धातूचे यंत्रण एक क्लिष्ट प्रक्रिया असून, त्यातील टर्निंग प्रक्रियेमध्ये केवळ एकच कर्तन कड वापरली जात असल्यामुळे ही प्रक्रिया मिलिंग आणि ड्रिलिंग प्रक्रियांपेक्षा समजण्यास सोपी आहे. मात्र, असे असले तरी टर्निंग प्रक्रियाही बऱ्याच घटकांवर अवलंबून असते. यामध्ये योग्य टूलची निवड करणे हा महत्त्वाचा भाग असून टूलची निवड करताना पुढील घटक महत्त्वाची भूमिका बजावतात.
1. कार्यवस्तूचे मटेरियल : त्याचे स्वरूप म्हणजे ते फोर्ज्ड आहे का, त्याचा आकार दंडगोलाकार आहे का, किती मटेरियल (बार स्टॉक) काढावयाचे आहे, त्याचे काठिण्य (हार्डनेस), ती सलग आहे का तुटक तुटक आहे, तसेच सममित (सिमेट्रिक) आहे की असममित आहे.
2. मशिनचा प्रकार, टूल होल्डरच्या शँकचा आकार, शीतकाचा प्रवाह आणि दाब, कार्यवस्तू पकडण्याचा प्रकार, हायड्रॉलिक आहे की यांत्रिकी इत्यादी.
साधारणपणे टर्निंग प्रक्रियेत टर्निंग सेंटर आणि यांत्रिकी अडथळ्यांच्या (इंटरप्शन)स्वरूपातील सममित भाग यांचा 65% समावेश असल्यामुळे या लेखात या सेटअपमधील टर्निंग प्रक्रियेसाठी योग्य टूलची निवड कशी करावी याबद्दल समजावून घेणार आहोत.
साधारणतः इंडेक्सेबल हत्यारधारकाचा (टूल होल्डर) वापर करताना मशिनवरून त्याच्या शँकचा आकार ठरविला जातो. टर्निंग प्रक्रियेची पद्धत आणि कार्यवस्तूचे स्वरूप यावर इन्सर्टची भूमिती आणि इन्सर्टचा आकार अवलंबून असतो, तर कार्यवस्तुच्या मटेरियलवरून इन्सर्टची ग्रेड ठरविली जाते.
1. आय.एस.ओ.च्या नियमन पद्धतीनुसार मटेरियलच्या सहा प्रमुख प्रकारांसाठी सहा वेगवेगळी अक्षरे निश्चित करण्यात आलेली आहेत.
स्टीलसाठी P : हा यंत्रण केल्या जाणाऱ्या मटेरियलमध्ये सर्वात जास्त वापरला जाणारा प्रकार आहे. यामध्ये मिश्रण नसलेल्या धातुपासून ते अतिउच्च दर्जाच्या मिश्रधातुंचा, तसेच कास्ट स्टीलच्या वस्तुंचा समावेश होतो. या सर्वांना ‘लाँग चिपिंग’ मटेरियल म्हणता येईल.
स्टेनलेस स्टीलसाठी M : या मिश्रधातूंमध्ये कमीतकमी 12% क्रोमिअम असते, तसेच निकेल आणि मॉलिब्डेनम मिसळलेले असतात. या मटेरियलमधील फेरिटिक, मार्टेनसिटिक, ऑस्टेनिटिक आणि ऑस्टेनिटिक - फेरिटिक (ड्युप्लेक्स) या सर्वांचा मिळून यंत्रणात मोठा वाटा आहे. या सर्वांमधील एक समान गुणधर्म म्हणजे, यंत्रण होताना ते मोठ्या प्रमाणावर उष्णता निर्माण करतात. टूलच्या नॉचची झीज होते आणि बिल्ट अप कड तयार होते.
ओतीव लोखंडासाठी K : स्टीलच्या अगदी विरुद्ध म्हणजे हे कमी लांबीच्या चिप निघणारे मटेरियल आहे. GCI आणि मॅलिएबल या लोखंडाचे यंत्रण सोपे असते. मात्र, NCI आणि CGI/ADI यांचे यंत्रण अवघड असते. सर्व कास्ट आयर्नमध्ये SiC असते, जे कर्तन कडेसाठी ॲब्रेझिव्ह ठरते.
नॉन फेरस धातुंसाठी N : हे अतिशय मऊ प्रकारचे धातू आहेत. जसे की, ॲल्युमिनिअम, तांबे, पितळ इत्यादी. 13% सिलिकॉन (Si) घटक असणारे ॲल्युमिनिअम हे फार ॲब्रेझिव्ह असते. यामध्ये यंत्रण वेग आणि टूलचे आयुष्य अधिक असण्याची अपेक्षा करता येते. CMC गटात ॲल्युमिनिअमचा प्रभाव अधिक असतो.
उष्णतारोधक (हीट रेझिस्टंट) सुपर अलॉईज (HRSA) साठी S : यामध्ये लोखंड, निकेल, कोबाल्ट आणि टायटॅनिअम हे मिश्रधातू असणाऱ्या मटेरियलचा समावेश होतो. ते चिवट असतात, तसेच यंत्रणामुळे कठीण होतात आणि उष्णता निर्माण करतात. ते M प्रकारच्या धातुंसारखेच असतात, मात्र यंत्रणास अधिक अवघड असतात.
कठीण (हार्डन्ड) स्टीलसाठी H : कठीण केलेल्या, टेम्परिंग केलेल्या आणि अतिशय कठीण स्टीलचा यामध्ये समावेश होतो, ज्यांचे काठीण्य 45-65 HRC इतके असते आणि जवळपास 400 HB कठीणपणा असलेले चिल्ड कास्ट आयर्न असते. त्यामुळे त्यांचे यंत्रण करणे अवघड असते. या मटेरिअलचे यंत्रण होताना अधिक प्रमाणात उष्णता निर्माण होते तसेच ते खूप ॲब्रेझिव्ह असतात.
या प्रत्येक मटेरिअल प्रकाराच्या यंत्रणाच्या वेगवेगळ्या गरजांमुळे टूलच्या वेगवेगळ्या श्रेणी आणि वेगवेगळ्या भूमिती विकसित करण्यात आलेल्या आहेत. तसेच प्रत्येक मटेरियलच्या प्रकारासाठी अनुरूप असे बदल त्यात केले आहेत.
2. टूलचे मटेरियल आणि यंत्रणाच्या भूमितीवरून इंडेक्सेबल इन्सर्ट बनविले जातात. कटिंग टूल मटेरियलचे प्रमुख प्रकार पुढीलप्रमाणे आहेत.
लेपन नसलेले सिमेंटेड कार्बाइड (HW)
लेपन असलेले सिमेंटेड कार्बाइड (HC)
सेरमेट (HT, HC)
सिरॅमिक (CA, CN, CC)
क्यूबिक बोरॉन नायट्राइड (BN)
पॉलिक्रिस्टलाइन डायमंड (DP, HC)
2.1. लेपन नसलेले सिमेंटेड कार्बाइड (HW)
स्टील, HRCA, टायटॅनिअम, कास्ट आयर्न आणि ॲल्युमिनिअम यांच्या टर्निंग, मिलिंग आणि ड्रिलिंगच्या मध्यम ते अवघड यंत्रणासाठी वापरले जातात.
ॲब्रेझिव्हमुळे होणाऱ्या झिजेला प्रतिरोध तसेच चिवटपणा (टफनेस) यांचे उत्तम मिश्रण.
धारदार कर्तन कडा मिळतात.
कडा सुरक्षित राहतात, मात्र अधिक वेगाने यंत्रण करताना झीज प्रतिरोध मर्यादित असतो.
अधिक उत्पादकता आणि त्यासाठी लागणारा जास्तीचा यंत्रण वेग तसेच सरकवेगाला आज महत्त्व आल्यामुळे या इन्सर्टचा कमी प्रमाणात वापर केला जातो.
2.2. लेपन असलेले सिमेंटेड कार्बाइड (HC)
सामान्यतः सर्व प्रकारच्या कार्यवस्तू आणि मटेरियलच्या यंत्रणासाठी यांचा वापर केला जातो.
झीज प्रतिरोध आणि चिवटपणा यांचे उत्तम मिश्रण असल्यामुळे बऱ्याच यंत्रभागांसाठी वापर.
याच्या बऱ्याच श्रेणी असून कठीण किंवा चिवट असलेल्या मूळ मटेरियलवर ‘ग्रेडीयंट सिंटरिंग’ करून वापरले जाते. त्यावर CVD आणि PVD प्रकारचे अनेक लेप दिलेले असतात.
उत्कृष्ट झीज प्रतिरोधक गुण असल्यामुळे टूलचे आयुष्य वाढण्यास मदत होते.
सर्व टूल उत्पादकांच्या इन्सर्टमध्ये लेपन केलेल्या कार्बाइडचा मोठा हिस्सा असतो. तसेच इन्सर्टच्या निवडीसंबंधी इन्सर्टच्या वेगवेगळ्या श्रेणी आणि भौमितिक आकार यावर आधारित तपशीलवार माहिती त्यांच्याकडून दिली जाते.
CVD म्हणजे केमिकल व्हेपर डिपॉझिशन आणि PVD म्हणजे फिजिकल व्हेपर डिपॉझिशन या दोन लेपनाच्या प्रमुख पद्धती आहेत.
CVD मधील वेगवेगळ्या लेपांचे कार्य
CVD पद्धतीने लेपन करताना नेहमी वापरली जाणारी संयुगे म्हणजे, टायटॅनिअम कार्बन नायट्राइड (TiCN), ॲल्युमिनिअम ऑक्साइड (Al2O3) आणि टायटॅनिअम नायट्राइड (TiN) होय.
यामध्ये मूळ मटेरियलवरील पहिला थर टायटॅनिअम कार्बन नायट्राइडचा (TiCN) असतो, ज्यामुळे ॲब्रेझिव्ह घर्षणामुळे होणाऱ्या झीजेपासून संरक्षण मिळते.
त्यानंतरचा थर ॲल्युमिनिअम ऑक्साइडचा असतो, ज्यामुळे उष्णतेपासून आणि रसायनांपासून होणाऱ्या झिजेला प्रतिरोध केला जातो. तसेच कायमस्वरूपी विस्थापन (प्लास्टिक डिफॉर्मेशन) आणि क्रेटर झीज होण्यापासून संरक्षण मिळते. यंत्रण प्रक्रियेत जितकी जास्त उष्णता निर्माण होणार असेल तितका ॲल्युमिनिअम ऑक्साइडचा जास्त जाड लेप द्यावा लागतो. लेपन खूप कठीण असते, त्यामुळे जास्त यांत्रिकी अडथळ्यांना (इंटरप्शन) तोंड देता येते. लेपांची जाडी खूप कमी असते याचे मुख्य कारण लेप अधिक जास्त जाड असल्यास ठिसूळ होऊन कडांचे नुकसान होऊ शकते. काही वेळा लेपनानंतर ब्लास्टिंग केले जाते.
यासाठी एक विशिष्ट ग्राइंडिंग मटेरियल वापरले जाते. यामुळे इन्सर्टचा चिवटपणा वाढतो आणि पृष्ठभाग अधिक गुळगुळीत होतो.
TiN मुळे झीज शोधणे सोपे होते आणि इन्सर्टचा पृष्ठभाग गुळगुळीत होतो.
CVD पद्धतीने लेपन (चित्र क्र. 1) केलेल्या इन्सर्टचे मूळ मटेरियल मऊ, मध्यम कठीण किंवा जास्त कठीण असते. यांचा वापर सर्व प्रकारच्या स्टील आणि कास्ट आयर्नच्या यंत्रणासाठी केला जातो. यंत्रणाचा वेग 150 मी./मिनिटपासून ते 350 मी./मिनिटापर्यंत ठेवून यंत्रण करता येते.
PVD मधील वेगवेगळ्या लेपांचे कार्य
PVD हे आवरण (चित्र क्र. 2) 500o से.पेक्षा जास्त तापमानामध्ये केले जाते. PVD मध्ये घन इलेक्ट्रोडचा वापर केला जातो.
म्हणजेच लेपनाचे कण धातूमधून येतात. (ज्या धातूचे बाष्पीभवन केलेले असते). योग्य दाब आणि तापमान यांचा PVD च्या कक्षात वापर करून कठीण धातूचे कण इन्सर्टच्या मूळ मटेरियलच्या पृष्ठभागावर जाऊन चिकटतात. PVD लेपन केलेले इन्सर्ट काळ्या रंगाचे असल्यासारखे दिसतात, म्हणजेच त्याला लेपन केलेले नसते.
PVD लेपनामुळे नॅनो जाडीचे लेप देऊन धारदार कर्तन कडा निर्माण करता येतात. इन्सर्टला तडे जाऊ नयेत यासाठी प्रतिरोध करता येतो, म्हणून अतिशय अवघड यंत्रणासाठी ही ग्रेड वापरण्यास उपयुक्त ठरते. PVD इन्सर्टचा वापर, अंतिम किंवा अंतिम टप्प्यापूर्वीच्या यंत्रणासाठी आवश्यक असलेल्या धारदार कर्तन कडांची आवश्यकता असते तेव्हा केला जातो.
2.3. सेरमेट इन्सर्ट
क्लोज टॉलरन्स आणि पृष्ठभागाचे उत्कृष्ट फिनिश मिळविण्यासाठी अंतिम टप्प्यातील किंवा त्यापूर्वीच्या टप्प्यातील यंत्रणासाठी या इन्सर्टचा वापर करण्यात येतो.
मूळ मटेरियल कठीण आणि झीज प्रतिरोधक असते, तसेच रासायनिकदृष्ट्या स्थिर असते.
यामध्ये टायटॅनियमवर आधारित (TiC, TiCN) सिमेंटेड कार्बाइडचा समावेश असतो, तर कोबाल्ट हा बाईंडर घटक असतो.
PVD लेपनामुळे टूलची झीज प्रतिरोधक शक्ती वाढून त्याचे आयुष्य वाढते. स्वयं धारदारपणा (सेल्फ शार्पनिंग) हा गुण असतो, तर चिवटपणा कमी असतो.
बाजारपेठेमध्ये उपलब्ध असलेल्या एकूण इन्सर्टच्या संख्येत सेरमेट इन्सर्टचा वाटा कमी असून, सेरमेट इन्सर्टचा वापर विशेषकरून स्टीलवर जिथे कमी टॉलरन्समध्ये यंत्रण करावयाचे असते तेव्हा शेवटच्या टप्प्यात करण्यात येणाऱ्या फिनिशिंग यंत्रणासाठी केला जातो.
2.4. सिरॅमिक इन्सर्ट
सिरॅमिकच्या ग्रेडनुसार या इन्सर्टचा वापर कास्ट आयर्न आणि स्टील, कठीण मटेरियल आणि HRSA यांच्या यंत्रणासाठी केला जातो.
सिरॅमिकच्या ग्रेड साधारणपणे झीज प्रतिरोधक असतात, तसेच उष्णता वाढल्यावरसुद्धा कठीणपणा टिकवून ठेवतात. वेगवेगळ्या प्रकारचे मटेरियल आणि यंत्रभागांसाठी यांचा वापर केला जातो.
सिरॅमिक सहसा ठिसूळ असतात आणि ते वापरताना स्थिर (स्टेबल) यंत्रण परिस्थिती लागते. मिश्र आणि व्हिस्कर रीएन्फोर्स्ड् सिरॅमिक मिसळून त्याचा चिवटपणा वाढविता येतो. एकूण इन्सर्टच्या बाजारात यांचा वाटा 20% आहे. सिरॅमिक इन्सर्टचा वापर मुख्यत्वे करून विमान उद्योगासाठी लागणारे यंत्रभाग (विशेषतः इंजिनचे भाग) आणि कठीण स्टील, कास्ट आयर्नमध्ये रोल टर्निंग तसेच, अधिक वेगाने बोअरिंग करण्यासाठी केला जातो.
2.5. क्युबिक बोरॉन नायट्राइड (CBN)
कठीण स्टीलच्या शेवटच्या टप्प्यातील यंत्रणासाठी.
ग्रे कास्ट स्टीलमध्ये जास्त वेगाने केल्या जाणाऱ्या प्राथमिक यंत्रणासाठी.
व्हाइट/चिल्ड कास्ट आयर्नच्या भरड (रफ) टर्निंगसाठी.
अधिक झीज प्रतिरोध आणि कठीणपणा ज्या ठिकाणी गरजेचा असतो त्या ठिकाणी याचा वापर केला जातो.
CBN मध्ये बोरॉन नायट्राइडबरोबर सिरॅमिक किंवा टायटॅनिअम नायट्राइड बाईंडर असतो.
अधिक वेगाने यंत्रण करताना उच्च तापमानाचा प्रतिकार करतात.
क्युबिक बोरॉन नायट्राइड एका विशिष्ट कामासाठी वापरले जाते. यामध्ये योग्य आर्थिक गणित, अपेक्षित टॉलरन्स आणि ग्राइंडिंगसदृश फिनिश मिळविण्यासाठी भक्कम टर्निंग सेंटर तसेच संतुलित पकड असणे गरजेचे असते.
55 HRC पेक्षा जास्त कठीणता असलेल्या भागांसाठी सिरॅमिकपेक्षा क्युबिक बोरॉन नायट्राइड अधिक चांगली कामगिरी बजावतात.आज अनेक ठिकाणी कठीण यंत्रभागांचे ग्राइंडिंग करण्यापेक्षा त्यांचे टर्निंग करण्याकडे अनेकांचा कल असतो. यामध्ये कठीणता असलेले गिअर ब्लँक, ड्राइव्ह शाफ्ट इत्यादींसाठी याचा वापर केला जातो. अर्थात यासाठी हार्डिंजसारख्या हार्ड पार्ट टर्निंग करण्याची क्षमता असलेल्या मशिनची गरज असते.
2.6. पॉलिक्रिस्टलाइन डायमंड (PCD)
ॲल्युमिनिअमचे कमी तापमानावर टर्निंग करताना तसेच, अतिशय ॲब्रेझिव्ह असलेल्या हायपरयुटेक्टिक ॲल्युमिनिअमच्या (10% सिलिकॉन) टर्निंगसाठी आणि नॉन मेटल, नॉन फेरस मटेरियलसाठी वापर केला जातो.
उच्च दर्जाची झीज प्रतिरोधक ग्रेड, चिपसाठी संवेदनाक्षम असते.
इन्सर्टच्या कोपऱ्यावर पॉलिक्रिस्टलाइन डायमंडने ब्रेझिंग केलेले असते किंवा मूळ मटेरियलवर डायमंडचा पातळ लेप दिलेला असतो.
दीर्घ आयुर्मान असलेले टूल तसेच उच्च झीज प्रतिरोधक शक्ती. जास्त तापमानामुळे विघटन होते, तसेच लोखंडात सहज विरघळतात.
दुचाकी आणि चारचाकी वाहनांमध्ये असलेल्या ॲल्युमिनिअमच्या भागांचे बोअरिंग करताना यांचा वापर केला जातो. याचे मुख्य कारण म्हणजे, कमी टॉलरन्स, उत्तम पृष्ठभाग फिनिश मिळविताना कार्बाइडच्या तुलनेत दीर्घ आयुष्य मिळते.
3. टर्निंगवर परिणाम करणारे घटक
टर्निंग म्हणजे दोन प्रकारच्या हालचालींचा एकत्रित परिणाम असतो. उदाहरणार्थ, गोल फिरणारी कार्यवस्तू आणि पुढे सरकणारे टूल. (चित्र क्र. 3) काहीवेळा कार्यवस्तू स्थिर असते आणि टूल त्याच्याभोवती काप काढण्यासाठी फिरत असते, पण मूळ तत्व तेच असते.
टूल सरकण्याची हालचाल कार्यवस्तुच्या अक्षाच्या दिशेने असते. त्यामुळे कार्यवस्तुचा व्यास टर्निंग केल्यानंतर लहान होतो. काहीवेळा टूल कार्यवस्तुच्या शेवटी केंद्ररेषेपर्यंत सरकविले (फेसिंग ऑफ) जाते. बऱ्याचवेळेला या दोन्ही हालचाली एकाचवेळ करून टेपर किंवा वक्र आकार (प्रोफाइल) मिळविले जातात. सध्या वापरल्या जाणाऱ्या टर्निंग सेंटरमधील उपलब्ध प्रोग्रॅम वापरून हे अगदी सहजपणे करता येते.
कर्तन वेगाचे (Vc) सूत्र असे आहे,
Vc : यंत्रण वेग मी./मिनिट
Dm : यंत्रण केलेला व्यास
n : प्रति मिनिट परिभ्रमणे (आर.पी.एम.)
कापाची खोली, टूलचा प्रवेश कोन, सरकवेग, मटेरियलचा प्रकार आणि टूलची भूमिती यानुसार चिपमध्ये बदल होतात.
टूलच्या प्रवेश कोन आणि नोज त्रिज्येचा चिपच्या काटछेदावर (क्रॉस सेक्शन) परिणाम होतो. टूल नोज त्रिज्येचा (चित्र क्र. 4) प्रतिपरिभ्रमण सरकवेगावरती परिणाम होतो. टूलच्या प्रवेश कोनाचा यंत्रात तयार होणाऱ्या बलांच्या दिशांवर, काप घेताना उपयोगात येणाऱ्या कर्तन कडेच्या लांबीवर, कर्तन कडेचा कार्यवस्तुशी होणाऱ्या संपर्कावर तसेच काप घेण्याच्या प्रकारावर परिणाम होतो.
प्रवेशकोन (चित्र क्र. 5) साधारणपणे 45 ते 90 अंशाच्या दरम्यान ठेवला जातो, मात्र प्रोफाइल यंत्रणाचेवेळी यापेक्षा अधिक मोठे प्रवेश कोन उपयोगी ठरतात. प्रवेशकोन कमी असला तर चिपची जाडी कमी होते आणि रुंदी वाढते. स्पायरल पिच योग्य पद्धतीने वाढविले तर चिपच्या प्रवाहाची दिशा अधिक योग्य पद्धतीने बदलता येते.
कापाच्या खोलीचे चिप निर्मितीवर होणारे परिणाम
कापाची खोली (ap) म्हणजे कार्यवस्तूमध्ये शिरणारी कर्तन कडेची लांबी. कापाच्या खोलीनुसार (ap) तसेच कर्तन कडेच्या नोज त्रिज्येमुळे चिपचा आकार आणि दिशा बदलत असतात. जेव्हा कापाच्या खोलीच्या प्रमाणात टूलची नोज त्रिज्या (जी कर्तन कडेचा महत्त्वाचा भाग असते) कमी असते तेव्हा स्पायरल चिप (चित्र क्र. 6) तयार होते.
कापाची खोली वाढल्यानंतर त्रिज्येचा परिणाम कमी होतो, तसेच कर्तन कडेच्या प्रवेश कोनाचा परिणाम वाढतो आणि बाहेरच्या दिशेने प्रवाहित होणाऱ्या सर्पिलाकार (स्पायरल) चिप तयार होतात. सरकवेगाचा चिपच्या रुंदीवर आणि त्यांच्या प्रवाहाच्या दिशेवरही परिणाम होतो.
4. वरील माहितीच्या पोर्शभूमीवर आता आपण टर्निंग प्रक्रियेसाठी टूलची निवड कशी करायची ते पाहू.
4.1. यंत्रभाग आणि कार्यवस्तूचे मटेरियल यंत्रभाग
सर्वप्रथम यंत्रभागाचे आकारमान आणि यंत्रण केल्या जाणाऱ्या पृष्ठभागाच्या दर्जाचा अभ्यास करा.
यंत्रणाचा प्रकार (लाँगिट्युडिनल, कॉपिंग)
यंत्रण आतून का बाहेरून
रफिंग, मध्यम किंवा फिनिशिंग
टूलचा मार्ग (पाथ)
टूलच्या पासची संख्या
टॉलरन्स
कार्यवस्तूचे मटेरियल
यंत्रणक्षमता
कास्ट, फोर्ज्ड किंवा प्राथमिक यंत्रण केलेले
चिप ब्रेक्रिंगची वैशिष्ट्ये
P/M/K/S/H प्रकार
कठीणता
मिश्रधातुतील घटक धातू
4.2. मशिनच्या निवडीमधील प्रमुख मुद्दे
मुख्यतः मोठ्या व्यासासाठी स्थिरता, ताकद आणि टॉर्क
कार्यवस्तू पकडण्याची पद्धत
टूलची स्थिती (पोझिशन)
टूल बदलण्यास लागणारा वेळ/टरेटमधील टूलची संख्या
आर.पी.एम.वरील मर्यादा, बार फीड मॅगेझिन
सबस्पिंडल किंवा टेलस्टॉक उपलब्धता
शक्य असतील ते आधार
प्रोग्रॅमिंग सहज करण्याची सोय
कटिंग फ्लुइड आणि शीतक
4.3. टूल होल्डरची निवड
निवडलेल्या इन्सर्टच्या आकाराप्रमाणे टूल होल्डरची निवड करावी लागते. इन्सर्टचा आकार आणि पॉइंट कोन यामध्ये खूप बदल होत असतात. सर्वात कमी म्हणजे, 35 अंशापासून ते गोल इन्सर्टपर्यंत कोन बदलतो. हा कोन 550, 600, 800, 900 चा असतो. प्रत्येक कोनाचे काही विशिष्ट गुणधर्म असतात. काही भरड (रफ) यंत्रणासाठी आवश्यक ताकद देतात तर काही प्रोफाइल आकारांना आवश्यक संपर्क साधण्यासाठी उपयुक्त ठरतात. त्याचबरोबर प्रत्येकाच्या काही विशिष्ट मर्यादा असतात. उदाहारणार्थ, यंत्रणाचेवेळी कर्तन कडेला जास्त भागापर्यंत पोहोचणे शक्य करताना कर्तन कड कमकुवत होण्याची शक्यता असते.
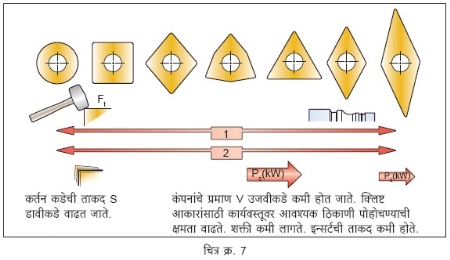
चित्र क्र. 7 मधील उजवीकडील आकाराच्या इन्सर्टच्या कर्तन कडा यंत्रण करण्याच्या आकारानुसार सहज पोहोचू शकतात. मात्र, त्यांच्या कर्तनकडा कमकुवत असतात. याउलट डावीकडील आकाराचे इन्सर्ट दणकट असतात. परंतु, त्यामध्ये कंपने येण्याची शक्यता अधिक असते. तसेच ते अधिक उर्जा वापरतात. परंतु सेटअपच्या भक्कमपणानुसार त्यांची निवड करावी. खड्डा पडून झीज होण्याला (नॉच वीअर) प्रतिरोध करणाऱ्या इन्कोनेल आणि तत्सम HRSA मटेरियलच्या यंत्रणासाठी दणकटच नव्हे तर गोल इन्सर्टसुद्धा वापरायला प्राधान्य दिले जाते. त्यामुळे आवश्यक सुगमता (ॲक्सेसेबिलिटी) मिळविण्यासाठी आवश्यक असणाऱ्या टूलच्या प्रवेश कोनाच्या गरजेनुसार इन्सर्टच्या आकाराची निवड करणे आवश्यक असते.
इन्सर्टला अधिक ताकद आणि विेशासार्हता देण्यासाठी शक्य तेवढा जास्त पॉइंट कोन असण्याची गरज असते. पण ही निवड कापामधील फरकांवरही अवलंबून असते. मोठ्या पॉइंट कोनामुळे इन्सर्ट भक्कम होतात, मात्र यंत्रण करताना मशिनला अधिक ताकद वापरावी लागते. यामुळे जास्त कंपने येण्याची शक्यता असते. याउलट पॉइंट कोन लहान असल्यास इन्सर्ट कमकुवत होतात. तसेच यंत्रणाचेवेळी कर्तन कडेची कमी लांबी कार्यवस्तुच्या संपर्कात आल्याने निर्माण होणाऱ्या उष्णतेचा इन्सर्टवर परिणामहोऊ शकतो.
4.4. इन्सर्टच्या नोज त्रिज्येची निवड
टर्निंग प्रक्रियेत नोज त्रिज्या हा महत्त्वाचा घटक असून वेगवेगळ्या नोज त्रिज्या असलेले इन्सर्ट उपलब्ध असतात.
मोठ्या नोज त्रिज्येच्या तुलनेत कमी नोज त्रिज्येचे इन्सर्ट कमकुवत असतात, मात्र लहान काप घेण्यासाठी अधिक उपयुक्त असतात.
मोठ्या नोज त्रिज्येमुळे भक्कम कर्तनकड मिळते, मात्र मटेरियल काढण्यासाठी सरकवेग अधिक ठेवावा लागतो.
(चित्र क्र. 8)
सर्वसाधारणपणे कापाच्या खोलीपेक्षा थोडी कमी नोज त्रिज्या निवडण्याचा संकेत (थम्ब रुल) आहे. त्यामुळे रेडियल कर्तनबल कमीतकमी ठेवता येते, तसेच सर्वाधिक नोज त्रिज्येमुळे मिळणारी भक्कम कर्तन कड, उत्तम पृष्ठभाग आणि कर्तन कडेच्या सर्व भागांवर एकसमान दाब असे फायदे मिळविता येतात. भरड यंत्रणासाठीचा दुसरा नियम म्हणजे सरकवेग, नोज त्रिज्येच्या निम्मा असणे आवश्यक असते.
4.5. टूल मार्गाची निवड
टूल मार्गाचा (चित्र क्र. 9) यंत्रणाच्या प्रक्रियेवर आणि टूलच्या निवडीवर पुढीलप्रमाणे परिणाम होतो.
चिपवर नियंत्रण
इन्सर्टची झीज
पृष्ठभागाची गुणवत्ता
टूलचे आयुष्य
ज्यावेळी यंत्रण करून विशिष्ट आकार (प्रोफाइल) (चित्र क्र. 10) तयार करायचा असतो, त्यावेळी समाधानकारक यंत्रण होण्यासाठी योग्य प्रवेश कोन निवडणे आवश्यक असते.
जे टर्निंग टूल मार्ग प्लंजिंगऐवजी प्रोफाइल तयार करतात ते प्रक्रियेसाठी अधिक सुरक्षित आणि सातत्यपूर्ण ठरतात. ते यंत्रभागांमध्ये कमी ताण (स्ट्रेस) निर्माण करीत असल्याने HRSA सारख्या यंत्रणासाठी अवघड असलेल्या मटेरियलचे यंत्रण करण्यासाठी प्राधान्याने वापरले जातात.
सारांश
टर्निंग प्रक्रियेसाठी योग्य टूल निवडण्यासाठी पुढे दिलेला क्रम सुचविता येईल.
टूल होल्डर
इन्डेक्सेबल इन्सर्ट
आकार
आकारमान
नोजची त्रिज्या
भूमिती
ग्रेड
यंत्रणाचे तपशील
टूल उत्पादकांनी केलेल्या सूचनांची जागा घेण्याचा या लेखाचा प्रमुख हेतू नसून, टूलचा वापर करणाऱ्यांच्या दृष्टीने सर्वसाधारण दृष्टिकोन मांडणे एवढाच आहे.
9359104060
रवि नाईक यांना टूलिंग क्षेत्रातील 40 हून अधिक वर्षांचा अनुभव असून ते टूलिंग आणि मशिनिंग ॲप्लिकेशनविषयक
सल्लागार आहेत.