डी.एम.जी. मोरी कंपनीने नुकतीच भारतीय बाजारपेठेत ॲडिटिव्ह मॅन्युफॅक्चरिंगमधील दोन उत्पादने सादर केली आहेत. इतर देशांमध्ये ही उत्पादने 1990 पासून कार्यरत आहेत. ॲडिटिव्ह आणि सबट्रॅक्टिव्ह ही दोन्ही तंत्रज्ञान (टेक्नॉलॉजी) (चित्र क्र. 1) एकाच मशिनमध्ये आणणारी डी.एम.जी. मोरी ही पहिली कंपनी आहे. प्रिंटिंग केल्यानंतर वस्तुचा फिनिश कास्टिंग केलेल्या वस्तुसारखा असतो. त्यामुळे त्याला यंत्रणाची आवश्यकता असते. डी.एम.जी. मोरीच्या मशिनवर त्याच सेटअपमध्ये यंत्रणही करता येते.
एकाच सेटअपमध्ये प्रिंटिंग आणि यंत्रण
या लेखात आपण ॲडिटिव्ह उत्पादन तंत्राविषयी जाणून घेणार आहोत. त्यामध्ये प्रामुख्याने दोन तंत्रज्ञान येतात.
1. सिलेक्टिव्ह लेझर मेल्टिंग (SLM) ज्याला पावडर बेड तंत्रज्ञान असे म्हटले जाते.
2. लेझर डिपॉझिशन वेल्डिंग, ज्याला पावडर नॉझल तंत्रज्ञान असे म्हटले जाते.
या दोन प्रक्रियांचे अधिक तपशील आपण जाणून घेऊ.
सिलेक्टिव्ह लेझर मेल्टिंग (SLM) किंवा पावडर बेड तंत्र
सिलेक्टिव्ह लेझर मेल्टिंग पद्धतीत एक बंदिस्त प्रक्रिया (क्लोज्ड् प्रोसेस) चेंबर (चित्र क्र. 2) असतो, ज्यामध्ये ऑरगॉन वायू (गॅस) भरलेला असतो. या दाबयुक्त चेंबरमध्ये 3D प्रिंटिंग केले जाते. जेव्हा लेझरने कुठलेही मटेरियल वितळविले (फ्यूज) जाते, तेव्हा उष्णतेमुळे आणि हवेतील ऑक्सिजनमुळे ऑक्सिडेशन होण्याची शक्यता अधिक असते. हे टाळण्यासाठी ऑरगॉन आणि नायट्रोजन या दोन प्रकारचे वायू वापरले जातात, परंतु नायट्रोजन सगळ्याच प्रकारच्या धातूवर चालतोच असे नाही. उदाहरणार्थ, ॲल्युमिनिअम, टायटॅनिअम किंवा तांबे यांसारख्या शीघ्र प्रतिसाद (हाय रिॲक्टिव्ह) देणाऱ्या धातूंवर नायट्रोजन पुरेसा प्रभावी ठरत नाही. त्यामुळे अशा धातुंसाठी ऑरगॉन वायू वापरला जातो आणि हा वायू सर्व धातूंवर चांगल्या पद्धतीने आच्छादन (शिल्डिंग) देत असल्यामुळे ऑक्सिडेशन वाचते.
वस्तू निर्मिती वेग (बिल्ड रेट)
या प्रक्रियेमध्ये वस्तू निर्मिती वेग 84 ग्रॅम/तास असून हा सरासरी दर आहे. शीघ्र प्रतिसाद देणाऱ्या टायटॅनिअमचा वितळण बिंदू (मेल्टिंग पॉइंट) उच्च असल्यामुळे त्यांना फ्युजनलाही वेळ लागतो. स्टीलच्या कार्यवस्तुंचा वेग 10 सेमी3/तास मिळतो, कारण स्टीलचा वितळण बिंदू तुलनेने कमी आहे. स्टीलमध्ये आपल्याला 110 -120 ग्रॅम/तास हा वेग मिळू शकतो.
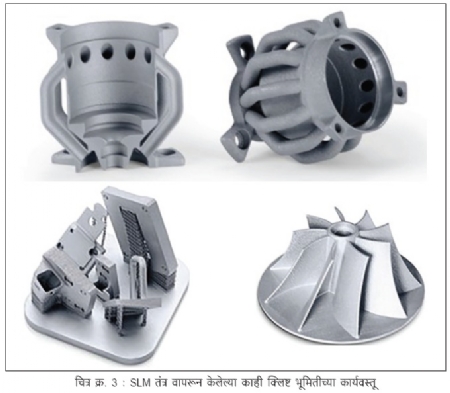
खूप क्लिष्ट भूमिती, अनवट (इंट्रिकेट) आकार असलेल्या छोट्या वस्तू (चित्र क्र. 3) बनवायच्या असतील, तर पावडर बेड तंत्रज्ञान वापरले जाते. या पावडर बेड तंत्रज्ञानात वस्तुसाठी एक टेबल असते. त्याबरोबरच रिकोटर नावाची एक यंत्रणा असून, ज्या धातूमध्ये आपल्याला प्रिंटिंग करायचे आहे त्या धातुची पावडर असलेले एक कार्ट्रिज असते. प्रत्येक वेळी रिकोटर, 20 मायक्रॉन ते 100 मायक्रॉन या मर्यादेमध्ये जी ठरविलेली थराची जाडी असेल, त्या प्रमाणात पावडर घेतो आणि तेवढ्या जाडीचा थर देतो. पावडरच्या थरावर लेझर बीम येऊन सॉलिड मॉडेलप्रमाणे जी भूमिती ठरविलेली असेल, तेवढ्याच भागात जाऊन ती पावडर वितळवितो. (म्हणूनच याला सिलेक्टिव्ह लेझर मेल्टिंग असे म्हणतात). बाकी ठिकाणी पावडर तशीच राहते. अशा पद्धतीने पहिला थर तयार झाल्यावर पुन्हा पावडरचा थर देऊन त्या थरात ठरविलेल्या जागेवरील पावडर वितळवून दुसरा थर तयार होतो. अशा पद्धतीने क्रमाक्रमाने वस्तू तयार होत जाते. थराची जाडी धातुच्या गुणधर्मावर अवलंबून असते.
समजा आपण 10 मिमी. उंचीपर्यंतची वस्तू तयार केली. त्यानंतर पुढचा थर 20 मायक्रॉनचा द्यायचा आहे. अशावेळी पावडरच्या थराची उंची आणि वस्तुची उंची सारखीच असते. पुढचा थर देण्याआधी टेबल हवे तेवढे खाली सरकविले जाते. वस्तू तयार झाल्यावर ती पावडरमध्ये पूर्णपणे बुडालेली असते. काम पूर्ण झाल्यावर टेबल परत वर उचलले जाते आणि टेबलवरील अतिरिक्त पावडर शोषून घेतली जाते.
या पद्धतीच्या मशिन (चित्र क्र. 4) पुढील 2 आकारातील कार्यवस्तू बनविण्यासाठी उपलब्ध आहेत.
300 X 300 X 300 (सर्व आकडे मिमी.)
125 X 125 X 200 (सर्व आकडे मिमी.)
या भौमितिक आकारात बसणाऱ्या कुठल्याही आकाराच्या, कितीही वस्तू एकाचवेळी बनविता येतात. कार्यवस्तू कितीही वेगवेगळ्या असल्या तरी ठरलेल्या वस्तू निर्मितीच्या वेगानेच धातू वितळवून 3D प्रिंटिंग करता येते.
वापरण्यात येणारा धातू
हा धातू साधारणपणे 123 मायक्रॉन आणि 63 मायक्रॉन अशा दोन प्रकारच्या आकाराचे कण असलेल्या पावडर स्वरूपात मिळतो. यापेक्षा बारीक आकाराची पावडर बाजारात मिळू शकते, परंतु ती खूप महाग असते. पावडर तयार करणारे आपल्याला ज्या मिश्रणाची पावडर पाहिजे त्यानुसार तयार करून देत असतात. ही पावडर पूर्णपणे शुद्ध स्वरूपात येते.
याचा वापर मुख्यत्वे कमी संख्येत बनणाऱ्या वस्तुंसाठी फार प्रभावीपणे करता येतो. उदाहरणार्थ, स्पेस शटलचा एखादा भाग आपल्याला ताबडतोब बनवायचा असेल आणि त्यासाठी पारंपरिक प्रक्रिया वापरायची असेल, तर त्याचे डाय आणि पॅटर्न बनवा, मोल्डिंग करा, कास्टिंग काढा, यंत्रण करा. या सगळ्या प्रक्रियेला एक ते दीड महिन्याचा कालावधी सहज लागतो. असे केवळ 5-6 भागच बनवायचे असतील तर ते फार महागही असते. जेव्हा हा भाग 1 ते 2 दिवसांतच उपलब्ध होणे गरजेचे असते तेव्हा ही प्रक्रिया (जिला रॅपिड प्रोटोटायपिंग असेही म्हणतात) उपयोगाला येते. धातुच्या मिश्रणाचे तपशील देऊन पावडर बनविता येते. कार्यवस्तूचे ड्रॉईंग मशिनच्या सॉफ्टवेअरमध्ये फीड करून मशिन योग्य पॅरामीटरला सेट करून लगेच उत्पादन करता येते.
आता आपण दुसऱ्या तंत्राबद्दल जाणून घेऊ.
लेझर डिपॉझिशन वेल्डिंग
लेझर डिपॉझिशन वेल्डिंगला पावडर नॉझल तंत्र असेही म्हटले जाते. यामध्ये वेल्डर जसा वेल्डिंगचा रॉड धातुच्या पृष्ठभागावर वितळवून थर देत जातो, त्याच पद्धतीने इथे पृष्ठभागावर धातुची पावडर फवारली जाते. ही उघड्यावर होणारी प्रक्रिया आहे.
चित्र क्र. 5 मध्ये लेझर डिपॉझिशन वेल्डिंगचे संकल्पना चित्र दाखविले आहे. चित्रात दिसणारा लाल रंगाचा भाग म्हणजे लेझर बीम आहे. त्याच्या बाजूला दिसणाऱ्या काळ्या रंगाच्या तुटक रेषा म्हणजे धातुची पावडर आहे आणि निळ्या रंगाच्या रेषा आच्छादन करणारा वायू दर्शवितात. जास्त वॅटेजचे लेझर वापरून, पावडर वितळवून त्याचा 4-5 मिमी. व्यासाचा द्रवरूप धातुचा ठिपका (मेल्ट पूल) केला जातो. त्यावेळी ऑक्सिडेशन थांबविण्यासाठी त्यावर उदासीन वायूचे (इनर्ट गॅस) आच्छादन तयार केले जाते. कुठल्याही जागेवर दुरुस्ती करणे, नमुना उत्पादन (प्रोटोटाइप), लेप देणे (कोटिंग) यासाठी ही प्रक्रिया वापरली जाते.
चित्र क्र. 6 मध्ये दुरुस्ती होणारा भाग हा इंजिन टायरॉड केसिंगचा भाग आहे. याची इनलेट फ्लँज खराब झाल्यामुळे संपूर्ण एअरक्राफ्ट इंजिन हाउसिंग फेकून देण्यापेक्षा, मूळ धातुची पावडर वापरून तुटलेली फ्लँज जागेवरच परत दुरुस्त करून म्हणजे 3D प्रिंटिंग करून तिथेच त्याला यंत्रण करता येते.
वस्तू निर्मिती वेग (बिल्ड रेट)
लेझर डिपॉझिशन वेल्डिंग या प्रक्रियेचा वस्तू निर्मिती वेग सिलेक्टिव्ह लेझर मेल्टिंगपेक्षा 10 पटीने जलद आहे. स्टीलसाठी 750 ग्रॅम/तास किंवा 90 सेमी3/तास या वेगाने निर्मिती करता येते. या पद्धतीमध्ये 0.8 ते 1.5 मिमी. पर्यंत जाडीचा थर देता येतो. त्यामुळे या प्रक्रियेत जास्त वेगाने वस्तू बनविता येतात.
वेल्डिंग गुणवत्ता
वेल्डिंगमध्ये येऊ शकणारे पोरॉसिटी, ब्लोहोल, अंडरकट असे दोष टाळण्यासाठी मशिनमध्ये ॲडॅप्टिव्ह प्रोसेस कंट्रोल सिस्टिम वापरलेली आहे, जी वेल्ड संपूर्ण एकजीव झाल्याचा फीडबॅक मिळेपर्यंत अक्षाला पुढची हालचाल करण्याचा आदेश देत नाही. हा फीडबॅक ऑनलाईन कॅमेऱ्यामार्फत तापमानाची प्रतिमा बघून दिला जातो. या मशिनसाठी एअरक्राफ्ट आणि स्पेस रिसर्च प्रयोग शाळा हे मुख्य दोन ग्राहक आहेत. कारण इथे सर्वोच्च गुणवत्ता आणि कमी संख्या या दोन बाबी प्रभावी असतात.
मशिनचा आकार
DMU 65 मोनोब्लॉक मशिनमध्ये (चित्र क्र. 7) 500 मिमी. व्यासाच्या परीघात आणि 400 मिमी. उंचीमध्ये बसणाऱ्या कुठल्याही आकाराच्या, कितीही कार्यवस्तू एकाचवेळी बनविता येतात. डङच तंत्रामध्ये जास्त क्लिष्ट वस्तू तयार करता येतात, कारण तिथे थराची जाडी 20 मायक्रॉनपासून सुरू होते. परंतु, इथे कमीतकमी 0.8 मिमी. जाडीचा थर मिळत असल्यामुळे क्लिष्ट भूमिती असलेल्या वस्तू बनविता येत नाहीत. (चित्र क्र. 8 ) या प्रक्रियेने तयार झालेल्या वस्तूचे फिनिशिंग करण्यासाठी त्याच मशिनच्या स्पिंडलवरील लेझर हेड काढून बाजूला ठेवता येते आणि यंत्रण करावयाच्या स्पिंडलमध्ये कटिंग टूल वापरून यंत्रणसुद्धा त्याच जागेवर करता येते. मोठ्या आकाराच्या वस्तुंसाठी मशिनचे हे वैशिष्ट्य अधिक उपयुक्त ठरते.
वापरण्यात येणारा धातू
SLM प्रक्रियेमध्ये वापरल्या जाणाऱ्या पावडरमधील कणांच्या आकाराच्या तुलनेत या प्रक्रियेमध्ये मोठ्या म्हणजे 150 ते 200 मायक्रॉनपर्यंतच्या कणांच्या आकाराची पावडर वापरता येते.
DMG च्या ॲडिटिव्ह उत्पादनासाठीच्या मशिन, यंत्रणाच्या इतर प्रक्रियांबरोबर संयोग (कॉम्बिनेशन) करून वापरता येतात. काही कार्यवस्तुंसाठी मिलिंग करावे लागते, तर काहीना टर्निंग करावे लागते. त्यासाठी मिलिंगसह अथवा टर्निंगसह प्रक्रिया करण्याची सुविधा असलेल्या कॉम्बिनेशन मशिन (चित्र क्र. 9) उपलब्ध आहेत. या कॉम्बिनेशन मशिनमध्ये मिलिंगचे/टर्निंगचे नियंत्रक (कंट्रोल) वेगळे आहेत आणि मेल्टिंगचे नियंत्रक वेगळे आहेत. याला ॲडॅप्टिव्ह प्रोसेस नियंत्रक (चित्र क्र. 10) असे म्हटले जाते. मेल्टिंगचा वेगळा नियंत्रक असून, तो केवळ मेटलर्जी हाताळतो. प्रिंटिंगची मेटलर्जी आणि त्याच्याशी संबंधित सर्व पॅरामीटरची हाताळणी आणि त्याचे नियंत्रण करतो.
दुसरा नियंत्रक मुख्य मशिनच्या पॅरामीटरची काळजी घेतो. दोन्ही नियंत्रक एकमेकांशी जोडलेले आहेत, कारण प्रिंटिंग करतानाही मशिनचे अक्ष हलतात आणि ते अक्ष हलण्यासाठी मशिन नियंत्रक साहाय्य करतो. मेल्टिंगशी संबंधित जेवढ्या प्रक्रिया आहेत त्या सर्व ॲडॅप्टिव्ह प्रोसेस नियंत्रक हाताळतो.
प्रक्रिया साखळ्या (प्रोसेस चेन)
चित्र क्र. 11 मध्ये चार वेगवेगळ्या पद्धतीच्या प्रक्रिया साखळ्या दाखविलेल्या आहेत. प्रक्रिया साखळी म्हणजे कुठलीही प्रक्रिया सुरू केल्यानंतर त्यामध्ये घडणाऱ्या आणि एकमेकांवर अवलंबून असणाऱ्या गोष्टींची मालिका होय.
पहिली प्रक्रिया म्हणजे कॉम्प्युटर मॉडेलिंग. यामध्ये कार्यवस्तूचे ऑटोकॅड ड्रॉईंग बनविणे, त्याचे मॉडेल बनविणे, IGES/step फाईल बनविणे अशी कामे होतात.
दुसऱ्या प्रक्रियेमध्ये ही फाईल संबंधित मशिनला दिली जाते. प्रत्येक मशिनचा इनपुट विशिष्ट फॉरमॅटमध्ये दिला तरच ते मशिन त्यावर काम करू शकते.
तिसरी प्रक्रिया म्हणजे मशिनवर 3D प्रिंटिंग करणे. संगणकात बनविलेल्या मॉडेलप्रमाणे धातू वितळवून कार्यवस्तू बनविली जाते.
चौथ्या प्रक्रियेमध्ये तयार कार्यवस्तूचे आवश्यक तिथे यंत्रण करून अंतिम स्वरूपातील वस्तू तयार होते. क्लिष्ट भूमिती असलेल्या वस्तूंचे यंत्रण करण्यासाठी 5 अक्षीय मशिन वापरले जाते.
काही वेळा आधी यंत्रण करून नंतर प्रिंटिंग केले जाते. यामध्ये कच्च्या स्वरूपातील कार्यवस्तू मशिनिंग सेंटरमध्ये पूर्ण तयार केली जाते. नंतर ज्या पृष्ठभागावर यंत्रण केलेले असते, त्या पृष्ठभागावर धातू वितळवून अंतिम स्वरूपातील भाग बनविला जातो. याचे उत्तम उदाहरण म्हणजे गुडघ्याचा कृत्रिम सांधा (नी जॉईंट). या सांध्याच्या खालच्या भागातील पट्टीचे आधी यंत्रण केले जाते आणि त्यावर वरची बिजागरी (हिंज) नंतर प्रिंट केली जाते.
चित्र क्र. 12 मध्ये दाखविलेली प्लेट वेगळ्या धातुची आहे. प्रत्यक्ष संपर्कात येणारी प्लेट टायटॅनिअमची आहे. येथे दोन वेगळे धातू आहेत. एकाच पावडरमध्ये दोन वेगळे धातू टाकता येत नाहीत, म्हणून SLM तंत्रात आधी एक भाग प्रिंट करावा लागतो, त्याचे यंत्रण करावे लागते आणि त्यानंतर दुसरा भाग त्यावर प्रिंट करता येतो. त्यामध्ये आधी प्रिंटिंग केलेला भाग वितळवला जातो. त्याची जाडी जास्तीतजास्त 0.1 मिमी. किंवा 0.2 मिमी. एवढीच असते. जेव्हा एकाच मॉडेलमध्ये दोन प्रकारचे धातू असतात तेव्हा सॉफ्टवेअरमध्ये तशी माहिती देऊन बेस धातूचे पॅरामीटर आणि त्यावर बसणाऱ्या धातूचे फ्युजिंग पॅरामीटर, त्यांची जाडी काय आहे याचे व्यवस्थापन सॉफ्टवेअरकडून केले जाते. त्या प्रमाणात लेझर बीमची तीव्रता (इंटेन्सिटी) ठरविली जाते.
पावडर व्यवस्थापन प्रणाली
पावडर व्यवस्थापन प्रणाली, मशिनमध्ये वापरल्या जाणाऱ्या CELOS प्रणालीचाच भाग आहे. धातुची पावडर दाबयुक्त ऑरगॉनने पंप केली जाते आणि नॉझलमधून मशिन बेडवर आणली जाते.
समजा सुरुवातीला टायटॅनिअमची कार्यवस्तू प्रिंट झाली आणि पुढची कार्यवस्तू जर ॲल्युमिनिअमची असेल, तर पूर्ण मशिन स्वच्छ करून पहिल्या पावडरचा कण अन् कण काढावा लागतो. या संपूर्ण प्रक्रियेला एक ते दीड दिवस लागतो. पण रीप्लग पेटंटेड तंत्रज्ञानामुळे (चित्र क्र. 13) हेच काम दोन तासांच्या आत होते. यामध्ये प्रत्येक धातुच्या पावडरचा वेगवेगळा कार्ट्रिज ठेवावा लागतो. साधारणपणे 98% पावडर परत मिळविता येते.
फ्युजन होणाऱ्या क्षेत्राजवळ असलेल्या पावडरच्या कणांचा आकार आणि त्याचे गुणधर्म बदलतात. समजा आपण 120 मायक्रॉन आकाराची पावडर वापरली असेल, तर त्या क्षेत्रातील पावडरचा आकार 150 मायक्रॉन होऊ शकतो. ती पावडर जेव्हा रीसायकल पावडर टोनर प्लांटमध्ये येते, तेव्हा तिथे अल्ट्रासॉनिक सीव्हिंग व्यवस्था आहे. त्या चाळणी प्रक्रियेतून फक्त 120 मायक्रॉनची पावडर परत कार्ट्रिजमध्ये पाठविली जाते. उरलेली पावडर वेगळी गोळा करून त्या पावडरसाठी वेगळे प्रोसेस पॅरामीटर ठरविले जातात, कारण त्या पावडरवर उष्णतेचा परिणाम होऊन तिचे गुणधर्म बदललेले असतात. त्याचा अंतिम कार्यवस्तुच्या गुणवत्तेवर परिणाम होऊ नये यासाठी ‘इनटेक डीएमएलएस’ कंपनीने डी.एम.जी. मोरी कंपनीसाठी OPTOMET सॉफ्टवेअर विकसित केले आहे. ते वापरल्यामुळे शुद्ध पावडरच्या पहिल्या वापरापासून नंतर ती पावडर 10 वेळा वापरली गेली, तर प्रत्येक वेळेस पावडरच्या बदललेल्या गुणधर्मानुसार प्रोसेस पॅरामीटर बदलले जातात. यामुळे मूळ पावडरचा वापर केलेल्या आणि दहाव्यांदा वापरलेल्या पावडरपासून बनलेल्या कार्यवस्तुची गुणवत्ता समान मिळते.
8956930556
rajendra.desai@dmgmori.com
राजेंद्र देसाई ‘डीएमजी मोरी इंडिया प्रा. लि.’ कंपनीमध्ये उत्पाद विक्री व्यवस्थापक आहेत. त्यांना या क्षेत्रातील कामाचा 31 वर्षांचा अनुभव आहे