जागतिकीकरण, इंडस्ट्री 4.0 असे शब्द ऐकल्यावर एका लहान उद्योग चालविणाऱ्या उद्योजकाला धडकी भरण्याची शक्यता नाकारता येत नाही. याचे प्रमुख कारण म्हणजे त्याबद्दल पुरेशी माहिती नसणे. सध्याच्या स्पर्धात्मक जगात टिकून रहायचे असल्यास संपूर्ण जग आपली बाजारपेठ आहे, असा दृष्टिकोन ठेवून कारखान्यात योग्य ते बदल करून ते अंमलात आणणे गरजेचे असते. अशावेळी छोटे कारखानदार गुंतवणुकीच्या दृष्टीने मागे पडतात. उद्यमबाग बेळगांव येथील आमची प्राइम इंडस्ट्री सी.एन.सी. यंत्रण आणि ग्राइंडिग सेवा पुरविणारी एक लहान कंपनी आहे. प्रतिस्पर्ध्यांबरोबर स्पर्धा करून या स्पर्धात्मक जगात टिकून राहण्यासाठी, उपलब्ध असलेल्या गोष्टींमध्ये सुधारणा करणे हाच आमच्याकडे पर्याय असतो. त्यामुळे आपल्याकडील संसाधने (रिसोर्सेस) जास्तीतजास्त कशी वापरता येतील, याचा विचार करणे भाग पडते. त्याबरोबरच होणारे नुकसान कसे कमी करता येईल याकडे लक्ष देणेही गरजेचे वाटते. या दोन गरजा लक्षात घेऊन आम्ही एक सॉफ्टवेअर विकसित करण्याचे ठरविले आणि आमच्या कारखान्यातील माहितीचे व्यवस्थापन करणाऱ्या किफायतशीर सॉफ्टवेअरची निर्मिती केली, त्याचाच हा प्रवास.
आमच्या कारखान्यात वेगवेगळ्या प्रकारचे यंत्रभाग तयार होतात. कोणत्या वेळी कोणता भाग बनवायला येईल याची पूर्वकल्पना नसते. त्यामुळे एखादा भाग आल्यानंतर त्याला लागणारे नवीनतम ड्रॉइंग, टूलिंग, इन्सर्ट तपशील, प्रोसेस ड्रॉइंग, मशिन सेटअप यांची शोधाशोध करून ही माहिती जमविताना वेळ वाया जातो. अशावेळी जुने बाद झालेले डॉक्युमेंट हाती लागण्याची शक्यता वाढते, काही वेळेला तसा प्रसंगही उद्भवला आहे. चुकीचे ड्रॉइंग वापरल्यामुळे दोन बॅच नाकारल्या गेल्या आहेत. तसेच ही सर्व माहिती काही ठराविक लोकांनाच ज्ञात असल्यामुळे त्यांच्यावर अवलंबून रहावे लागते. त्यामुळे आवश्यक असणारी सर्व माहिती एकाच ठिकाणी मिळणे अवघड होते.
अशा बऱ्याचशा समस्या आमच्या कारखान्यात होत्या. त्यामुळे त्यावर योग्य उपाय शोधणे हे आमच्यासमोर आव्हान होते. आज तंत्रज्ञानात इतकी प्रगती झाली असतानाही जुन्या पारंपरिक पद्धतीने काम करून चालणार नव्हते. त्यासाठी आम्ही कागदावर असलेल्या सर्व फाइल आणि माहिती डिजिटल डाटाच्या स्वरूपात बदलण्याचे ठरविले आणि त्यासाठी बाजारामध्ये असणारे सॉफ्टवेअर पर्याय शोधण्याचा प्रयत्न चालू केला. त्यावेळी असे लक्षात आले की, या सर्व उत्पादनांच्या किंमती काही लाखांमध्ये आहेत आणि आम्हाला तेवढा खर्च करणे परवडणारे नव्हते. त्यामुळे आम्ही कारखान्यातील माहिती व्यवस्थापनाची आमची स्वतःची प्रणाली विकसित करण्याचे ठरविले आणि त्या अनुषंगाने काम चालू केले.
हे सर्व करताना इंडस्ट्री 4.0 विषयीसुद्धा काही माहिती मिळत होती. त्याचीही गरज लक्षात घेऊन कारखान्यातील सर्व अहवाल (रिपोर्ट) डिजिटल फॉरमॅटमध्ये आणण्याचा विचार केला. सुरुवातीला हे सर्व अहवाल आम्ही लेखी स्वरूपात संग्रहित करीत होतो. त्यातून माहिती घेऊन संगणकावर ती माहिती एक्सेल शीटमध्ये भरून, त्याचे संकलन करून, वाचायला सुलभ होतील असे अहवाल व्यवस्थापनाकडे सादर करणे यासाठी एका व्यक्तीचा दररोज अर्धा दिवस जात होता. त्या कुशल व्यक्तीचा महत्त्वाचा वेळ या कामी गुंतून राहत होता.
अहवालामध्ये उत्पादन आणि कार्यक्षमता, मशिनचा अनुत्पादक वेळ, उत्पादक वापर, रिजेक्शन ही सर्व माहिती होती. सर्व अहवाल आम्हाला काही मिनिटांतच मिळतील अशी प्रणाली विकसित करायची होती. हे सर्व काम करताना कमीतकमी खर्चात आणि ‘पेपरलेस’ कसे होईल यावर आम्ही भर दिला. E-fac (इकॉनॉमिकल, एफिशिएंट, इकोफ्रेन्ड्ली) नावाचे सॉफ्टवेअर विकसित केले आणि ते करताना आम्ही याची काळजी घेतली की, एखादा अकुशल कामगारसुद्धा ते वापरू शकेल. आम्ही कमीतकमी इनपुट देऊन जास्तीतजास्त आउटपुट मिळेल यावर लक्ष केंद्रित केले.
हे सॉफ्टवेअर विकसित केल्यानंतर आम्ही त्याचे दोन भागात रूपांतर केले. एक कारखाना माहिती व्यवस्थापन आणि दुसरे डिजिटल अहवाल. कारखान्यातील माहिती व्यवस्थापनामधून आम्हाला कोणत्याही कार्यवस्तुची इत्थंभूत माहिती एका क्षणात मिळू लागली. त्यामुळे गोंधळ नाहीसा होऊन वेळ, कष्ट आणि परस्परावलंबन टळले. डिजिटल अहवालातून कारखान्यातील होणारे नुकसान समजायला लागले. सर्व मशिन किती क्षमतेने वापरली जात आहेत, कामगारांची कार्यक्षमता किती आहे, उत्पादनातील नापास होणाऱ्या भागांचे ‘पीपीएम’ आकडे, ही सर्व माहिती मिळू लागली जी कारखान्यामध्ये सुधारणा करण्यासाठी आम्हाला आवश्यक होती. त्या अनुषंगाने आम्ही आमची उद्दिष्ट्ये आखून घेतली आणि त्यावर टप्प्याटप्याने सुधारणेच्या कामाला लागलो. यामध्ये कामगारांची कार्यक्षमता वाढल्यामुळे त्यामध्ये 5 ते 10 टक्क्यांनी सुधारणा झाली. नुकसान कमी झाले. मशिनचा उत्पादक वापर वाढला, तसेच यंत्रभागाशी निगडित सर्व माहिती काही क्षणातच एका ठिकाणी मिळू लागली. काही सल्लागारांच्या मदतीने त्यामध्ये पीपीसी गुणवत्तेचे मॉड्युलसुद्धा विकसित केले. हे सॉफ्टवेअर विकसित करताना लघु आणि मध्यम उद्योगांत असणारे प्रतिस्पर्धी, इंडस्ट्री 4.0 मध्ये सामील होण्याची इच्छा परंतु त्यास लागणारे भांडवल, तसेच पेपरलेस नोंदी करून खर्च कमी करणे या सर्व बाबींचा विचार केला. कार्यक्षम, आर्थिकदृष्ट्या परवडणारे आणि वापरण्यास सुलभ असे ए-षरल सॉफ्टवेअर तयार करून इंडस्ट्री 4.0 च्या प्रवाहात कसे सामील होता येईल, यावर लक्ष केंद्रित केले.
E-fac सॉफ्टवेअरमुळे झालेले फायदे
कोणत्याही कंपनीतील सर्वात महत्त्वाची आणि महागडी गोष्ट म्हणजे मशिन होय. ग्राहकाने मागितलेले सर्व यंत्रभाग योग्य वेळेत देणे गरजेचे असते. आमच्याकडे साधारणतः 80 प्रकारचे भाग सी.एन.सी. यंत्रण आणि ग्राइंडिंगसाठी येत असतात. सर्व प्रकार मिळून प्रति महिना 25,000 भागांची निर्मिती होते. यंत्रभागांचा वेळेत पुरवठा करण्यासाठी ग्राहकाचा दबाव असायचा. त्यासाठी नवीन मशिनची खरेदी करावी का असाही विचार आम्ही केला. मात्र हा निर्णय खूप खर्चिक म्हणजे साधारण 20 ते 25 लाखांचा होता. त्यावर योग्य तो निर्णय घेणे आम्हाला गरजेचे होते.
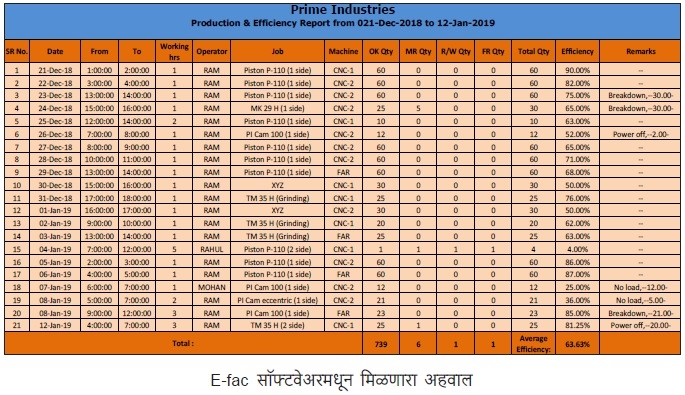
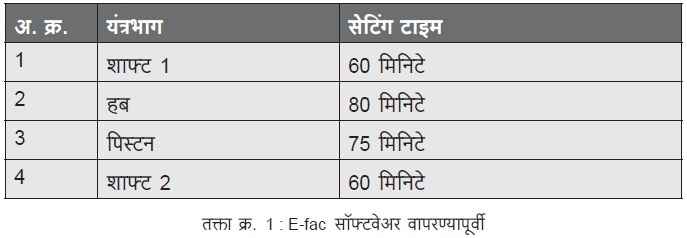
दरम्यान, आम्ही E-fac सॉफ्टवेअर वापरण्यास सुरुवात केल्यापासून आमच्या असे लक्षात आले की, आम्ही मशिनचा केवळ 70% वापर करीत आहोत. म्हणजेच आमच्याकडे मशिनचा 30% अतिरिक्त वेळ उपलब्ध होता. या बाबीचा अभ्यास करताना आमच्या लक्षात आले की, आमचे प्रॉडक्शन प्लॅनिंग चुकत आहे. त्यासाठी आम्ही एकाच प्रकारच्या यंत्रभागांचे यंत्रणासाठी एकत्रीकरण केले. पूर्वी शाफ्ट 1 आणि शाफ्ट 2 वेगवेगळ्या वेळी तयार होत होते. या एकाच प्रकारच्या कार्यवस्तू असल्याने त्या आम्ही एकापाठोपाठ करावयाचा निर्णय घेतला. त्यामुळे शाफ्ट 2 चा सेटिंग टाइम वाचून एकूण वेळ 60 मिनिटांवरून 30 मिनिटांवर आला. अशा पद्धतीने 30 मिनिटे वाचली. आमचा सेटिंग टाइम कमी झाल्यामुळे मशिनचा वापर 92 टक्क्यांपर्यंत वाढविता आला. यामुळे ग्राहकांची मागणी वेळेत पूर्ण करणे आम्हाला शक्य झाले. याशिवाय नव्याने मशिन घेण्याचा लाखोंचा खर्चदेखील वाचला. ग्राहकाकडून नाकारण्यात आलेल्या गोष्टींची माहिती वेगवेगळ्या रजिस्टरमध्ये नोंदविलेली असल्यामुळे यांचा अभ्यास करण्यासाठी आमचा बराच वेळ खर्ची जात होता. यासाठीदेखील आम्ही E-fac चा वापर करण्यास सुरुवात केल्याने आम्हाला सर्व माहिती एका ठिकाणी तात्काळ उपलब्ध होण्यास मदत झाली. नाकारण्यात आलेल्या गोष्टींचा अभ्यास करणेही त्वरित शक्य झाले. योग्य ते निर्णय घेतल्यामुळे नाकारलेल्या वस्तूंचे प्रमाण 11,000 PPM वरून 5000 पर्यंत आणण्यात यश आले.
या व्यतिरिक्त कंपनीतील शॉप फ्लोअरवर अनेक स्वरूपाच्या कमतरता होत्या, ज्या पूर्वी आमच्या निदर्शनात आल्या नाहीत. त्यामुळे 350 तास वाया जात होते. E-fac ची मदत घेऊन वाया जाणारे तास 350 वरून 150 ते 175 तासांपर्यंत आणण्यात आम्ही यशस्वी झालो.
राहुल फडके
भागीदार, प्राइम इंडस्ट्रीज्
0 9341102624
राहुल फडके यांत्रिकी अभियंते असून त्यांनी फायनान्समध्ये एम.बी.ए. केले आहे. त्यांना उत्पादनक्षेत्रातील 19 वर्षांचा अनुभव आहे.