आवश्यकतेनुसार आणि विशिष्ट कार्यानुसार यंत्रभागावर विविध प्रक्रारच्या खाचांचे डिझाइन केले जाते. ग्रूव्हिंग प्रक्रियेद्वारे खाचांचे यंत्रण केले जाते, तर, तयार झालेला यंत्रभाग पार्टिंग ऑफ प्रक्रियेने बारपासून विभक्त केला जातो. या ग्रूव्हिंग आणि पार्टिंग प्रक्रियेचे बारकावे तपशिलात समजावून सांगणारा हा लेख.
विविध कामांसाठी आणि प्रक्रियेतील गरजांसाठी टर्निंग केलेल्या कार्यवस्तूच्या बाह्य व्यासावर (OD), अंतर्व्यासावर (ID) किंवा फेसवर ग्रूव्हिंग केले जाते. आवश्यकतेनुसार कार्यवस्तूवर विविध आकाराच्या आणि प्रकारच्या खाचांचे (ग्रूव्ह) डिझाइन (चित्र क्र. 1) केलेले असते. अशा खाचांची काही सामान्य उदाहरणे पुढे दिली आहेत.
· O रिंग आणि सील (वंगण सील, पिस्टन रिंग) अशा सीलिंग यंत्रभागांच्या जुळणीसाठी (फिटमेंट) असलेल्या खाचा
· सरक्लिपसारख्या अॅसेम्ब्लीमधील यंत्रभागांच्या जुळणीमध्ये (फिटमेंट) असलेल्या खाचा
· योग्य ठिकाणी तेल (ऑइल) पोहोचविण्यासाठी मार्ग देणाऱ्या ऑइल ग्रूव्ह
कोपरा त्रिज्या (कॉर्नर रेडियस) न वापरता कार्यात्मक क्षेत्रे (जसे की, शाफ्ट किंवा स्टेप फेसवर बेअरिंग बसविण्याची जागा) निश्चित करण्यासाठी किंवा स्टेप व्यासावर ग्राइंडिंग, गिअर कटिंग किंवा स्लॉटिंगसारख्या कामांमध्ये टूल क्लिअरन्स देण्यासाठी असलेले अंडरकट/रिसेस.
· पट्ट्यांसाठी (बेल्ट) पुली ग्रूव्ह
· बॉल बेअरिंग रेस, बॉल नट किंवा कॅम अशा यंत्रभागांच्या सापेक्ष हालचालींना (रीलेटिव्ह मूव्हमेंट) मार्गदर्शन करण्यासाठीदेखील खाच तयार केली जाते.
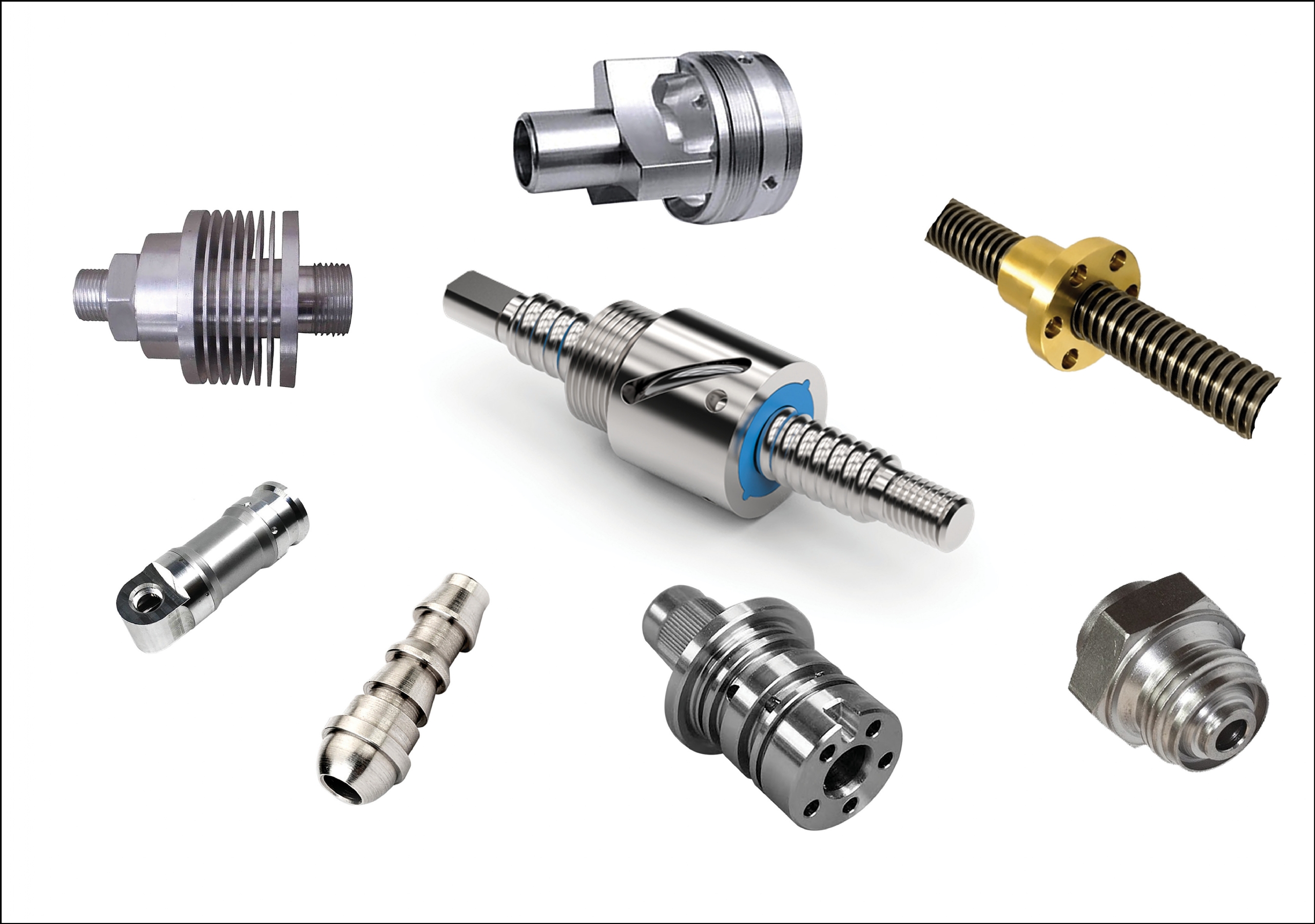
चित्र क्र. 1 : विविध यंत्रभागांवरील वेगवेगळ्या आकारांच्या खाचा
खाच गोलाकार, सर्पिलाकार (हेलिकल/स्पायरल) किंवा अनियमित आकाराची असू शकते. खाच कशासाठी वापरली जाणार आहे, त्यानुसार तिची गुणवत्ता, पृष्ठीय फिनिश, खाचेचा व्यास, खाचेच्या स्थानाची परिमाणे आणि खाचेच्या प्रोफाइलची अचूकता इत्यादी ठरविले जाते. सहसा, खाचेच्या बाजू (साइड वॉल), खाचेच्या खालचा पृष्ठभाग आणि कोपरा त्रिज्या किंवा चॅम्फर यांची गुणवत्ता कशी असली पाहिजे, ते स्वतंत्रपणे निर्देशित केलेले असते. या आवश्यकतांनुसार खाचेसाठी कोणती यंत्रण प्रक्रिया वापरायची ते ठरविले जाते.
यंत्रभागावर खाच करण्यासाठी ग्रूव्हिंग बाय टर्निंग ही प्रक्रिया बहुतेकदा वापरली जाते. इतर प्रक्रियेमध्ये जसे खाचांचे मिलिंग हे विशेष ग्रूव्हिंग टूलने अक्षीय दिशेत, U अक्षात किंवा (C-S) काटछेद करून टर्न मिल/बहुअक्षीय (मल्टीअॅक्सिस) मशीनवर केल्या जातात.
चित्र क्र. 2 : ग्रूव्हिंग आणि पार्टिंग ऑफचे संकल्पना चित्र
आता आपण टर्निंग मशीनवर खाच करण्यासंदर्भात अधिक माहिती घेऊ. फिरत्या कार्यवस्तूसाठी खाचेच्या अपेक्षित आकाराचे पूर्ण फॉर्म टूल प्लंज करणे ही ग्रूव्हिंगसाठी सर्वात सोपी आणि वेगवान टर्निंग प्रक्रिया ठरते. खाचेचा आकार (साइज आणि शेप), खाचेचा प्रकार आणि खाचेचे स्थान यांच्यानुसार टर्निंग मशीनवर खाचांचे यंत्रण करताना विविध प्रकारची आव्हाने असतात. लहान ते मध्यम आकाराच्या खाचेसाठी (चित्र क्र. 3) प्लंजिंग पद्धत सर्वात सोयीस्कर ठरते.
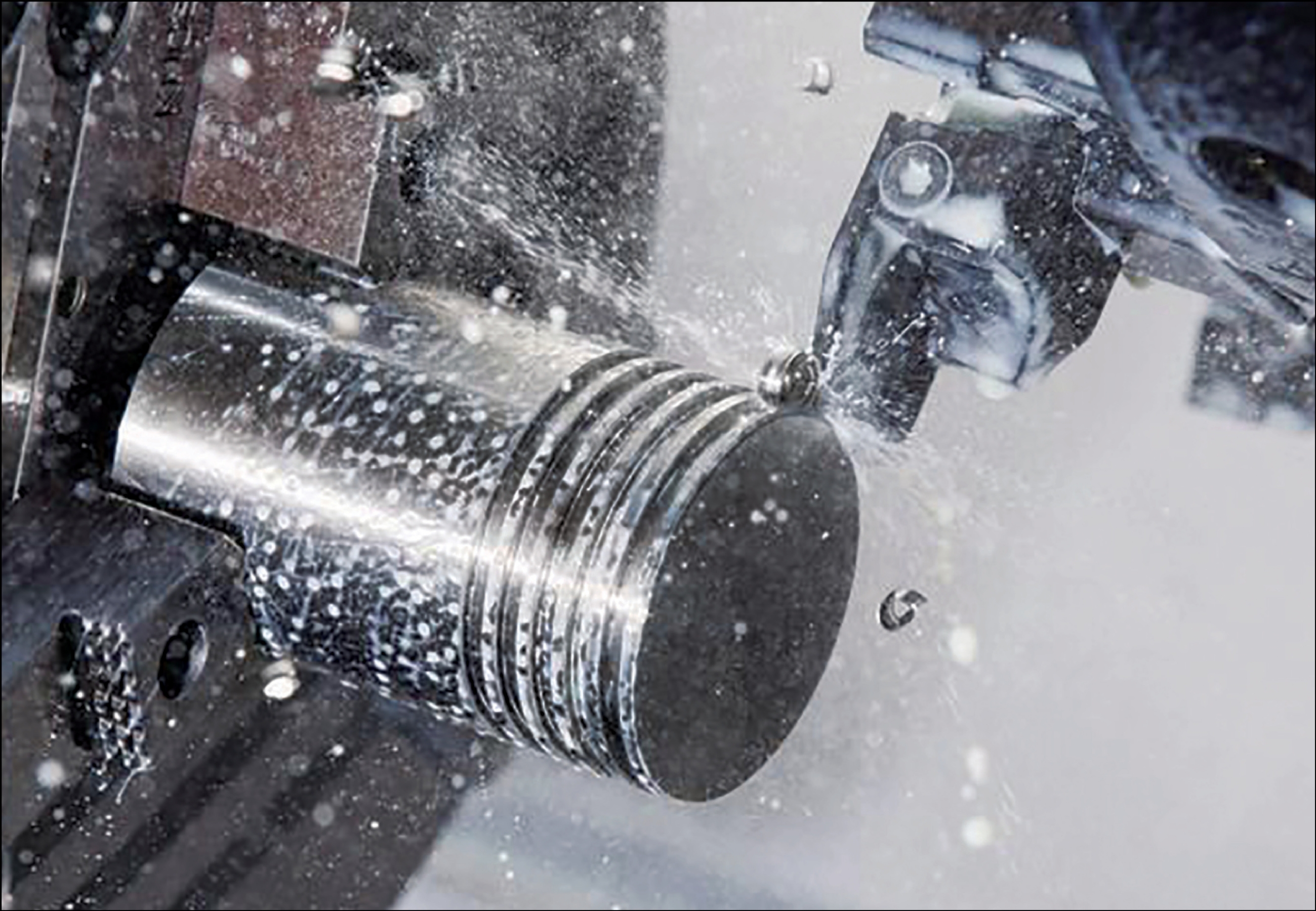
चित्र क्र. 3 : प्लंजिंगद्वारा ग्रूव्हिंग ऑपरेशन
मोठ्या काटछेदाच्या (क्रॉस सेक्शन) खाचेसाठी, अधिक प्रमाणात मटेरियल काढावे लागते आणि टूलच्या सर्व बाजूंची कर्तन कडा (कटिंग एज) बराच काळ संपर्कात रहाते. या प्रक्रियेत उच्च कर्तन बले (कटिंग फोर्स) असतात आणि म्हणूनच मटेरियल आणि खाचेच्या आकारानुसार दृढता (रिजिडिटी) आणि स्पिंडल शक्तीची आवश्यकतादेखील अधिक असते. याचा परिणाम बहुतेकदा कार्यवस्तू आणि टूल यांच्यात विरूपण (डीफॉर्मेशन) होणे, कंपने आणि खाचेच्या पृष्ठभागावर चॅटर मार्क येणे आणि टूल तुटणे यांमध्ये होतो. उच्च उत्पादकतेसाठी जेव्हा एकाचवेळी अनेक खाचा करण्याचा प्रयत्न केला जातो, तेव्हा हे अधिक आव्हानात्मक (जसे पुलीवरच्या V आकाराच्या अनेक खाचा) बनते. ग्रूव्हिंगच्या अशा कामांसाठी, मशीन टूलची संरचना, गाइडवे, स्पिंडल आणि टरेट यांची दृढता हे घटक महत्त्वाची भूमिका बजावतात. स्पिंडलची पॉवर - टॉर्क क्षमता अशा कामाची व्यवहार्यता ठरविते. कंपने आणि चॅटरिंग न होऊ देता, प्लंजिंगद्वारे किती आकाराच्या खाचेचे यंत्रण करता येऊ शकते, हे अनेकदा मशीनची दृढता आणि मशीनच्या कामगिरीवर अवलंबून असते.
चित्र क्र. 4 : मल्टीपल ग्रूव्हिंग
प्रमाणित (स्टँडर्ड) रुंदी आणि खाचांच्या नेहमीच्या आकारांसाठी, प्रमाणित इन्सर्ट सहज उपलब्ध असतात. इतर विशेष आकारांसाठी, प्लंजिंग पद्धतीमध्ये आवश्यकतेप्रमाणे (कस्टमाइज्ड्) इन्सर्टचे डिझाइन करावे लागते. तयार केलेल्या खाचेच्या बाजूच्या फेसवरून टूल पूर्ण खोलीवर पोहोचेपर्यंत पुरेसा क्लिअरन्स निश्चित करण्यासाठी इन्सर्ट आणि धारकाची (होल्डर) भूमिती योग्य असणे आवश्यक आहे. अन्यथा दृढतेवर निश्चितपणे मर्यादा येतात.
यंत्रणादरम्यान तयार होणाऱ्या चिपचा आकार, इन्सर्टच्या भूमितीनुसार ठरतो. चीप बाजूच्या पृष्ठभागावर घासल्यामुळे तो खराब होऊ न देणे आणि त्या सहजपणे अरुंद भागातून बाहेर निघणे महत्त्वाचे असते. त्यामुळे अशा प्रकारच्या यंत्रणात निर्माण होणाऱ्या चिपचा आकार हा घट्ट गुंडाळलेल्या रेडियल स्प्रिंगसारखा असतो. हा आकार असलेली चिप आदर्श मानली जाते.
चित्र क्र. 5
यंत्रण बिंदूपर्यंत शीतक पोहोचविणे ही अभियंत्यासमोरील आणखी एक समस्या असते. ही समस्या टाळण्यासाठी हल्ली टूल निर्मात्याकडूनच तशी व्यवस्था दिली जाते. टूलची निर्मिती करताना टूल उत्पादक, फ्लड कूलंट आणि उच्च दाबासह टूलच्या आतून शीतक (थ्रू कूलंट) पोहोचविण्याची व्यवस्था करतात.
सी.एन.सी. मशीनवर मोठ्या खाचा बनविण्यासाठी प्लंजिंगऐवजी खाचेचा आकार निर्माण करण्यास प्राधान्य दिले जाते आणि ती अधिक प्रचलित पद्धती आहे. यामध्ये, खाचेच्या आकारापेक्षा लहान, प्रमाणित आकाराचे टूल वापरले जाते. खाचांचे रफिंग एक किंवा अधिक पासद्वारे X किंवा Z अक्षामध्ये खाचेची रुंदी आणि खोलीनुसार केले जाते. एकसारखी फिनिशिंग माया (अलाउन्स) सोडून हे टूल खाचेच्या आकाराच्या रफिंगसाठी एकदा किंवा एकापेक्षा जास्त वेळा प्लंज केले जाते आणि चालविले जाते. शेवटी, त्याच किंवा भिन्न टूलद्वारे खाच फिनिश केली जाते. खाचेची अंतिम प्रोफाइल तयार होईल, अशा रीतीने या टूलचा मार्ग प्रोग्रॅम केलेला असतो. वर वर्णन केल्याप्रमाणे खाचेच्या रफिंग आणि फिनिशिंगसाठी सी.एन.सी.मध्ये प्रमाणित प्रोग्रॅमिंग आवर्तने (सायकल) उपलब्ध आहेत.
चित्र क्र. 6 : अंतर्व्यासावरील ग्रूव्हिंग ऑपरेशन
फुल फॉर्म प्लंजिंगच्या तुलनेत खाच करण्याच्या पद्धतीचे फायदे
प्रत्येक खाचेच्या विशेष आकारासाठी विशेष टूलऐवजी प्रमाणित टूल वापरली जाऊ शकतात, कारण जोपर्यंत खाचेची रुंदी टूलच्या रुंदीपेक्षा जास्त असेल, तोपर्यंत तिचा आकार प्रोग्रॅम करता येण्यासारखा असतो.
· एक टूल कार्यवस्तूवर वेगवेगळ्या रुंदी आणि आकारांच्या खाचा निर्माण करू शकते. त्यामुळे लागणाऱ्या टूलची आणि यंत्रण आवर्तनामधील टूल बदलांची संख्या कमी होते.
· आवश्यक असल्यास पासची संख्या वाढवून रफिंगचे कार्य विभागले जाऊ शकते.
· कर्तन कडेच्या संपर्काची लांबी कमी केली जाते. त्यामुळे यंत्रण परिस्थिती आणि चिप दूर (इव्हॅक्युएशन) नेणे सुधारते.
· पृष्ठभागाचा फिनिश चांगल्या प्रकारे नियंत्रित केला जातो, कारण खाचांच्या निर्मितीमध्ये यंत्रणाच्या प्रत्येक पासमध्ये सरकवेग प्रोग्रॅम करता येतो.
ग्रूव्हिंग आणि टर्निंगसाठी विकसित केलेल्या बहूकार्य (मल्टीफंक्शन) टूलिंगमधील ग्रूव्हिंग टूल X अक्षामध्ये अरीय (रेडियल) दिशेत प्लंज केली जाऊ शकतात आणि नंतर टर्निंग प्रक्रिया करण्यासाठी त्यांना उजव्या किंवा डाव्या हाताच्या टूलसारखा Z अक्षामध्ये सरकवेग (चित्र क्र. 5) दिला जाऊ शकतो. यात X - Z अंतर्वेशन समाविष्ट असते. अशी टूल वापरून एकाच टूलद्वारे साधे टर्निंग, फेसिंग, ग्रूव्हिंग आणि प्रोफाइलिंग अशी यंत्रणाची कामे करणे शक्य होते.
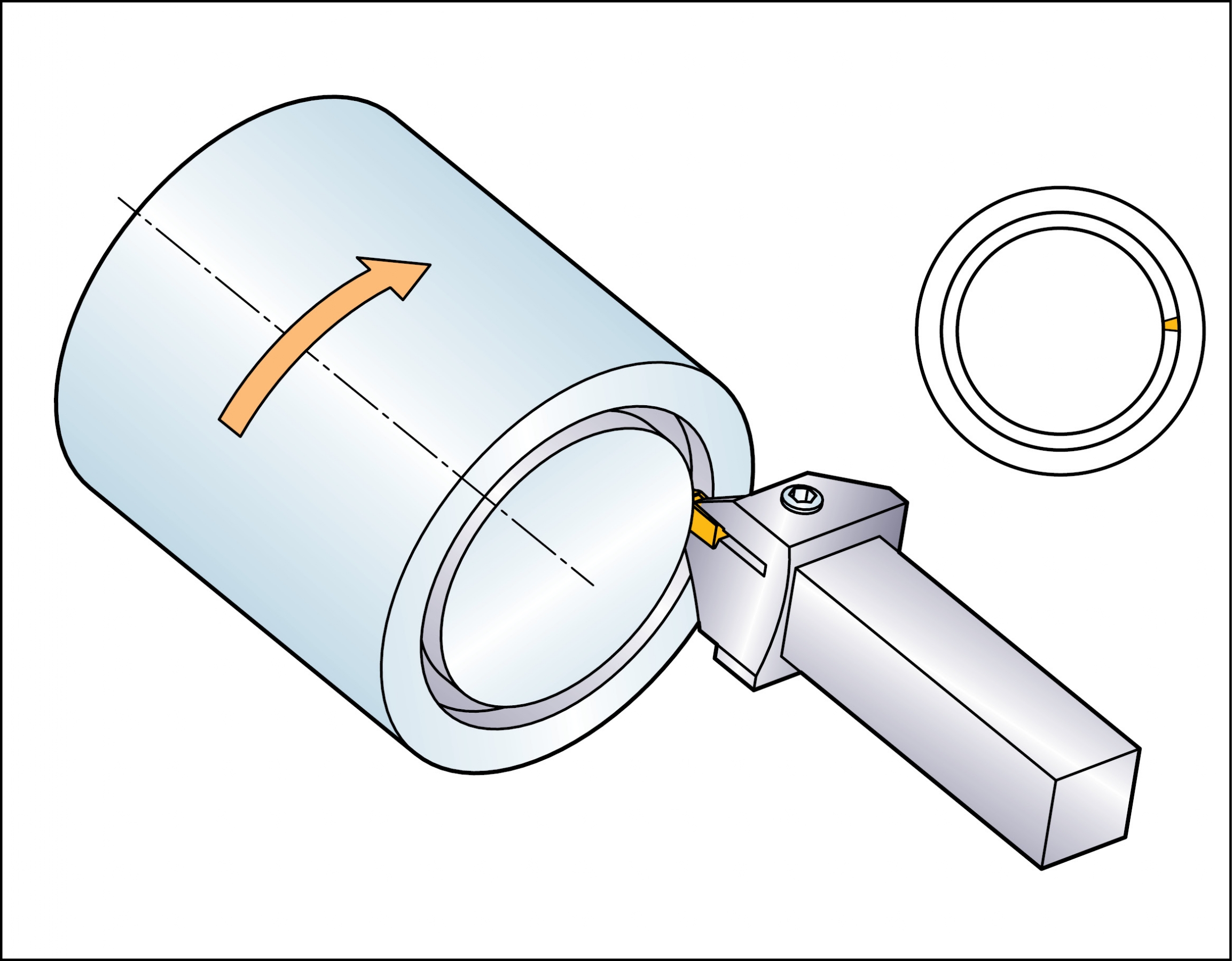
चित्र क्र. 7 : फेस ग्रूव्हिंग ऑपरेशन
विशेषत: लहान व्यासाच्या भोकामध्ये (बोअर) आणि फेसपासून खोलवर असलेल्या अंतर्व्यासावरील (ID) खाचेचे यंत्रण (चित्र क्र. 6) करणे अवघड जाते. मोठ्या खाचांच्या बाबतीत कंपन आणि चॅटर समस्या वाढू शकतात. अंतर्व्यासामधील बोअरिंगच्या यंत्रणाप्रमाणेच, येथेही टूलिंगची दृढता कमी असणे, हत्यारधारकाचे L/D गुणोत्तर (रेशो), इन्सर्टचा आकार, शीतकाचा पुरवठा आणि चिप दूर नेण्यासाठी जागेची मर्यादा या अडचणी असतात. इष्टतम उत्पादकता मिळविण्यासाठी, टूलद्वारे उच्च दाबाने शीतकाचा पुरवठा करणे, कंपनांचे अवमंदन (डॅम्पिंग) करणारे हत्यारधारकाचे डिझाइन करणे, यंत्रण प्रक्रियेचा योग्य क्रम आणि प्रोग्रॅमिंग आवश्यक असते.
फेस ग्रूव्हिंगमध्ये (चित्र क्र. 7) टूलचा प्रवेश (अॅक्सेस) आणि चिप बाहेर काढणे या दोन्ही बाबी सुलभ असतात. परंतु, टूलच्या डिझाइनमध्ये खाचेच्या बाजूंनी तयार होणाऱ्या कुंडलाकार जागेत विशिष्ट क्लिअरन्स ठेवावा लागतो. खाचेचा व्यास आणि रुंदीनुसार यास विशेष आकार (शेप) आवश्यक असतो. म्हणून टूलिंगचे डिझाइन किंवा उपलब्ध श्रेणीमधून टूलची निवड, यांच्यावर सखोल विचार करणे गरजेचे ठरते.
चित्र क्र. 8: बाह्यव्यासावरील ग्रूव्हिंग ऑपरेशन
पार्टिंग ऑफ यंत्रण
पार्टिंग ऑफ हे कार्यवस्तूच्या जवळजवळ मध्यभागी पोहोचलेले खोल OD ग्रूव्हिंग ऑपरेशन (चित्र क्र. 8) म्हणून मानले जाऊ शकते. सामान्यतः बार किंवा पाइप अशा मूळ कच्च्या मालामधून टर्न केलेल्या यंत्रभागाला विभक्त करण्याच्या हेतूने पार्टिंग ऑफ ऑपरेशन (चित्र क्र. 9) केले जाते.
चित्र क्र. 9 : बार मटेरियल आणि पार्टिंग ऑपरेशन
पार्टिंग ऑफच्या कामात बार फीडर वापरल्याने मशीनवर पुढील यंत्रभागाचे यंत्रण सुरू करण्यासाठी बार पुढे सरकविला जातो. लहान ते मध्यम आकाराच्या गोल यंत्रभागांच्या सातत्यपूर्ण उत्पादनासाठी ही पद्धत योग्य असल्याने, यंत्रणाच्या सर्वात शेवटच्या टप्प्यात पार्टिंग ऑफ करणे सामान्यतः आदर्श मानले जाते. म्हणून, पार्टिंग ऑफची कार्यक्षमता आणि किफायतशीरपणा अधिक महत्त्वाचा असतो.
विविध व्यासांच्या कार्यवस्तूंचे पार्टिंग ऑफ करण्यात अनेक तांत्रिक आव्हाने असतात. या आव्हानांवर पुढील उपायांद्वारे कार्यक्षमता साध्य करणे शक्य होते.
· उत्पादकतेसाठी इष्टतम यंत्रण पॅरामीटर वापरणे.
· मटेरियलचा अपव्यय कमी करणे. (किमान पार्टिंग रुंदी साध्य करणे)
· टूलची झीज/मोडतोड कमी करणे. (जागेची मर्यादा लक्षात घेऊन)
· चिप निर्मिती आणि अरुंद जागेतून त्यांना बाहेर काढणे.
· शीतक, यंत्रण क्षेत्रापर्यंत पोहोचविणे.
· पार्ट ऑफ केलेल्या पृष्ठभागाची गुणवत्ता राखणे.
यंत्रण (कटिंग) टूल, शीतक, प्रोग्रॅमिंग आणि मशीन डिझाइन यांच्यातील वेगवेगळ्या तंत्रज्ञानाद्वारे वरील उपाय साध्य करणे शक्य होते.
पार्टिंग टूल मुळात OD ग्रूव्हिंग टूलसारखीच असतात आणि आवश्यक ओव्हरहँगसह केंद्रापर्यंत पोहोचण्यासही ती सक्षम असतात. मोठ्या व्यासाच्या पार्टिंगसाठी मात्र परिस्थिती तुलनेने कठीण असते.
यंत्रभागाचे इष्टतमीकरण
पार्टिंग प्रक्रियेत इष्टतमीकरण आणण्यासाठी पुढील बाबींचा विचार करणे योग्य ठरते.
· कार्यवस्तूचा ओव्हरहँग कमीतकमी असावा.
· कार्यवस्तूच्या व्यासानुसार योग्य रुंदीचे पार्टिंग टूल निवडणे.
· योग्य मशीनची निवड करणे.
· कार्यवस्तू पकडण्यासाठी वापरलेल्या साधनांची दृढता निश्चित करणे.
· टूल माउंटिंग सेटअपची दृढता सुनिश्चित करणे.
· टूल टिपची योग्य केंद्रीय उंची राखणे.
· शून्य बिंदू जवळ येताना सरकवेग कमी करणे
· टूल मध्याच्या (सेंटर) थोडे आधी थांबवून कार्यवस्तूला कापण्याऐवजी ती पिप क्षेत्रातून तुटून वेगळी होऊ देणे. टूल मध्याच्या आधी थोडे थांबविण्याची शिफारस केली जाते, कारण मध्यभागी कापण्याची गती शून्य असते. पिप क्षेत्र म्हणजे पार्टिंग ऑफ करताना कार्यवस्तूच्या फेसवर निर्माण होणारा बटनासारखा आकार होय.
2 स्पिंडल वापरून पार्टिंग
यंत्रण प्रक्रियेचे नियोजन करताना, पार्टिंग ऑफ झालेल्या यंत्रभागाच्या हाताळणीचा विचार करणेदेखील महत्त्वाचे असते. एक स्पिंडल असलेल्या टर्निंग सेंटरमध्ये, पिप तयार होणे, चिमटा बसणे (पिंचिंग इफेक्ट), टूल घासणे किंवा आदळणे आणि फ्लायऑफची शक्यता दूर करण्यासाठी योग्य यंत्रण पॅरामीटर ठेवणे आवश्यक असते.
यंत्रणादरम्यान पहिल्या स्पिंडलमधून दुसऱ्या स्पिंडलमध्ये कार्यवस्तू हस्तांतरित करण्याची क्षमता बहुउद्देशीय टर्निंग मशीनमध्ये असते. तसेच एकाच मशीनवर दोन्ही सेटअपचे यंत्रण पूर्ण करण्याच्या क्षमतेमुळे टर्निंग सेंटर आणि दोन टर्निंग स्पिंडल एकमेकांसमोर असणाऱ्या बहुउद्देशीय टर्निंग मशीनचा वापर केला जातो. ही मांडणी (कॉन्फिगरेशन) पार्टिंगच्या कामामध्ये फायदेशीर ठरते.
पहिल्या स्पिंडलमध्ये पहिल्या बाजूचे यंत्रण झाल्यानंतर, पार्टिंग होण्याआधी, दुसरा स्पिंडल पुढे येतो आणि कार्यवस्तूला पकडतो. आवश्यक असल्यास कार्यवस्तूला बाहेर काढतो. यामुळे पार्टिंगदरम्यान उच्च यंत्रण पॅरामीटर वापरता येतात आणि अतिरिक्त दृढता मिळते. यात पिंचिंगची शक्यता नसल्यामुळे जवळजवळ केंद्रापर्यंत यंत्रण चालू ठेवता येते. दुसऱ्या स्पिंडलवर दुसऱ्या बाजूचे यंत्रण आणि आवश्यक असल्यास पार्टिंग केलेल्या पृष्ठभागाचे फिनिशिंगही केले जाऊ शकते.
पार्ट ऑफ केलेल्या कार्यवस्तूची हाताळणी
पार्ट ऑफ केलेली कार्यवस्तू ही फिनिश झालेला यंत्रभाग असते. पार्ट ऑफ केल्यानंतर कार्यवस्तूची गुणवत्ता टिकविणे महत्त्वाचे असते. त्यानुसार अनलोडिंगची पद्धत आणि स्वयंचलनाचे नियोजनही तितकेच काटेकोरपणे आणि काळजीपूर्वक करणे आवश्यक आहे.
फिनिश झालेली कार्यवस्तू पार्ट ऑफ झाल्यानंतर (किंवा यंत्रण पूर्ण झाल्यानंतर काउंटर स्पिंडलमधून बाहेर आल्यानंतर) खाली पडेल आणि हाताने किंवा भांड्यामध्ये (कलेक्टर किंवा कॅचर), श्यूट किंवा आउटपुट कन्व्हेअर वापरून ती बाहेर काढली जाते. या कामासाठी आता रोबोचाही मोठ्या प्रमाणात वापर होत आहे. कार्यवस्तू जमा होणाऱ्या पात्राचे (कलेक्टर बास्केट) किंवा रोबोच्या बोटांचे डिझाइन करताना त्यात चिप अडकणार नाहीत आणि फिनिश झालेल्या कार्यवस्तूवर कोणतेही नुकसान होणार नाही, पोचे, खड्डे पडणार नाहीत, असा विचार करावा.
दुसऱ्या स्पिंडलवरील इजेक्टर आणि अनलोडरसारख्या इतर स्वयंचलन व्यवस्था, फिनिश झालेल्या कार्यवस्तू सहजपणे हाताळू शकतात.
चित्र क्र. 10 : X अक्षावरील पारंपरिक सरकवेग आणि Y अक्ष पार्टिंगचे संकल्पना चित्र
Y अक्ष वापरून केलेले पार्टिंग
Y अक्ष असलेल्या बहुउद्द्ेशीय (मल्टीटास्किंग) टर्निंग मशीनमध्ये Y अक्ष वापरून पार्टिंगची (चित्र क्र. 10) कामगिरी सुधारणे शक्य झाले आहे. सामान्य पार्टिंग करताना टूलची चाल X अक्षामध्ये असते आणि मुख्य यंत्रण बल, टूलच्या इन्सर्टच्या ओव्हरहँगिंग बिंदूवर कार्य करते. त्यामुळे यंत्रणासाठी आवश्यक असलेली दृढता ही टूलचा ओव्हरहँग आणि त्याच्या काटछेदावर अवलंबून असते. विशेषत: मोठ्या व्यासाच्या कार्यवस्तूंमध्ये टूल ओव्हरहँग, कार्यवस्तूच्या त्रिज्येद्वारे निश्चित केला जातो. टूलचा काटछेद, पार्टिंगच्या रुंदीच्या तुलनेत मर्यादित असल्यामुळे त्याला अधिक खोल करावे लागेल.
Y अक्ष पार्टिंगमध्ये, पार्टिंग टूलचा यंत्रण फेस, हत्यारधारकाच्या एंड फेसला समांतर असतो. त्याला Y अक्षावर कार्यवस्तूमध्ये चाल दिली जाते. अशा प्रकारच्या यंत्रणात, इन्सर्टवरील मुख्य कर्तन बलांना त्याच्या काटछेदाऐवजी ब्लेडच्या उभ्या अक्षाद्वारे समर्थन मिळते. ब्लेडच्या या वाढलेल्या दृढतेमुळे विरूपण आणि कंपने कमी होतात. यामुळे उत्पादकता आणि फिनिशमध्येही फायदा होतो. Y अक्ष पार्टिंगसाठी लागणारी योग्य ब्लेड, कटिंग टूल पुरवठादारांकडे उपलब्ध असतात.
9860821701
प्रदीप किरकोळे यांत्रिकी अभियंते आहेत. त्यांनी आय.आय.टी. मुंबई येथून उत्पादन अभियांत्रिकीमध्ये एम.टेक. पदवी घेतली आहे. मशीन टूलच्या टेक्नॉलॉजी अॅप्लिकेशनमधील कामाचा त्यांना जवळपास 37 वर्षांचा अनुभव आहे.