सरफेस प्लेट, मापनाचे प्रिझम अशा मोजमापन संदर्भ उपकरणांमध्ये आणि मोजमापनामधील इतर साहाय्यक साधनांमध्ये वापरण्यासाठी ग्रॅनाइट आदर्श आहे. प्रिसिजन पृष्ठभाग मापनासाठी संदर्भ म्हणून स्टील अथवा कास्ट आयर्नपेक्षा ग्रॅनाइट( Granite ) अधिक चांगले असते. ग्रॅनाइट उत्पादांच्या विकसनातील आव्हानांसोबत ग्रॅनाइटमधील मोजमापन साधनांचा वापर आणि काळजी याबाबत सोदाहरण माहिती या लेखात वाचावयास मिळेल.
ग्रॅनाइट एक अतिशय कठीण, स्फटिकाच्या घडणीचा, नैसर्गिक अग्निज खडकातून तयार झालेला दगड प्रामुख्याने क्वार्टझ आणि फेल्स्पार यांच्यापासून बनलेला असतो. मेट्रॉलॉजीच्या कामांमध्ये या दगडाची कुठली ग्रेड वापरावी असे निश्चित केलेले नाही. या दगडात विविध खनिजे समाविष्ट असल्यामुळे तो विविध रंगात आढळतो आणि त्याची घनताही भिन्न असल्यामुळे मोजमापनाच्या कामात या दगडाच्या उपयुक्ततेवरदेखील त्याचा परिणाम होतो. काळ्या रंगाचा दगड सर्वात चांगला मानला जातो. तथापि, राखाडी आणि हिरव्या रंगाचे दगडदेखील तितकेच चांगले असू शकतात. वापर करण्यापूर्वी काळ्या रंगाव्यतिरिक्त इतर दगडांची चाचणी करून त्यांचे गुणधर्म तपासावे लागतात. सरफेस प्लेट, मापनाचे प्रिझम अशा मोजमापन संदर्भ उपकरणांमध्ये आणि मोजमापनासाठीच्या इतर साहाय्यक उपकरणांमध्ये वापरण्यासाठी ग्रॅनाइट अनेक कारणांमुळे आदर्श आहे.
प्रिसिजन पृष्ठभाग मापनासाठी संदर्भ म्हणून स्टील अथवा कास्ट आयर्नपेक्षा ग्रॅनाइट अधिक चांगले असते. त्याची कारणे पुढे दिली आहेत.
· रासायनिक प्रतिकारशक्तीमुळे त्याला गंज लागत नाही किंवा त्याचे क्षरण (झीज) होत नाही आणि त्यामुळे त्याची देखभाल करणे सोपे असते.
· उष्णता प्रसरणाचा गुणांक (हीट एक्स्पान्शन कोइफिशंट) कमी असल्यामुळे ते वेडेवाकडे (वार्प) होत नाही.
ग्रॅनाइट आणि कास्ट आयर्नचा रेखीय औष्णिक प्रसरणाचा गुणांक (CLTE)
काळा : 2.2 K-1,
हसन ग्रीन : 3.3 K-1,
कास्ट आयर्न : 10-12.5 K-1
· आयुर्मान दीर्घ असते.
· पृष्ठभाग नितळ असल्यामुळे कार्यवस्तूची हालचाल सहज होते.
· अचुंबकीय (नॉन मॅग्नेटिक) आहे.
· याचा सच्छिद्रपणा कमी (केवळ मोजमापन श्रेणीमध्ये) आहे आणि म्हणून ते सहजपणे वेडेवाकडे होत नाही किंवा त्यावर डाग पडत नाहीत.
· कास्ट आयर्नपेक्षा याचा कंपन प्रतिकार जास्त आहे.
· अधिक अचूकतेने फिनिश करता येऊ शकते.
· वापर करताना जर त्याच्या पृष्ठभागावर ओरखडा पडला, तर त्यात प्रतिक्रियात्मक उंचवटा निर्माण होत नाही. जर स्टीलवर ओरखडा पडला, तर ओरखड्याच्या कडेवरचे मटेरियल बाहेर ढकलले जाते आणि एक उंचवटा तयार होतो. जर उंचवटा मोठा असेल, तर स्टील प्लेटचा पृष्ठभाग पुन्हा फिनिश करावा लागतो.
· ग्रॅनाइटच्या संरचनेत मोठे कण असतात, जे फक्त तुटतात आणि बाहेर फेकले जातात. सपाटपणावर (फ्लॅटनेस) याचा परिणाम होत नाही. (कार्यवस्तूच्या तुलनेत ओरखड्याचा आकार लहान असेल तर)
· कास्ट आयर्नच्या अर्ध्या किंमतीत मिळते.
· कास्ट आयर्न वापरण्यास आकार प्रतिबंधक ठरू शकतो, कारण कोणत्याही कामासाठी कास्ट आयर्नचे ओतकाम यशस्वीपणे करण्यात आकाराच्या आणि फिनिशिंग करण्यात किफायतशीरपणाच्या मर्यादा असतात.
ग्रॅनाइट उत्पादनांच्या विकसनातील आव्हानेपूर्वी आमची सर्व मोजमापन उपकरणे कास्ट आयर्नची होती. हा उद्योग जसा विकसित होत गेला आणि अचूक यंत्रभागांची मागणी वाढत गेली, तसे कास्ट आयर्नचा उष्णता प्रसरणाचा गुणांक उच्च असण्याचे तोटे ठळकपणे दिसू लागले. ग्राहकांना अतिशय काटेकोर अचूकता हवी होती, म्हणूनच आम्ही ग्रॅनाइट वापरण्यास सुरुवात केली. उच्च अचूकता असलेल्या ग्रॅनाइट सरफेस प्लेट नियंत्रित तापमानात उपकरणे आणि गेज यांच्या कॅलिब्रेशनसाठी सर्वोत्कृष्ट असतात.
80 च्या दशकाच्या सुरुवातीस, विकसित देशांमध्ये ग्रॅनाइटचा वापर केला जात होता. कारण ग्रॅनाइटचा उष्णता प्रसरणाचा गुणांक कास्ट आयर्नपेक्षा खूपच कमी असल्यामुळे ते एक स्थायी (स्टेबल) मटेरियल होते आणि कमी खर्चिक होते. दक्षिण भारतातील दख्खनचे पठार जगातील अत्यंत उच्च प्रतीचे ग्रॅनाइट विपुल प्रमाणात मिळण्याचा उत्कृष्ट स्रोत आहे. गिंडी मशीन टूल्सने (GMT) एक खाण खरेदी करण्याची व्यवस्था केली आणि होसूरमधील SIPCOT औद्योगिक संकुलामध्ये कारखाना उभारण्यासाठी भाडेतत्त्वावर जमीनही घेतली.
खाणीतून दगड काढणे ही एक वेगळीच कथा आहे. या खाणी दुर्गम, डोंगराळ भागात होत्या आणि तिथे जंगली प्राणी आणि चोरांचाही त्रास होता. उत्खनन केला जाणारा दगड मेट्रॉलॉजी ग्रेडचा आहे की नाही हे निश्चित करण्यासाठी आमच्या कर्मचाऱ्यांना कच्च्या दगडाची तपासणी करायला खाणीवर जावे लागायचे. सार्वजनिक वाहतुकीच्या अभावामुळे त्यांना अनेक अडचणींचा सामना करावा लागायचा. कधी कधी तर जवळच्या बस स्थानकापासून खाणीपर्यंत शेवटचे काही किलोमीटर अंतर चालत जावे लागायचे. त्यानंतर आणखी एक अडचण निर्माण झाली. बांधकाम उद्योगातील ग्रॅनाइटचे मूल्य लक्षात घेऊन राज्य सरकारने सर्व खाणींचा ताबा घेतला, ज्यामुळे उपलब्धता अधिकच कठीण झाली.
80 च्या दशकाच्या सुरुवातीस, ग्रॅनाइट कापण्यासाठी कामगार हातोडा आणि लोखंडी छिन्नीने ग्रॅनाइटमध्ये अनेक छिद्रे पाडत आणि त्यात लाकडी पाचर घालून त्यांच्यावर पाणी ओतत. काही वेळाने लाकूड फुगल्यामुळे खडक फुटायचा. स्फोटाद्वारे ओळीने छिद्रे पाडणे हादेखील खडकातून दगड कापण्याचा एक उपाय होता. परंतु, या पद्धतींमुळे दगडांमध्ये अंतर्गत चिरा तयार होत होत्या ज्या फिनिशिंगच्या वेळीच दिसून येत आणि त्यामुळे बनविलेल्या प्लेट नाकारल्या जात होत्या. ही एक मोठी अडचण होती, कारण यामुळे अंतिम किंमत वाढत होती.
बऱ्याच चाचण्यांनंतर आम्ही डायमंड सॉ (हिऱ्याची करवत/आरी) वापरण्याचे ठरविले. यात दगड क्रॅक होत नाही आणि अपव्यय कमी होतो. खूप खोलवर काम करावयाचे असल्यास वायर कटिंगला प्राधान्य दिले जाते.
ग्रॅनाइट खरेदी केल्यानंतर, त्याला लॅप करण्यासाठी हाताने लॅपिंग करण्यात निष्णात असणाऱ्या कारागीरांची एक टीम तयार करावी लागली. हे अतिशय कष्टदायक आणि कठोर परिश्रमाचे काम आहे. प्लेटच्या पृष्ठभागाचे लॅपिंग करण्यात संपूर्ण दिवस जायचा. प्लेट कोरडी व्हायची वाट पहावी लागायची. प्रत्येक टप्प्यावर तपासणी करण्यापूर्वी पृष्ठभाग वातावरणीय तापमानावर यावा लागतो. थोडक्यात काय तर कामाच्या ओघामध्ये बरेच अडथळे होते. आज लॅपिंग मशीन वापरून 5 मायक्रोमीटरपर्यंतचा सपाटपणा मिळविला जाऊ शकतो, परंतु त्याच्यापेक्षा अधिक अचूकता केवळ हातानेच मिळू शकते.
अशाप्रकारे, 'हाय टेक' अॅप्लिकेशनसाठी लागणारी अत्यंत उच्च अचूकता असणारी उत्पादने मानवी हातांची, 'नो टेक' नैसर्गिक शक्ती आणि संवेदनशीलता वापरून विकसित केली गेली.
विश्वासार्ह तपासणी प्रयोगशाळा उभारणे हे पुढील लक्ष्य होते. लक्षात ठेवा, हे 80 च्या दशकात घडत होते. प्रयोगशाळेची सर्व अचूक साधने आयात करावी लागत होती आणि आयात शुल्क 300 टक्क्यांपर्यंत होते. त्यामुळे आमच्या आर्थिक अंदाजपत्रकाला खूपच धक्के बसले होते.
प्रिसिजन ग्रॅनाइट उत्पादने बनविण्यासाठी खाणीमध्ये अचूक दगड निवडण्यापासून, त्यांना योग्य प्रकारे कापून बाहेर काढणे, त्यांचे लॅपिंग, ड्रिलिंग, इन्सर्ट बॉँडिंग, पॅकिंग आणि डिस्पॅच करण्यापर्यंत बऱ्याच समस्या होत्या. बऱ्याचदा, आम्हाला आमच्या उत्पादांच्या गरजेनुसार मशीन बनवाव्या लागल्या. उदाहरणार्थ, सुरुवातीला आम्ही ग्रॅनाइटमध्ये इन्सर्टसाठी ड्रिल करताना रेडियल ड्रिलिंग मशीन वापरायचो. कालांतराने, ग्राहकांनी थ्रेडेड इन्सर्टची अचूकता अधिक हवी आहे, अशी मागणी केली. आम्ही ड्रिलिंगसाठी शीतक म्हणून पाणी वापरतो. असे मशीन सहज उपलब्ध नव्हते. म्हणून, आम्ही एक ग्रॅनाइट गॅँट्री संरचना (चित्र क्र. 7) बनविली आणि त्यावर एच.एम.टी. ड्रिलिंग हेड बसविले. आम्ही आता इन्सर्टवर 50 मायक्रोमीटर पिचची अचूकता मिळवू शकतो, तसेच मागणीनुसार यापेक्षाही अधिक अचूकपणा मिळवू शकतो.
चकाकी आणि त्यामुळे होणाऱ्या मापनातील समस्या टाळण्यासाठी, प्रिसिजन ग्रॅनाइट पृष्ठभाग कधीही पॉलिश केले जात नाहीत.
आमच्याकडे ग्रॅनाइटचे आता अनेक स्रोत आहेत. प्रत्येकवेळी जेव्हा आम्ही नवीन खाणीतला ग्रॅनाइट वापरतो तेव्हा आम्ही NABL मान्यताप्राप्त प्रयोगशाळेत त्याची तपासणी करतो. तक्ता क्र. 2 मध्ये प्रातिनिधिक परिणाम दाखविले आहेत.
मोजमापन उपकरणांची तपासणी परिमाणीय (डायमेन्शनल) मेट्रॉलॉजी उपकरणे प्रमाणित करण्यासाठी बरीच यांत्रिकी आणि इलेक्ट्रॉनिक गेज आहेत. सुरुवातीच्या काळात आम्ही ऑप्टिकल गेजदेखील वापरले. (उदाहरणार्थ, सरळपणाचे (स्ट्रेटनेस) प्रमाणीकरण करण्यासाठी ऑटोकॉलिमीटर.) यासाठी तपासणी करणाऱ्या व्यक्तीकडे उच्च दर्जाचे कौशल्य असणे आवश्यक आहे. 80 च्या दशकाच्या उत्तरार्धात, सपाटपणाच्या मापनासाठी इलेक्ट्रॉनिक लेव्हल उपकरणे वापरण्यास सुरुवात झाली. ती बसविणे आणि त्यांची देखभाल करणे हे आमच्यासाठी एक वेगळेच आव्हान होते, कारण त्यावेळी भारतातील कोणालाही अशा प्रकारच्या इलेक्ट्रॉनिक उपकरणांची फारशी माहिती नव्हती. मॅन्युअल तपासणीत, प्लेटच्या पृष्ठभागावर पेन्सिलने चौकटी (ग्रिड) आखाव्या लागतात आणि त्यांच्या प्रत्येक भागावरून स्पिरिट लेव्हल काळजीपूर्वक सरकवून स्तराचा तक्ता (आलेख क्र. 1) हाताने बनवावा लागतो.
ग्राहकांच्या गरजा संबोधित करण्यामधील टेक्नो कमर्शियल आव्हानेएका ग्राहकासाठी आम्ही 12 मीटर लांब T खाच (स्लॉट) असलेली 12 मीटर X 1.5 मीटर आकाराची एक प्लेट बनविली होती. T खाचेचा सरळपणा 150 मायक्रोमीटर/12 मीटर लांबीसाठी देण्याचे कबूल केलेले होते आणि आम्ही तो 80 मायक्रोमीटरमध्ये देऊ शकलो. T खाच इन्सर्ट संरेखित करण्यासाठी, संदर्भ म्हणून प्लेटच्या वरच्या पृष्ठभागापासून 100 मिमी. अंतरावर प्लेटच्या एका बाजूला (साइड) एक खाच केली. प्लेटच्या लांबीवर या 100 मिमी. पृष्ठभागाच्या सरळपणाची अचूकता 30 मायक्रोमीटर/12 मीटर होती आणि T खाचेची अचूकता 12 मीटर लांबीवर 80 मायक्रोमीटर होती. चित्र क्र. 9 पहा.
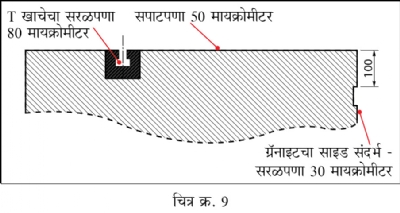
या आकाराचा एक दगड खाणीतून, खडकाच्या एका चांगल्या नसेमधून कापून काढण्यासाठी तीन वेळा प्रयत्न केल्यानंतर यश मिळाले. 30 टन वजनाची प्लेट खाणीतून कारखान्यात आणणे, अनलोड करणे, योग्य स्थानी ठेवणे आणि स्पेसिफिकेशनप्रमाणे फिनिश करणे यातील प्रत्येक गोष्ट आव्हानात्मक होती. त्यात तपासणी प्रक्रियेसाठी आम्हाला प्लेटच्या आसपास एक नियंत्रित वातावरण तयार करावे लागले. त्यानंतर ती प्लेट पॅक करणे, लोड करणे आणि घाटातून वाहतूक करून नेणे, नंतर ग्राहकाकडे ती अनलोड करून अनपॅक करणे आणि तिची कामगिरी सिद्ध करणे, हेसुद्धा काही कमी कठीण नव्हते.
दुसरे उदाहरण 5 अक्षीय मशीन कॅलिब्रेट करण्यासाठी सरफेस प्लेटउच्च दर्जाची अचूकता असलेल्या यंत्रभागांच्या उत्पादनामध्ये बहुअक्षीय मशीनचा वापर करण्याचा कल वेग घेत आहे. या मशीन स्थिर तापमानाच्या वातावरणात ठेवल्या जातात. एकदा मशीन स्थापित केल्यानंतर, उत्पादकाद्वारे मशीनवर 'झीरो सेटिंग' केले जाते. उपयोगानंतर, वापरकर्त्यास मशीनचे झीरो सेटिंग पुन्हा करण्यासाठी मशीन उत्पादकावर अवलंबून रहाणे आवश्यक असते, कारण कोणत्याही कॅलिब्रेशन प्रयोगशाळा 5 अक्षीय मशीनचे कॅलिब्रेशन करण्यासाठी अद्याप तयार नाहीत. हे अत्यंत महाग असते. याव्यतिरिक्त, त्यांना उत्पादकाकडून सेवेची वाट पाहावी लागते, ज्याने खर्चात अधिकच भर पडते.
एका ग्राहकाने आम्हाला कॅलिब्रेशन मास्टर (चित्र क्र. 11) विकसित करण्याची विनंती केली आणि आम्ही ते करण्यात यशस्वी झालो.
तिसरे उदाहरण ग्राहकांचा आवाज आपल्यापर्यंत पोहोचविण्याचा सर्वोत्तम मार्ग म्हणजे त्यांनी दिलेली प्रशंसापत्रे! आमचे एक ग्राहक, मे. नॅनोटॉम टेक्नॉलॉजीज् प्रा. लि., बंगळुरू यांनी नॅनो मिलिंग मशीनसाठी ग्रॅनाइट बेस आणि गँट्री खरेदी केली होती. नॅनोटॉमचे सतीशकुमार सांगतात की, ''ग्रॅनाइट बेस आणि कॉलम यांचा कडकपणा (स्टिफनेस) आमच्या ग्राहकाच्या अपेक्षेनुसार होता आणि निवडलेल्या ग्रॅनाइटचे गुणधर्मदेखील मानकांनुसार होते. अमेरिकेतील आमचे ग्राहक ग्रॅनाइटच्या कडकपणाने खूपच संतुष्ट आहेत.''
आवश्यक फ्रेमचा कडकपणा असलेला ग्रॅनाइट बेस आणि कॉलम (चित्र क्र. 12) मिळाल्याने ग्राहक खूप आनंदित झाला.
ग्रॅनाइट मोजमापन उत्पादनांचा वापर आणि काळजी 1. इन्स्टॉलेशनदरम्यान प्लेटला योग्य आधार द्या. सरफेस प्लेटच्या बाबतीत, लेव्हलिंग स्क्रूसह एक स्टँडदेखील दिला जातो. सरफेस प्लेटला प्लेटच्या टोकांपासून लांबीच्या 20 टक्के आत, 3 बिंदूंवर आधार देणे आदर्श असते. त्यातील दोन आधार प्लेटच्या लांब बाजूपासून रुंदीच्या 20% आत आणि उरलेला आधार मध्यभागी असला पाहिजे. उत्पादनादरम्यान हेच आधार बिंदू वापरले जातात.
2. प्लेट वापरण्यापूर्वी तिला सभोवतालच्या वातावरणाच्या तापमानावर येण्यासाठी कमीतकमी अर्धा तास वेळ द्या. उदाहरणार्थ, टूल रूममध्ये, वातानुकूलनाची यंत्रणा सतत चालू ठेवणे व्यावहारिक नसते. कधी कधी ती बंद करावी लागते. ती चालू केल्यानंतर, प्लेटच्या संपूर्ण क्रॉस सेक्शनमध्ये एकसारखे स्थिर तापमान येणे आवश्यक असते.
3. उत्पादाला स्वच्छ ठेवा. दिवसातून कमीतकमी दोनदा साबणाच्या पाण्याने पुसून काढा. उत्कृष्ठ परिणाम मिळविण्यासाठी, साफसफाईनंतर कोरडे होण्यास आणि सभोवतालच्या तापमानावर पोहोचण्यास पुरेसा वेळ द्या. मापनासाठी आवश्यक असलेल्या वस्तूंशिवाय उत्पादावर चहाचे कप किंवा इतर कोणतीही वस्तू ठेवू नका.
4. पृष्ठभागावर टवके पडणे हे नुकसान होण्याचे सामान्य चिन्ह आहे. प्लेट वापरात नसताना नेहमीच तिला वरच्या बाजूने झाकून ठेवा. प्लेटच्या पृष्ठभागाचे रक्षण करण्यासाठी GMT तयार लाकडी कवच पुरवू शकते. सामान्यत:, प्लेटची झीज होण्याचे सर्वात मोठे कारण अपघर्षक धूळ असते.
5. आपली प्लेट नियमितपणे कॅलिब्रेट करा. प्लेटची देखभाल कशी केली जाते आणि ती किती वापरली जाते यावर कॅलिब्रेशन करण्याचा कालावधी अवलंबून असतो. जर प्लेट स्थिर तापमानावर ठेवली गेली असेल आणि धूळ आणि कचऱ्यापासून संरक्षित असेल, तर ती आपल्याला अधिक काळ सेवा देईल.
6. कॅलिब्रेशन हे अॅप्लिकेशनवर अवलंबून असते. साधारणपणे वर्षातून कमीतकमी एकदा उपकरणे कॅलिब्रेट करावीत, असे आम्ही सुचवितो. कॅलिब्रेशनकरिता ग्राहकाने त्याच्या निर्मात्याशी किंवा NABL प्रमाणित प्रयोगशाळांशी संपर्क साधावा.
सहलेखक : व्ही. सेकर (जनरल मॅनेजर, मेट्रॉलॉजी विभाग, गिंडी मशीन टूल्स लि.)