अडॅप्टर इंजेक्टरचे (Adaptor injector) यंत्रण करण्यासाठी लुनार एंटरप्रायजेस कंपनीने केलेल्या सुधारणेबद्दल उदाहरणासह भाष्य करणारा लेख.
आमच्या लुनार एंटरप्रायजेस या कंपनीमध्ये आम्ही प्रामुख्याने रबर होजसाठी लागणारी हायड्रॉलिक फिटिंग तयार करीत होतो. साधारण 2000 च्या सुमारास उद्योगक्षेत्रातील सर्वजण मॅन्युअल मशिनकडून सी.एन.सी.कडे वळत होते. त्यावेळी आमच्या एका जुन्या ग्राहकाला अशी विनंती केली होती की, त्यांच्याकडचे इतर काही आव्हानात्मक भाग यंत्रणासाठी आम्हाला द्यावेत. तेव्हा 2002-03 मध्ये अॅडॅप्टर इंजेक्टर (चित्र क्र. 1) हा यंत्रभाग आमच्याकडे यंत्रणासाठी आला. हा भाग इंजिनातील इंधन (फ्युएल) यंत्रणेचा एक भाग होता.
अॅडॅप्टर इंजेक्टर हा यंत्रभाग सुमारे 280 ग्रॅम वजनाचा असून त्याचे बाह्य मोजमाप ø40 मिमी. X 96 मिमी. लांबी असे होते. त्याच्या वरच्या फेसचा सपाटपणा 0.0003" तर पृष्ठीय फिनिश 0.4 Ra अपेक्षित होता. यातील फेसवरील छिद्रांचे तसेच कोनात असलेले छिद्र आणि टॅपिंग केलेल्या छिद्राचे स्थान अचूक राखणे आवश्यक होते.
आमच्याकडे काम येण्यापूर्वी ग्राहकाकडे अॅडॅप्टर इंजेक्टरच्या यंत्रणाची प्रक्रिया वेगळी होती. एखाद्या थ्रेड रिंग गेजप्रमाणे या अॅडॅप्टरचे आटे ग्राइंडिंग प्रक्रियेद्वारे केले जात होते. या अॅडॅप्टरचे आटे ग्राइंड करण्यासारखे त्यात एवढे काय असेल याचा आम्ही विचार करीत होतो. या आट्यांचा अक्ष त्यांच्या खाली असलेल्या रिंगचा फेस आणि वरच्या फेसला काटकोनात असणे गरजेचे असते. जुन्या पद्धतीमध्ये पारंपरिक लेथ मशीनवर आटे तयार होत असल्याने त्यात अपेक्षित अचूकता मिळत नव्हती. त्यामुळे त्यांना ग्राइंडिंग करण्याची गरज तयार झाली असावी असे लक्षात आले. आट्यांचे ग्राइंडिंग करून जी अचूकता मिळते ती गेजची अचूकता, या भागासाठी गरजेची नव्हती. आम्ही ग्राहकाला आट्यांचे ग्राइंडिंग न करता ते यंत्रण सी.एन.सी.वर करण्याचे सुचविले. त्यांना अपेक्षित असलेली अचूकता यावरदेखील मिळेल, असा विश्वास आम्ही दिला. आम्ही हे आव्हान स्वीकारले. ग्राहकाला दिलेला विश्वास सार्थ ठरविण्यासाठी आम्ही प्रगति ऑटोमेशनच्या अशोक साठे यांच्याकडे गेलो आणि त्यांच्याशी याबाबत सविस्तर चर्चा केली. आम्हाला या भागाचे सर्व यंत्रण सी.एन.सी.वर करावयाचे आहे, असे त्यांना सांगितले.
त्या यंत्रभागाची मोजमापे अत्यंत काटेकोर मिळविणे आवश्यक होते. कोणत्याही प्रक्रियेमध्ये जेव्हा मॅन्युअल आणि तुकड्या तुकड्यांमध्ये (स्प्लिट) काम केले जाते तेव्हा, प्रत्येक ऑपरेशनची अचूकता मिळविणे महत्त्वाचे आणि गरजेचे असते. त्यात फरक पडू शकतो. त्यामुळे या भागाची अपेक्षित अचूकता लक्षात घेता आम्ही सर्व ऑपरेशन कमीतकमी सेटअपमध्ये (चित्र क्र. 2) करण्याचे ठरविले. त्यामुळे आम्ही सी.एन.सी. टूल्ड अप मशीनची निवड केली. 'एस डिझाइनर्स'ला आम्ही सांगितले की, या यंत्रभागाला जेवढी छिद्रे आहेत ती सर्व कमीतकमी सेटअपमध्ये झाली पाहिजेत. त्याप्रमाणे त्यांनी आम्हाला फिक्श्चर (चित्र क्र. 3) डिझाइन करून दिली. सर्व चर्चेनंतर 'एस' कंपनीकडून आम्ही टूल्ड अप मशीन विकत घेतली.
आम्ही ग्राहकाला सी.एन.सी.वर थ्रेडिंग करून दिले ज्याची अचूकता त्यांच्या अपेक्षेप्रमाणे होती. त्यामुळे संपूर्ण थ्रेड ग्राइंडिंग ऑपरेशन यामधून वगळता आले. ग्राहकदेखील या यंत्रणावर खूश आहे. आजही आम्ही त्यांना प्रति महिना 8 ते 10 हजार अॅडॅप्टर इंजेक्टरचा पुरवठा करीत आहोत.
दुसरी सुधारणा म्हणजे, ग्राहकाकडे या अॅडॅप्टरचा पृष्ठभाग (फेस) अँग्युलर व्हील हेड ग्राइंडरवर ग्राइंड केला जात होता. पूर्वीच्या पद्धतीमध्ये अॅडॅप्टर टरेट लेथवर तयार होत होता. त्यामुळे त्याचा पृष्ठीय (सरफेस) फिनिश सुरुवातीला फार खराब असायचा. त्यावरील टूलचे चरे लॅपिंगआधी काढून अपेक्षित फिनिश मिळविण्यासाठी ग्राइंडिंगची गरज होती. पण आम्हाला असे लक्षात आले की नवीन पद्धतीमध्ये यंत्रण केल्यावर तिथेच चांगला फिनिश मिळतो आहे. त्यामुळे त्याचे फिनिशिंग करण्यासाठी अँग्युलर व्हील हेड ग्राइंडरची काहीही आवश्यकता राहिली नाही. त्यामुळे तो पृष्ठभाग थेट लॅपिंग मशिनवर आम्ही लॅपिंग प्रक्रियेद्वारे करण्याचे ठरविले. त्यासाठी आम्ही लॅपिंग मशिन विकत घेतली आणि त्याच्या ट्रायल घेतल्या. लॅपिंग प्रक्रियेद्वारे अपेक्षित फिनिश मिळत असल्याचे आमच्या निदर्शनास आले. त्यामुळे आम्ही ग्राइंडिंग ऑपरेशन पूर्णतः वगळले. असे अनेक बदल आम्ही आमच्या प्रक्रियेमध्ये केले.
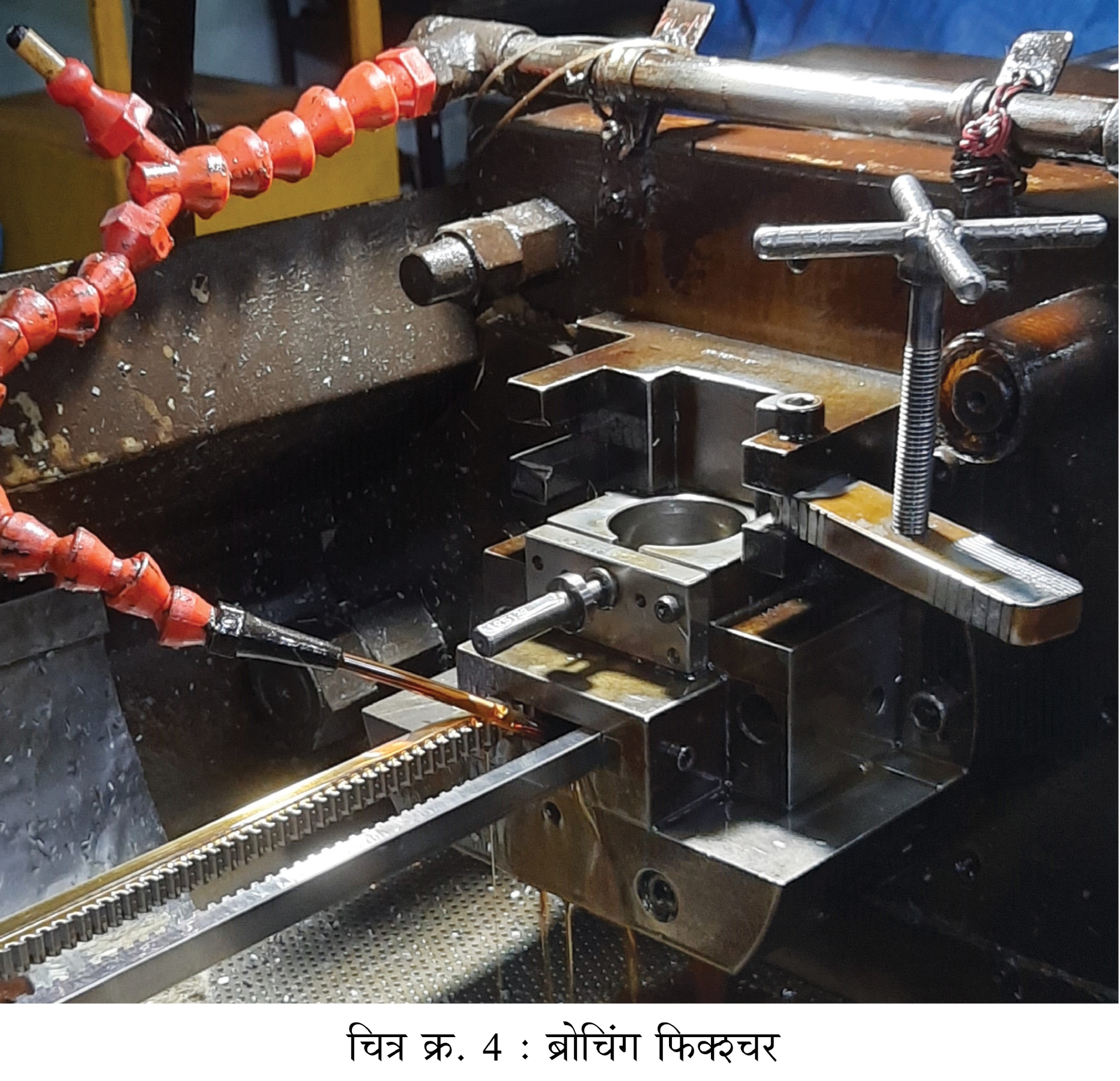
या अॅडॅप्टर इंजेक्टरला स्पॅनर बसविण्याकरिता एक खाच (स्लॉट) आहे. दंडगोलाकार अॅडॅप्टरवर एका एंडला समोरासमोर दोन खाचा आहेत. त्यामुळे 180 अंशामध्ये इंडेक्सिंग मिलिंग करावे लागत असे. हे करताना असा विचार केला की ही खाच आपण सरफेस ब्रोचिंग करूनही तयार करू शकतो. त्यासाठी आम्ही फिक्श्चर (चित्र क्र. 4) डिझाइन करून हायड्रॉलिक ब्रोचिंग मशीनवर दोन ब्रोच वापरून काम करायचे ठरविले. हे काम फिक्श्चरवर करीत असल्याने तसेच ब्रोचिंगमध्ये प्रतिदंत अतिशय कमी मटेरियल निघत असल्यामुळे यंत्रभाग बरमुक्त होतो आणि फिनिश अधिक चांगला (चित्र क्र. 5) मिळतानाच जलदही होतो. प्रक्रियेत बदल केल्यामुळे यंत्रण आणि डीबरिंग कामासाठी लागणाऱ्या वेळेत प्रति अॅडॅप्टर सुमारे 2.5 मिनिटांची बचत झाली.
आमच्यासाठी ती एक उत्कृष्ट बाब होती आणि ग्राहकालादेखील खूप चांगले, विश्वासार्ह उत्पाद मिळू लागल्यामुळे तेदेखील समाधानी होते.
लघु, मध्यम उद्योगांमध्ये प्रक्रियेचा वेळ कमीतकमी कसा ठेवता येईल हे अधिक महत्त्वाचे असते. कच्च्या मालाच्या मागणीपासून ते भाग विक्रीला जाईपर्यंतच्या प्रक्रियेचा वेळ जितका कमी तेवढा फायदा अधिक होतो. त्यामुळे मनुष्यबळ, जागा, चलन असे सर्वच वाचते.