सर्व अभियांत्रिकी उद्योगांमध्ये, अंतिम उत्पादनाची गुणवत्ता सुयोग्य राखण्याच्या दृष्टीने, निरनिराळ्या टप्प्यांवर आपण वापरत असलेल्या मटेरियलची भौतिक गुणवत्ता तपासणे अनिवार्य ठरते. बहुसंख्य प्रकारचे धातू आणि मिश्रधातू वाहन उद्योगापासून हेवी इंजिनिअरिंगमधील विविध उत्पादनांमध्ये वापरले जातात. या उत्पादनांमध्ये नवनवीन सुधारणा होत असताना मूलतः जास्तीतजास्त दाब आणि जास्तीतजास्त ताण यांचा सामना करताना कार्यकाळ, झीज, मोडतोड इत्यादी बाबींमध्ये धातू कसा प्रतिसाद देईल यासाठी मूळ धातूंचे टेन्साइल स्ट्रेंग्थ, कॉम्प्रेसिव्ह स्ट्रेंग्थ, शिअर स्ट्रेंग्थ हे गुणधर्म महत्त्वाचे असतात. उत्पादन प्रक्रियेमध्ये वेगवेगळ्या टप्प्यांवर उदाहरणार्थ, मटेरियल आल्यापासून ते उष्णतोपचारानंतर (हीट ट्रीटमेंट) निरनिराळ्या प्रक्रियांच्या शेवटी इतकेच नव्हे तर संशोधन आणि विकासाच्या निरनिराळ्या प्रयोगांदरम्यान, अशा सर्व ठिकाणी हे गुणधर्म तपासून घेणे अत्यावश्यक ठरते. ही तपासणी करण्यासाठी युनिव्हर्सल टेस्टिंग मशिन नावाचे उपकरण वापरले जाते.
आमची ‘फाय’ (FIE) कंपनी जवळपास 50 वर्षांपासून मटेरियल टेस्टिंग मशिनच्या क्षेत्रात कार्यरत आहे. भारतामध्ये सर्वप्रथम आम्ही मटेरियलच्या चाचणीसाठी (टेस्टिंग) लागणारी डिस्ट्रक्टिव्ह टेस्टिंग मशिन विकसित केली. त्यामध्ये युनिव्हर्सल टेस्टिंग मशिन, हार्डनेस टेस्टर, इम्पॅक्ट टेस्टर, बॅलन्सिंग मशिन अशी मशिन विकसित केली आहेत. भारतातील अग्रगण्य अशा नॅशनल फिजिकल लॅबोरेटरीमधील (एन.पी.एल.) चाचण्यांसाठी लागणारा सर्व सेटअप ‘फाय’ने दिला आहे.
युनिव्हर्सल टेस्टिंग मशिनपासून आमची मशिन बनविण्याची सुरुवात झाली. त्यानंतर साधारणपणे 50 वर्षांपूर्वी पहिल्यांदा भारतात आम्ही हार्डनेस टेस्टर बनविले. त्यानंतर इम्पॅक्ट टेस्टिंग, चेन आणि रोप टेस्टिंग, बॅलन्सिंग मशिन, टॉर्शन टेस्टिंग, फटिग टेस्टिंग, ड्रॉपवेट टेस्टिंग अशा वेगवेगळ्या चाचण्यांच्या क्षेत्रामध्ये आम्ही अद्ययावत मशिन पुरवित आहोत.
गुणवत्तेमध्ये आम्ही कधीच तडजोड करीत नाही. मशिन विकसित करताना अमेरिकेतील मशिन आणि भारतात बनविलेले मशिन एकसारखे असले पाहिजे, असा आमचा प्रयत्न आहे आणि त्यानुसार आम्ही कामाची आखणी करीत गेलो. त्यासाठी गुणवत्ता नियम सुधारले.
मटेरियल चांगले असावे यासाठी त्याची फेरतपासणी कशी करायची, इंजिनिअरिंग टॉलरन्स कुठे पाळावे लागणार आहेत, प्रक्रिया कुठे बदलायला लागणार आहे. त्यासाठी कोणती मशिन लागणार आहेत, त्याची किंमत किती आहे, ती सुविधा दुसरीकडे कुठे उपलब्ध आहे का? या गोष्टी आम्ही तपासत गेलो. उदाहरणार्थ, दर्जेदार कास्टिंगची आमची प्रक्रिया वेगळी आहे. आम्ही फ्युरॉन मोल्डिंग पद्धतीने कास्टिंग करतो. साच्यामध्ये नोबेक सँड ही रेझिनयुक्त वाळू असते, ती प्रक्रियेदरम्यान स्वतःच कठीण (हार्ड) होते. त्यामुळे मोजमाप आणि कास्टिंगची गुणवत्ता चांगली मिळते. त्याला लागणारा वेळ कमी कसा करायचा, यावर आम्ही विचार करून फक्त कास्टिंगचीच नव्हे तर टेस्टिंगची एकूण कार्यपद्धती बदलली. कठोर परिश्रम करून, उत्पाद विकसित करून ते मोठ्या संख्येमध्ये विकण्यात आम्हाला यश आले. अर्जेंटिना, स्विर्त्झलँड अशा देशांमध्ये आज आम्ही मशिन निर्यात करतो. भारतातही आमची मोठी बाजारपेठ आहे.
मेकॅनिकल, सॉफ्टवेअर आणि इलेक्ट्रॉनिक्सचा विकास
टेस्टिंग मशिन नेहमीच अचूक, विेशासार्ह आणि देखभालीसाठी सुलभ असावे असा आमचा दृष्टिकोन असतो. ऑपरेटरला चिन्हांद्वारे निरनिराळे पर्याय कळायला हवेत. त्याला निवड प्रक्रियेमध्ये कुठल्याही अडचणी यायला नकोत. कुठल्याही क्षणी काहीही खराब झाले तरी ते काढून दुसरे लावण्यासाठी आम्ही त्याचे प्रमाणीकरण (स्टँडर्डायजेशन) केलेले आहे. खराब सर्किट बोर्डमुळे मशिन बंद राहिल्यास अशावेळी डीलरकडे असलेले दुसरे कार्ड बदलून मशिन पुन्हा सुरू करता येते. तिथे चूक कोणाची आहे ही दुय्यम बाब आहे. पहिल्यांदा मशिन सुरू होणे गरजेचे आहे. आमच्या 12 प्रकारच्या मशिनसाठी एकाच प्रकारचा सर्किट बोर्ड असून तो 12 वेगवेगळ्या कॉन्फिगरेशन हाताळण्यास सक्षम आहे.
ग्राहकांना चांगले उपाय (सोल्युशन) आणि स्वयंचलित दोषमुक्त यंत्रणा विकसित करून, आधुनिकीकरण, प्रमाणीकरणाचे फायदे देतानाच ते मशिन दिसायलाही चांगले असले पाहिजे याची आम्ही काळजी घेतो. ग्राहकाला त्याचे रीडिंग योग्यच दिसले पाहिजे. ते प्रणालीमधून त्यांच्या अहवालाच्या (रिपोर्ट) पद्धतीत अपेक्षित स्वरूपात जायला पाहिजे. यासाठी मशिनमधील सॉफ्टवेअर आणि इलेक्ट्रॉनिक भाग, बेसिक अल्गोरिदम, मॅथेमॅटिक्स आणि मोजमापनाची सूत्रे आम्ही आमच्याकडेच विकसित करीत आहोत. उदाहरणार्थ, कॅमेऱ्यामधून गोल निशाणी (राउंड इंडेन्टेशन) चित्रित करून ती प्रतिमा प्रणालीमध्ये डीकोड केली जाते. समजा एखाद्या प्रतिमेचे दोनच पॉइंट घेतले तर व्यास चुकण्याची शक्यता जास्त असते. पण मानकानुसार चार पॉइंट गरजेचे असले तरी आम्ही 1000 पॉइंट घेतो. त्यामुळे अर्थात अचूकता वाढते. आम्ही अशाच पद्धतीचे तीन वेगवेगळे अल्गोरिदम तयार केले. प्रतिमा (इमेज) कशी येते आहे त्या पद्धतीने कोणता अग्लोरिदम निवडायचा हेही त्या सॉफ्टवेअरमध्येच ठरविता येते. एक वर्ष सातत्याने चाचण्या घेतल्यानंतरच ते सॉफ्टवेअर उत्पादनप्रक्रियेमध्ये अंतर्भूत केले.
टेस्टिंग मशिनमधील स्वयंचलन :
हार्डनेस टेस्टर
टेस्टिंग मशिनमध्ये कंपनीतील जुने कामगार त्यांचा अनुभव, काम यादृष्टीने कधीही उजवे ठरतात. तेच काम नवीन कामगार लगेच करू शकत नाहीत. त्यामुळे कामात चुका होण्याची शक्यता जास्त असते. लोकांनी नोकऱ्या बदलल्यामुळे, तसेच बदलत्या मागणीनुसार कर्मचार्यांमध्येही बदल करावा लागतो. अशावेळी कुशल कामगार मिळणे ही मोठी समस्या आहे. उदाहरणार्थ, हार्डनेस टेस्टरमध्ये हार्डनेस नंबर मिळविण्यासाठी यंत्रण झालेला किंवा हार्डनिंग झालेला यंत्रभाग मशिनवर ठेवला जातो. त्यावर हँड व्हील हळू फिरवून इंडेन्टरचा यंत्रभागाला स्पर्श करायचा. जोपर्यंत त्याला 10 किग्रॅ. लोड जात नाही, तोपर्यंत तो हळू फिरवत जायचा आणि त्यानंतर स्केल निवडायची अशी प्रक्रिया आहे. HR-A, HR-B, HR-C स्केल निवडल्यानंतर त्या स्केलला पाहिजे तो लोड निवडायचा आणि लोडिंग द्यायचे. म्हणजेच स्केल निवड आणि लोड निवड हे दोन निकष पूर्ण झाल्यानंतर आणि प्रीलोड दिल्यानंतर मुख्य लोड कार्यान्वित होतो. मुख्य लोड पडून त्याचा असलेला ड्वेल टाइम झाल्याशिवाय कार्यवस्तू अनलोड करता येत नाही. अन्यथा त्याचे रीडिंग चुकते. ही काहीशी क्लिष्ट आणि मोठी प्रक्रिया नवीन कामगार आत्मसात करेल का? आणि जरी त्याने ती केली तरी त्यामध्ये चुकांचे प्रमाण जास्त असू शकते. एक पॅरामीटर जरी बदलला तर त्याच्यापुढील पॅरामीटरमुळे चुकांची विविध परम्युटेशन, कॉम्बिनेशन तयार होतात. या परिस्थितीमध्ये बदल करण्यासाठी आमच्या कंपनीतील काही सदस्यांनी सुचविल्याप्रमाणे आम्ही त्याचे स्वयंचलन करून सर्व सेटिंग अँड्रॉइड फोनप्रमाणे असावीत असे ठरविले. यामध्ये चिन्हे (सिम्बॉल) असतील आणि त्या चिन्हांना स्पर्श करत जाणे आणि हो किंवा नाही एवढेच कामगाराने निवडावे असे स्वयंचलन करण्याचे ठरविले. त्यातील उर्वरित गोष्टींची काळजी मशिन घेतेच. हे मशिन आम्ही 2017 मध्ये विकसित केले. त्याची किंमत जास्त होती तरीही आम्ही ते मशिन सादर केले. त्याचवर्षी 50 पेक्षा जास्त मशिन विकण्यास आम्हाला यश आले. त्यानंतर ग्राहक स्वयंचलित मशिनची मागणी करू लागले. स्मार्टफोन आणि ॲपच्या वातावरणात काम करणे कामगारांसाठी अधिक सोपे होते. त्यासाठी आम्ही ते उत्पादन वाढविले आणि आम्हाला यशही मिळाले.
ब्रिनेल हार्डनेस टेस्टिंग मशिन
हे मशिन पूर्णपणे स्वयंचलित आहे. त्यामध्ये पूर्ण कॅमेरा आधारित प्रणाली आहे. आधी ब्रिनेल नंबर मोजताना मायक्रोमीटर स्लाइड फिरविली जायची. त्यानंतर मायक्रोमीटरचा लीस्ट काउंट काढून रीडिंग तयार होऊन ते रीडिंग तक्त्यातून नंबरमध्ये रूपांतरित करायचे, अशी प्रक्रिया होती. आम्ही या प्रक्रियेला स्वयंचलित पर्याय तयार केला. यामध्ये टेबलवर कार्यवस्तू ठेवल्यावर इंडेन्टर स्पिंडलमार्फत खाली येऊन कार्यवस्तूवर आपली निशाणी (इंडेन्टेशन) तयार करतो. त्यानंतर मशिनमधील कॅमेरा त्या निशाणीचे फोटो घेऊन सॉफ्टवेअरकडे पाठवितो. आम्ही तयार केलेल्या अल्गोरिदमचा वापर करून त्या निशाणीची तपासणी होते आणि किती हार्डनेस आहे ते समजते. चांगली निशाणी मिळविण्यासाठी काही केसमध्ये स्पॉट फेसिंग करावे लागते. या स्वयंचलित प्रक्रियेमध्ये ग्राहक किंवा ऑपरेटर 3 ते 4 पर्याय निवडून काम करू शकतात. बाकी सर्व काम मशिन करते. यामध्ये आवश्यक लोडच्या 1 टक्क्यामध्ये अचूकता आवश्यक असते. आमच्या मशिनमध्ये ती 0.5 टक्क्यापर्यंत मिळते. कारण आम्ही यांत्रिकी व्यवस्था वापरून सर्व्हो मोटरसह क्लोज लूप प्रणाली वापरली आहे.
ब्रिनेल हार्डनेस तपासणीसाठी आणखी एक मॉडेल विकसित केले ते म्हणजे इनलाइन ब्रिनेल हार्डनेस टेस्टिंग मशिन. मोठमोठ्या यंत्रभागांच्या हाताळणीसाठी त्याला कन्व्हेअर बसविला आहे. यंत्रभाग लोड करून आवर्तन सुरू केले की, कन्व्हेअरवरून कार्यवस्तू अपेक्षित स्थानावर जाते. त्यावर दिलेल्या भारामुळे निशाणी तयार होते. कॅमेऱ्यामार्फत तिचे मोजमाप होऊन संगणकाला माहिती पुरविली जाते आणि स्क्रीनवर हार्डनेस मूल्य मिळते. यामध्ये दुसरी सुधारणा अशी केली ती म्हणजे, यंत्रभाग ठेवल्यानंतर सायकल स्टार्टचे बटण दाबले की स्वयंचलितपणे यंत्रभागावर लोडिंग होते. त्यानंतर निशाणी घेऊन टचस्क्रीनवर त्याचे ब्रिनेल हार्डनेस मूल्य कळते.
यंत्रभाग जर 5 टन असेल, तर तो एवढ्याशा C फ्रेममध्ये मावणार नाही. त्यावर विचारविनिमय करून आम्ही एवढा मोठा यंत्रभाग वर नेण्यापेक्षा इंडेन्टर असलेले हेड खाली आणण्याचे ठरविले. त्यासाठी एक टेबल तयार केले, त्यावर यंत्रभाग ठेवला तर हेड खाली येतो. त्यासाठी आम्ही व्ही.एम.सी. संकल्पनेनुसार प्रणाली विकसित केली. (व्ही.एम.सी.मध्ये दिलेल्या प्रोग्रॅमप्रमाणे हेड खाली येते, टेबल हलते, यंत्रण होते आणि हेड पुन्हा वर जाते. हे हाताने किंवा बटणाने करणे शक्य होते.) आमच्याकडे फक्त कटरऐवजी इंडेन्टर आहे. ब्रिन्मॅक्स मशिनवर चाचणी सुरू असतानाचा व्हिडिओ पाहण्यासाठी शेजारी दिलेला QR कोड मोबाइलवर स्कॅन करा.
रॉकवेल कम ब्रिनेल हार्डनेस टेस्टिंगसाठी लागणाऱ्या ऑप्टिकल ट्यूबही आम्ही विकसित केल्या. ब्रिनेलचे घेतलेले इम्प्रेशन थेट मोजता येत नाही. त्यामुळे ऑप्टिक्स यंत्रणा वापरून व्यास मोजून त्याचा हार्डनेस कसा मोजायचा याचा तक्ता तयार केला. त्यानंतर 10, 15, 30, 45 अशा छोट्या लोडच्या स्केलही आम्ही यामध्ये अंतर्भूत केलेल्या आहेत. इलेक्ट्रॉनिक मायक्रो कंट्रोलरवरती एल.सी.डी. डिस्प्लेसह छोटे कार्ड दिले आहे. एल.सी.डी. डिस्प्लेबरोबरच आम्ही संगणकीय सॉफ्टवेअरही विकसित केले. त्यामुळे टिपलेली प्रतिमा संगणकाकडे पाठविली जाते आणि त्यावर प्रक्रिया होते. त्यातून वेगवेगळे आलेखही काढता येतात आणि प्रिंट काढता येते.
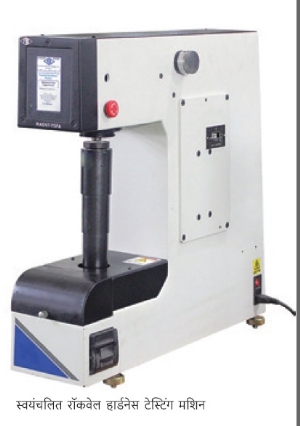
याच्या पुढची सुधारणा टचस्क्रीन मॉडेल वापरून माहितीची नोंद करणे. मशिनच्या यांत्रिकी आणि मूलभूत गोष्टी तशाच ठेवून केवळ इलेक्ट्रॉनिक्स प्रणाली बदलत गेली. हार्डनेस मूल्य थेट डिस्प्ले व्हायला लागले. त्याबरोबर आम्ही एक थर्मल प्रिंटर इंटरफेस केले, ज्यामुळे तपासणी झाल्यानंतर थेट प्रिंट मिळतो. यातील पुढची सुधारणा म्हणजे पूर्ण तपासणी प्रक्रिया पूर्णपणे स्वयंचलित करणे. मशिनमध्ये एक यंत्रभाग ठेवायचा. आवर्तन सुरू करावयाचे बटण दाबले की लोडिंग, प्रीलोडिंग, मुख्य लोडिंग, रिझल्ट आणि प्रिंट अशी पूर्ण स्वयंचलित प्रक्रिया या मशिनमध्ये होते. यात मनुष्यामुळे होणाऱ्या सर्व संभाव्य चुका टाळल्या जातात. यंत्रणेकडूनही आवश्यक विचारणा करून इंडेन्टर संदर्भातील गफलती दुरुस्त केल्या जातात. उदाहरणार्थ, बॉल इंडेन्टर ब्रिनेलला तर डायमंड इंडेन्टर रॉकवेलसाठी वापरला जातो. तो तक्ता आम्ही आधीच यंत्रणेमध्ये अंतर्भूत केलेला आहे. त्यामध्ये काही चूक असेल तर यंत्रणा वापरकर्त्याला सांगते. यंत्रणा स्केल आणि लोड बदलेल आणि त्यानुसार कोणता इंडेन्टर लावायचा हे सांगेल.
विकर्स हार्डनेस टेस्टिंग मशिन
विकर्स हार्डनेस टेस्टिंगमध्ये 50 किलोपर्यंत लोड येतो आणि यंत्रभागावर लोडमुळे निर्माण झालेली निशाणी मोजली जाते. यासाठी त्यामध्ये ऑप्टिकल स्क्रीन असायची. त्या स्क्रीनमध्ये प्रतिमेचा कर्ण (डायगोनल) मोजून, तक्त्यामधून त्याचा हार्डनेस किती आहे, हे ठरविले जायचे. यामध्ये आम्ही कॅमेरा वापरून संगणकीय सॉफ्टवेअर टाकले. जी प्रतिमा येते, ती आम्ही संगणकावर बघायला लागलो. संगणकामधून स्वयंचलितपणे निशाणी मोजून हार्डनेस मूल्य मिळायला लागले. आलेखामधील फरक, वारंवारितेचे वितरण आलेख, वेगवेगळ्या प्रकारचे अहवाल, नमुन्याच्या डेटा एन्ट्रीची सोय या सगळ्या गोष्टी आम्ही सॉफ्टवेअरमध्ये देत गेलो.
त्याच्या पुढचे मॉडेल म्हणजे टचस्क्रीन. यात अंगभूत संगणक (इनबिल्ट पीसी) लावला आणि कॅमेऱ्याचे इनपुट त्याला दिले. यु.एस.बी. कॅमेरा संगणकाला जोडून प्रतिमा थेट मिळू लागली. यामध्ये वेगवेगळे अहवाल, सर्व्हरला माहिती देण्याची सोय, डेटाबेसमध्ये माहिती साठविणे, या सर्व गोष्टी टचस्क्रीन वापरून करता येतात.
ग्राहकाच्या गरजेनुसार या सुधारणा आम्ही करीत गेलो. यामध्ये एखाद्या ग्राहकाला वेगळे मॉडिफिकेशन पाहिजे असेल, तर ते आम्ही करून देतो. जनरल सॉफ्टवेअर सगळ्यांना सारखे असते.
युनिव्हर्सल टेस्टिंग मशिन (यु.टी.एम.)
इलेक्ट्रोमेकॅनिकल युनिव्हर्सल टेस्टिंग मशिनमध्ये 100 किलोपासून 10 टनापर्यंत हायड्रॉलिक, नॉनहायड्रॉलिक, सर्व्हो चालित मशिन आम्ही तयार करतो. यु.टी.एम.मध्येही अगदी 10 टनापासून 200 टनापर्यंत वेगवेगळ्या क्षमता असलेली मशिन विकसित केली आहेत. मेकॅनिकल प्रणाली मुख्यत: टेस्टिंगचे लोडिंग करण्यासाठी आहे. टेस्टिंग चालू असते त्यावेळी हालचाल आणि लोडचे मूल्य या दोन्ही गोष्टी मोजण्यासाठी इलेक्ट्रॉनिक्स प्रणाली विकसित केली. लोडचे आणि विस्थापनाचे (डिस्प्लेसमेंट) मूल्य मोजण्यासाठी आम्ही संवेदक (सेन्सर) वापरतो. रेकॉर्डिंग सिस्टिममध्ये आम्ही मेमरी चिप दिलेली आहे. चाचणीनंतर डॉटमॅट्रिक प्रिंटरद्वारे प्रिंट घेता येते. ऑनलाइनसाठी संगणक सॉफ्टवेअर विकसित केले आणि अहवाल द्यायला सुरुवात केली. टचस्क्रीन मॉडेलमध्ये ही सर्व वैशिष्ट्ये उपलब्ध आहेत. ग्राहकांना ऑनलाइन निकाल (रिझल्ट) पाहणे किंवा क्लाउडला माहिती साठविणे शक्य आहे.
या मशिनमध्ये पूर्वी यंत्रभाग वरच्या बाजूने लोड व्हायचा. त्यावेळी यंत्रभाग व्यवस्थित पकडला गेला आहे की नाही हे कळत नव्हते. त्यासाठी आम्ही समोरून लोडिंग करता येईल अशी व्यवस्था केली. हायड्रॉलिक पकड असल्यामुळे खात्रीशीर पकड मिळते. याच मशिनला टचस्क्रीन, इलेक्ट्रॉनिक सिस्टिम लावता येते किंवा ॲनालॉग सिस्टिमही लावता येते.
यु.टी.एम मध्ये प्रूफ स्ट्रेस, मॉड्युलस मोजण्यासाठी कार्यवस्तू ओढली जात असताना ती किती लोडला किती लांबते आहे याचे निरीक्षण एक्स्टेन्सोमीटर हे उपकरण करीत असते. सामान्यपणे क्लिप ऑन प्रकारच्या मेकॅनिकल एक्स्टेन्सोमीटरला 2 मिमी. ते 10 मिमी. मर्यादा असते. पण कार्यवस्तू तुटेपर्यंत ते चालू राहिले तर एक्स्टेन्सोमीटर खराब होतो. यासाठी जर्मनीमध्ये व्हिडिओ एक्स्टेन्सोमीटरचा वापर केला जातो. कार्यवस्तूचे ताणले जाणे व्हिडिओमध्ये चित्रित करून त्या आधारे बाकीची निरीक्षणे नोंदविली जातात. परंतु, त्याच्या किंमती 13 ते 15 लाखांच्या घरात असतात. आम्ही त्यावर विचार करून आमच्याकडे उपलब्ध असलेल्या ज्ञान आणि अनुभवावर आधारित सॉफ्टवेअर विकसित करून व्हिडिओ एक्स्टेन्सोमीटर तयार केले. यालाच नॉन कॉन्टॅक्ट एक्स्टेन्सोमीटर म्हणता येईल. तो यंत्रभागावर न लावता मशिनच्या समोर ठेवला जातो आणि कॅमेऱ्यातून टिपलेली प्रतिमा टचस्क्रीनवर दिसते. त्या स्क्रीनवर मोजमाप, तसेच स्ट्रेस X स्ट्रेन आलेख ऑनलाइन मिळतो. एक्स्टेन्सोमीटर आणि मशिनदरम्यान प्रत्यक्ष संबंध नसल्यामुळे कार्यवस्तू तुटेपर्यंत ते प्रत्यक्ष घडणाऱ्या घडामोडींची नोंद केली जाते आणि अपेक्षित आलेखाच्या स्वरूपात अहवाल मिळू शकतो. पिनिअनला जॉ जोडलेला असल्यामुळे यंत्रभाग तुटल्यानंतर बॅकप्रेशरमुळे जॉ मूळ स्थानी परत येतात. यंत्रभाग बाहेर किंवा खाली पडणे या गोष्टी हायड्रॉलिक पकडीमुळे होत नाहीत.
यामध्ये आम्ही 100/500 किलो किंवा 1/5/10 टन सिंगल स्क्रू ड्रिव्हन आणि डबल स्क्रू ड्रिव्हन अशी दोन मॉडेल केली आहेत. या मशिन सर्व्हो चालित असल्यामुळे त्यात बॉल स्क्रू आणि लोडसेल वापरला आहे. त्यामुळे हायड्रॉलिक यंत्रणेपेक्षा यामध्ये अचूकता जास्त मिळते. यामध्ये वेगवेगळ्या प्रकारची फिक्श्चर विकसित केली आहेत. टेन्साइल, कॉम्प्रेशन, बेंडिंग या टेस्टिंगसाठी अशी मशिन घेऊ शकतो. प्लास्टिक, पेपर यांच्या चाचणीलाही हे मशिन चालते. तसेच या मशिनवर आवर्ती भार वापरून चाचणी करणेही शक्य आहे.
बॅलन्सिंग मशिन
जे फिरणारे (रोटेटिंग) यंत्रभाग असतात, ते संतुलित करावे लागतात. बॅलन्सिंग मशिनवर यंत्रभाग फिरविल्यावर त्यातील असंतुलितता मोजली जाते. अशावेळी यंत्रभागावर आवश्यक खुणा करून आणि बाहेर काढून तिथे किती ड्रिलिंग करायचे त्याचे गणित करून तेवढे मटेरियल काढले जाते. ही प्रक्रिया जास्त संख्येने होणाऱ्या उत्पादनासाठी योग्य नाही. म्हणून तो यंत्रभाग संतुलनाची प्रक्रिया पूर्ण होईपर्यंत मशिनवरून काढावा लागू नये, अशी यंत्रणा आम्ही विकसित केली. तसेच तो यंत्रभाग फिरल्यावर समजा 15० स्थानावर 50 ग्रॅमचे असंतुलन आले तर तो यंत्रभाग 15० स्वयंचलितपणे वरच्या बाजूला यायला पाहिजे. ते स्थान वरच्या बाजूला आल्यानंतर किती असंतुलित आहे, हे यंत्रणेमार्फत नक्की होऊन यंत्रभागावर ड्रिलिंग हेड स्वयंचलितपणे यायला पाहिजे. हे स्वयंचलन वाटताना सोपे वाटत असले तरी यातील अवघड भाग म्हणजे मोजले गेलेले असंतुलन अॅनालॉग वेव्ह स्वरूपात मिळणे. अचूकतेसाठी ते फिल्टर केल्यावर जो असंतुलितपणा असेल तो एका ड्रिलनेच जाईल असे नाही. त्यासाठी फेसला एक ड्रिल करून जर असंतुलितपणा गेला नाही तर किती भोके करावयाची याचे धोरण ठरवावे लागते. त्यासाठी त्या यंत्रणेची अचूकता सुधारावी लागली, जेणेकरून तो असंतुलितपणा अचूकपणे दूर करता येईल. ड्रिलिंग हेडने अचूकपणे त्याचे स्थान आणि खोली सेन्स करून, हे सगळे फीडबॅक घेऊन ती प्रणाली धोरण ठरविण्यास सक्षम आहे. यंत्रभाग संतुलित होत नाही तोपर्यंत ही प्रक्रिया सुरू राहते. एकदा धोरण ठरविल्यावर मशिन रात्रंदिवस चालू राहील. त्याच्या लोडिंग अनलोडिंग स्वयंचलनाचेही आमच्याकडे डिझाइन आहेत. त्यामुळे यंत्रभाग लोड केल्यानंतर तिथे कुठल्याही ऑपरेटरला थांबण्याची गरज नसते. याप्रकारे टेस्टिंग मशिनचे स्वयंचलन झाल्यामुळे कुठल्याही कारखान्यात चाचण्या घेणे अतिशय सोपे झाले आहे. यासाठी आमच्या एका ग्राहकाचे अनुभव पुढे दिले आहेत.
केस स्टडी
हातकणंगले येथील व्हॉल्व्ह वर्क्स इंडिया कंपनीचे रोहन वाडकर सांगतात की, “आमच्याकडे विविध प्रकारच्या व्हॉल्व्हचे उत्पादन होते. त्यासाठी बाहेरून येणाऱ्या विविध आकाराच्या आणि वजनाच्या फोर्जिंग केलेल्या व्हॉल्व्ह बॉडीच्या हार्डनेसची आम्ही ब्रिनेल हार्डनेस नंबर तपासून खात्री करून घेतो. पूर्वी हार्डनेस तपासण्यासाठी वापरीत असलेले मशिन मॅन्युअली चालवावे लागत होते, त्यामुळे मोजमापनामध्ये आणि अहवालांमध्ये अनेक चुका असायच्या. तसेच चाचणी करताना दिलेला भार (लोड) आणि ड्वेल टाइम यात अचूकता नसायची. जुन्या मशिनच्या आकारावरही मर्यादा होत्या. आम्ही व्हॉल्व्ह तयार करीत असल्यामुळे मानवी चुकांमुळे होणारे यंत्रभागांचे रिजेक्शन आम्हाला परवडणारे नव्हते. त्यासाठी यंत्रभागांची हार्डनेस तपासणी, मोजमापन आणि निकाल आम्हाला अचूक आणि स्वयंचलित हवे होते. त्यासाठी आम्ही ‘फाय’चे ब्रिनेल हार्डनेस टेस्टिंग मशिन घेण्याचे ठरविले.
फायचे टेस्टिंग मशिन घेतल्यापासून अनेक कामातील मानवी हस्तक्षेप नगण्य झाला आहे. ब्रिनेल हार्डनेस टेस्टिंग मशिनची BHN अचूकता +/-3 टक्क्यांच्या मर्यादेत असून येणाऱ्या निशाणीचा व्यास +/-10 मायक्रॉनमध्ये मोजला जातो. तसेच मशिनची वजन पेलण्याची क्षमता आणि आकार जास्त आहे. सध्या आमच्याकडे 900 X 900 X 1200 मिमी. लांबीचा यंत्रभाग असून तो 2 टन क्षमतेचा आहे. 900 मिमी. लांबीवर दोन ठिकाणी हार्डनेस तपासावा लागतो. त्यासाठी ‘फाय’च्या मशिनमध्ये आम्ही बदल करून घेतले. म्हणजेच 1000 मिमी. मर्यादा असलेली लांबी 1200 मिमी. करून घेतली. तसेच आमच्या आणि ग्राहकाच्या गरजेनुसार सॉफ्टवेअरमध्ये योग्य ते बदल करून घेतले, ज्यामुळे यंत्रभागाची ट्रेसेबिलीटी आणि नंबर मिळण्यास मदत होऊन यंत्रभागाची सर्व माहिती अहवालांमधून सविस्तर मिळू लागली. काही यंत्रभागांना 2 तर काहींना 4 लोकेशन असतात, त्याप्रमाणे त्याची तपासणी झाली पाहिजे यासाठी आम्ही सॉफ्टवेअर विकसित करून घेतले. पूर्वीच्या मशिनमध्ये मानवी चुका जास्त असल्यामुळे पुरवठादार आणि आमच्यामध्ये होणारा गोंधळ कमी करण्यासाठी नवीन मशिनचा मोठा फायदा झाला आहे.
फायदे
• सर्व अहवाल अचूक येऊ लागले.
• स्वयंचलित काम झाले.
• दिलेला भार मोजता येऊ लागल्यामुळे यंत्रभागांची अचूकता वाढली.
• अप्रशिक्षित कामगारसुद्धा सहजतेने काम करू शकतो.
आमोद कुलकर्णी यांत्रिकी अभियंते असून, ते FIE चे संचालक आहेत.
पदवी घेतल्यानंतर त्यांनी मशिन टूल मेंटेनन्सपासून काम करण्यास सुरुवात केली.
त्यानंतर त्यांनी मशिन टूल उत्पादनाचा अनुभव घेतला. मागील पाच वर्षांपासून ते टेस्टिंग मशिनच्या उत्पादनामध्ये नवनवीन सुधारणा करीत आहेत.