मागील अंकातील लेखामध्ये आपण धातूंच्या कर्तनक्षमतेचा विचार केला आहे. त्याच अनुषंगाने ॲल्युमिनिअमच्या यंत्रणात घ्यावयाच्या उपाययोजनांबाबतही पाहिले आहे. ॲल्युमिनिअमचे यंत्रण करताना ज्याठिकाणी यंत्रण होते, त्या कर्तनबिंदूपाशी कमीतकमी उष्णता निर्माण होईल, अशी काळजी घेण्याचे महत्त्व अधोरेखित झाले आहे. अशाच प्रकारचा त्रास ॲल्युमिनिअमच्या ड्रिलिंगमध्येही होतो. ॲल्युमिनिअम कमी तापमानाला वितळत असल्यामुळे त्याचे ड्रिलिंग त्रासदायक ठरते.
सर्वसाधारणपणे स्टीलवर ड्रिलिंग करतानादेखील चिप बाहेर काढणे जिकिरीचे असते. चिप बाहेर न आल्यामुळे ड्रिल अडकून तुटण्याचे प्रकार स्टीलवर काम करताना होतात. यामध्ये ॲल्युमिनिअमचा मऊपणा आणि लवकर वितळण्याच्या गुणधर्माची भर पडते. हे टाळण्याकरिता ड्रिलिंगमधून तयार होणारी चिप लवकरात लवकर बाहेर निघणे आणि ती ड्रिलच्या अंतर्गत भागावर चिकटून राहणार नाही ही काळजी घेणे हे ॲल्युमिनिअमच्या ड्रिलिंगमधील मर्म आहे.
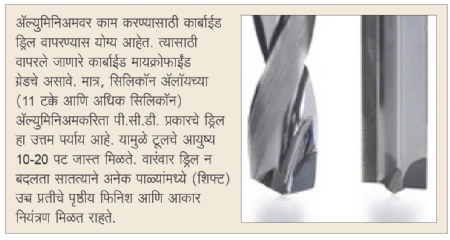
ॲल्युमिनिअममध्ये योग्य चिप तयार होणे आणि ती बाहेर काढणे याकडे लक्ष दिले पाहिजे. यासाठी टूलची रास्त भूमिती आणि सुयोग्य शीतक यांची गरज असते. ॲल्युमिनिअममध्ये असलेल्या ’बिल्टअप एज’ तयार होण्याच्या विशिष्ट गुणांमुळे जर योग्य त्या आकारात चिप तयार झाली नाही, तर टूलच्या कर्तनबिंदूवर ती चिकटते. या बिल्टअप एजमुळे टूलचा मूळ आकार बिघडून यंत्रण जास्तच त्रासदायक होते. पर्यायाने कर्तनबिंदूजवळ जास्त उष्णता तयार होऊन या चिप, ड्रिलच्या फ्ल्यूटमध्ये वितळून घट्ट होऊन बसतात, याला ’फ्ल्यूट क्लॉगिंग’ असे म्हणतात. अशा प्रकारात टूल तुटण्याची दाट शक्यता असते. हे टाळण्यासाठी ड्रिल निवडताना पुढील गोष्टींचा विचार करणे महत्त्वाचे ठरेल.
1. आजकाल कार्बाईड ड्रिल सहज उपलब्ध असतात. त्यांचा वापर हा एच.एस.एस. ड्रिलपेक्षा किफायतशीर आहे.
2. ड्रिलचा हेलिक्स कोन जास्त असला पाहिजे.
3. ड्रिलचा पॉर्ईंट कोन 130० ते 140० असावा.
4. ड्रिल केलेल्या भोकाचा आकार कायम राहण्यासाठी ’साईझिंग डायमीटर’ पॉलिश केलेला असावा.
5. चिप वहन सुधारण्याकरिता फ्ल्यूट पॉलिश करावे लागतात.
6. ॲल्युमिनिअमकरिता वापरल्या जाणाऱ्या कार्बाईड ड्रिलला लेपन (कोटिंग) करण्याची गरज नाही, त्याउलट लेपन करताना कर्तन कडेवर जे ’एज होनिंग’ केले जाते ते ॲल्युमिनिअमसाठी त्रासदायकच ठरते. कारण ॲल्युमिनिअमकरिता धारदार कडेची गरज असते. तसेच बहुतेक लेपनामध्ये ॲल्युमिनिअम नायट्राईडचा वापर होत असल्याने ते कार्यवस्तूबरोबर संयोग पावण्याची भीती असते. मात्र, जिथे सिलिकॉनच्या अतिरिक्त प्रभावामुळे ड्रिलची झीज वाढते, तिथे झिरकॉन नायट्राईड लेपन केलेली ड्रिल वापरली जातात.
7. साधारणपणे लेपन नसलेली आणि पॉलिश केलेली ड्रिल हाच चांगला पर्याय आहे.
8. या सर्व प्रकारच्या ड्रिलमध्ये अंतर्गत शीतक वहनाची नितांत गरज असते. या शीतकाचे वहन जास्त दाबाने झाले पाहिजे, जेणेकरून चिप वहन सुलभ झाले पाहिजे.
9. ड्रिलच्या तोंडाकडे वेब थिनिंग करून कर्तनास मदत केली पाहिजे.
अशा प्रकारची ड्रिल वापरताना जिथे भोकाची लांबी जास्त असते, तेव्हा तिथे चिप बाहेर येण्यास अडचण निर्माण होते. त्यावर उपाय म्हणून सरळ फ्ल्यूट असलेली, उच्च दर्जाचे पॉलिश असलेली आणि अंतर्गत शीतक वहनाची सोय असलेली ड्रिल हा पर्याय जास्त योग्य आहे. अशा ड्रिलमुळे भोकाचा आकार आणि गोलाई अधिक चांगली तयार होते. (चित्र क्र. 2)
Ø 25 मिमी.च्या पुढील भोकांकरिता इन्सर्ट असलेले ड्रिल वापरले जाते. त्यासाठी उच्च रेक असलेले इन्सर्ट उपलब्ध आहेत. तसेच डायमंडचे लेपन असलेल्या इन्सर्टचा पर्यायही आता आवाक्यात येत आहे. अर्थातच असे इन्सर्ट असलेल्या ड्रिलमध्ये शीतकाचा वापर आणि त्याचा दाब हे चिप वहनाकरिता कळीचे मुद्दे आहेत. स्टीलमधील चिप बाहेर काढण्यासाठी ड्रिल वारंवार बाहेर काढणे (वूड पेकिंग सायकल) यासारख्या क्रिया केल्या जातात, मात्र हे ॲल्युमिनिअमवर केल्यास भोकाचे आकारमान बिघडते. चिप योग्यप्रकारे तोडणारे इन्सर्ट निवडणे हेदेखील महत्त्वाचे आहे. उच्च वहन आणि उच्च दाब हे तत्व ॲल्युमिनिअमच्या शीतकासाठी लक्षात ठेवावे लागते.
जिथे भोकाची लांबी व्यासाच्या तुलनेत जास्त असते, तिथे गन ड्रिल, गन रीमरसारखी ड्रिलिंग टूल वापरावी लागतात. ॲल्युमिनिअमचा ’मॉड्युलस ऑफ इलॅस्टिसिटी’ जास्त असल्यामुळे कार्यवस्तूवर जास्त दाब असेल, तर तयार आकार बदलण्याची शक्यता अधिक असते, हे आपण यापूर्वीच्या लेखात पाहिले आहे. गन ड्रिलला घर्षण पॅड असतात. (चित्र क्र. 3) त्यांची जागा आणि टूलची भूमिती यांचा योग्य मेळ घालून या पॅडवर कमीतकमी दाब येईल असे डिझाईन करावे लागते आणि योग्य त्या शीतकाचा वापर करून या पॅडला कायम वंगण मिळेल याची दक्षता घ्यावी लागते. पॅड, गन ड्रिलचा आकार ठरविणारा भाग आणि चिप कॅव्हिटी या सर्व भागावर उच्च दर्जाचे पॉलिश केल्याने यावर कुठेही ॲल्युमिनिअम चिकटत नाही. तयार झालेल्या भोकाचा आकार आणि त्याचे पृष्ठीय फिनिश चांगले मिळते. चिपचे वहन लवकर होण्यासाठी ड्रिलमधून वाहणाऱ्या शीतकाचा दाब जास्त असणे योग्य ठरते.
चित्र क्र 3 मध्ये असे वापरले गेलेले BTA ड्रिल हेड दाखविले आहेत. या कामासाठी एस.पी.एम. वापरात आहे. कार्यवस्तूची लांबी 500 मिमी. आहे. त्यावर Ø 30 मिमी. आणि Ø 34 मिमी.ची भोके करण्यासाठी 3000 आर.पी.एम. आणि 0.75 मिमी./मिनिट इतका सरकवेग वापरला जातो.
कार्बाईड टिप BTA च्या तुलनेत पॉलीकार्बोनेट डिपॉझिशन केलेले म्हणजेच पी.सी.डी. टिप BTA मध्ये टूलचे आयुष्य 12 पट जास्त मिळते. तसेच सर्व कार्यवस्तूवर सातत्याने उत्तम पृष्ठीय फिनिश मिळत राहतो.
विमानाचे काही भाग ॲल्युमिनिअमच्या एकत्र केलेल्या शीटमधून बनविले जातात. त्यांना जोडताना अनेक रिवेट मारण्यासाठी छिद्रे आणि काउंटरसिंक मारावी लागतात. याठिकाणी छिद्रांची अचूकता आणि काउंटरसिंकला कुठेही बर तयार होऊ न देणे हे दोन महत्त्वाचे निकष असतात. या कामासाठी वापरले जाणारे ॲल्युमिनिअमचे गुणधर्मही वेगळे असतात. बऱ्याचवेळी ॲल्युमिनिअम आणि CRPF चे शीट एकत्र असतात. या कामासाठी शक्यतो शीतक न वापरता काम करणे गरजेचे असते, कारण यंत्रणानंतर मोठ्या प्रमाणात तयार झालेल्या कार्यवस्तू स्वच्छ करणे अत्यंत त्रासदायक आणि वेळखाऊ काम बनते. चित्र क्र. 4 मध्ये दाखविलेल्या विशिष्ट भूमितीचे ड्रिल या कामासाठी वापरले जाते.
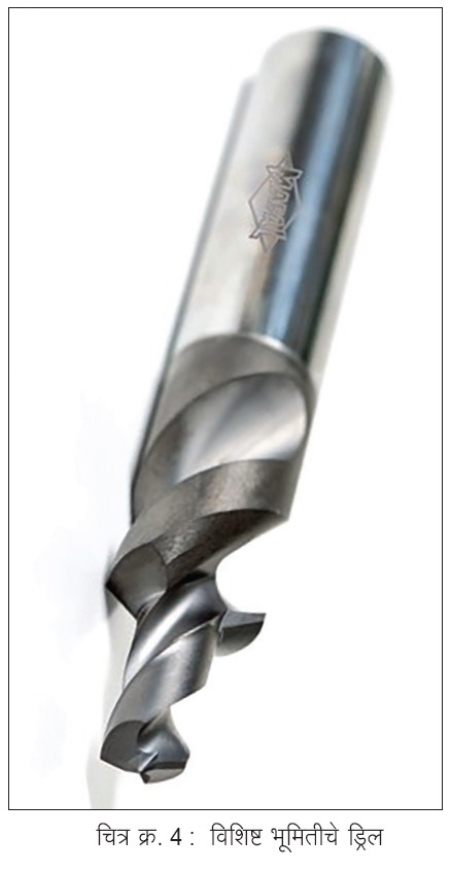
पूर्णतः उत्तम पॉलिश केलेले फ्ल्यूट, बाहेरील कडा (एज), जास्त रेक कोन आणि चिप वहनास योग्य अशी जागा हे या ड्रिलचे वैशिष्ट्य आहे. ड्रिल पॉर्ईंटमध्ये केलेल्या रचनेमुळे सेंटर ड्रिल न वापरता हे ड्रिल काम करते. अधिक उत्तम पॉलिश करून ड्रिल व्यास काटेकोरपणे बनविलेला असतो. त्यामुळे छिद्राचे आकारमान दीर्घकाळ अचूक मिळते. त्यामुळे रीमरचा वेगळा वापर करण्याची गरज टळून वेळेचीही बचत होते. पर्यायाने उत्पादकता वाढते. उच्च कार्यक्षमतेसाठी ही ड्रिल बरेचदा डायमंडचे लेपन केलेली असतात. अशा ड्रिलचे आयुष्य लेपन केलेल्या ड्रिलपेक्षा 20 पटीने जास्त असते. याचा उपयोग अनेक रिवेट छिद्रे एकाच ड्रिलने करण्यासाठी होतो आणि सर्व छिद्रांवर भौमितिक अचूकता सारखीच राहते. या रिवेटचा आकार Ø 5 ते Ø 10 मिमी.पर्यंत असतो. या ड्रिलसाठी 5,000 ते 10,000 वेग वापरावा लागतो. त्यासाठी अनुरूप मशिन असावी लागतात.
अनेकदा भोकाच्या आकाराच्या नियंत्रणामुळे ड्रिलिंगनंतर रीमर वापरून भोकाचा अचूक आकार मिळवावा लागतो. ॲल्युमिनिअममध्ये रीमर वापरताना त्याच्या कडांना ड्रिलसारखेच पॉलिश करणे इष्ट आहे. वाढीव उत्पादकतेसाठी पी.सी.डी. रीमर वापरणे जास्त किफायतशीर आहे. ॲल्युमिनिअमसाठी रीमरचा पुढील कोन नेहमीपेक्षा कमी (150 ते 200) ठेवणे आवश्यक आहे. त्यामुळे रीमर कार्यवस्तूमध्ये घुसण्याची भीती कमी होते. ऑटोमोबाईल क्षेत्रामध्ये अचूक व्हॉल्व्ह गाईड बोअर मिळविण्यासाठी काटेकोरपणे काम करावे लागते. त्यात ॲल्युमिनिअमची कार्यवस्तू बनत असल्यामुळे कामाचा किचकटपणाही वाढला आहे. पी.सी.डी. रीमर हा त्यावरील उत्तम उपाय आहे.
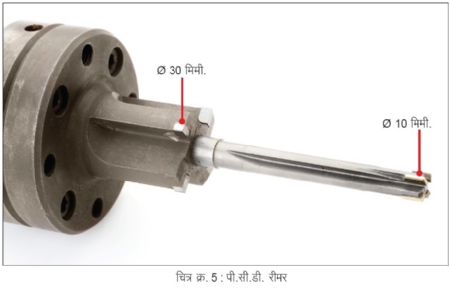
चित्र क्र. 5 मध्ये दाखविलेल्या स्टेप रीमरवर Ø 10 मिमी. व्यास असलेल्या पुढील जागी कार्बाईडवर तर Ø 30 मिमी. स्टेप असलेल्या मागील बाजूवर स्टील बॉडीवरती पी.सी.डी. टिप बसविले आहेत. (त्यामुळे रीमरच्या किंमतीवर नियंत्रण राहते.) या रीमरच्या पुढील भागास योग्य कोन दिलेला असून, कडा आणि रिलीफ कोन पॉलिश केले आहेत. या कामासाठी 350 मी./मिनिट वेग आणि 0.3 मिमी./फेरा सरकवेग वापरला आहे. यामुळे रीमर न बदलता अनेक पाळ्या विनासायास काम होत आहे. हा रीमर पुण्यातील ’हाय कट टूल्स’ कंपनीने बनविला
आहे.
अशाप्रकारे सुयोग्य ड्रिल, त्यास पूरक असा वेग देणारी मशिन आणि योग्य दर्जाचे शीतक वापरून ॲल्युमिनिअमवर सुलभपणे ड्रिलिंग करता येते.
9822881939
दत्ता घोलबा गेली 45 वर्षे कटिंग टूल या विषयाशी निगडित कार्य करीत असून, ते विविध कंपन्यांना स्वतः डिझाईन करून आवश्यक टूलिंग पुरवितात.