उद्योगाच्या विस्तृत क्षेत्रामध्ये हलक्या धातूंपैकी अॅल्युमिनियम हा कदाचित सर्वाधिक ठिकाणी वापरला जाणारा धातू असेल. धातुशास्त्र आणि धातूला आकार देण्याच्या प्रक्रियांमध्ये होणाऱ्या प्रगतीमुळे अॅल्युमिनियम जीवनाच्या प्रत्येक अंगामध्ये कामात आणले जात आहे. सर्वात सहजपणे दिसणारा उपयोग म्हणजे अन्नपदार्थ गुंडाळण्यासाठी वापरली जाणारी अॅल्युमिनियम फॉइल, तर सर्वात उच्च तंत्रातील वापर म्हणजे विमानाच्या सांगाड्यासाठी होणारा वापर. मानवाने उपयोगात आणलेला हा त्या मानाने नवा धातू आहे. 1825 साली त्याचा शोध लागल्यावर उद्योगजगताने त्याचे गुणधर्म समजून घेतले आणि वापर सुरू केला.
कास्टिंग, फोर्जिंग, एक्स्ट्रूजन आणि रोलिंग अशा विविध प्राथमिक प्रक्रियांद्वारे अॅल्युमिनियमला आकार दिला जातो. या प्रक्रियांद्वारे आपल्याला यंत्रणासाठी तयार अशी कास्टिंग आणि फोर्जिंग,पत्रे (शीट), विशेष सेक्शन, ट्यूब, बार आणि वायर रॉड मिळतात.
अॅल्युमिनियमपासून तयार होणारे मिश्र धातू (अलॉय) हे उत्तम यंत्रणक्षमता असलेल्या धातूंपैकी एक समजले जातात. धातूला कापण्यासाठी लागणारे बल, टूलचे आयुर्मान, उत्तम पृष्ठीय फिनिश निर्माण करण्याची क्षमता, चिप्स सहजपणे दूर करण्याची क्षमता आणि शीघ्र गतीने धातू कापण्याची क्रिया या सर्वांसाठी ‘यंत्रणक्षमता’(मशिनॅबिलिटी) ही एक व्यापक संज्ञा वापरली जाते. विविध उत्पादनांमध्ये विविध गुणधर्म मिळवण्यासाठी अॅल्युमिनियममध्ये निरनिराळे इतर धातू मिसळले जातात. विविध मिश्र धातूंचे यंत्रणविषयक गुणधर्म वेगवेगळे असतात. त्यांचा यंत्रणक्षमतेवर होणारा परिणाम तक्ता क्र.1 मध्ये दिला आहे.
अॅल्युमिनियमच्या ज्या मिश्र धातूवर यंत्रण करायचे असेल, त्याचे रासायनिक घटक आणि त्यांचे प्रमाण, तसेच भौतिक गुणधर्म लक्षात घेणे जरूरीचे असते. मिश्र धातूचे धातुशास्त्रीय गुणधर्म आणि आपल्याकडे उपलब्ध असलेल्या मशिनची क्षमता या दोन्ही गोष्टी विचारात घेऊन टूलचा प्रकार-भूमिती, फिक्श्चर, कार्यवस्तू पकडण्याची व्यवस्था, कर्तनाचे पॅरामीटर, शीतक वगैरेची निवड करावी लागते.
अॅल्युमिनियमची कठीणता कमी असल्यामुळे ते कापण्यासाठी व्हाईट बिट टूलपासून पॉलीक्रिस्टलाईन डायमंडपर्यंत (पीसीडी) विविध प्रकारची टूल वापरता येऊ शकतात. जेव्हा मशिन स्पिंडलच्या आरपीएमवर मर्यादा असेल, तेव्हा ‘एचएसएस’सारखी कार्बाईडपेक्षा नरम (सॉफ्ट) टूल वापरावी. तथापि, त्यात पृष्ठीय फिनिशवर मर्यादा येतात. कमी कर्तन वेगाच्या बाबतीत ‘बिल्टअप कड’ ही प्रमुख समस्या असते. त्यासाठी रेक अँगल काळजीपूर्वक निवडावा लागतो. सिलिकॉनबरोबरच्या मिश्र धातूंमध्ये मोठा रेक अँगल ठेवल्याने, तर मॅग्नेशियम,तांब्याबरोबरच्या मिश्र धातूंमध्ये लहान रेक अँगल ठेवल्याने चांगले काम होते. एचएसएस टूल वापरताना पाण्यात विरघळणारी कर्तन तेले (सोल्युबल कटिंग ऑइल्स) अथवा केरोसीन चांगले काम देते. परंतु केरोसीन ज्वालाग्राही आणि धोकादायक असल्यामुळे ते वापरू नये, अशी शिफारस केली जाते. कर्तनाचा वेग कमी असताना, चिप बाहेर काढणे हा मोठा प्रश्न असतो, कारण त्यात निर्माण होणाऱ्या चिप अखंड आणि लांबसडक असतात. कर्तनाच्या कमी वेगावर 6.3 Ra इतका आणि विशेष परिस्थितीमध्ये 3.2 Ra इतका पृष्ठीय खरबरीतपणा (रफनेस) मिळू शकतो.
कोटिंग केलेली आणि कोटिंग न केलेली कार्बाईड टूल वापरूनसुद्धा आपण कर्तन वेग वाढवू शकतो. त्याने बिल्टअप कड या समस्येचे बहुतांश निराकरण होते. टर्निंग, मिलिंग आणि टॅपिंग यांच्यासारख्या विविध प्रक्रियांसाठी कटिंग टूलचे उत्पादक निरनिराळे उपाय सुचवतात. सर्वोत्कृष्ट परिणाम मिळवण्यासाठी उच्च गतीचे मशिन स्पिंडल आवश्यक असते. पाण्यात विरघळणार्या सिंथेटिक आणि सेमी-सिंथेटिक कटिंग ऑईलचे विविध पर्याय उपलब्ध आहेत. कार्बाईड टूल वापरल्याने कमी लांबीच्या चिप निर्माण होतात आणि त्या बाहेर काढणे सोपे असते. कार्बाईड टूल वापरून साधारणपणे 3.2 Ra इतका पृष्ठीय खरबरीतपणा आणि विशेष परिस्थितीमध्ये 1.6 Ra पर्यंतचा पृष्ठीय खरबरीतपणा मिळवणे शक्य असते.
प्रगत सी.एन.सी. मशिनिंग सेंटरमध्ये 20000 आरपीएम पर्यंतचा स्पिंडल वेग मिळू शकतो. इथे पीसीडीपासून बनवलेली टूल वापरणे शक्य असते. ही टूल फिनिशिंगसाठी वापरली जातात आणि त्यापासून सामान्यतः 0.8 Ra इतका आणि विशेष परिस्थितीमध्ये 0.2 Ra इतका पृष्ठीय खरबरीतपणा मिळू शकतो. जिथे अतिशय नितळ पृष्ठीय फिनिश हवा असतो आणि मोजमापाचा टॉलरन्स अतिशय कमी असतो, अशा सूक्ष्म बोअरिंग, मिलिंग आणि रीमिंग या कामामध्ये ही टूल वापरली जातात. ही टूल वापरताना विरघळणार्या खास सिंथेटिक कटिंग ऑईलचा उपयोग केला जातो. उच्च आरपीएमवर ही टूल वापरताना त्या आरपीएमवर टूलचे डायनॅमिक बॅलन्सिंग करून घेणे आवश्यक असते. बॅलन्स न केलेली टूल वापरली तर त्यांची महागडी अग्रे(टिप)तुटण्याची शक्यता असते. पीसीडी बोअरिंग बार किंवा रीमर वापरण्याच्या आधी अजून एक काळजी घ्यावी लागते, ती म्हणजे आधीच्या कामात वापरलेल्या रफिंग टूलचे (ड्रिल) अवशेष आत अडकलेले नसावेत. विशेषतः ब्लाईंड होलच्या बाबतीत खास काळजी घ्यावी लागते. तुटलेल्या टूलचे तुकडे आत राहू शकतात (चित्र क्र.1) आणि स्वयंचलित सायकलनुसार पुढच्या टप्प्यावरील कामात पीसीडी टूल त्यावर आदळते आणि तुटते. जर पीसीडी तुटले, तर ते महागडे टूल वापरण्याचे आर्थिक फायदे नाहीसे होतात.
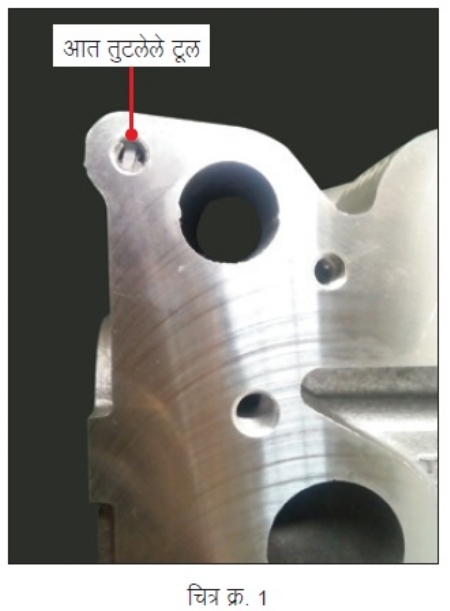
फिक्श्चरच्या डिझाईनमध्ये क्लॅम्प आणि लोकेटरचेही विशेष लक्ष ठेवावे लागते. पूर्वी यंत्रण केलेल्या पृष्ठभागावर क्लॅम्प वापरताना किंवा लोकेशनच्या भोकात डॉवेल पिनचा वापर करताना फिक्श्चरच्या कठीण(हार्ड) केलेल्या या भागांमुळे कार्यवस्तूच्या पृष्ठभागावर पोचे/खड्डे किंवा तत्सम नुकसान होण्याची शक्यता असते. अशावेळी नुकसान टाळण्यासाठी क्लॅम्पवर पितळी टोपणे/बटण बसवावे किंवा पट्टी ब्रेझ करावी (चित्र क्र. 2) किंवा शक्य असल्यास शंकूच्या आकाराची पितळी टोपणे लोकेशन पिनवर बसवावी. लोकेशन पिनला मोठा शॅम्फर द्यावा. जिथे हा शॅम्फर व्यासाला मिळतो, तिथे रेडियस द्यावी.
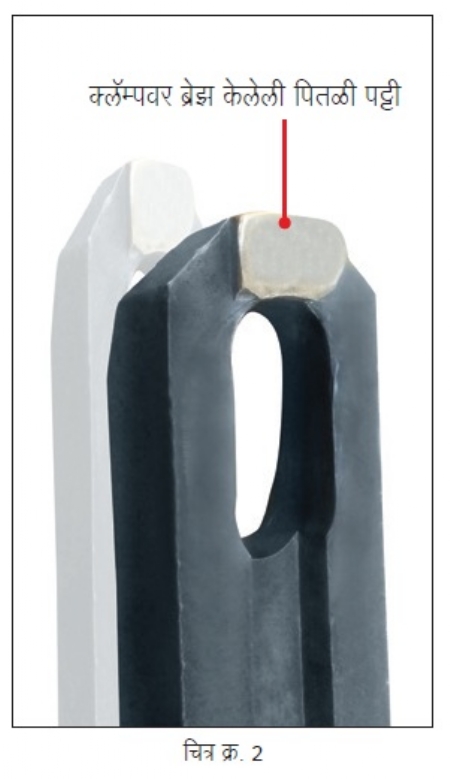
अॅल्युमिनियम यंत्रणाच्या फिक्श्चरमध्ये क्लॅम्पिंगचे बल अतिशय नियंत्रित असणे, फार महत्त्वाचे असते. यांत्रिकी फिक्श्चरच्या बाबतीत ऑपरेटरचा कल रिंग स्पॅनर वापरून कार्यवस्तू त्यात जास्तीत जास्त घट्ट पकडण्याकडे असतो. हे फार धोकादायक असते आणि यामुळे यंत्रभाग वेडावाकडा होऊन रिजेक्ट होतो. त्यामुळे यांत्रिकी फिक्श्चरच्याबाबतीत काळजीपूर्वक टॉर्क सेट करून नंतर टॉर्क रेंचचा वापर करणे अत्यावश्यक आहे. हायड्रॉलिक फिक्श्चरच्याबाबतीत क्लॅम्पिंगचा दाब तपासून सेट करता येतो.
अॅल्युमिनियमच्या यंत्रभागांचे डीबरिंग करणे सोपे असते, पण त्यातही एका बाबतीत काळजी घ्यावी लागते. जर नितळपणे मिल केलेल्या पृष्ठभागाच्या कडांवर आपण रोटरी बर टूलचा वापर करत असाल, तर डीबरिंग गन कडेवरून सटकण्याची आणि फिनिश केलेल्या नितळ पृष्ठभागावर घासण्याची शक्यता असते. (चित्र क्र. 3) यामुळे पृष्ठभागाचे दुरुस्त न करण्याजोगे नुकसान होते. अतिशय सुंदरपणे यंत्रण केलेले अॅल्युमिनियमचे यंत्रभाग, खास करून ज्यांच्या भिंती पातळ कास्टिंगच्या असतात असे यंत्रभाग, चुकीच्या डीबरिंगमुळे रिजेक्ट होतात. हा धोका टाळण्यासाठी योग्य उंची असलेला वर्क बेंच व शक्य झाल्यास वर्क होल्डिंग फिक्श्चर वापरावे. जेणेकरून ऑपरेटरच्या हातातून डीबरिंग गन चुकीच्या दिशेला सटकणार नाही. कार्यवस्तूच्या आकारानुरूप सुयोग्य प्रकारचे रोटरी बर टूल वापरावे. याशिवाय ऑपरेटर प्रशिक्षण महत्त्वाचे आहेच.
अॅल्युमिनियमचे उच्च अचूकतेचे यंत्रभाग हाताळताना विशेष काळजी घ्यावी लागते. आपल्याजवळील ट्रॉली आणि बिन प्लॅस्टिकच्या असाव्या किंवा त्यांच्यावर टेफ्लॉनचे कोटिंग करणे हितावह असते.
अॅल्युमिनियम यंत्रणामध्ये खास करून सी.एन.सी. मशिनवर सर्वोत्कृष्ट उत्पादनक्षमता मिळवण्यासाठी निव्वळ कर्तनासाठी लागणारा वेळ आणि अनुत्पादक वेळ अशा धर्तीवर विश्लेषण करणे महत्त्वाचे आहे. अनुत्पादक वेळात टूलच्या हालचालीस लागणारा वेळ (एअर कटिंग) आणि टूल बदलण्यासाठी लागणारा वेळ यांचा समावेश होतो. कर्तनाचा वेग उच्च असल्याने एकंदर आवर्तन वेळात निव्वळ कर्तनासाठी लागणारा वेळ बराच कमी असतो. त्यामुळे मशिनचा अनुत्पादक वेळ कमी करण्यासाठी विविध उपाय योजावे लागतात. टूल बदलण्यात वाया जाणारा वेळ कमी करण्यासाठी कॉम्बिनेशन टूलचा उपयोग करणे आणि कर्तनाचा एक पास झाल्यावर दुसऱ्या पाससाठी योग्य स्थानी शीघ्रतेने परत येणे (फास्टर रॅपिड मुव्हमेंट) यांचा शक्य तितका वापर करावा लागतो. सी.एन.सी. मशिनमध्ये हल्ली झालेली रॅपिडसंबंधीतील प्रगती अॅल्युमिनियम यंत्रणातील उत्पादकतेला वरदानच ठरते आहे.
रॅपिड मुव्हमेंट व टूल बदल वेळेचा एकंदरीत उत्पादकतेवर होणारा परिणाम यासाठी सोबतचा केस स्टडी पाहावी.
राजेश म्हारोळकर यांत्रिकी अभियंते असून ते ’श्रीनिवास इंजिनिअरिंग ऑटो कंपोनंटस् प्रा. लि.’चे संचालक आहेत. ही कंपनी ट्रॅक्टरचे कंपोनंट आणि ऑटोमोटिव्ह उद्योगांना आयर्न कास्टिंग आणि प्रिसिजन मशिनिंगबाबत सेवा देते.