चिप ब्रेकिंगवर प्रभाव टाकणाऱ्या सर्व घटकांचे वर्णन मागील अंकात (जुलै, 2018) केले आहे आणि वेगवेगळ्या आयएसओ मटेरियल समूहामध्ये त्यांच्या यंत्रणक्षमतेवर आधारित चिप ब्रेकिंगचे नैसर्गिक स्वरूप त्यातून स्पष्ट केले आहे. या लेखात आपण उत्पादनात खंड येणार नाही अथवा कार्यवस्तूच्या पृष्ठीय फिनिशचे नुकसान होणार नाही यासाठी चिपवर नियंत्रण करण्याचे विविध उपाय पाहणार आहोत.
1. टूल जॉमेट्री
यंत्रणाची क्रिया बहुतांशी टूल जॉमेट्रीद्वारा ठरविली जाते. विविध कार्यवस्तूंमधील धातू कापून चिपच्या स्वरुपात सुलभपणे बाहेर काढण्यासाठी टूल जॉमेट्रीचे डिझाईन केले जाते. एक मजबूत कटिंग एज पुरविणे आणि चिपला तोडून एका आटोपशीर आकारामध्ये तिचे रूपांतर करणे, हेसुद्धा टूलच्या जॉमेट्रीद्वारेच निर्धारित केले जाते. बऱ्याच इंडेक्सेबल इन्सर्टमध्ये लहान काप घेताना कोपऱ्याजवळ चिप ब्रेकिंगचे कार्य आणि यंत्रण कडेला लागून मोठ्या खोलीचे काप घेण्याचे कार्य यांचे संयोजन केलेले असते. प्रत्येक इन्सर्टची जॉमेट्री एका विशिष्ट कामासाठी सरकवेग आणि कापाची खोली यांच्या शिफारस केलेल्या रेंजसाठी विकसित केलेली असते.
आधुनिक इंडेक्सेबल इन्सर्ट हे कर्तनाची क्रिया, संपर्क लांबी, चिप ब्रेकिंग यासाठी इष्टतम चिप निर्मिती करणारे कोन, फ्लॅट आणि त्रिज्यांचे एक क्लिष्ट संयोजन असते. बहुतेक इन्सर्टमध्ये रेक कोन धन (+) असतो, परंतु हत्यारधारकामध्ये (टूल होल्डर) त्याला ऋण (-) दिशेत कलवता येण्याची सोय असते. या संयोजनामुळे चिप निर्मिती चांगली होते आणि कर्तनाची क्रिया सुकर होते. यंत्रण कड मजबूत करण्यासाठी जॉमेट्रीच्या कार्यशील क्षेत्रानुसार निरनिराळ्या लांबीच्या ऋण प्राथमिक (प्रायमरी) लँड दिलेल्या असतात.
टूल मटेरियलसोबत इन्सर्ट जॉमेट्रीचा चिप ब्रेकिंग आराखडा (सरकवेग आणि कापाची खोली यांच्या शिफारस केलेल्या पल्ल्यासाठी) इन्सर्ट निवडण्यासाठी महत्त्वपूर्ण असतो. यामुळे आपल्याला इन्सर्ट जॉमेट्रीचे कार्यशील क्षेत्र समजण्यास मदत होते. उदाहरणार्थ, स्वीकारार्ह चिप नियंत्रण मिळविण्यासाठी कापाची खोली (ap) आणि सरकवेग (fn) जॉमेट्रीच्या चिप ब्रेकिंग क्षेत्राबरोबर (चित्र क्र. 1 मधील निळ्या रंगाच्या क्षेत्राने दर्शविलेल्या) जुळवून घेणे आवश्यक आहे.
• चिप ब्रेकिंग अतिशय कठीण असेल, तर इन्सर्ट तुटण्याची शक्यता असते.
• अतिशय लांब चिपमुळे यंत्रण प्रक्रियेत अडथळा येतो आणि पृष्ठभागाचा फिनिश खराब होतो.
सर्वसाधारणपणे टर्निंगची बहुतेक कामे रफिंग, सेमीफिनिशिंग आणि फिनिशिंग अशा तीन प्रकारात विभागता येतात. या प्रत्येक विभागातील कामांसाठी डिझाईन केलेल्या जॉमेट्रीमध्ये वेगवेगळी चिप ब्रेकिंग क्षेत्र असतात. याचे साधारण स्वरूप तक्ता क्र. 1 आणि चित्र क्र. 2 मध्ये दिले आहे. या विचारातून कामाच्या प्रत्येक क्षेत्रासाठी इन्सर्ट विकसित केले जातात.
कामातील निरनिराळ्या आवश्यकतेनुसार मायक्रो आणि मॅक्रो जॉमेट्री वापरल्या जातात. सर्वच यंत्रण कडांवर विशिष्ट साईझ आणि शेपपर्यंत मायक्रो एज स्तरावर एज राऊंडिंग (ईआर) केले जाते, परंतु प्राथमिक लँडवर मॅक्रो जॉमेट्रीच्या डिझाईनमध्ये रुंदी आणि कोन यांच्यात फरक असू शकतात.
स्टेनलेस स्टील, आयएसओ-एम विभाग यांच्यासाठीची जॉमेट्री आयएसओ-पी मटेरियलपेक्षा अधिक धन (+) असते आणि कडा अधिक तीक्ष्ण असतात. कास्ट आयर्नच्या आयएसओ-के विभागातील जॉमेट्री अधिक ऋण (-) असू शकते, कारण या मटेरियलमधून निघणाऱ्या चिप अतिशय सहजपणे तुटू शकतात.
(चित्र क्र. 3)
आयएसओ-एम विभागातील मार्टेनसिटिक आणि ड्युप्लेक्स स्टेनलेस स्टील आणि आयएसओ-एच विभागातील उष्णतारोधक सुपर संमिश्र धातुंच्या बाबतीत चिपवरील नियंत्रण तर अधिक अवघड होत जातेच पण यंत्रण करणेही सोपे नसते. आयएसओ-एच आणि आयएसओ-एम विभागातील काही ठिकाणी टूल जॉमेट्रीला मजबूत बनविण्यासाठी अतिरिक्त उपाय योजावे लागतात. इथे त्यांची थोडक्यात माहिती घेऊ.
1. शीतक
उच्च दाबातील शीतक विशिष्ट दिशेने फवारून यंत्रण कडेपासून चिप सुटी केली जाते आणि अशा प्रकारे तिच्यावर नियंत्रण ठेवले जाते.
उच्च दाबातील शीतक हे चिपचा खालचा पृष्ठभाग आणि इन्सर्टचा वरचा पृष्ठभाग यांच्यामध्ये पाचरीसारखे काम करून फट पाडते. शीतकाचा सामान्य प्रवाह चिपवर काय परिणाम करतो ते आधी पाहू. चित्र क्र. 4 मध्ये आपल्याला दिसते की, इन्सर्टचा फारच कमी भाग शीतकाच्या संपर्कात येत आहे आणि चिप शीतकाला इन्सर्टपर्यंत पोहोचण्यास अडथळा आणत आहे. त्यामुळे चिप आणि इन्सर्ट यांच्यामध्ये शीतक शिरकाव करू शकत नाही. काम करताना हार्डनिंग होणाऱ्या मटेरियलमध्ये चिप अधिकच जाड आणि जड होत जाते आणि लगेचच मूळ मटेरियलसोबत वेल्ड झाल्यासारखी चिकटल्यामुळे त्यातून टूलचे मोठे नुकसान होते. यंत्रण वेग आणि सरकवेग कमी करून आणि धारदार यंत्रण कड वापरून यावर परंपरागत पद्धतीमध्ये मार्ग काढला जातो. परंतु असे केल्यामुळे टूलचे आयुर्मान कमी होते आणि प्रक्रियेच्या सुरक्षिततेवर गंभीर प्रश्नचिन्ह उभे राहते, कारण अशा प्रकारचे टूल फेल्युअर कधी होईल ते सांगता येत नाही. त्यासोबत उत्पादकताही कमी होते आणि मग आयएसओ-एम विभागातील मार्टेनसिटिक आणि ड्युप्लेक्स स्टेनलेस स्टील आणि आयएसओ-एस-एच.आर.एस.ए. यांना ‘यंत्रण करण्यास अवघड’ असे म्हणायला सुरुवात होते.
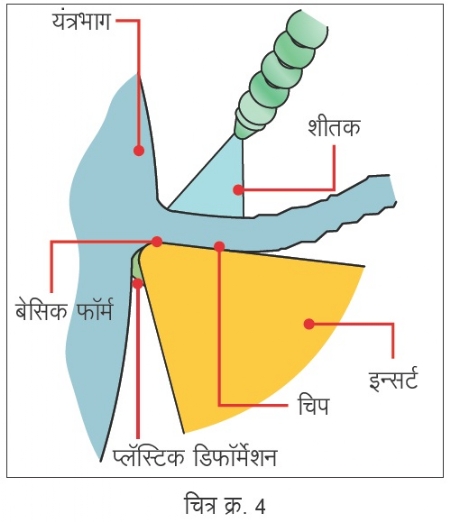
उपलब्ध असलेली कटिंग टूल (इष्टतमीकरण केलेल्या नॉझलमधून शीतकाचा थेट प्रवाह असलेली टूल) आणि उच्च दाबाच्या शीतक प्रणाली (चिप ब्लास्टर प्रकारच्या) या दोन्हीमध्ये आज प्रगत तंत्रज्ञान उपलब्ध झाले आहे. यात चिप आणि इन्सर्टच्या पृष्ठभागांच्यामध्ये उच्च दाबाने शीतक फवारले जाते, ज्यामुळे चिप ब्रेकिंगची गती वाढते, यंत्रण कड कार्यक्षमतेने काप घेते आणि काम करताना होणारे हार्डनिंग कमीत कमी होते. अशारीतीने प्रक्रियेतील सुरक्षितता आणि उत्पादकता दोन्ही वाढतात.
येथे मुख्यत्वे पुढील गोष्टी काम करतात.
• शीतकाचे उच्च गतीचे जेट, इन्सर्टचा वरचा पृष्ठभाग आणि चिपचा खालचा पृष्ठभाग यांच्यामध्ये एक हायड्रॉलिक पाचर (वेज) निर्माण करते.
• शीतक संपर्क झोनमध्ये (A) इन्सर्टला जागेवरच थंड करते.
• शीतक चिपला लवकरात लवकर इन्सर्टपासून दूर ढकलते आणि त्यामुळे इन्सर्टची (B) कमी झीज होते.
• चिपचे लहान तुकडे करण्यात आणि त्यांना यंत्रण क्षेत्रातून बाहेर काढण्यात मदत करते.
दाब = बल/क्षेत्रफळ या तत्त्वावर हे चिप ब्रेकिंगचे काम केले जाते. हत्यारधारकामध्ये वापरलेल्या नॉझलमधून येणाऱ्या शीतकाची गती नॉझलच्या छिद्राचा आकार कमी करून वाढविली जाते. उच्च दाबाचे शीतक असल्याने ते कमी आकाराच्या छिद्रातून वेगाने जाऊ शकते आणि त्याचा रोख चिपचा खालचा पृष्ठभाग आणि इन्सर्ट वरचा पृष्ठभाग यांच्यामध्ये ठेवणे शक्य होते. (चित्र क्र. 5 आणि 6)
या तंत्रामुळे सामान्य शीतक वापरून अवघड मटेरियलसाठी रफिंगच्या कामातील यंत्रण वेग 20-50 टक्क्याने वाढविता येतो. सामान्य शीतकामुळे आणि शीतक 70 बार मुळे होणारे चिप ब्रेकिंग चित्र क्र. 7A आणि 7B मध्ये दाखविले आहे.
2. ट्रॉकॉइडल टर्निंग
यामध्ये हलके (कमी खोलीचे) काप आणि उच्च सरकवेग ठेवून, ज्या दराने उष्णता निर्माण होऊन पुढे जाते त्यापेक्षा अधिक वेगाने टूल धावेल अशी व्यवस्था केलेली असते. त्यामुळे काम करताना कठिणीकरण होत नाही. हलके काप आणि उच्च सरकवेगामुळे नियंत्रण करता येण्याजोग्या चिप निर्माण होतात. एच.आर.एस.ए. मटेरियलचे यंत्रण करताना इन्सर्टच्या नॉचची झीज होणे ही प्रमुख समस्या असते. जेव्हा कापाची खोली नोज त्रिज्येपेक्षा मोठी असते आणि प्रवेश कोन 900 असतो, तेव्हा सर्वात वाईट नॉचिंग होते.
कापाची खोली हा प्रभावशाली घटक आहे. कापाची खोली नोज त्रिज्येपेक्षा लहान असल्यावर इन्सर्टवरील कोन 900 असला तरीही परिणामी प्रवेश कोन कमी होतो. त्यामुळे 25 ते 45 अंशाचा प्रवेश कोन वापरा.
कापाच्या बदलणाऱ्या खोलीसह गोल इन्सर्टचा वापर हा पर्याय सर्वाधिक पसंतीचा असतो, कारण यात फक्त कापाची खोली बदलल्यामुळे आपल्याला 25 ते 45 अंशाचा kr (प्रवेश कोन) मिळतो. उदाहरणार्थ, जर कापाची खोली = 0.15 x गोल इन्सर्टचा व्यास अशी प्रोग्रॅम केली असेल, तर सुमारे 45 अंशाचा कोन मिळतो. (चित्र क्र. 8)
जेव्हा प्रवेश कोन 450 पेक्षा कमी असतो, तेव्हा सर्वोत्तम कामगिरी मिळते. यात 0.15 x इन्सर्ट व्यास इतकी कापाची खोली मिळते. (कापाची अधिकतम खोली, 0.25 x व्यासपेक्षा जास्त नसावी). कापाची खोली नोज त्रिज्येपेक्षा कमी असणाऱ्या स्टँडर्ड इन्सर्टमध्येही हे तत्त्व लागू आहे. व्यासाच्या 25% पेक्षा मोठ्या कापाच्या खोलीसाठी 450 हा स्थिर प्रवेश कोन ठेवून स्क्वेअर इन्सर्ट वापरणे सर्वात उत्तम असते.
तथापि, उपलब्ध असलेल्या इन्सर्टमध्ये गोल इन्सर्ट सर्वात मजबूत असतात आणि त्यांच्यामुळे उच्च उत्पादकता मिळते. परंतु गोल इन्सर्ट कंपनाच्या समस्येपुढे टिकत नाहीत. त्यामुळे एच.आर.एस.ए. मटेरियलमध्ये काम करताना प्रोग्रॅमिंग धोरणांवर चांगले नियंत्रण ठेवून गोल इन्सर्ट कसे वापरायचे हे समजून घेणे जरुरीचे आहे.
क) जेव्हा गोल इन्सर्ट वापरले जातात, तेव्हा कोपऱ्यामध्ये प्लंजिंग किंवा प्रोफाईलिंग करताना ‘रॅप अराउंड’ ही समस्या उद्भवते. कोपऱ्यामध्ये कोनीय एंगेजमेंट अधिक असल्याने यंत्रण दाब फारच वाढतो आणि सरकवेग कमी करावा लागतो. ही समस्या कमी करण्यासाठी इष्टतम प्रोग्रॅमिंग धोरणांसोबत लहान त्रिज्येचे इन्सर्ट वापरावे.
चित्र क्र. 9 मधून आपल्याला दिसते की, जर कार्यवस्तूच्या त्रिज्येच्या तुलनेत इन्सर्ट त्रिज्या फार मोठी असेल तर, एक तर इन्सर्ट त्रिज्या कमी करावी लागेल अथवा कार्यवस्तूची त्रिज्या वाढवावी लागेल. त्रिज्येतील ‘रॅप अराउंड’ समस्येमुळे कापाची खोली जशी वाढते, तसा सरकवेग कमी करावा लागतो. कार्यवस्तूची त्रिज्या आणि इन्सर्ट त्रिज्या यांच्यातील फरक जितका अधिक, तितका सरकवेग कमी कमी करावा लागतो. तथापि, समांतर कापाच्या तुलनेत अर्धा सरकवेग वापरणे हा ठोकताळा वापरणे उपयुक्त असते. (चित्र क्र. 10)
ख) कार्यवस्तूचे यंत्रण करताना फेस आणि व्यास एकाच वेळी यंत्रण करावे लागणार नाहीत याची काळजी घ्यावी, कारण त्यामुळे कापाची खोली वाढेल आणि ‘रॅप अराउंड’ची समस्या उद्भवेल.
ग) एच.आर.एस.ए. मटेरियलमध्ये ट्रॉकॉइडल टर्निंगसारखी तंत्रे वापरली की, त्यातील कापाच्या कमी खोलीमुळे आपोआपच लहान प्रवेश कोन (चित्र क्र. 11) मिळतील. तसेच, प्रोग्रॅमला लहान लहान तुकड्यांत विभागून सर्व प्रोफाईलिंगच्या कामात ही पद्धत वापरता येईल. गोल इन्सर्ट वापरताना किंवा त्रिज्या असलेले ग्रुव्हिंग इन्सर्ट वापरताना त्यांच्या कडेचा सर्वोत्तम उपयोग करून घेण्यासाठी पाठोपाठच्या पासेसची दिशा एकमेकांविरुद्ध ठेवता येईल.
ट्रॉकॉइडल टर्निंगमधील हलके काप घेताना आपण एच.एस.एम.मध्ये वापरतो तसे मोठे सरकवेग वापरू शकू. त्यामुळे यंत्रणादरम्यान हार्डनिंग होणार नाही, चिप नियंत्रण चांगले राहील आणि त्याच्या परिणामस्वरूपे सुरक्षितता आणि उत्पादकता यांच्यात वाढ होईल.
वरील सर्व विवेचनातून असा निष्कर्ष काढता येईल की, मटेरियलचे यंत्रण जसे अधिकाधिक अवघड होत जाते, तसे चांगल्या चिप नियंत्रणासाठी केवळ टूल जॉमेट्री पुरेशी नाही. त्यासाठी स्मार्ट प्रोग्रॅमिंग आणि उच्च दाबाचे शीतक अशा तंत्रांचा वापर करणे आवश्यक असते, हे लक्षात घेणे महत्त्वाचे आहे.
रवि नाईक यांना टूलिंग क्षेत्रातील 40 हून अधिक वर्षाचा अनुभव असून ते टूलिंग आणि मशिनिंग ॲप्लिकेशन विषयक सल्लागार आहेत.