अभियांत्रिकी आरेखनांमध्ये बऱ्याचवेळा ‘’ चिन्ह वापरले जाते. अचूक स्थान (ट्रू पोझिशन) दर्शविण्यासाठी या चिन्हाचा वापर केला जातो. या लेखात आपण अचूक स्थानाचे वेगवेगळ्या संदर्भात असणारे महत्त्व, अचूक स्थानामध्ये फरक पाडणारे विविध घटक आणि या फरकावर नियंत्रण ठेवण्याचे विविध उपाय या सर्व गोष्टी समजावून घेणार आहोत.
एखाद्या आकाराच्या मध्य (सेंटर), अक्ष किंवा मध्यप्रतल (सेंटर प्लेन) या घटकांना त्यांच्या अपेक्षित अचूक स्थानापासून दूर जाण्याची मर्यादा दर्शविणारे क्षेत्र म्हणजे अचूक स्थान होय. ज्या अर्थी या व्याख्येमध्ये ’क्षेत्र’ हा शब्द वापरला आहे, त्या अर्थी या क्षेत्राचा आकार निश्चित करावा लागतो. सर्वसाधारणपणे हे क्षेत्र वर्तुळाकार असते आणि वर्तुळाच्या व्यासाद्वारे ही मर्यादा सहजपणे दाखविता येते.
चित्र क्र. 1 मध्ये हे स्थान ठरविताना दोन संदर्भ वापरले आहेत.
• संदर्भ ‘A’ - एक प्रतल आहे.
• संदर्भ ‘B’ - एक छिद्र आहे.
‘C’ छिद्राचा अक्ष आणि ‘A’ संदर्भ प्रतलाचा छेदबिंदू, हा अचूक स्थानाला केंद्रस्थानी धरून काढलेल्या 0.1 मिमी व्यासाच्या वर्तुळाच्या आत असला पाहिजे. अशा परिस्थितीत ‘C’ छिद्राच्या व्यासाचा त्या स्थानाच्या टॉलरन्सवर काहीही परिणाम होत नाही. मात्र छिद्राचा प्रत्यक्ष व्यास मर्यादेमध्येच परंतु थोडा अधिक असेल, तर स्थान मर्यादेबाहेर असेल किंवा अक्षीय स्थानामध्ये फरक असेल तरी, ते वाढलेल्या व्यासात बसू शकेल (चित्र क्र. 2) इतक्या प्रमाणात असल्यामुळे जोडणी होऊ शकते. आरेखकाला ही परिस्थिती दाखविण्यासाठी मटेरियलची कमाल परिस्थितीच आणि किमान परिस्थिती (छिद्र किंवा शाफ्ट असेल त्याप्रमाणे) त्या वैशिष्ट्यांच्या नियंत्रण तक्त्यांमध्ये दाखवावी लागते. चित्र क्र. 1 मधील उदाहरणात, समजा आरेखकाने वैशिष्ट्य (फीचर) नियंत्रण तक्ता चित्र क्र. 3 प्रमाणे दाखविला, तर याचा अर्थ 0.1 मिमी. टॉलरन्स ‘C’ छिद्राच्या कमाल मटेरियल परिस्थितीमध्ये लागू होतो. म्हणजेच छिद्राचा आकार कमीतकमी (10 मिमी.) असताना, स्थानाचा टॉलरन्स 0.1 मिमी. आहे. समजा प्रत्यक्ष छिद्राचा आकार 10.02 मिमी. असेल, तर हाच टॉलरन्स 0.12 मिमी. होईल. छिद्राचा आकार 10.04 मिमी. असेल, तर त्याचा टॉलरन्स 0.14 मिमी. होईल.
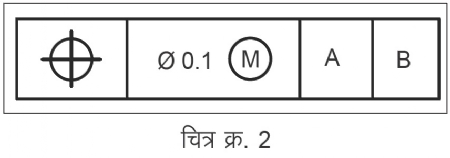
स्थानाच्या नियंत्रणाच्या मर्यादा देऊन आरेखक अपेक्षित कामाच्या गरजा कमी शब्दात अचूकपणे स्पष्ट करतो. अचूक स्थान सांगण्यासाठी त्याचा अक्ष, मध्यबिंदू किंवा मध्यप्रतल हे घटक देऊन स्पष्ट करावे लागते. त्याशिवाय त्या मटेरियलची स्थिती (कमाल किंवा किमान) द्यावी लागते. भूमिती योग्य पद्धतीने स्पष्ट होण्यासाठी त्याची मदत होते. जेव्हा आकाराच्या स्थितीकडे विशेष लक्ष देण्याची गरज असते, तेव्हा आरेखकाला गोलाकार, लंबगोलाकार, सपाटपणा किंवा पृष्ठभागाचा आकार या गोष्टी वेगळ्या स्पष्ट कराव्या लागतात. सरळ किंवा तिरकी छिद्रे, आटे असलेली छिद्रे, मोठी छिद्रे, बाह्य व्यास, कार्यवस्तूचा मध्यबिंदू आणि त्याचा फोकस, खाचा, पोकळ्या (गॅप) आणि उंचवटे (प्रोजेक्शन) अशा कामांसाठी स्थानावरील टॉलरन्स अगदी बारकाईने दिले जातात. यासाठी मिलिंग, ड्रिलिंग, बोअरिंग, ग्रार्ईंडिंग इत्यादी प्रक्रिया कराव्या लागतात.
आता आपण प्रक्रियांमधील स्थानावर परिणाम करणाऱ्या घटकांकडे बघू. स्थानाची अचूकता मर्यादेमध्ये राहण्यासाठी प्रक्रियेवर दोन मूलभूत प्रकारे नियंत्रण ठेवावे लागते.
1. यंत्रण सुरू करण्यापूर्वी संदर्भ स्थानापासून टूल योग्य ठिकाणी आहे याची खात्री करावी.
2. चल (डायनॅमिक) परिस्थितीवर यंत्रण करताना नियंत्रण ठेवावे.
मोठ्या संख्येने यंत्रभागांचे उत्पादन करताना प्रत्येक यंत्रभागासाठी ही नियंत्रणे काम करीत आहेत, याची वारंवार खात्री करावी लागते. यंत्रण सुरू करण्यापूर्वी टूल योग्य जागी आहे, याची खात्री करण्यासाठी काय करावे लागते, ते प्रथम समजावून घेऊ.
मशिनची स्थानजन्य (पोझिशनिंग) अचूकता आणि पुनरावर्तनक्षमता (रिपीटॅबिलिटी) यांची यामध्ये महत्त्चाची भूमिका असते. मशिनची स्थानजन्य अचूकता म्हणजे, टूल/कार्यवस्तू एका जागेवरून दुसऱ्या जागेवर हलताना अपेक्षित असलेल्या अंतराइतकीच हालचाल करण्याची क्षमता होय. पुनरावर्तनक्षमता म्हणजे, एकाच जागेवर पुन्हा पुन्हा अचूकतेने येऊ शकण्याची मशिनची क्षमता. लेझर इंटरफेरोमीटरच्या साहाय्याने मशिनच्या अक्षांचे प्रमाणीकरण (कॅलिब्रेशन) करून मशिनची स्थानजन्य अचूकता आणि पुनरावर्तनक्षमता निश्चित करता येते. (चित्र क्र. 4) पुनरावर्तनक्षमतेमध्ये काही अडचणी आढळल्यास मशिनची पातळी समान करून मशिनची देखभाल करावी लागते. दरवर्षी एकदा मशिनचे प्रमाणीकरण करणे आवश्यक असते. ज्या मशिनमध्ये हालचालींचे मापन अप्रत्यक्षपणे म्हणजे लीड स्क्रूच्या फेर्यांची मोजणी करून केले जाते, अशा मशिनसाठी हे करणे जास्त गरजेचे असते. ज्या मशिनमध्ये लिनिअर स्केल वापरून (किंवा रोटरी टेबलचा अँग्युलर एनकोडर) स्लाईडच्या हालचालींचे मापन केले जाते, अशा मशिनमध्ये स्थानजन्य अचूकतेमध्ये त्रुटी येण्याची शक्यता कमी असते. मशिनमधील झीज आणि काही यंत्रभागांचे तुटणे अशा कारणांमुळे स्थानजन्य अचूकतेमध्ये जास्त फरक पडू लागतो.
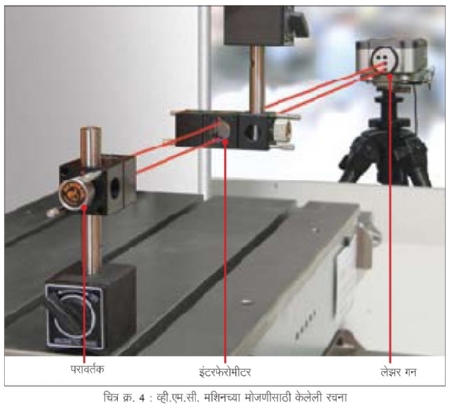
पुढचा घटक म्हणजे यंत्रणासाठी वापरण्यात येणाऱ्या फिक्श्चरची मशिनशी योग्य आणि भक्कम अलाईनमेंट करणे. टेकू, स्थान आणि दिशा (ओरिएंटेशन) या तिन्ही बाबतीत यंत्रणाच्या फिक्श्चरचे आरेखन आणि उत्पादन होताना जास्तीत जास्त अचूकता असणे अपेक्षित असते. ढोबळमानाने असे म्हणता येईल की, यंत्रणासाठी फिक्श्चर तयार करताना फिक्श्चरमध्ये तयार होणाऱ्या कार्यवस्तूंच्या टॉलरन्सच्या जास्तीतजास्त 10 टक्के टॉलरन्समध्ये त्या फिक्श्चरच्या भागांचे उत्पादन करावे लागते. फिक्श्चरचे टेकणारे, स्थान निश्चित करणारे आणि दिशा ठरविणारे भाग तसेच टूलला दिशा देणारे भाग यांची झीजविरोध क्षमता खूप जास्त असावी लागते. अलाईनमेंट सहजपणे करता यावी यासाठी फिक्श्चरचे आरेखन करताना पहिल्या भागापासूनच संदर्भासाठीची (रेफरन्स) छिद्रे, कडा योग्य मापांची द्यावीत.
मशिन योग्य असल्याची आणि फिक्श्चर अलाईन केल्याची खात्री केली की, मग कार्यवस्तूचे जे घटक, टेकणे, स्थान आणि दिशा (ओरिएंटेशन) यासाठी महत्त्वाचे असतात, ते योग्य नियंत्रणात आहेत याची निश्चिती करावी. या घटकांमध्ये अपेक्षेपेक्षा अधिक फरक असतील, तर यंत्रणानंतर त्या भागाच्या स्थानातील टॉलरन्स साध्य होतील अशी अपेक्षा करणे व्यर्थ ठरेल.
प्रोग्रॅमवर चालणाऱ्या मशिनवर प्रोग्रॅम करताना कोणतीही चूक न करता स्थान ठरवावे लागते. घटकांवर एकाच बाजूचे (युनिलॅटरल) टॉलरन्स दिले असतील, तर प्रोग्रॅममध्ये नाममात्र मूल्य (नॉमिनल व्हॅल्यू) ‘मीन’वर गृहीत धरून गणित करावे लागते. उदाहरणार्थ, एखादा कोऑर्डिनेट 100+0.2 दाखविला असेल, तर प्रोग्रॅमरने काळजी घेऊन 100.00 हे नाममात्र मूल्य न वापरता 100.10 हे नाममात्र मूल्य घेतले पाहिजे. वरील पद्धतीने अचूकपणे मांडणी केल्यानंतर आपण आता यंत्रण प्रक्रिया चालू असताना स्थानावर परिणाम करणाऱ्या घटकांकडे पाहू.
चल (डायनॅमिक) यंत्रण परिस्थितीत अचूक स्थानावर नियंत्रण करण्यासाठी पुढील बाबी महत्त्वाच्या असतात.
1. कार्यवस्तूचे यंत्रणभारामुळे होणारे विरूपण (डिस्टॉर्शन) किंवा विस्थापन (डिफ्लेक्शन)
योग्य पद्धतीने फिक्श्चरचे आरेखन करून आणि योग्य अवस्थेतील कार्यवस्तू वापरून यंत्रणादरम्यान कार्यवस्तूचे यंत्रणभारामुळे होणारे विरूपण किंवा विस्थापन थांबविता येते. उदाहरणार्थ, कार्यवस्तूचे फिक्श्चरवरील स्थान निश्चित करण्यासाठी दिलेल्या छिद्राचा व्यास जर गरजेपेक्षा जास्त असेल, तर कार्यवस्तूच्या स्थानामध्ये मोठ्या चुका होऊ शकतात. जर कार्यवस्तू टेकण्याची जागा, स्थान आणि दिशा ठरविणारे भाग खडबडीत आणि अनियमित असतील, तर यंत्रण करताना यंत्रणभारामुळे कार्यवस्तू फिक्श्चरमधून सरकणार नाही याची काळजी घ्यावी लागते. यासाठी कार्यवस्तू पकडणारे भाग कठीण (हार्ड) केलेलेच असले पाहिजेत आणि त्यांचे कार्यवस्तूच्या संपर्कात येणारे पृष्ठभाग चरे (सरेशन) पाडलेले (चित्र क्र. 5) किंवा चेकर्ड असले पाहिजेत. कार्यवस्तू पकडण्याचा दाब योग्य असला पाहिजे. एखाद्या प्रक्रियेत अतिशय कमी स्थानीय टॉलरन्स असलेल्या यंत्रभागांचे उत्पादन करायचे असेल, तर संदर्भ म्हणून वापरायचे पृष्ठभाग यंत्रण केलेले असावेत अशी अपेक्षा असते.
2. यंत्रणावेळी टूलचे विस्थापन
जेव्हा यंत्रणावेळी टूलचा कार्यवस्तूला स्पर्श होतो, तेव्हा पृष्ठभागाच्या अनियमिततेमुळे टूलचा अक्ष विस्थापित होण्याची परिस्थिती निर्माण होते. अतिशय काटेकोर मर्यादांमध्ये असलेले स्थान साध्य करण्यासाठी सुरुवातीला पूरक यंत्रण परिस्थिती निर्माण करणे महत्त्वाचे असते. उदाहरणार्थ, काटेकोर मर्यादांमध्ये छिद्रे करताना मुख्य ड्रिलने काम करण्याआधी सेंटर ड्रिल वापरून मध्यबिंदू तयार करून घेतला, (चित्र क्र. 6) तर सुरुवातीलाच ड्रिल विस्थापित होण्याची शक्यता कमीतकमी होते. टूलच्या लवचीकपणावर टूलचे विस्थापित होणे कमी जास्त होते. उदाहरणार्थ, एच.एस.एस. ड्रिल हे टंगस्टन कार्बाईड ड्रिलपेक्षा जास्त लवचीक असल्यामुळे ते जास्त विस्थापित होते. कर्तनकडेची झीज झाल्यावर टूल जास्त विस्थापित व्हायला लागते. झिजलेल्या कडांमुळे टूलचे विस्थापन सुरू होण्यापूर्वी टूल बदलणे महत्त्वाचे असते. टूलच्या मटेरियलशिवाय त्याचा सडपातळपणासुद्धा (लांबी आणि व्यास यांचे 5 पेक्षा जास्त गुणोत्तर) टूलच्या स्थितीवर परिणाम करणारा महत्त्वाचा घटक आहे. हे L/D गुणोत्तर जेवढे जास्त, तेवढे टूल जास्त लवचीक असते आणि जास्त विस्थापित होते.
जेव्हा जास्त गुणोत्तर असलेले टूल वापरणे अपरिहार्य असते, तेव्हा टूलला आवश्यक तसा मार्गदर्शक (गाईड) दिल्यामुळे टूलच्या विस्थापनाचे प्रमाण कमी करता येते.
यंत्रण करताना निर्माण झालेल्या चिप हा आणखी एक नको असलेला परंतु प्रक्रियेचा अविभाज्य घटक आहे. चिप तातडीने न काढल्यास त्या टूल आणि कार्यवस्तू यांच्यामध्ये अडकून राहतात आणि टूलला विस्थापित करतात. त्यामुळे चिप वेळोवेळी काढल्या जातील आणि शीतकाच्या साहाय्याने वाहून नेल्या जातील याची खबरदारी घ्यावी लागते. उच्च दाबाच्या शीतकाचा वापर करून केलेल्या यंत्रणामध्ये स्थानाच्या मर्यादांसंबंधी अगदी चांगले निकाल मिळतात आणि टूलचे आयुष्यही वाढते, तसेच यंत्रण वेगाने होते.
टूलला रीग्राईंडिंग केल्यावर त्याच्या कर्तनकडा दर्जेदार करणे हा टूलचे विस्थापन कमी करण्यासाठी महत्त्वाचा मुद्दा असतो. यासाठी टूल अँड कटर ग्राइंडरवर योग्य ती काळजी घेऊन रीग्राईंडिंग करून चांगली समतोल कर्तन कड मिळवता येते.
3. फिक्श्चरवर कार्यवस्तू व्यवस्थित न पकडल्यामुळे होणारे विरूपण
प्रक्रियेतील सर्व घटकांवर म्हणजे मशिनची अचूकता आणि टूलचे गुणधर्म यांच्यावर नियंत्रण मिळविल्यावर उत्पादन केलेली कार्यवस्तू फिक्श्चरमध्ये पकडलेली असताना तिचा आकार स्थानीय मर्यादांमध्ये असतो. कार्यवस्तू फिक्श्चरमध्ये पकडताना जर आकार बदलला गेला असेल, तर फिक्श्चरमधून काढल्यावर इलॅस्टिसिटीमुळे तिचे आकारमान बदलेल. त्यामुळे काटेकोर मर्यादा असलेल्या कार्यवस्तूंचे यंत्रण करताना, त्यांच्या आकारात फिक्श्चरमध्ये पकडताना कमीतकमी बदल होईल याची काळजी घेणे गरजेचे असते. जास्त मटेरियल कापताना क्लॅम्पिंगचे बल (फोर्स) जास्त ठेवणे आणि प्रोग्रॅममध्ये M0 टाकून फिनिश कट काढायच्या आधी टॉर्क कमी करणे, हा यावर उत्तम उपाय ठरतो.
4. औष्णिक विरूपण
भौतिक विस्थापनाबरोबरच तापमानातील बदलांमुळेदेखील स्थानीय टॉलरन्समध्ये फरक पडू शकतो. यासाठी यंत्रण करताना कार्यवस्तूमध्ये निर्माण झालेली उष्णता योग्य शीतकांचा वापर करून कमीतकमी वेळात काढून घ्यावी लागते.
काम करतेवेळी वर नमूद केलेल्या सूचना आणि विविध उपायांचा अवलंब केल्यास अचूक स्थान मिळविण्यात निश्चित यश मिळेल.
9359104060
राजेश म्हारोळकर यांत्रिकी अभियंते असून, ते स्वतंत्र सल्लागार आहेत. ’श्रीनिवास इंजिनिअरिंग ऑटो कंपोनंटस् प्रा. लि.’चे ते संचालकदेखील आहेत. ही कंपनी ट्रॅक्टरचे कंपोनंट आणि ऑटोमोटिव्ह उद्योगांना आयर्न कास्टिंग आणि प्रिसिजन मशिनिंगबाबत सेवा देते.