गेल्या काही लेखातून आपण ओव्हरऑल इक्विपमेंट इफेक्टिव्हनेस (OEE) ही संकल्पना समजून घेण्याचा प्रयत्न करीत आहोत. या संकल्पनेमध्ये मशिनची उपलब्धता, कार्यक्षमता आणि उत्पादनाचा दर्जा यांचा समावेश केला जातो. आपण यासाठी मशिनची उपलब्धता आणि उत्पादनाची कामगिरी कशी मोजता येईल, तसेच या दोन्ही गोष्टींवर परिणाम करणारे घटक कोणते आणि या घटकांवर नियंत्रण ठेवण्यासाठी कोणते उपाय करता येतात याचे विश्लेषण पाहिले. या लेखात उत्पादनाचा दर्जा या OEE मधील शेवटच्या घटकाचा आपण विचार करणार आहोत.
आपल्याला गुणवत्ता म्हणजे काय हे माहिती असल्याने त्याची व्याख्या इत्यादी तपशिलात आपण जाणार नाही.
एकूण OEE चे मूल्यमापन करताना गुणवत्तेच्या कामगिरीचे मोजमाप ‘गुणवत्तेच्या दराची टक्केवारी’ असे करावे लागते. ‘धातुकाम’च्या डिसेंबर 2018 अंकातील पहिल्या लेखात आपण पाहिलेले गुणवत्ता दराचे सूत्र पुढे दिले आहे.
गुणवत्तेचे मूल्यमापन करण्याची ही अगदी प्राथमिक पद्धत आहे. ज्या एकूण कालमर्यादेसाठी OEE ठरविला जातो, त्या पूर्ण वेळेत एकाच प्रकारच्या यंत्रभागाचे उत्पादन केले गेले असेल तर ही पद्धत चालू शकते. पण यंत्रभाग बनविणाऱ्या कारखान्यात उत्पादनासाठी वेगवेगळा आवर्तन काळ (सायकल टाइम) लागणारे विविध भाग बनविले जातात, अशावेळी आपण वरील सूत्रात चांगले आणि वाईट भाग बनविण्यासाठी मशिनला लागलेला वेळ याचा विचार करावा.
यंत्रभागाच्या उत्पादनासाठी लागणारा मशिनचा एकूण प्रमाणित वेळ
TTOTAL = एका भागासाठी लागणारा प्रमाणित आवर्तन काळ X एकूण उत्पादन केलेले भाग.
बाद झालेले भाग आणि दुरुस्त केलेले भाग यासाठी लागणारा मशिनचा एकूण प्रमाणित वेळ
TRR = एका भागासाठी लागणारा प्रमाणित आवर्तन काळ X (बाद झालेले भाग + दुरुस्त केलेले भाग)
या ठिकाणी आपल्याला एका भागासाठी लागणारा प्रमाणित वेळ धरणे आवश्यक आहे. भाग बनविण्यासाठी लागलेला प्रत्यक्ष वेळ या ठिकाणी घेऊन चालणार नाही. उत्पादकता काढताना लागलेल्या प्रत्यक्ष वेळेचा परिणाम लक्षात घेतला जातो. भाग बनविण्यासाठी लागणाऱ्या वेळेचे मोजमापाच्या एककात रूपांतर करून, वेगवेगळी वेळ लागणारे भाग बनविण्यासाठी वापरलेल्या यंत्रणाच्या गुणवत्तेचा दर ठरविता येतो. ही पद्धत जास्त कालावधीसाठीचा OEE ठरविण्यासाठी उपयुक्त ठरते.
गुणवत्तेवर परिणाम करणारे घटक
गुणवत्तेमधील सुधारणा हा एक वेगळा विषय असून, गेली अनेक वर्षे गुणवत्तेवर लक्ष केंद्रित करून त्याचे व्यवस्थापन करणाऱ्या वेगवेगळ्या पद्धती/तंत्र सतत विकसित केली गेली आहेत. त्यामध्ये वेळोवेळी सुधारणा केल्या जात आहेत. आपण मशिन शॉपच्या दृष्टिकोनातून OEE च्या संदर्भातील गुणवत्तेवर लक्ष केंद्रित करूया. उत्पादनाची गुणवत्ता आणि शेवटी बाद होणाऱ्या/पुन्हा काम कराव्या लागणाऱ्या भागांची संख्या ठरविताना पुढील घटक महत्त्वाचे ठरतात.
1. मशिन वापरण्यासाठी सक्षम कर्मचारी.
2. उत्पाद बनविण्यासाठी सुयोग्य (कम्पॅटिबल) आणि सक्षम (कॉम्पिटंट) मशिन.
3. उत्पाद आणि मशिन यांचा योग्य मिलाफ घडवून आणणारी सुयोग्य पद्धत.
4. उत्पाद आणि प्रक्रिया यांना पूरक गुणवत्ता व्यवस्थापन पद्धती.
1. मशिन वापरण्यासाठी सक्षम कर्मचारी
एखादे विशिष्ट मशिन किंवा प्रक्रिया हाताळण्यासाठी एखादा कर्मचारी सक्षम आहे का हे निश्चित करण्यासाठी आणि त्याचे मूल्यमापन करण्याची पद्धत आहे. पारंपरिक मशिनसाठी कर्मचाऱ्याचे कौशल्य उत्पादनाच्या दर्जावर परिणाम करण्यात मोठी भूमिका बजावत असते. मात्र, आजकाल आपण बघतो की, पारंपरिक मशिनची जागा सी.एन.सी. मशिन घेत आहेत. स्वयंचलन आणि सी.एन.सी. मशिनचा उदय झाल्यामुळे ‘कौशल्याची कमी पातळीसुद्धा मशिन चालविण्यास पुरेशी ठरेल’ असा समज होत आहे. पण हे लक्षात घेतले पाहिजे की, हालचालीवरील नियंत्रण सोडले तर मशिन आणि प्रक्रियेचे पॅरामीटर आदी गोष्टी ऑपरेटरलाच हाताळाव्या लागतात. बऱ्याचवेळा ऑपरेटरने सी.एन.सी. मशिनवरील टूल बदलण्यासारखी एखादी प्रक्रियेत बदल करणारी कृती केल्यानंतर तयार होणारे भाग बाद होताना दिसतात. प्रक्रिया सुरू असताना मशिन अनेकवेळा धोक्याचे इशारे आणि संदेश देत असते. ऑपरेटरने हे इशारे लक्षात घेऊन योग्य ती पावले उचलणे गरजेचे असते. या दृष्टिकोनातून विचार केला तर प्रशिक्षण देऊन (चित्र क्र. 1) ऑपरेटरची कौशल्ये विकसित करणे आणि त्यांच्या कौशल्याचे मूल्यमापन करणे अतिशय महत्त्वाचे असते. कर्मचार्यांना मशिन चालविण्यासाठी सक्षम बनविण्याकरता कंपनी, कर्मचारी कौशल्य विकास कार्यक्रम बनवू शकते. आपण ‘मशिन चालविण्यासाठी सक्षम’ हा शब्दप्रयोग वापरतो जो एका विशिष्ट मशिनशी निगडित असून ‘कुशल’ या सर्वसाधारण संज्ञेपेक्षा त्याचा अर्थ वेगळा आहे.
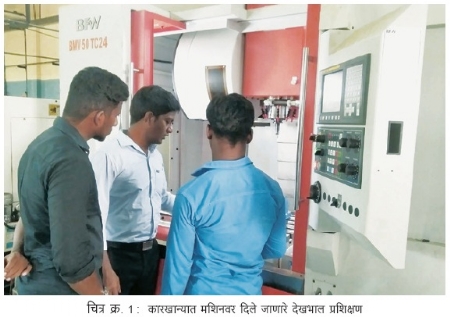
2. उत्पाद बनविण्यासाठी सुयोग्य आणि सक्षम मशिन
अ. सुयोग्यता (कम्पॅटिबिलिटी)
कधीकधी मशिन उत्पादनाशी सुयोग्य नसणे हे यंत्रभाग बाद होण्यामागचे मूळ कारण असते. बऱ्याच वेळा सुविधा आणि आर्थिक बाबतीमधील मर्यादा, व्यवसायामधील अडचणी आणि कधीकधी मशिनच्या क्षमतेविषयी अपुरी माहिती या कारणांमुळे उत्पादनाशी सुयोग्य नसलेली मशिन वापरण्यात येतात. बऱ्याचवेळा असेही निदर्शनास येते की, मशिनचे स्पिंडलही इष्टतम यंत्रण पॅरामीटरना हाताळण्यासाठी पुरेसे सक्षम नसतात. उदाहरणार्थ, पोलाद/ओतीव लोखंड यांच्या तुलनेत ॲल्युमिनिअमच्या यंत्रणासाठी जास्त आर.पी.एम. आणि कमी टॉर्क लागतो. जर स्पिंडल इष्टतम पॅरामीटर हाताळू शकत नसेल, तर त्यासाठी केलेल्या तडजोडीमुळे गुणवत्ता धोक्यात येऊ शकते. एखादे उत्पादन विकसित करताना विचाराधीन असलेले मशिन अपेक्षित प्रक्रियेसाठी सुयोग्य असल्याची खात्री करणे हे प्रक्रिया ठरविणारा अभियंता आणि व्यवस्थापन यांच्यासाठी आवश्यक असते. वर सांगितल्याप्रमाणे जर आर्थिक आणि व्यावसायिक अडचणींमुळे सुयोग्य मशिन उपलब्ध करणे शक्य नसेल तर सुरुवातीला थोड्या काळासाठी प्रक्रियेवर विशेष, कल्पक प्रकारे नियंत्रण ठेवणे आणि नंतर दूरगामी परिणामांसाठी सुयोग्य मशिनसाठी गुंतवणूक करणे गरजेचे असते.
ब. क्षमता (कॉम्पिटन्स)
जर मशिन सुयोग्य असेल पण झीज झाल्यामुळे तसेच इतर बिघाडांमुळे हवी तशी गुणवत्ता देऊ शकत नसेल, तर आपण मशिनला अक्षम (इन्कॉम्पिटंट) म्हणतो. जेव्हा आपल्याला काही भागांचे अतिशय कमी मर्यादा असलेल्या अचूकतेमध्ये यंत्रण करायचे असते तेव्हा मशिनची क्षमता अतिशय महत्त्वाची ठरते. मशिनच्या क्षमतेचे मूल्यमापन करण्याची सोपी पद्धत म्हणजे एखाद्या उत्पादनाच्या आपल्याला महत्त्वपूर्ण असणाऱ्या मोजमापांची अपेक्षित मोजमापापेक्षा किती फारकत (रीडिंगचा स्प्रेड) दिसते आहे हे पाहणे. यासाठी महत्त्वपूर्ण मशिनच्या प्रक्रियाक्षमतेचे नियमितपणे संख्याशास्त्रीय मोजमाप केले पाहिजे. यामुळे उत्पादन अभियंत्याला योग्य वेळेत योग्य ती सुधारणा करून बाद होणाऱ्या उत्पादांची संख्या नियंत्रित करून OEE वर होणारा परिणाम टाळता येईल.
जेव्हा एखादे नवीन उत्पादन विकसित करायचे असते तेव्हा उत्पादनाच्या ज्या तपशिलांवर काटेकोर नियंत्रण ठेवायचे आहे, त्यांच्याकडे विशेष लक्ष देणे आवश्यक असते. जेव्हा आपल्याला कारखान्यातील उपलब्ध मशिनची क्षमता माहिती असेल तेव्हाच आपण विशिष्ट उत्पादन विशिष्ट मशिनवर पाहिजे त्या दर्जाचे मिळवू शकू. विशिष्ट उत्पादनांसाठी नवीन आणि समर्पित गुंतवणूक करायची असेल तेव्हा मशिन उत्पादकाकडून आणि प्रक्रिया आरेखकाकडून उच्च दर्जा आणि प्रक्रिया क्षमतेची मागणी केली गेली पाहिजे. असे केल्यामुळे झीज झाल्यामुळे मशिनच्या गुणवत्तेतील होणाऱ्या नुकसानावर बऱ्याच काळपर्यंत नियंत्रण ठेवता येऊ शकते.
3. उत्पाद आणि मशिन यांचा योग्य मिलाफ घडवून आणणारी सुयोग्य पद्धत
सर्वात आधी मशिनच्या क्षमतेची माहिती घेऊन प्रक्रियेचे पॅरामीटर ठरवावे लागतात. या दोन्ही गोष्टी एकमेकांशी जुळत नसतील तर त्याचा उत्पादनाच्या पॅरामीटरवर विपरीत परिणाम होऊ शकतो. उदाहरणार्थ, ज्या मशिनमध्ये पुरेशी टॉर्क क्षमता आणि ताकद नाही अशा मशिनवर मोठ्या व्यासाचा मिलिंग कटर योग्य कामगिरी करू शकत नाही. तसेच उत्पादनाच्या गरजेनुसार सक्षम अशा प्रक्रिया पॅरामीटरची निवड केली पाहिजे हे पुढील उदाहरणावरून स्पष्ट होते.
सिलिंडर हेडचे (चित्र क्र. 2) यंत्रण करताना यंत्रण केलेल्या पृष्ठभागावर काही भोके पाडण्यासाठी ड्रिलिंग करायचे होते. ही भोके ओतकामाने बनविलेल्या सिलिंडर हेडमधील पाण्याच्या प्रवाहासाठी असलेल्या अंतर्गत गुंतागुंतीच्या आकाराच्या पोकळीत उघडणार होती. मशिनच्या क्षमतेनुसार प्रक्रिया ठरविणाऱ्या अभियंत्याने सर्वोत्तम उत्पादकता मिळण्यासाठी उच्च सरकवेग ड्रिलिंगची निवड केली. जेव्हा ड्रिल पोकळीत उघडण्याआधी 0.25 ते 1 मिमी. इतक्या खोलपर्यंत पोहोचले तेव्हा शेवटचा (उरलेला) धातुचा भाग ड्रिलच्या उच्च अक्षीय बलामुळे चिपच्या स्वरुपात निघण्याऐवजी एका चकतीच्या आकारात तुटला. त्यामुळे चकती पाण्याच्या आच्छादनाच्या पोकळीत पडली.
सिलिंडर हेडची जुळणी करण्यापूर्वी संपूर्ण सिलिंडर हेड कचऱ्यापासून किंवा इतर अनावश्यक मटेरियलपासून पूर्णपणे मुक्त असणे गरजेचे आहे. सिलिंडर स्वच्छ करण्यासाठी त्याला धुण्याची प्रक्रिया होती मात्र, धातुची चकती पाण्याच्या मार्गात अडकून बसली होती. पाण्याच्या वितरणात धातुची चकती अडकण्याचा संभाव्य धोका असल्यामुळे हे सिलिंडर हेड वापरण्यास अयोग्य ठरविले जाते. याचा अर्थ असा होतो की, प्रक्रियेसाठी मशिन सक्षम होते पण उत्पादनासाठी सक्षम नव्हते. उत्पादनासाठी सक्षम प्रक्रियेमध्ये, छिद्र पोकळीत उघडण्याआधी सरकवेग कमी ठेवला गेला असता तर चकतीच्या आकाराचा धातुचा तुकडा पडण्याऐवजी धातुच्या बारीक चिप निघाल्या असत्या. दुसरे उदाहरण आहे ते म्हणजे बोअरिंगची प्रक्रिया संपल्यानंतर बोअरिंग बार बाहेर काढताना तयार होणारी रेषेची खूण. जेव्हा बोअरमध्ये ऑइल किंवा गॅस सील लावायचे असते तेव्हा ही खूण स्वीकारली जात नाही.
4. उत्पादन आणि प्रक्रिया यांना पूरक गुणवत्ता व्यवस्थापन पद्धत
उत्तमपणे अभियांत्रिकी आरेखन केलेल्या प्रक्रियेसाठी गुणवत्ता व्यवस्थापन पद्धतीचे भक्कम पाठबळ असणे गरजेचे असते. नियमित परीक्षण करून उत्पादन केलेल्या भागांच्या गुणवत्तेचे नियंत्रण करणे गरजेचे असते आणि भागांच्या परीक्षणामधून मिळालेल्या माहितीनुसार प्रक्रियेवर नुकसान होण्यापूर्वी आवश्यक प्रतिबंधात्मक (प्रोॲक्टिव्ह) कृती कराव्या लागतात. बऱ्याच गुणवत्ता व्यवस्थापन पद्धतीमध्ये प्रक्रिया नियंत्रणावर सखोल अभ्यास आणि काम केले जाते. यात महत्त्वाचा मुद्दा असतो तो म्हणजे उत्पादन आणि प्रक्रिया यांच्या गरजेनुसार पद्धत लवचीक ठेवावी लागते. उत्पादन आणि प्रक्रियेनुसार सक्षम अशी पद्धत वापरली जाणे महत्त्वाचे असते.
तपासणीसाठी वापरण्याची उपकरणे, तपासणीची वारंवारिता, निरीक्षणांची नोंद करण्याची पद्धत या सर्व गोष्टी प्रक्रियेची क्षमता, मशिनची क्षमता आणि कर्मचाऱ्याची क्षमता यांची वास्तव आणि अचूक माहिती घेऊन मगच ठरवाव्या लागतात. गुणवत्ता व्यवस्थापन पद्धतीमधून यासंबंधी मार्गदर्शन करण्यात येते, पण या मार्गदर्शनाची विशिष्ट उत्पादन पद्धतीशी योग्य सांगड घातली तरच गुणवत्तेची उत्तम कामगिरी मिळते. ही OEE चे कमीतकमी नुकसान होण्याची गुरुकिल्ली आहे.
या लेखमालेत आपण OEE ची संकल्पना, त्यावर परिणाम करणारे घटक आणि त्यावर नियंत्रण करणाऱ्या पद्धती पाहिल्या. कारखान्यात मशिनच्या वेळेची उपलब्धता, कामगिरी आणि गुणवत्ता या सर्व बाबतीत होणारे नुकसान याबद्दलची आवश्यक ती सर्व माहिती मिळणारी माहिती व्यवस्था तयार केली पाहिजे. या माहितीच्या आधारे OEE ची मोजणी करता येते. OEE चे आकडे कंपनीच्या आर्थिक फायद्यावर थेट परिणाम करणारे असतात. तसेच वेगवेगळ्या कारणांमुळे होणारा तोटा, त्याबाबतीत त्वरित कारवाई करण्याचे संदेश देतात आणि व्यवस्थापनाला त्यातून लक्ष्य आणि दिशा दाखविण्याचे काम करतात.
9359104060
राजेश म्हारोळकर यांत्रिकी अभियंते असून, ते सल्लागार म्हणून काम करतात. ‘श्रीनिवास इंजिनिअरिंग ऑटो कंपोनंटस् प्रा. लि.’चे ते संचालक आहेत. ही कंपनी ट्रॅक्टरचे यंत्रभाग आणि ऑटोमोटिव्ह उद्योगांना आयर्न कास्टिंग आणि प्रिसिजन यंत्रणाची सेवा देते.