उत्पादन क्षेत्रात गुणवत्ता नियंत्रण विभागावर अतिशय कमी वेळात मोठ्या आणि क्लिष्ट कामांची तपासणी करून त्या कामाच्या गुणवत्तेला प्रमाणित करण्याची जबाबदारी असते. जर निर्माण होणारी प्रत्येक वस्तू अचूक आहे की नाही हे ठरविण्यासाठी तिला गुणवत्ता ओशासन चाचणीमधून जावे लागणार असेल, तर उत्पादन विभागाची क्षमता गुणवत्ता नियंत्रण विभागाच्या कामावर अवलंबून राहते. यामुळे गुणवत्ता नियंत्रण विभागावरील कामाचा भार वाढतो. जर एकाच कार्यवस्तूमध्ये तपासण्याच्या अनेक बाबी असतील, उदाहरणार्थ, कडा, वक्र भाग, ड्रिल केलेली भोके, ग्रूव्ह, वगैरे, तर हे काम अजूनच अवघड होते आणि त्यासाठी प्रशिक्षित आणि कुशल कर्मचाऱ्यांची मोठी आवश्यकता असते. उत्पादनाच्या संख्येमध्ये मागणीनुसार नेहमीच चढ-उतार होत असल्यामुळे गुणवत्ता तपासणाऱ्या कर्मचाऱ्याच्या कार्यभारावर त्याचा परिणाम होतो. त्यामुळे प्रसंगी त्यांच्या कामाच्या गुणवत्तेचा बळी पडू शकतो.
गुणवत्ता नियंत्रणासाठी उद्योगक्षेत्रात विविध तंत्रे/साधने वापरली जातात. तथापि, प्रत्येक साधनाच्या क्षमतेनुसार त्याच्या अचूक मापनाच्या टॉलरन्स आणि फिटच्या काही दशांशामधील मर्यादा आहेत. यामुळेसुद्धा यंत्रभाग ॲसेम्ब्ली विभागापर्यंत पोहोचतो, तेव्हा नाकारला जाण्याची शक्यता वाढते.असे अस्वीकृत यंत्रभाग उत्पादन विभागात दुरुस्ती/पुनःप्रक्रियेसाठी परत पाठविले जातात आणि एखादा कुशल कर्मचारी उत्पादन/यंत्रण झाल्यानंतर लहान-मोठ्या दुरुस्त्या करण्यासाठी खास नियुक्त करावा लागतो. यामुळे यंत्रणासाठी लागणारा वेळ आणि खर्च दोन्ही वाढतात. अचूक यंत्रणाने या समस्येचे निराकरण होऊ शकते, परंतु यातील मानवी त्रुटींच्या शक्यतेकडे दुर्लक्ष करून चालत नाही. उत्पादन कार्यामध्ये संपूर्ण स्वयंचलन पुरविण्यासाठी प्रथम श्रेणीचे गुणवत्ता ओशासन आवश्यक आहे.
गुणवत्ता नियंत्रण आणि तपासणीची प्रणाली हवी असणाऱ्या एका अभियंता गटाने आम्हाला शेकडो वस्तूंच्या गुणवत्ता नियंत्रणासाठी एक शीघ्र प्रतिसाद देणारी आणि मायक्रोमीटर स्तरावरील अचूकता असणारी प्रणाली हवी असल्याची गरज सांगितली.
त्यांच्या मागणीचा सखोल अभ्यास केल्यावर आम्ही एका सोप्या उपायावर येऊन पोहोचलो. आम्ही त्यांना त्यांच्या गुणवत्ता नियंत्रण विभागात लेझर स्कॅनिंग करणारे एक लहान मशिन वापरण्याचे सुचविले.
लेझर प्रणाली कशी काम करते?
लेझर विस्थापन सेन्सर पद्धतीवर आधारित लेझर मापन तंत्र हा या प्रणालीचा गाभा आहे. ज्याठिकाणी पारंपरिक पद्धतीने अंतरे किंवा परिमाणे (डायमेन्शन) यांचे मापन करणे अतिशय अवघड असते, अशा क्लिष्ट पृष्ठभागांसाठी लेझरवर आधारित मापन तंत्र ही पद्धत खास विकसित केली गेली आहे. या प्रणालीच्या दुसऱ्या टप्प्यावर, अपेक्षित भागाची जाडी तपासणे या कामासाठीही तिच्यात आवश्यक सुधारणा केल्या आहेत.
हे लेझरवर आधारित एक अतिशय सुलभ स्कॅनिंग मशिन आहे. यात व्हॉल्युम इल्युमिनेशन आणि फोटो डायोड रिसीव्हर तसेच, हाय रेझोल्युशन कॅमेरेसुद्धा (चित्र क्र.1अ आणि 2अ) आहेत.
कोणत्याही प्रातिनिधिक प्रणालीमध्ये पुढे दिल्यानुसार घटक असतात. ऑप्टिकल लेझर स्कॅनर, एक डिटेक्शन युनिट, एक डेटा प्रोसेसिंग युनिट. रिसीव्हरच्या आधी (चित्र क्र. 2 ब) फिल्टर आणि भिंगे बसविलेली असतात.
ही भिंगे वाईड अँगल ॲडजेस्टमेंट करून वस्तूवर किरण फोकस करण्यासाठी असतात. प्रकाशाच्या ज्या तरंगलांबींमुळे व्यत्यय निर्माण होऊ शकतो, त्या फिल्टरद्वारा अडविल्या जातात. लेझरच्या तरंगलांबीनुसार फिल्टरची निवड केली जाते. अंतराच्या मापनासाठी (चित्र क्र. 1अ) आवश्यकतेनुसार साधा लेझर बिंदू किंवा लेझर रेषा पुरेशी असते. लेझर स्कॅनिंग प्रणालीमध्ये ज्या पृष्ठभागाची तपासणी/निरीक्षण करायचे असेल, त्याला लेझर प्रकाशाच्या शलाकेद्वारे (बीम) प्रत्येक बिंदूवरून स्कॅन केले जाते. त्यामुळे पृष्ठभागावर एक तेजस्वी बिंदू निर्माण होतो. जेव्हा फोकस केलेली लेझर शलाका एखाद्या पृष्ठभागावर पडते, तेव्हा उत्सर्जित झालेल्या किरणांचे विखुरणे हे पृष्ठभागाच्या स्वरुपावर आणि रचनेवर अवलंबून असते. कोणत्याही वस्तूच्या संपूर्ण पृष्ठभागाची तपासणी करावयाची असल्यास कोणतीही जागा न वगळता, प्रतिमा स्वच्छ येईल अशी भिंगांची रचना करून (फोकस) लेझर किरणाने पृष्ठभागावरील प्रत्येक बिंदूंची तपासणी करणे आवश्यक असते. प्रकाश पकडणारे (लाईट रिसीव्हिंग) युनिट इमेजिंग लेन्समधून, वर सांगितलेल्या तेजस्वी बिंदूचे अवकाशीय स्थान एका पीसीडी किंवा सीसीडीसारख्या प्रकाशबिंदू स्थान शोधकाद्वारे (पोझिशन डिटेक्टर) नोंदवत असते. मापन प्रणालीमधील सिग्नल प्रोसेसिंग युनिट प्रोबसारखे काम करून वस्तूच्या विस्थापनातील बदलांची गणना करते आणि मापनाच्या वेळी पृष्ठभागावर फिरणाऱ्या तेजस्वी बिंदूचे बदलते स्थान सतत नोंदवले जाते.
प्रणालीद्वारा वस्तूच्या आदर्श नमुन्याचे (मास्टर) त्रिमितीमध्ये स्कॅनिंग केले जाते आणि संदर्भासाठी त्या नमुन्याचा एक नकाशा निर्माण केला जातो. स्कॅनिंग प्रक्रिया सुरू करण्यापूर्वी एक आरंभबिंदू निश्चित केला जातो. या आदर्श नमुन्याच्या पृष्ठभागांची लेझर प्रतिबिंबे प्रत्येक स्कॅनिंगच्यावेळी प्रणालीच्या स्मृतीमध्ये संग्रहित केली जातात. पृष्ठभागांची निवड क्रमशः करता येते आणि त्यानुसार त्यांचे मशिनखाली स्कॅनिंग करता येते. संपूर्ण नमुन्याची स्कॅनिंग प्रक्रिया पूर्ण झाल्यानंतर घन प्रतिकृती (सॉलिड मॉडेलिंग) निर्मितीच्या सॉफ्टवेअरद्वारा त्याची पुनर्रचना केली जाते. आपल्याला पाहण्यासाठी हे सॉफ्टवेअर एक प्रीव्ह्यू तयार करू शकते. गुणवत्ता ओशासन विभागातील कार्यगट या टप्प्यावर आपले योगदान देऊन परिमाणात अजून सुधारणा आणू शकतो. ज्या क्षेत्राचे विश्लेषण करायचे आहे, ते कितीही मोठे असू शकते आणि स्थानसंबंधी सूक्ष्मता मायक्रोमीटरपेक्षाही कमी असू शकते. लेझरच्या बिंदूचे पृष्ठभागावरील स्थान कोणत्याही टप्प्यावर अतिशय
अचूकपणे निश्चित करता येते, त्यामुळे हे शक्य होते.
वापरात आणण्याचे मार्ग
विेशासार्हतेच्या नव्या मागण्यांना पुरे पडण्यासाठी पूर्वीपासून माहिती असलेल्या गणितातील पद्धती आणि तंत्रे (इंटरफेरोमेट्रिक, स्कॅटरिंग, ट्रँग्युलेशन, फ्रिंज प्रोजेक्शन इत्यादी.) आता नव्याने अभ्यासली जात आहेत आणि विकसित केली जात आहेत. खास करून त्रिकोणीकरणावर आधारित पद्धतींचा उपयोग व्याप्ती किंवा पल्ल्याचे संवेदन (रेंज सेन्सिंग), 3D आकार परीक्षण, स्थलरुपिक (टोपोग्राफिक) मूल्यांकन आणि खडबडीत पृष्ठभागांचे सूक्ष्म परीक्षण यांच्यामध्ये विस्तृतपणे केला जात आहे. स्कॅनिंग प्रक्रियेदरम्यान तपासल्या जाणार्या पृष्ठभागाची तुलना, सेन्सर त्याच्या स्मृतीमधील काल्पनिक संदर्भ प्रतलाशी सतत करत असतो आणि नंतर तो या दोन पृष्ठभागांमधील सापेक्ष विस्थापनाचे अंतर मोजून त्याची नोंद करतो. हा नकाशा त्याच्या स्मृतीमध्ये संग्रहित केला जातो. त्याचा उपयोग उत्पादन विभागातील कार्यरत मशिनवर आवश्यकतेनुसार केला जाऊ शकतो. स्कॅनिंग करतेवेळी वस्तू तीनही अक्षामध्ये, 360 अंशात फिरविता येते. जर गोल फिरवणे शक्य नसले, तर स्वयंचलनावरील कार्यभार कमी करण्यासाठी स्कॅनिंग युनिटची एक मालिका (ॲरे) आयोजित करणे शक्य असते. (चित्र क्र. 3 अ आणि ब).
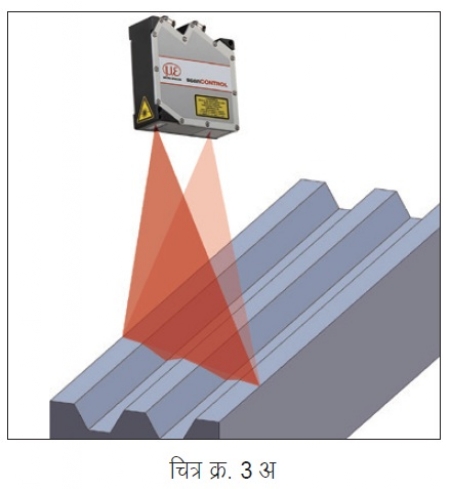
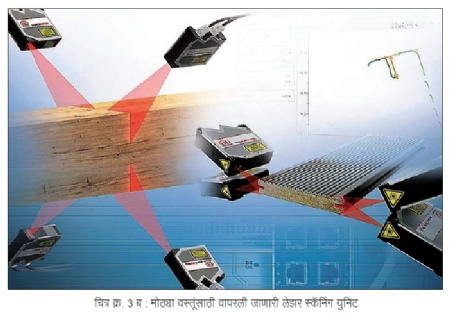
एकाच वस्तूसाठी ही तपासणी वापरकर्त्याच्या गरजेप्रमाणे कितीही वेळा करता येते. पूर्वी उल्लेख केल्यानुसार चित्र क्र. 3 अ आणि ब मध्ये दाखविल्याप्रमाणे स्कॅनिंग प्रणालीची मालिका आयोजित करणे शक्य असते. स्कॅनिंग युनिटच्या संख्येवर आधारित वस्तूचे भाग अथवा खंड (सेक्शन) वेगळे पाडले जातात. जोपर्यंत त्यामुळे काही व्यत्यय निर्माण होत नाही, तोपर्यंत विभाग एकमेकावर काही प्रमाणात आच्छादित (ओव्हरलॅप) झाले, तरी काही प्रश्न नसतो. परंतु जर त्याने व्यत्यय निर्माण होत असेल, तर निरनिराळ्या तरंगलांबीचे लेझर वापरता येऊ शकतात. (चित्र क्र. 4अ, 4ब) जर 2 किंवा 3 स्कॅनिंग युनिट कार्यरत असतील, तर हे सोपे असते. परंतु जर 3 पेक्षा अधिक स्कॅनिंग युनिट वापरली जात असतील, तर निरनिराळी क्षेत्रे आखून घ्यावी लागतात आणि स्कॅनिंग मशिन त्याप्रमाणे नियुक्त करावी लागतात, कारण उपलब्ध असलेल्या लेझर तरंगलांबींची संख्या मर्यादित आहे.
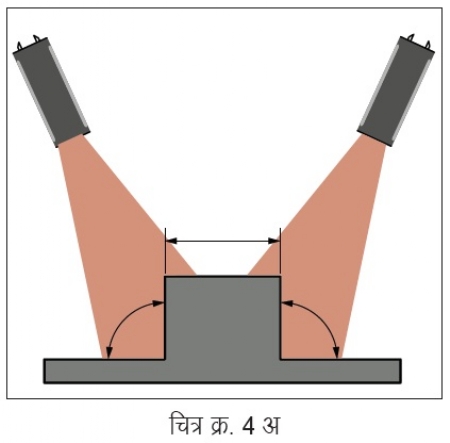
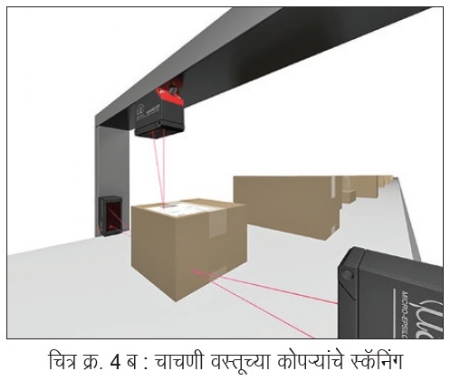
वापरकर्त्याला ऑनलाईन मोडमध्ये परिणाम सादर केले जातात आणि उत्पादनातील न जुळणारे उत्पाद त्वरित वेगळे करता येतात. (चित्र क्र. 5) उत्पादन यंत्रणा जितक्या गतीने काम करू शकेल, तितक्या गतीने ही प्रणाली काम करू शकते. स्कॅनिंगचा दर प्रति वस्तू कमीत कमी 3 सेकंद इतका असू शकतो. परंतु हे त्या वस्तूची क्लिष्टता आणि आकार यांच्यावर अवलंबून असते. सोप्या उत्पादांसाठी हा दर जास्त असू शकतो. या सोबत जोडलेल्या सॉफ्टवेअर पॅनेलप्रमाणे उत्पादाचा अंतिम तपशील असतो. सॉफ्टवेअर बहुरंगी नकाशांच्या स्वरुपात आउटपुट देते. त्यामुळे सदोष भाग ओळखण्यास साहाय्य होते आणि त्यात सहज सुधारणा करता येते.
उदाहरण
आपण स्प्रॉकेट व्हील टूथ तपासणीचे एक क्लिष्ट उदाहरण घेऊ. चित्र क्र.6 अ मध्ये दाखविल्यानुसार लेझर स्कॅनिंग मशिनवर स्प्रॉकेट टूथचे स्कॅनिंग केल्यानंतर चित्र क्र. 6 ब आणि 6 क प्रमाणे नकाशा निर्माण केला जाईल.
दोन दात्यांमधील कोन, दोन दात्यांमधील खोबणीची लांबी, दात्याची खोली, वक्रता किंवा प्रोफाईल, पिच आणि सर्वात महत्त्वाचे म्हणजे, व्हीलच्या पृष्ठभागाचा फिनिश, हे पॅरामीटर तपासले जातील. या व्यतिरिक्त ही प्रणाली वस्तूवरील पोचे, दात्यांचा वेडेवाकडेपणा किंवा सपाटपणा किंवा दात्यांची व्हीलवरील अलाइनमेंट, हेसुद्धा तपासू शकते.
लेझरचे विविध कामातील उपयोग
हे तंत्र वापरून वस्तूंची गुणवत्ता पाहणे आणि प्रमाणित करणे यासाठी एक मनुष्य पुरेसा आहे. कास्टिंगच्या उद्योगक्षेत्रात यंत्रणापूर्वी परिमाणाच्या मर्यादा तितक्या काटेकोर नसतात. त्यामुळे परिमाणाची तपासणी अतिशय वेगाने करता येते. अयोग्य कास्टिंगमुळे उद्भवणारे दोष किंवा वातछिद्रे (ब्लोहोल) अगदी मायक्रोमीटरच्या स्तरावर शोधणे शक्य असते. त्यामुळे जरूर पडल्यास याचा उपयोग पृष्ठभाग परीक्षणाचे साधन म्हणूनही करता येतो. त्याउलट प्लॅस्टिक मोल्डिंग उद्योगक्षेत्रात जेव्हा डायद्वारा दाबून निर्माण केलेल्या वस्तूमध्ये आतल्या भागात दातेरीपणा असतो किंवा मोल्ड केलेल्या वस्तू टॉलरन्सबाहेर असतात, तेव्हा असे दोष शोधणे अतिशय सहजपणे शक्य होते. हे दोष साध्या डोळ्यांनी दिसू शकत नाहीत. ते साध्या दृष्टीवर आधारित तपासणीमध्ये निसटून जातात. रबर उद्योगक्षेत्रात रिंग, बुशिंग अशानंतर कठिणीकरण करण्यात येणाऱ्या वस्तूंमध्ये सहज फिट होण्याच्या दृष्टीने उच्च स्तरावरील अचूकता आवश्यक असते. या प्रणालीमुळे तपासणीच्या वेळेमध्ये प्रचंड बचत होऊ शकते.
सपाट पृष्ठभागाच्या स्कॅनिंगसाठी ही प्रणाली कोणताही खड्डा, पोचा किंवा फुगीर भाग, कोपरे, सपाटपणा आणि वस्तूची परिमाणे तपासू शकते.
अचूकतेच्या स्तरासोबत, ही प्रणाली लहानापासून मोठ्यापर्यंत कोणत्याही वस्तूसाठी तितकीच परिणामकारकपणे उपयुक्त आहे हा आणखी एक फायदा आहे. ऑटोमोटिव्ह उद्योगक्षेत्रात लहानशा स्क्रूपासून चॅसीसारख्या अवाढव्य गोष्टीपर्यंत, साध्या बारपासून ते क्लिष्ट अशा दरवाज्याच्या डिझाईनपर्यंत सर्व काही स्कॅन करून तपासण्याचे काम ही प्रणाली करू शकेल. (चित्र क्र. 8) त्यासाठी तिला निरनिराळ्या उत्पादन दालनात सहजपणे नेता येणेही शक्य आहे.
या प्रणालीच्या केवळ एकाच युनिटचा उपयोग करून एका प्लांटमधील सर्व उत्पादने सहजपणे तपासता येतील. प्रत्येक जागेवर हे युनिट फक्त प्लग-इन करा आणि कामाला सुरुवात करा, या तत्त्वावर चालवता येते. ही प्रणाली संपूर्णपणे सुरक्षित आहे, कारण या प्रणालीमध्ये दुसऱ्या श्रेणीच्या लेझरचा उपयोग केलेला आहे. यात कोणतेही यांत्रिक भाग नसल्यामुळे कोणत्याही प्रकारचे सेफ्टी स्विच किंवा मशिनविषयक विलंबामुळे प्रणाली सुरू होण्यास काही वेळ लागणे, असेही नसते. लेझर स्कॅनिंग प्रणालीचे सर्वात महत्त्वाचे फायदे म्हणजे हाय रेझोल्युशन, वेगवान स्कॅनिंग आणि उच्च (कॉन्ट्रास्ट) असलेल्या प्रतिमांची उपलब्धता.
प्रणाली वापरताना घ्यावयाची काळजी
ही प्रणाली उत्पादन विभागाने निर्माण केलेले सर्व उत्पादन नापास करून त्यांना मोठा धक्का देऊ शकते. इथे काही मानवी त्रुटीमुळे चुका असलेली वस्तू आदर्श नमुना (मास्टर) म्हणून निवडली गेली असली, तर असा घोटाळा होऊ शकतो. हे टाळण्यासाठी वापरकर्त्याने पुरेशी काळजी घेऊन आदर्श नमुना विकसित केला पाहिजे. अतिशय अचूक मास्टर बनविण्यासाठी अधिक प्रयत्न केले, म्हणजे आपोआपच गुणवत्ता नियंत्रण युनिटमधील कष्ट आणि वेळ यांची बचत होईल. ही प्रणाली कोणत्याही वातावरणात काम करू शकते. कुठूनतरी येणाऱ्या किंवा आजूबाजूच्या प्रकाशामुळे अंतिम परिणामामध्ये कोणतीही अतिरिक्त चूक/त्रुटी येत नसते. त्यामुळे ही प्रणाली सूर्यप्रकाशात किंवा काळोख्या दालनात तितक्याच अचूकतेने काम करते. तापमानातील फरकाचा मापनावर काहीही परिणाम होत नाही, परंतु याला जी वस्तू तपासायची आहे तिच्या तापमानाचा अपवाद आहे. (कारण वस्तूच्या तापमानानुसार तिची परिमाणे बदलतात) जाडी आणि आकारमान यांच्या व्यतिरिक्त ही प्रणाली आकार, सपाटपणा, लांबी, वाकडेतिकडेपणा, तरंगमयता (वेव्हीनेस), सम-प्रतलता (को-प्लेनॅरिटी) यांच्या बाबतीत उत्तमपणे चालते. हिचा देखभालीचा खर्च अतिशय कमी आहे.
तापमानातील फरक, प्रतिमेच्या प्रक्रियेतील त्रुटी आणि गणिती प्रतिमानातील मर्यादा यांच्यामुळे मापनात होणाऱ्या चुका, अशा पूर्वी मर्यादा होत्या. आता नवीन तंत्रज्ञानाद्वारे त्या जवळपास नाहीशा झाल्या आहेत. आता पृष्ठभागावर असलेल्या कचऱ्यामुळे किंवा बाहेरच्या गोष्टींमुळे (फॉरेन बॉडीज) बहुतेक चुका उद्भवतात.
या प्रणालीची किंमत ती कोणत्या कामासाठी हवी आहे आणि किती अचूकता अपेक्षित आहे, त्यावर आधारित आहे. एक उच्च रेझोल्युशन असलेली अतिशय साधी 1D स्कॅनिंग प्रणाली एखाद्या कमी रेझोल्युशन असलेल्या 3D प्रणालीपेक्षा अधिक महाग असू शकते.
सुधारलेल्या गुणवत्ता परीक्षण दरामुळे उत्पादन विभागावरील ताण कमी होऊ शकतो आणि जे गुणवत्ता नियंत्रण प्रक्रियेमधील ताणतणावाचे कौतुक करतात, त्यांच्या चेहऱ्यावर आपण स्मित पाहू शकतो.
गणपती कांबळे यांनी आयआयटी चेन्नई येथून एअरोस्पेस अभियांत्रिकीमध्ये MS केले आहे. यांत्रिकी अभियंते असलेले कांबळे जोस्ट्स इंजिनिअरिंग’ या कंपनीत नॅनो टेक्नॉलॉजी अँड अनॅलिटिकल सिस्टिम्स या विभागात काम करतात.