व्हेईकल्स प्रा. लि., जॉन डिअर, फोर्ब्स मार्शल इत्यादी कोअलायजरच्या कार्यावर तसेच तत्पर सेवेवर समाधानी आहेत. आजपर्यंत अंदाजे 500 पेक्षा जास्त कोअलायजर भारतातील विविध ठिकाणी वापरले जात आहेत.
अजिंक्य केळकर ‘इनोव्हेशन फिल्टर सिस्टिम प्रा. लि.’ कंपनीचे संचालक आहेत.