बऱ्याच वेळा छिद्र आणि बाह्य व्यास यांच्या आरेखनाच्या तपशिलात गोला-कारिता (राऊंडनेस) आणि दंडगोलाकारिता (सिलेंड्रिसिटी) यांच्यावर डिझाईनरने मर्यादा घालून दिलेल्या असतात. या दोन वेगवेगळ्या भौमितिक गुणधर्मांसाठी संज्ञा असल्या तरी, या दोन्हीवर नियंत्रण ठेवण्यासाठी करण्यात येणाऱ्या क्रिया सारख्या असल्यामुळे या दोन्हींचा आपण एकत्रितपणे विचार करू. सर्वप्रथम आपण या दोन्हींच्या व्याख्या आणि अर्थ समजावून घेऊ.
गोलाकारिता किंवा वर्तुळाकारिता
हे दोन्ही समानार्थी शब्द एकाच गुणवैशिष्ट्यांबद्दल वापरले जातात. (चित्र क्र.1) गोलाकारिता म्हणजे, दोन काल्पनिक समकेंद्री वर्तुळांच्या त्रिज्येतील फरक, ज्यामध्ये त्या कार्यवस्तूच्या परिमितीवरील सर्व बिंदू समाविष्ट असतात. यावरून हे स्पष्ट होईल की, हे गुणवैशिष्ट्य दंडगोल किंवा छिद्र यांच्या संपूर्ण पृष्ठभागाशी संबंधित नसून फक्त त्यांच्या एका भागाशी संबंधित असते.
दंडगोलाकारिता
एका दंडगोलाचे सर्व बिंदू ज्या दोन समकेंद्रित दंडगोलांध्ये असतात, त्या दोन दंडगोलांच्या त्रिज्येधील फरकाला दंडगोलाकारिता म्हणतात. (चित्र क्र. 2) यावरून हे स्पष्ट होईल की हे गुणवैशिष्ट्य दंडगोलाच्या संपूर्ण पृष्ठभागाशी संबंधित असून एखाद्या विशिष्ट भागापुरते मर्यादित नाही.
गरजेनुसार आणि एखाद्या विशिष्ट कारणासाठी वापरण्यात येणाऱ्या ‘फिट’प्रमाणे डिझाईनर गोलाकारिता किंवा दंडगोलाकारिता यांच्यावरील मर्यादा निश्चित करतो.
बोअरिंगमधील समस्या
आता आपण ‘बोअरिंग’ प्रक्रियेत गोलाकारिता आणि दंडगोलाकारिता यांच्यावर कसा परिणाम होतो आणि त्यावर नियंत्रण कसे करायचे ते समजून घेऊ.
कार्यवस्तू पकडणाऱ्या घटकांचे परिणाम
कार्यवस्तू पकडण्याच्या बलांमुळे कार्यवस्तूचे विरूपण (डिस्टॉर्शन) होऊ नये, यावर नियंत्रण करणे महत्त्वाचे असते. जेव्हा टूल फिरवून बोअरिंग केले जातेतेव्हा कार्यवस्तू आणि फिक्श्चर यांच्या जोडणीवर कार्यवस्तूच्या आकारात होणारा बदल अवलंबून असतो. जेव्हा कार्यवस्तू गोल फिरवून बोअरिंग केले जाते, तेव्हा कार्यवस्तूच्या आकारात होणारा बदल हा जॉ आणि कार्यवस्तू यांच्यामधील पृष्ठभागाच्या संपर्कावर (इंटरफेस) अवलंबून असतो. गोल फिरणाऱ्या टूलने यंत्रण करताना एक सोपी चाचणी घेता येते. कार्यवस्तू फिक्श्चरमध्ये बसविल्यानंतर ज्या भागात बोअरिंग करायचे आहे तिथे डायल इंडिकेटर ठेवायचा. रेस्ट पॅडवर संवेदक (सेन्सर)टेकेल इतकाच पकडीचा दाब ठेवून, डायल शून्यावर आणायची आणि पकडीचा दाब पाहिजे तेवढाच वाढवायचा. या दरम्यान डायलचा काटा हलला तर कार्यवस्तूचेविरूपण होत आहे हे समजते. डायल 90 अंशात फिरवून विरूपणाची दिशा लक्षात येईल. ही चाचणी त्याच भागावर केल्यास त्याचा गोलाकारितेवरील परिणाम लक्षात येईल.
जेव्हा दंडगोलाकारितेवर अगदी काटेकोर नियंत्रण मिळवायचे असेल आणि भोकाच्या आकारानुसार दोन डायल गेज लावता येतअसतील, तेव्हा भोकाच्या सुरुवातीला एक आणि शेवटी एक अशी दोन गेज लावली तर लांबीच्या दिशेने होणारे विरूपण समजून येईल.
या चाचण्यांवरून, यंत्रण करणाऱ्याला विरूपणाच्या स्वरुपाचा अंदाज येईल आणि यंत्रणाच्या चाचण्या घेण्याआधी आवश्यक ती कृती करून तो या विरूपणावर नियंत्रण मिळवू शकेल. या चाचण्या फिक्श्चर मशिनवर बसविण्यापूर्वीच घेतल्या तर मशिनचा वाया जाणारा वेळ वाचविता येईल.
आता लेथ मशिनवर (पारंपरिक किंवा सी.एन.सी. मशिन) बोअरिंग करताना काय होते ते बघू. साधारणपणे लेथवर 3 जॉ चक वापरला जातो. (चित्र क्र. 3) जॉचा वापर करून क्लॅम्पिंग करताना घर्षणजन्य बलामुळेपकड करणारे बल मिळते, जे यंत्रण बलाच्या विरुद्ध दिशेने काम करते. पण जॉने त्याच्या हालचालीच्या दिशेने लावलेले बल कार्यवस्तूचा आकार बिघडवू शकते. येथे स्थिर घर्षणाचे साधे सूत्र लागू पडते.
जर कार्यवस्तूची जाडी कमी असेल,तर विरूपण टाळणे अधिक आव्हानात्मक असते. अशावेळी घर्षणाचे बल वाढवून जॉने दिलेले बल कमी ठेवावे लागते. जॉचे बल कमी करण्यासाठी दाब तोच ठेवून संपर्क क्षेत्र वाढविणे हा पर्याय असतो. काही वेळा हे संपर्क क्षेत्र प्रति जॉ 1000 ते 1100 मिळेल असे विशेष जॉ बनवावे लागतात. (चित्र क्र. 4) या जॉचे कार्यवस्तूच्या आकाराला अनुरूप असे अचूक बोअरिंग करावे लागते. त्यामुळे कार्यवस्तूचे विरूपण होण्याची शक्यता कमी होते.
घर्षणाचा सहगुणक वाढविण्यासाठी जॉचा पृष्ठभाग खडबडीत करावा लागतो त्याला सरेशन कराव्या लागतात किंवा चरे पाडावे लागतात. पण सरेशनमुळे जॉने पकडलेल्या पृष्ठभागावर त्याच्या खुणा दिसतात. म्हणून जेव्हा पकडण्याचा पृष्ठभाग यंत्रण केलेला नसेल किंवा अशा खुणा चालत असतील तेव्हाच सरेशन केलेले जॉ वापरतात. या उपायांमुळे चकमुळे होणारे आकारातील विरूपण कमी करता येते.
स्पिंडलच्या ‘डायनॅमिक्स’चे परिणाम
स्पिंडल हा फिरणारा भाग असल्यामुळे त्याचा कार्यवस्तूच्या गोलाकारितेवर परिणाम होतो. कर्तन दाबामुळे चांगला स्पिंडल कधीही झटके/धक्के देत नाही. बेअरिंगमधील क्लिअरन्स वाढला तर स्पिंडल झटके देऊ शकतो. यंत्रण करताना स्पिंडल हालला तर कार्यवस्तू अपेक्षित गोलाकारात न होता लंबगोलाकार (ओव्हल) किंवा इतर आकाराची बनते. अशा आकाराच्या भोकांना जास्त लंबगोलाकारिता आहे असे म्हणतात. बऱ्याच वेळा स्पिंडल नुसता फिरवला तर ’रनआऊट’ दाखवत नाही, पण त्यावर यंत्रण भार (लोड) आल्यावर हा दोष दिसून येतो. त्यामुळे मशिन उत्पादकाने सांगितलेले प्रतिबंधात्मक आणि अंदाजात्मक (प्रेडिक्टिव्ह) तंत्र वापरून स्पिंडलची वेळोवेळी देखभाल करणे गरजेचे असते.
कार्यवस्तू किंवा टूलची रचना किंवा वजनाची ठेवण अशी असू शकते की, ज्यामुळे ते स्पिंडलवर लावल्यावर स्पिंडलचे संतुलन बिघडते. विशेषकरून स्पिंडलचा प्रति मिनिटाला फिरण्याचा वेग वाढला की, गतिशीलतेधील असंतुलन वाढते आणि त्यामुळे स्पिंडल झटके देतो. यामुळे गोलाकारिता तर बिघडतेच पण टूलचे आर्युानही कमी होते. यावर उपाय म्हणजे, बोअरिंग टूलचे गतिशील संतुलन (डायनामिक बॅलन्सिंग) करणे किंवा लेथच्या बाबतीत कार्यवस्तू चकमध्ये बसविल्यावर संतुलन करणे होय. जेव्हा फिरणाऱ्या संपूर्ण भागाचे गतिशील संतुलन केलेले असते तेव्हा गोलाकारिता सुधारते.
यंत्रण बलाचे परिणाम
यंत्रण बलाच्या अक्षीय भागाचा विरूपणावर आणि त्यामुळे गोलाकारितेवर परिणाम होतो. या घटकाचा परिणाम कमीतकमी होण्यासाठी अचूक भोक पाडण्यासाठी धन (पॉझिटिव्ह) रेक असणारी टूल वापरावीत. त्यामुळे दर कार्यवस्तूागे येणारा टूलचा खर्च काहीवेळा वाढला तरी कार्यवस्तूधील दोष कमीतकमी होत असल्यामुळे रिजेक्शनमुळे होणारे नुकसान कमी होते. प्रक्रिया पुन्हापुन्हा ‘रीसेट’ करावी लागत नसल्यामुळे वाया जाणारा वेळ वाचतो. या सर्व गोष्टींचा विचार करून योग्य तो निर्णय घ्यावा लागतो.
रेडियल यंत्रण करताना निर्माण होणाऱ्या बलावर फिनिशिंग करतेवेळी काढावयाचे मटेरियल आणि टूलची नोज त्रिज्या यांचाही परिणाम होतो. पण पृष्ठभागाच्या खरबरीतपणावरील नियंत्रणासाठी याचा जास्त विचार करावा लागतो.
औष्णिक विरूपणामुळे होणारे परिणाम
कोरडे यंत्रण करताना निर्माण होणाऱ्या उष्णतेुळे कार्यवस्तूचे तापमान वाढते. जेव्हा कर्तनानंतर कार्यवस्तू फिक्श्चरमधून काढली जाते आणि मोकळ्या वातावरणात थंड होऊ दिली जाते, तेव्हा भोकाच्या पृष्ठभागातून उत्सर्जित होणारी उष्णता ही भोकाभोवतीच्या वजनाच्या वितरणानुसार असते. कार्यवस्तूच्या रचनेप्रमाणे उष्णता वेगवेगळ्या भागातून वेगवेगळ्या प्रमाणात बाहेर फेकली जाते, ज्यामुळे कार्यवस्तूचे विरूपण होऊ शकते, ज्याचा गोलाकारितेवर आणि दंडगोलाकारितेवर परिणाम होतो. असे औष्णिक कारणामुळे होणारे विरूपण टाळण्यासाठी शक्य तेव्हा शीतक वापरून यंत्रण करावे.
भोकाच्या लांबीमुळे होणारे परिणाम
भोकाची लांबी जर व्यासाच्या तुलनेत जास्त असेल, (L/D>>5) तर गोलाकारितेपेक्षा दंडगोलाकारितेवर जास्त परिणाम होण्याची शक्यता असते. जेव्हा अधिक लांबीचे बोअरिंग बार वापरले जातात आणि कार्यवस्तूची रचना आणि इतर अडचणीमुळे लांबी/व्यास हे गुणोत्तर योग्य ठेवणे शक्य नसते तेव्हा लंबगोलाकारितेवरील नियंत्रण कमी होण्याची शक्यता असते. बोअरिंग बारच्या कमी कडकपणामुळे (स्टिफनेस) त्याच्यावर कर्तन बलाचा परिणाम होऊन किती विचलित (डिफ्लेक्ट) होईल (चित्र क्र. 5) याचा अचूक अंदाज बांधणे अवघड असते. बोअरिंग बारचा कडकपणा वाढविण्यासाठी त्याच्या डिझाईन आणि उत्पादनात वेगवेगळी तंत्रे वापरली जातात. बोअरिंग बारचा कडकपणा वाढविण्यासाठी टूल उत्पादकांकडे वेगवेगळे उपाय असतात. एकंदर किंमतीचा विचार करून यापैकी योग्य उपायांची निवड केली जाते.
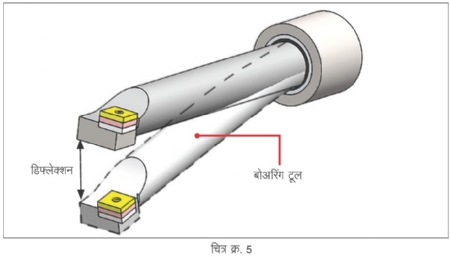
वेगवेगळ्या यंत्रणाच्यावेळी वर उल्लेख केलेल्या सर्व घटकांचा गोलाकारिता आणि दंडगोलाकारिता यांच्यावर कमी अधिक परिणाम होतो. सर्व घटकांचे योग्य मूल्यमापन करून आणि त्यांच्यावर नियंत्रण मिळविण्यासाठी प्रत्येक यंत्रणाच्या बाबतीत योग्य ते उपाय करावे लागतात. काहीवेळी वर उल्लेख केलेल्यापैकी काही घटकांचा परिणाम होत नाही पण वर्तुळाकार किंवा दंडगोलाकार कार्यवस्तूचे उत्पादन करताना हे सर्व घटक लक्षात ठेवणे जरुरीचे आहे.
राजेश म्हारोळकर यांत्रिकी अभियंते असून, ते ’श्रीनिवास इंजिनिअरिंग ऑटो कंपोनंटस् प्रा. लि.’चे संचालक आहेत. ही कंपनी ट्रॅक्टरचे कंपोनंट आणि ऑटोमोटिव्ह उद्योगांना आयर्न कास्टिंग आणि प्रिसिजन मशिनिंगबाबत सेवा देते.