टायटॅनिअम आणि उष्णता प्रतिरोधक सुपर अलॉयसारखी (HRSA) काही मटेरियल यंत्रणासाठी क्लिष्ट असतात. या मटेरियलच्या यंत्रणामध्ये उच्च दाबाचे शीतक (हाय प्रेशर कूलंट, HPC) वापरण्याची संकल्पना काही युरोपिअन विद्यापीठांनी विकसित केली. अशा मटेरियलचे सुरक्षिततेसह किफायतशीरपणे यंत्रण करण्यावर या संकल्पनेचा मोठा प्रभाव पडत आहे. तो समजून घेण्यासाठी उपयुक्त ठरणारा हा लेख.
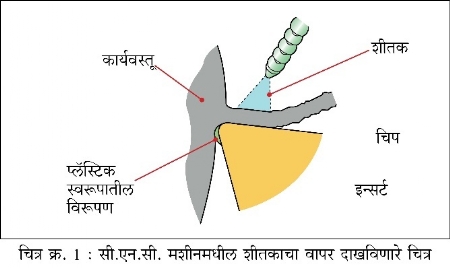
गेल्या काही वर्षांत ड्युप्लेक्स स्टेनलेस स्टील, कडा कठीण (एज हार्डनिंग) केलेले सुपर अलॉय, इन्कोनेल, इतर हीट रेझिस्टंट सुपर अलॉय (HRSA), टायटॅनिअम इत्यादी क्लिष्ट मटेरियलच्या यंत्रणामध्ये उच्च दाबाच्या शीतकाचे महत्त्व झपाट्याने वाढले आहे. अशा प्रकारच्या मटेरियलचे यंत्रण करण्यासाठी फक्त एक धारदार कर्तन कड (शार्प कटिंग एज) देणे आणि टूलचे तुलनेने कमी आयुर्मान स्वीकारणे, या पारंपरिक संकल्पनेपासून यंत्रण तंत्रज्ञान दूर गेले आहे. आता दीर्घकाळापर्यंत कर्तन धार सुरक्षित ठेवण्यासाठी चिपचा आकार नियंत्रित करणे आणि यंत्रण होणारा भाग थंड ठेवणे, ही संकल्पना पुढे आली आहे. यामुळे टर्निंग सेंटरसाठी बरेच कटिंग टूल उत्पादक, नॉझलद्वारा थेट कर्तन कडेवर शीतक सोडले जाईल असे हत्यारधारक (टूल होल्डर) उपलब्ध करून देऊ लागले आहेत. कर्तन कडेवर उच्च वेगाने निर्देशित केलेले उच्च दाबाचे शीतक (हाय प्रेशर कूलंट, HPC) वापरण्याची संकल्पना काही युरोपिअन विद्यापीठांनी विकसित केली आहे. याचा उपयोग विमान आणि मेडिकल उद्योगांमध्ये वापरल्या जाणाऱ्या टायटॅनिअम आणि उष्णता प्रतिरोधक सुपर अलॉयसारख्या (HRSA) यंत्रण करण्यासाठी अवघड मटेरियलच्या यंत्रणामध्ये करता येतो. आचेनच्या जर्मन विद्यापीठाने त्यांच्या प्रयोगशाळेत या विषयावर बरेच संशोधन केले आहे. अशा मटेरियलच्या प्रक्रियेदरम्यान सुरक्षित आणि किफायतशीरपणे यंत्रण करण्यावर या संकल्पनेचा इतका मोठा प्रभाव का पडत आहे, ते समजून घेण्यासाठी या मटेरियलच्या यंत्रणविषयक वैशिष्ट्यांविषयी या लेखात आपण जाणून घेणार आहोत.
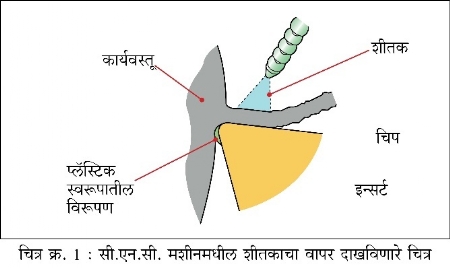
HRSA मटेरियलमध्ये औष्णिक वाहकता सामान्यत: कमी असल्यामुळे त्यात 'वर्क हार्डनिंग' होण्याची प्रवृत्ती अधिक असते. त्यामुळे कर्तन कडेवर उच्च तापमान आणि उच्च कर्तन बले निर्माण होतात, ज्यामुळे कर्तन कडेचे फार लवकर नुकसान होऊ शकते. टायटॅनिअममध्येही अशीच यंत्रणविषयक वैशिष्ट्ये आहेत आणि त्याशिवाय उच्च तापमानावर त्याची टूलच्या मटेरियलबरोबर रासायनिक प्रक्रियादेखील होऊ शकते.
पारंपरिक उपाय
1. उच्च +ve रेक असलेली धारदार कर्तन कड
2. गरम स्थितीत उच्च कठीणता (कमी CO%) आणि कडेचा चिवटपणा (टफनेस) उच्च असलेली (फाइन ग्रेन असलेली) ग्रेड वापरणे.
परंतु, पारंपरिक उपायांमुळे केवळ पारंपरिक परिणामच मिळाले. या मटेरियलची वर्क हार्डनिंग होण्याची प्रवृत्ती असली तरीही चिपचा प्रवाह इष्टतम (ऑप्टिमम) करणे गरजेचे होते.
जेव्हा कार्यवस्तूचे मटेरियल यंत्रणासाठी आव्हानात्मक असते अशावेळी उच्च दाबाचे शीतक वापरल्यामुळे पुढील फायदे मिळतात.
· उच्च यंत्रण सुरक्षा मिळते.
· यंत्रण प्रक्रियेमध्ये सातत्य येते.
· मशीन बंद पडण्याचे प्रमाण कमी होते.
· अधिक चांगल्या गुणवत्तेचे यंत्रभाग तयार होतात.
· यंत्रणास लागणारा वेळ कमी होतो.
आता आपण या सिद्धांतामागील संकल्पना तपासून पाहू आणि ती योग्य आहे की नाही ते ठरवू.
1. उच्च दाबाचे शीतक किंवा उच्च वेग असलेले शीतक
2. निर्देशित शीतक किंवा प्रवाही शीतक
3. इष्टतम वेगाने योग्य दिशेने सोडलेल्या शीतकामुळे स्वीकारार्ह आकाराच्या चिपच्या गुंडाळ्या बनण्यात मदत
HRSA, ड्युप्लेक्स स्टेनलेस स्टील, टायटॅनिअम अशा मटेरियलच्या यंत्रणामध्ये चिपच्या खाली कटिंग फ्लुइडचा उच्च वेगाने मारा केल्यावर चिप उचलल्या जातात आणि लहान गुंडाळ्यांच्या आकारात सहजपणे त्या बाहेर निघतात. कटिंग फ्लुइडचा उच्च दाबाने, उच्च वेगाने आणि योग्य दिशेत मारा केल्यास यंत्रणासाठी अवघड असलेल्या मटेरियलची यंत्रणक्षमता सुधारते हे आता सिद्ध झाले आहे.
चित्र क्र. 2
सामान्य शीतक प्रवाह
सी.एन.सी. मशीनमध्ये शीतक कसे वापरले जाते ते चित्र क्र. 1 मध्ये दाखविले आहे.
यंत्रण होणाऱ्या क्षेत्रात शीतकाचा केवळ मोठ्या प्रमाणातील प्रवाह पुरेसा नसतो. जर शीतकाचा प्रभावी उपयोग करावयाचा असेल, तर योग्यप्रकारे दिशा दिलेल्या, उच्च दाबांच्या जेटद्वारे त्याचा मारा करणे आवश्यक आहे. जेव्हा असे जेट, स्तरीय (लॅमिनर) प्रवाहामध्ये नियंत्रित केलेले असते, तेव्हा ते चिप आणि रेक फेस यांच्यातील संपर्क लांबी कमी करते. निर्माण होणारी उष्णता कशी वितरित होईल आणि वाहून नेली जाईल, टूलची किती प्रमाणात झीज होईल, चिप कशी तयार होईल आणि तुटेल, तसेच कर्तन कडेवर कार्यवस्तूचे मटेरियल किती प्रमाणात पसरेल, या सगळ्या घटकांवर शीतकाचा परिणाम होऊ शकतो. यंत्रण करण्यास आव्हानात्मक असलेल्या मटेरियलच्या बाबतीत हे विशेष महत्त्वाचे असते, कारण त्यात उष्णता आणि चिप नियंत्रणासाठी अतिरिक्त उपायांची आवश्यकता असते. उच्च दाबाचे शीतक चिपच्या खाली निर्देशित केल्यावर ते टूलच्या कडेवरील चिपचा संपर्क मोठ्या प्रमाणात कमी करते, याला कूलंट वेज इफेक्ट (चित्र क्र. 2 आणि 3) असे म्हणतात.
चित्र क्र. 3
शीतक वेज कशी मदत करते?
इन्सर्टचा वरचा पृष्ठभाग आणि चिपची खालची बाजू यादरम्यान शीतकाच्या उच्च वेगवान जेटद्वारे हायड्रॉलिक वेज तयार केली जाते. शीतक जेट, संपर्क क्षेत्रामध्ये (A) इन्सर्टला जागीच थंड (चित्र क्र. 3) करते. चिपला इन्सर्टच्या पृष्ठावरून त्वरित बाजूला नेऊन इन्सर्टची (B) झीज कमी करते, तसेच चिप लहान तुकड्यांमध्ये तोडण्यास आणि यंत्रण क्षेत्रापासून दूर नेण्यास मदत करते.
शीतकाचा वेग कसा वाढविला जातो?
स्तरमय (लॅमेलर) फ्लो
टूलमध्ये आपल्याला यंत्रण क्षेत्रावर फेसच्या वरच्या बाजूला आणि चिपच्या खाली निर्देशित केलेले, उच्च गतीचे समांतर लॅमेलर जेट तयार करण्यासाठी एका योग्य नॉझलची (चित्र क्र. 5) आवश्यकता असते. शीतकांसारख्या द्रवपदार्थांचा दाब, वेग आणि प्रवाह दर यांच्यातील संबंध दाखविणारा एक सिद्धांत (बर्नौली) आहे. जेव्हा द्रव पदार्थ मोठ्या व्यासाच्या नलिकेमधून, तुलनेने लहान व्यासाच्या नलिकेत जातो, तेव्हा उच्च वेगाचे जेट मिळविण्यासाठी लागणारा प्रवाह दर कमी असतो. आपण बागेत वापरतो त्या रबरी नळीच्या टोकाला एक नॉझल लावल्यामुळे तोच परिणाम मिळतो. नॉझलच्या बाह्य छिद्राचा (आउटलेट) व्यास जितका अधिक, तितका विशिष्ट दाबासाठी लागणारा प्रवाह दर अधिक असतो. उच्च दाबाच्या शीतकामध्ये केवळ दाब नसतो, तर त्यात पंपापासून टूलपर्यंत शीतकाचा प्रवाह दर आणि शीतक ज्यातून बाहेर पडते त्या छिद्राचा आकार, अशी संपूर्ण प्रणाली समाविष्ट असते.
शीतक बाहेर पडण्याचे छिद्र (हत्यारधारकावरील नॉझल) कमी व्यासाचे केल्याने नॉझलमधून बाहेर येणाऱ्या द्रवाच्या गतीमध्ये वाढ होते. नॉझल जितके मोठे असेल, तितका नलिकेमधील द्रवाचा प्रवाह दर अधिक असायला हवा. शिवाय नॉझलच्या संख्येवर (एकंदर आउटलेट क्षेत्र) द्रवाचा परिणामी दाब अवलंबून असेल. (यात नॉझल कार्यक्षमता आणि द्रव घनता हे घटकदेखील आहेत). चित्र क्र. 4 आणि 5 पहा. इष्टतम वेग मिळविण्यासाठी, मशीन टूलमध्ये 50 ते 80 किलो/सेमी2 दाबापर्यंत कार्य करू शकणारी शीतक प्रणाली असली पाहिजे. टर्निंग करताना, स्तरीय प्रवाह आणि उच्च गती असलेले अचूक शीतक जेट तयार करण्यासाठी, 1 मिमी. आकाराचे छिद्र असलेल्या नॉझलची शिफारस केली जाते. तसेच, किमान 20 लिटर प्रति मिनिटाचा प्रवाह दर योग्य समजला जातो. यासाठी 0.6 ते 1.4 मिमी. आकाराची बाह्य (आउटलेट) छिद्रे असलेली, बदलता येण्याजोगी, नॉझल उपलब्ध आहेत.
चित्र क्र. 4
चित्र क्र. 5 : हत्यारधारकातील शीतक नॉझल
कार्यवस्तूच्या बहुतेक मटेरियलवर इष्टतम टर्निंग, मिलिंग आणि ड्रिलिंग करताना उच्च कामगिरी आणि परिणाम मिळविण्यासाठी 50 ते 80 बार इतक्या शीतक दाबाची शिफारस केली जाते. टूलमध्ये कार्यरत असलेल्या प्रत्येक 1 मिमी. व्यासाच्या नॉझलसाठी, दाब कायम ठेवण्यासाठी 5 लीटर प्रति मिनिट शीतक प्रवाह दर आवश्यक असतो. दाब वाढविण्यासाठी आणि उपलब्ध प्रवाह दराचा योग्य वापर करण्यासाठी नॉझलच्या आउटलेटच्या आकारातील फरकाचा वापर करावा. तर, मल्टी इन्सर्ट टूलिंगद्वारा केलेल्या मिलिंगमध्ये, वापरात असलेल्या नॉझलच्या संख्येच्या हिशोबाने उच्च प्रवाह दर आवश्यक असतो.
लहान बाह्य छिद्रे असलेली नॉझल वापरून प्रवाहाची गरज कमी केली जाऊ शकते.
· 0 ते 10 लीटर प्रति मिनिट शीतक प्रवाहासाठी - 1 मिमी. व्यासाचे छिद्र
· 10 ते 20 लीटर प्रति मिनिट शीतक प्रवाहासाठी - 0.8 मिमी. व्यासाचे छिद्र
· 20 पेक्षा जास्त लीटर प्रति मिनिट शीतक प्रवाहासाठी - 0.6 मिमी. व्यासाचे छिद्र
ड्रिलिंगमध्ये, फ्ल्यूटमधून चिप चांगल्याप्रकारे बाहेर काढण्याची खात्री करण्यासाठी दाबाइतकाच प्रवाहही महत्त्वाचा असतो. उच्च दाब असला की, चांगला प्रवाह मिळतो आणि म्हणूनच ड्रिलिंग प्रक्रिया सुरक्षित व्हायला मदत होते. शीतकाचा प्रवाह जास्तीतजास्त मिळण्यासाठी ड्रिल व्यास आणि पंप क्षमतेबरोबर शीतक छिद्राचा आकार अनुकूलित केला जातो. फ्ल्यूटमधून चिप कार्यक्षमरीतीने बाहेर काढण्यासाठी तुलनेने उच्च प्रवाह दर आवश्यक असतो.
ढोबळमानाने 12 मिमी.पेक्षा कमी ड्रिलसाठी, प्रति मिनिट 16 लिटर प्रवाह दर पुरेसा आहे. 12 ते 40 मिमी. ड्रिलसाठी, प्रति मिनिट 30 लिटर या प्रवाह दराने सुरुवात करायला हरकत नाही. हे तत्त्व वेगवेगळ्या मशीनमध्ये वापरल्याची उदाहरणे चित्र क्र. 6 मध्ये दिली आहेत. चित्रामध्ये दाखविल्याप्रमाणे उच्च दाबाचे शीतक उच्च वेगाने निर्देशित केल्याने आपण पुढील गोष्टींची अपेक्षा करू शकतो.
· समान यंत्रण पॅरामीटरसाठी: टूलच्या आयुर्मानात + 50% वाढ
· कर्तन वेग 20% (50 ते 60 मी./मिनिट) वाढविता येतो. यामुळे आवर्तन काळात सुधारणा होते.
जेव्हा इंडेक्सेबल इन्सर्ट मिलिंग कटर आणि 40 मिमी.पेक्षा जास्त व्यासाचे ड्रिल वापरले जातात, तेव्हा कमीतकमी 50 लिटर प्रति मिनिट क्षमतेचा शीतक पंप वापरण्याची शिफारस केली जाते. क्षमता जितकी जास्त, तितके चांगले. किमान शीतक प्रवाह दर 30 लिटर/मिनिट आहे. परंतु, प्रति मिनिट 75 लिटर देणारे स्टँडर्ड पंपदेखील उपलब्ध आहेत.
चित्र क्र. 6
उच्च दाबाची शीतक प्रणाली कशी सुरू करावयाची?
मशीन शॉपमध्ये आधीपासून बसविलेल्या बहुतेक आधुनिक मशीन टूलना उच्च दाबाचा पंप जोडता (रेट्रोफिटिंग) येतो. परंतु असा बदल करताना निश्चितपणे काही गडबड होऊ शकते. जो कंत्राटदार हे अपग्रेडेशनचे काम करणार असेल, त्याने सीलिंग, शीतक गळती, सध्याच्या नियंत्रकामध्ये (कंट्रोलर) शीतकासाठी नवीन M कोड जोडणे, इत्यादी बाबतीत लक्ष देणे आवश्यक आहे. नवीन प्लांट आणि उपकरणांची खरेदी करतानाच मशीनला उच्च दाबाचे शीतक असलेल्या प्रणालीने सुसज्ज करणे योग्य असते. यामुळे खर्च कमी होतो, तसेच प्रोग्रॅम आणि यंत्रण माहिती (डाटा) यांच्यात नवीन तंत्रज्ञानाची क्षमता निश्चितपणे प्रतिबिंबित होण्यास मदत होईल. सुरुवातीपासूनच शॉप फ्लोअरचे संपूर्ण आयोजन करण्याचा हा एक फायदा आहे.
नवीन मशीन खरेदी करताना पुढील गोष्टी सुनिश्चित कराव्यात.
· मशीनची क्षमता : मशीन 80 बारपर्यंतच्या दाबावर चालविण्यासाठी सक्षम असावे. सील आणि व्हॉल्व्ह तपासून पहावेत.
· उच्च दाब पर्याय : मशीनमध्ये शीतक पंप चालविण्यासाठी योग्य M कोड उपलब्ध असल्याची खात्री करावी.
· पंपाची निवड : व्हॉल्युम क्षमता निश्चित करणे आवश्यक आहे. बऱ्याचदा दाब तपासला जातो, परंतु व्हॉल्युमसुद्धा तपासणे गरजेचे असते. सामान्य टर्निंग प्रक्रियेसाठी पंप व्हॉल्युम 20 लीटर/मिनिट इतका असावा.
· बहुउद्देशीय मशीनसाठी किंवा जेव्हा मोठ्या व्यासाची ड्रिल लेथवर वापरली जातात, तेव्हा जास्त प्रमाणात शीतकाची आवश्यकता असते. या कामांसाठी प्रति मिनिट 40 ते 80 लीटरपर्यंत पंप व्हॉल्युम ठेवण्याची शिफारस केली जाते.
· शीतकाची जास्त मात्रा आवश्यक असलेल्या कामांसाठी, ज्यामध्ये बदलता दाब (व्हेरिएबल प्रेशर) उपलब्ध असेल, असा एक पर्याय मशीनमध्ये असणे खूप उपयुक्त ठरू शकते.
उपाय
आज, उच्च दाबाचे शीतक वापरून यंत्रण प्रक्रिया सुधारण्यासाठी लागणाऱ्या दोन मुख्य मूलभूत अटींची पूर्तता आधीपासूनच केलेली असते. बऱ्याच आधुनिक सी.एन.सी. मशीनमध्ये मानक किंवा पर्यायी म्हणून कमीतकमी 70 बारच्या दाबावर शीतक पुरवठा दिलेला असतो. बऱ्याच मशीनमध्ये उच्च दाबाच्या शीतक पुरवठ्यासाठी अनुकूल हत्यारधारक प्रणालीसुद्धा दिलेली असते. त्यामुळे, सर्वोत्कृष्ट टूलिंग प्रणालीचा वापर करून मशीन टूलच्या उपलब्ध क्षमतेचा अधिकाधिक वापर कसा करता येईल, हेच आव्हान आहे. उत्पादक वेळेचा सर्वोत्कृष्ट समतोल साधणे हा यामागील हेतू आहे. मशीन उच्च वेगाने चालविणे पण ते असंख्य वेळा बंद पडणे किंवा अनावश्यक इतक्या कमी वेगाने चालविणे, या दोन्ही पर्यायांपेक्षा योग्य आणि सातत्यपूर्ण असा यंत्रण दर केव्हाही चांगला ठरतो.
उच्च दाबाच्या शीतकाने सुसज्ज असलेली टूल हाताळणे, हे ज्यात शीतक जेटसाठी ऑपरेटरला कोणतीही सेटिंग करावी लागत नाहीत, अशा सामान्य टूल हाताळण्याइतकेच सोपे आणि कार्यक्षम आहे. बाह्य आणि अंतर्गत अशा दोन्ही प्रक्रियेसाठी, तसेच ग्रूव्हिंग, प्रोफाइलिंग आणि पॉकेटिंग यांच्यासाठीही हे फायदेशीर ठरते.
9359104060
रवि नाईक यांना टूलिंग क्षेत्रातील 40 हून अधिक वर्षांचा अनुभव असून ते टूलिंग आणि मशीनिंग अॅप्लिकेशनविषयक सल्लागार आहेत.