सध्याच्या स्पर्धेच्या युगात टिकून राहण्यासाठी प्रत्येक कारखानदाराने नवनवीन सुधारणा करण्याचे प्रयत्न करणे तसेच आपल्याकडे उपलब्ध असलेल्या साधनसामुग्रीचा वापर करून उत्पादनक्षमता कशी वाढविता येईल याबद्दल नेहमीच विचार करणे गरजेचे आहे. याच विचाराने आम्ही आमच्या सातारा येथील खुटाळे इंजिनिअरिंग प्रा. लि. कंपनीमध्ये ‘लीन मॅनेजमेंट’चे तत्त्व वापरून, शॉप फ्लोअरवर आवश्यक ते बदल करून वाया जाणारा वेळ आणि खर्चात कशा प्रकारे कपात केली याविषयीची माहिती या लेखात दिली आहे.
लीन व्यवस्थापन म्हणजे काय?
लीन व्यवस्थापन संकल्पनेनुसार कंपनीच्या प्रक्रियेमध्ये सातत्याने बदल करीत विकास करत राहणे आवश्यक असते. गुणवत्तापूर्ण आणि कार्यक्षम उत्पादनासाठी सातत्याने प्रक्रियांमध्ये सुधारणा करीत राहणे लीन मॅनेजमेंटचा मुख्य हेतू आहे. हा हेतू साध्य करताना उत्पादन प्रक्रियेमधील वाया जाणारा वेळ, पैसा यांना कारणीभूत ठरणारे घटक दूर करणे यावर ही संकल्पना आधारलेली आहे.
लीन व्यवस्थापनामध्ये कंपनीमधील सर्व प्रक्रिया प्रथम समजून घेऊन कार्यक्षम उत्पादन निर्मितीसाठी त्यात बदल केले जातात किंवा प्रक्रियेतील काही अनावश्यक टप्पे (जे ग्राहकाच्या उत्पादनक्षमतेवर परिणाम करणारे नसतात.) वगळले जातात.
क्लस्टरच्या माध्यमातून बदल
आज देशभरात मोठे आणि छोटे असे अनेक उद्योग व्यवसाय आहेत. मोठ्या कंपन्यांमध्ये विविध विभागांमध्ये कामाची विभागणी केलेली असते. त्यामुळे छोट्या कंपन्यांच्या तुलनेत या कंपन्यांचे काम व्यवस्थित केले जाते. मात्र, आजही अनेक छोट्या कंपन्यांमध्ये कर्मचारी संख्या आणि जागा मर्यादित असल्यामुळे कामांचे व्यवस्थापन तितके शास्त्रीय नसते. त्यामुळे तेथील प्रक्रिया काहीशा विस्कळित असल्याचे आढळून येते. मोठ्या कंपन्यांप्रमाणे छोट्या कंपन्यांचेसुद्धा काम व्यवस्थित व्हावे या उद्देशाने लघु, मध्यम उद्योजकांसाठी क्लस्टर संकल्पना उदयास आली. यामागचा मुख्य उद्देश म्हणजे एकाच प्रकारचे काम करणार्या उद्योजकांनी एकत्र येऊन त्यांच्याकडील चांगल्या गोष्टींची देवाणघेवाण करणे, तसेच काही समान समस्यांवर मात करण्यासाठी प्रशिक्षण आयोजित करणे होय.
क्लस्टरच्या माध्यमातून आम्ही रोजच्या कामाचे नियोजन, कोणकोणत्या गोष्टींचा विचार केला पाहिजे, कोणत्या कामाचा किंवा गोष्टींचा पाठपुरावा केला पाहिजे, त्याशिवाय टोटल एम्प्लॉई इन्व्हॉल्व्हमेंट, सेफ्टी कल्चर आदी गोष्टी शिकण्यास मदत झाली. सध्या सुरू असलेल्या झिरो डिफेक्ट क्लस्टरमध्ये आम्ही अनेक गोष्टी शिकतोय पैकी फाइव्ह सेन्स ट्री कल्पना जसे की, दृष्टी (डोळ्यांना दिसणार्या काही चुकीच्या गोष्टी), आवाज (जास्त किंवा वेगळा येत असेल), वास (वेगळा येत असेल), स्पर्श (मशिन गरम). आणि चव म्हणजेच जाणीव (फील) ही पाच इंद्रिये वापरून कंपनीत जे काही चुकीचे आहे ते शोधायचे आणि त्यावर उपाय करण्याची सवय लावून शून्य दोष असलेल्या उत्पादन निर्मितीची चालना आम्हाला मिळाली.
सर्वात पहिल्यांदा आम्ही 2010 मध्ये मराठा चेंबर आणि पुढे आतापर्यंत कॉन्फेडरेशन ऑफ इंडियन इंडस्ट्री (CII) आणि गोदरेज अँड बॉइस कंपनीने संयुक्तपणे आयोजित केलेल्या लीन मॅन्युफॅक्चरिंग एक्सलन्स आणि ग्रीनको प्रशिक्षणामध्ये भाग घेतला. त्यातून आमच्या असे लक्षात आले की, आपल्या कंपनीत अनेक बदल करून सुधारणा करणे शक्य आहे आणि गरजेचे आहे. आमच्या कारखान्यात फर्निचरमध्ये लागणार्या धातुच्या फ्रेम तसेच प्रेस्ड आणि फॉर्म्ड कंपोनंट (चित्र क्र. 1) तयार केले जातात.
3M चा अभ्यास
कुठल्याही कंपनीचे कार्य सुरळीत चालण्यासाठी सर्वप्रथम येणार्या अडचणींचा अभ्यास करणे अतिशय आवश्यक असते. त्यानुसार आम्ही 3M म्हणजे ‘मुडा’ (नुकसान - वाया जाणारे मटेरियल, वेळ, नैसर्गिक स्त्रोत), ‘मुरी’ (कामाचा किंवा इतर ताण), ‘मुरा’ (असंतुलन) या तीन गोष्टींवर लक्ष केंद्रित करायचे ठरविले आणि त्यावर उपाय शोधण्याचे निश्चित केले. कंपनीत सात प्रकारच्या अडचणी असल्याचे आमच्या निदर्शनास आले. यामध्ये उत्पादांमधील दोष, अतिरिक्त उत्पादन, वाहतूक, वाट पाहणे, इन्व्हेंटरी, अतिरिक्त हालचाली, अतिरिक्त प्रक्रिया आदी विविध गोष्टींचा समावेश होता. तसेच वीज, पाणी, गॅस, हवा आणि कच्चा मालदेखील मोठ्या प्रमाणावर वाया जात होता. या सर्व समस्यांवर उपाय शोधण्यासाठी आम्ही सर्वात प्रथम कोणकोणत्या प्रकारच्या अडचणींवर काम करावयाचे, ते निश्चित केले. त्यासाठी विशिष्ट कार्यगट तयार करून आवश्यक असलेली सर्व माहिती एकत्र केली. कंपनीत तयार होत असलेले एकूण उत्पादन आणि त्यासाठी लागणारी प्रक्रिया समजावून घेतली. लागणारे मटेरियल, फ्लो प्रोसेस, विविध विभाग, उपलब्ध असलेली जागा, एकूण मशिन आदी बाबींचा अभ्यास केला आणि टप्प्याटप्प्याने सुधारणा करण्यास सुरुवात केली.
बसण्याची व्यवस्था
सुरुवातीला आमच्याकडे कामगार बसून काम (चित्र क्र. 2) करीत असत. बसून काम केल्याने मशिनवर काम करताना जी सतर्कता (अॅलर्टनेस) हवी असते, त्यात कमतरता येत असल्याचे आढळून आले. त्यामुळे अपघातदेखील घडले होते. त्यामुळे आम्ही बसून काम करण्याऐवजी उभे राहून काम करण्याची पद्धत (चित्र क्र. 3) अंगिकारली. यामुळे अपघातांचे प्रमाण कमी होण्यासोबतच उत्पादाची गुणवत्ता वाढण्यास मदत झाली.
मशिन व्यवस्था आणि मटेरियल
कंपनीची सुरुवात झाल्यापासून ज्या ठिकाणी मोकळी जागा आहे त्या ठिकाणी येणार्या मशिन, कच्चा माल आदी ठेवले जात असे. त्यामुळे मशिन एका कोपर्यात असेल तर त्यासाठी लागणारा कच्चा माल दुसर्या कोपर्यात ठेवलेला असायचा. त्यात कच्चा माल मशिनपर्यंत नेण्यासाठी कोणत्याही प्रकारची व्यवस्था नव्हती. त्यामुळे कामगारांना मटेरियल खांद्यावर उचलून न्यावे लागायचे. कधी कधी मटेरियलची ने आण करण्यासाठी पॅलेट येईपर्यंत संबंधित कर्मचारी वाट पहात बसायचा. त्यामुळे कर्मचार्यांचा मोठ्या प्रमाणात वेळ वाया जायचा. मटेरियल मशिनवर वेळेत न पोहोचल्याने उत्पादनावर याचा परिणाम होत असे. तसेच कच्चा माल, प्रोसेसिंग, फिनिश आणि डिस्पॅच या क्रमाने सर्व मशिनचा नवा लेआऊट करण्याचे निश्चित केले. या बदलासाठी सर्व कर्मचार्यांची मनोभूमिका तयार करणे हे प्रमुख आव्हान आमच्यापुढे होते.
पहिल्या टप्प्यातील काही सुधारणा
अनेकवेळा लागणार्या आणि न लागणार्या वस्तू भिंतींना टेकवून ठेवल्या जायच्या. यामुळे भिंती तर खराब होतच होत्या, तसेच चालताना अडचणी येत असल्यामुळे अपघाताची शक्यता होती. यावर उपाय म्हणून सर्वप्रथम आम्ही 5 - एस तंत्र वापरून वापरात नसलेले, खराब, निरुपयोगी मटेरियल, यंत्रभाग, मशिन, प्रेस टूल, गेज आदी साधारण सहा लाख रुपयांचे मटेरियल भंगारात विकून टाकले. मटेरियल, वेळ, कष्ट आदी वाया जाणार्या गोष्टी टाळण्यासाठी ‘एव्हरीथिंग ऑन अ व्हील’ ही संकल्पना अंमलात आणली. कुठलीही वस्तू, उत्पाद जमिनीवर न ठेवता चाके असलेल्या ट्रॉली, पॅलेट अथवा टेबलवर ठेवण्यास सुरुवात केली. प्रत्येक मशिनजवळ आवश्यक असलेली टूल आणि प्रेस टूल रॅकवर ठेवली. तसेच नेहमी बसून काम करण्याच्या दृष्टीने डिझाइन केलेले पॉवर प्रेस फॅब्रिकेटेड स्टँडवर ठेवून उभ्यानेच प्रत्येक काम करता येईल असे बदल करून घेतले. यामुळे कामगारांची सुरक्षितता वाढण्याबरोबर जागेचा अपव्यय टाळता आला.
कामाची जुनी पद्धत आणि त्यातील बदल
कंपनीत आम्ही जुन्या पद्धतीनुसार काम करीत असताना कच्चा माल एका ठिकाणी ठेवायचो. (चित्र क्र. 4 मध्ये कंपनीतील मशिनचा जुना लेआउट दाखविला आहे.) त्यानंतर कार्यवस्तुच्या नियोजनानुसार मटेरियल वेगवेगळ्या मशिनवर पाठविले जायचे. या मटेरियलची वाहतूक करण्यासाठी कर्मचार्याचे कष्ट आणि वेळ दोन्ही मोठ्या प्रमाणात वाया जात होते. या पद्धतीनुसार काम करताना एका कामगाराला दिवसात साधारण 247.5 मीटर अंतर चालावे लागत असे. ज्यावेळी आम्ही कामाची पद्धत आणि मशिनचा लेआऊट (तक्ता क्र. 1) बदलली त्यावेळी असे लक्षात आले की, कंपनीत एकूण 934.6 मी. जागा उपलब्ध आहे आणि त्यातील कामासाठी आवश्यक असणारी जागा केवळ 447.3 मी. इतकीच आहे. म्हणजेच कंपनीत पुरेशी जागा उपलब्ध होती. मात्र, मशिन, कच्चा माल यासह इतर गोष्टींची रचना आणि मांडणी व्यवस्थित न केल्याने इतके दिवस आम्हाला उपलब्ध जागेचा योग्य वापर करता येत नव्हता. कच्चा माल आणि मशिन यांच्या चुकीच्या स्थानांमुळे कामगाराला दिवसात 247.5 मीटर इतके अंतर कापावे लागत होते.
माहिती जमा करणे
चालू असलेली प्रक्रिया शास्त्रीय पद्धतीने तपासण्यासाठी फ्लो चार्ट, स्ट्रिंग डायग्राम (चित्र क्र. 5) बरोबरच पुढील पद्धती वापरल्या.
- समस्या निश्चिती
- माहिती संकलन
- PQ उत्पादाच्या गुणवत्तेचे परीक्षण
- थ्रू पुट टाइम गँट (Gantt) चार्ट
- स्पेस रिलेशनशिप डायग्रॅम
कामाची नवीन पद्धत
माझ्यासह चैतन्य रासने, आदित्य खुटाळे, राकेश पवार या आमच्या चमूने नवीन पद्धतीच्या संशोधन आणि अंमलबजावणीची जबाबदारी घेतली होती. आम्ही ज्यावेळी कंपनीची एकूण जागा आणि वापरातील जागा यांचा अभ्यास केला त्यावेळी मशिन, कच्चा माल आदी विभागांचा लेआऊट हव्या त्या पद्धतीनुसार नसल्याचे लक्षात आले. यात सुधारणा करण्यासाठी आम्ही कार्यवस्तूवर करीत असलेल्या प्रक्रियेच्या क्रमानुसार विभागांची रचना (चित्र क्र. 6 आणि 7) करण्याचा निर्णय घेतला. यामुळे कर्मचार्याला दिवसाला कापावे लागणारे अंतर 247.5 मीटरवरून केवळ 90 मीटर इतके झाले. यामुळे झालेले इतर फायदे तक्ता क्र. 2 मध्ये दिले आहेत.
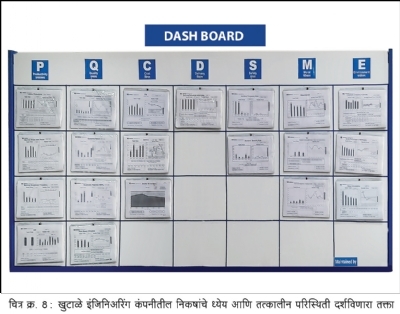
कंपनीत सुरुवातीला हवा गळती होण्याचे प्रमाण जास्त होते. त्यामुळे हवेसोबत वीजही मोठया प्रमाणात वाया जात होती. दरम्यान ग्रीन मॅन्युफॅक्चरिंगसाठी ‘सी.आय.आय’ ‘ग्रीनको’ रेटिंग (ही एक कंपन्यांचे पर्यावरण सजगतेच्या निकषांवर नामांकन करणारे रेटिंग आहे.) आम्हाला रेसिप्रोकेटिंग कॉम्प्रेसरऐवजी स्क्रू कॉम्प्रेसर बसविला तर वाया जाणार्या विजेची बचत करता येऊ शकते याबाबत मार्गदर्शन मिळाले. त्यानंतर विजेची प्रति दिवस 25 युनिटची बचत होण्यास सुरुवात झाली. म्हणजेच 250 रुपयांची प्रति दिवस बचत होऊ लागली. विजेची बचत व्हावी या उद्देशाने आमच्या कंपनीत सुरुवातीपासूनच शॉप फ्लोअरवर नैसर्गिक प्रकाश येईल अशा प्रकारची सोय करण्यात आली आहे. तसेच रूफ व्हेंटिलेटरदेखील बसविण्यात आले आहेत. वीज, पाणी आणि रॉ मटेरियल वाचविण्यासाठी विविध उपाय राबविले आहेत.
या आणि अशा अनेक सुधारणा आमच्या कंपनीमध्ये सातत्याने सुरू असण्याचे कारण म्हणजे सर्व कर्मचार्यांना कंपनी कामकाजामध्ये सहभागी करून घेणारी आमची कार्यसंस्कृती! औपचारिक सहभागासाठी आम्ही कामाच्या संदर्भातील सर्व निकषांचे ध्येय आणि तत्कालीन परिस्थिती दर्शविणारे तक्ते (चित्र क्र. 8) शॉप फ्लोअरवर लावून त्यावर चर्चा घडवून आणतो, तर अनौपचारिक सहभागासाठी विविध सण साजरे करण्याबरोबरच कर्मचार्यांनी आणि कुटुंबियांनी मिळविलेल्या यशाचे सार्वजनिक कौतुक करतो. यामुळे मनोबल वाढते. त्यासाठी वेगवेगळ्या ‘दिवसांचे’ आयोजन केले जाते. अशा सर्वांच्या सहभागाने केलेल्या संपूर्ण कारखान्याचे स्वरूप पालटणार्या सुधारणेचे आम्ही IMTMA ने 2019 मध्ये आयोजित उत्पादकता परिषदेमध्ये सादरीकरण केले होते. त्यासाठी आम्हाला लघु, मध्यम उद्योग गटामध्ये उत्कृष्ट सादरीकरणाचे प्रथम पारितोषिक मिळाले होते. हा आमच्या कार्यसंस्कृतीचाच गौरव आहे असे मी मानतो. गोदरेज अँड बॉइज सारखा उत्तम ग्राहक आणि CII च्या विविध क्लस्टरमधून लाभलेले मार्गदर्शन यांच्यामुळे कंपनीमध्ये आदर्श कार्यसंस्कृति रुजविण्यास आणि ती अधिक स्पर्धात्मक बनविण्यास मोठा हातभार लाभला आहे.
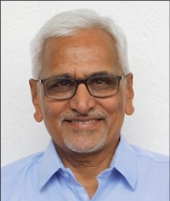
शिरीष खुटाळे
अध्यक्ष आणि व्यवस्थापकीय संचालक,
खुटाळे इंजिनिअरिंग प्रा. लि.
9822032220
शिरीष खुटाळे यांत्रिकी अभियंते असून, खुटाळे इंजिनिअरिंग प्रा. लि. कंपनीचे ते अध्यक्ष आणि व्यवस्थापकीय संचालक आहेत. त्यांना उत्पादन क्षेत्रातील कामाचा प्रदीर्घ अनुभव आहे.