बरीच उत्पादने, त्यांचे भाग, त्यांचे डिझाइन बऱ्याच वर्षांपूर्वी झाल्याने, कंपनीतील नवनवीन वाढत्या कामाच्या व्यापामुळे त्याच्यावर संशोधन आणि विकसन करायला वेळ मिळत नाही आणि उत्पादन तर चालूच असते. त्यामुळे डिझाइनमधील अशा किरकोळ सुधारणा करून प्रक्रियेत पर्याय निर्माण करून स्वावलंबन आणि बचत करणे शक्य झाले.
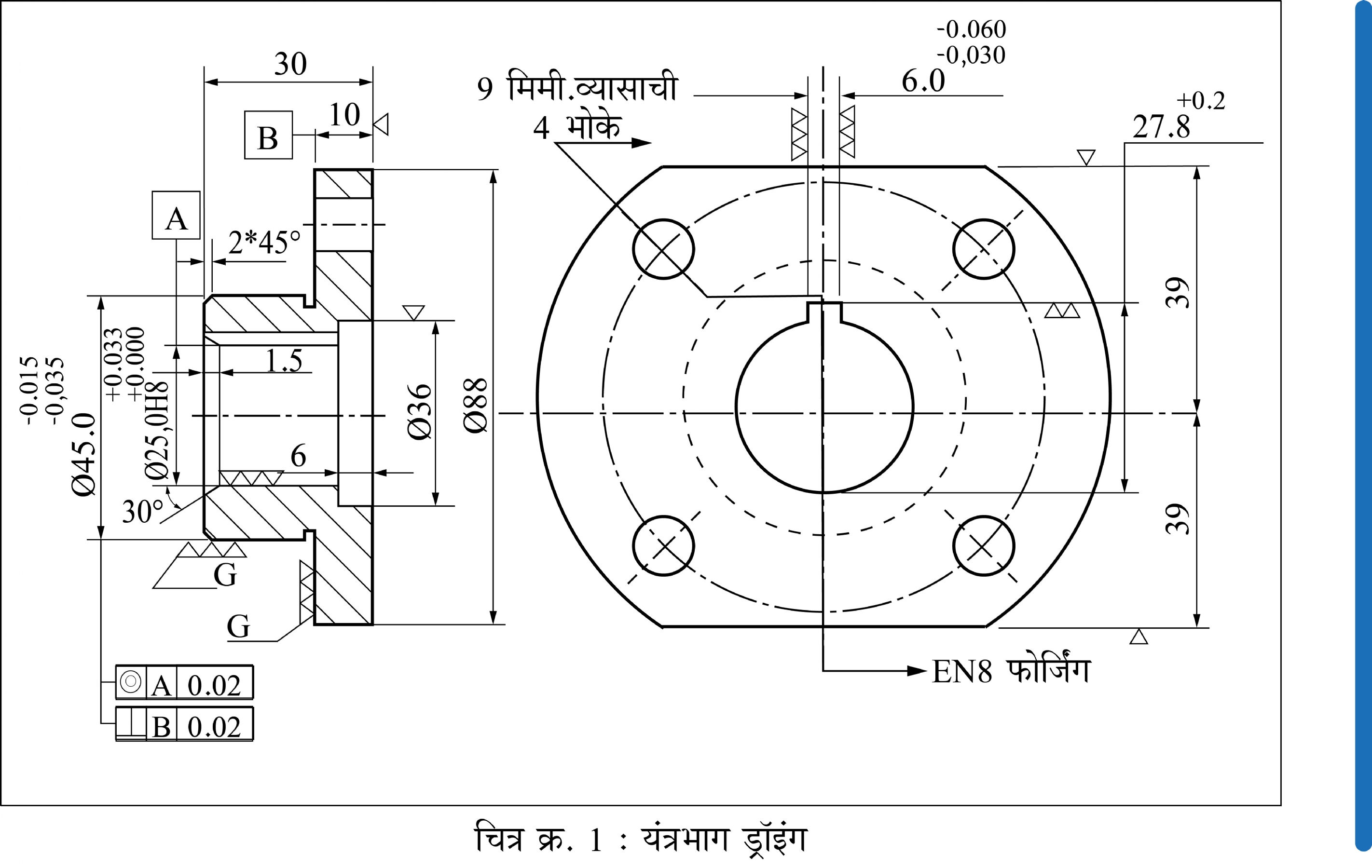
मी गेली 10-12 वर्षे सल्लागार क्षेत्रात असल्याने विविध कामांसाठी तसेच अडीअडचणींवर मार्गदर्शनासाठी माझा बऱ्याच कंपन्यांशी संबंध येतो. त्यातीलच एका कंपनीच्या मालकांबरोबर अधूनमधून सल्लामसलत होत असे. त्यांच्याकडे विविध देशी परदेशी कंपन्याच्या यंत्रभागांची आव्हानात्मक कामे होती. यावेळी एका परदेशी कंपनीच्या पंप अॅसेम्ब्लीचा एक यंत्रभाग विकसित करण्याचे काम चालू होते. त्यातील काही समस्यांविषयी चर्चा करताना त्यांनी त्या यंत्रभागाची ठरविलेली उत्पादन प्रक्रिया सांगितली. या यंत्रभागाची दरमहा मागणी 5000 नग इतकी होती. सदर यंत्रभागाचे तपशील पुढे दिले आहेत.
हा यंत्रभाग स्टील फोर्जिंगचा होता. नंतर त्याच्यावर सर्व प्रक्रिया करावयाच्या होत्या. त्यामुळे सुरुवातीला काही महिने त्यांच्या फोर्जिंग पुरवठादाराकडून कच्चा माल मिळणार आणि नंतर आम्ही त्यावर फोर्जिंगची सुधारणा करावयाची असे ठरविले. सुरुवातीला यंत्रभागाच्या फिनिश ड्रॉइंग (चित्र क्र. 1) आणि फोर्जिंग ड्रॉइंगचा (चित्र क्र. 2) एकत्रित प्राथमिक अभ्यास करून सर्वसाधारण उत्पादन प्रक्रिया (तक्ता क्र. 1) ठरविली.
चित्र क्र. 2
उत्पादन प्रक्रिया प्रवाहउत्पादनाला सुरुवात करताना असे लक्षात आले की, कारखान्यात 12 तासांची शिफ्ट असल्याने मासिक 5000-5500 यंत्रभाग होण्याच्या दृष्टीने रोज अंदाजे 200-220 नग होणे आवश्यक होते. अभ्यासाअंती असे दिसले की, प्रत्येक ऑपरेशनचा आवर्तन काळ (सायकल टाइम) अंदाजे 2.5 मिनिटे होता. आमच्याकडे कीवे शेपिंग/मिलिंग, फ्लॅट फेस मिलिंग आणि उष्णतोपचार (हीट ट्रीटमेंट) या सुविधा नसल्याने ती कामे बाहेर देऊन, उरलेली कामे आमच्या कारखान्यात करण्यास सुरुवात झाली. आतमध्ये होणाऱ्या कामांचे व्यवस्थित नियोजन आणि निरीक्षण चालू असल्याने काही अडचण नव्हती. तसेच कीवे आणि उष्णतोपचार प्रक्रियेसाठीही काही अडचण येण्याची शक्यता नव्हती. परंतु, फ्लॅट फेस मिलिंगचे काम नियोजित वेळेत होईना. कारण त्या कारखान्यात 8 तासांची एक शिफ्ट चालू होती. बाहेर दिलेल्या कामात विलंब झाल्याने त्यानंतरच्या पुढील शेवटच्या कामांवर परिणाम होणार होता. उत्पादन उद्दीष्टपूर्तीवर प्रश्नचिन्ह निर्माण झाले.
मिलिंग करणाऱ्या कंपनीशी चर्चा करून, अडचणीची कल्पना देऊन त्यांना मिलिंगसाठी आणखी दोन तास काम चालू ठेवण्याची गरज स्पष्ट केली. त्यांनीही होकार देत अतिरिक्त काम चालू ठेवले आणि वेळेवर नियंत्रण ठेवून दररोज 200-210 नगाचे उत्पादन मिळू लागले. त्यामुळे पहिल्या दोन महिन्यांच्या परिश्रमानंतर प्रतीमहिना 5000 नग होऊन पुरवठा चालू झाला. या सर्व प्रक्रियेत सुरळीतपणा आल्याने आणि 6-7 महिन्यांनी ग्राहकाकडे एकदम व्यवसाय वाढल्याने नंतर त्याची मागणी दरमहा 7000 नग एवढी झाली. त्यामुळे आम्ही त्यावर नव्याने अभ्यास करून नियोजन केले. तेव्हा असे लक्षात आले की, वाढीव मागणीच्या दृष्टीने आमच्याकडील कामाचे योग्य नियोजन करून ते पूर्ण करणे शक्य होते. कीवे करणाऱ्या कंपनीनेसुद्धा उत्पादन वाढवून देण्याचे मान्य केले. पण फ्लॅट फेस मिलिंगचे काम वाढवून मिळणे शक्य नव्हते. त्यामुळे यावर काय मार्ग काढता येईल यासंदर्भात चर्चा सुरू झाली. ग्राहकाकडून आलेल्या पंप अॅसेम्ब्लीच्या दर्शनीभागाच्या संदर्भ ड्रॉइंगवरून असे लक्षात आले की, या यंत्रभागावरील फ्लॅट फक्त फाउलिंग टाळण्यासाठी रिलीव्ह म्हणून आहेत आणि ते फारसे महत्त्वाचे नसावेत. याप्रमाणे कार्यवस्तूचे नवीन पर्यायी ड्रॉइंग (चित्र क्र. 3) करून ग्राहकाकडून त्याला मान्यता मिळते का यासाठी प्रयत्न करण्याचे ठरले.
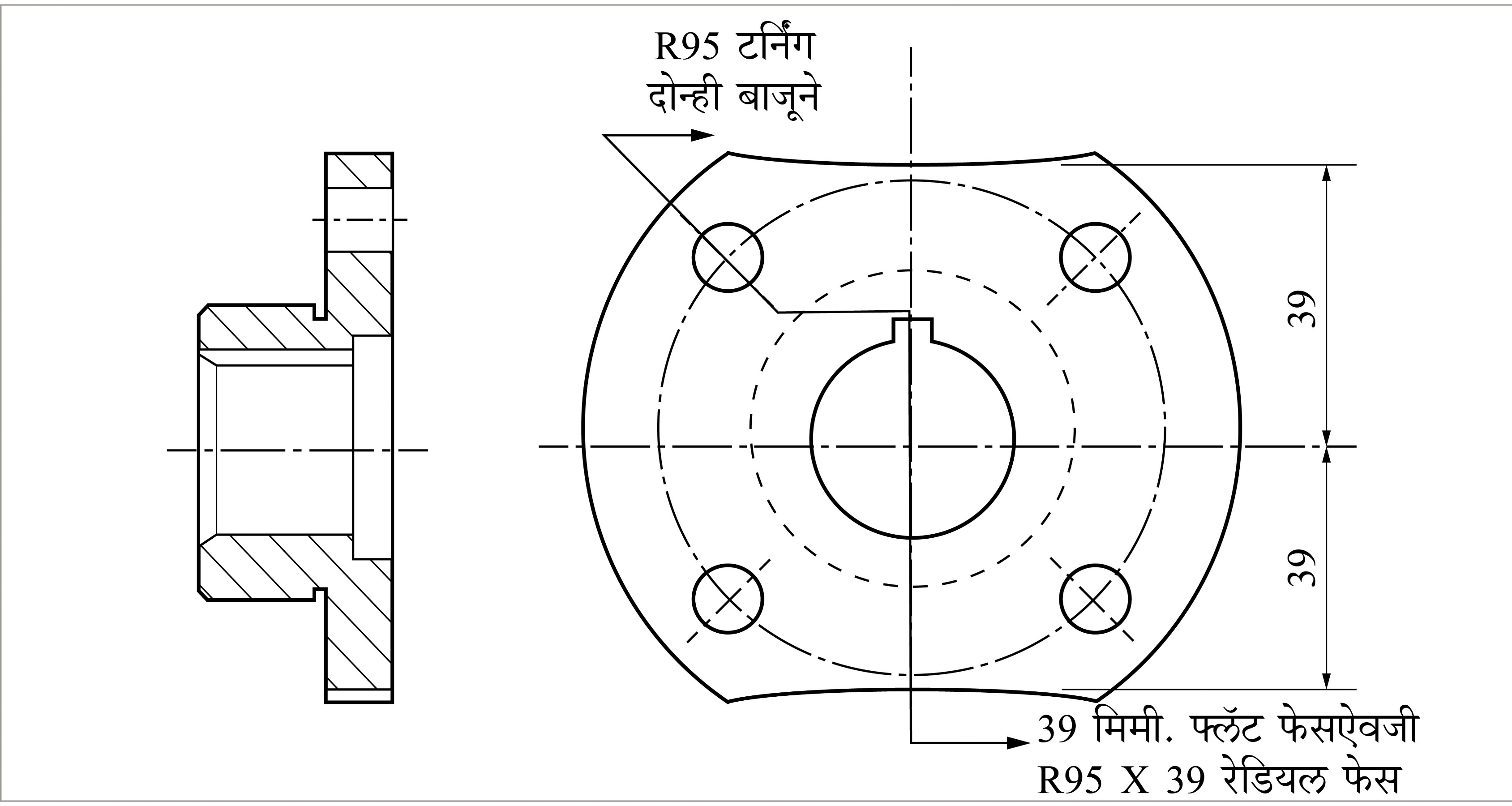
चित्र क्र. 3
पर्यायी ड्रॉइंगमध्ये मिलिंगऐवजी टर्निंग ऑपरेशनद्वारे रिलीव्ह करून, ते काम आतमध्ये करण्याचे ठरले. पर्यायी ड्रॉइंग पाठविताना ग्राहकाला मिलिंग ऑपरेशन, मशीन उपलब्धता ही अडचण स्पष्ट करण्यात आली. आमच्या सुदैवाने ग्राहकाला निकड असल्याने 10-12 दिवसांत ग्राहकाकडून थोड्याफार सुधारणा करून मान्यता मिळाली आणि नवीन ड्रॉइंगप्रमाणे एक लॉट पाठविण्याविषयी पत्रही मिळाले. परवानगी देताना त्यांनी स्पष्ट केले की, ड्रॉइंग बदलामुळे पंपाची अॅसेम्ब्ली कार्यक्षमता आणि मुख्य म्हणजे दर्शनी भागावर काही परिणाम होत नव्हता. उलट पंपाचे बाह्यरूप (अॅस्थेटिक्स) अधिक चांगले झाल्याचा त्यांनीउल्लेख केला.
खरं म्हणजे ग्राहकाने पर्यायी ड्रॉइंगप्रमाणे टर्निंग रिलीव्ह भागाला (पोर्शन) मान्यता दिल्याने सदर काम सी.एन.सी. मशीनवर करणे सहज शक्य होते. पण त्याकरिता एक सी.एन.सी. मशीन अडकून पडले असते. तसेच प्रति कार्यवस्तू खर्चाचा विचार करून ते आटोक्यात ठेवणेही गरजेचे होते. पारंपरिक (कन्व्हेन्शनल) मशीनच्या सेटअपमध्ये नवीन 4-5 सी.एन.सी. मशीन असल्याने पूर्वीच्या जुन्या 2-3 लेथ मशीन फारशा कामात वापरल्या जात नसल्याने त्या बाजूला अडगळीत पडल्यासारख्याच होत्या. क्वचित अडचणीच्यावेळी किरकोळ कामासाठी त्यांचा वापर होत असे.
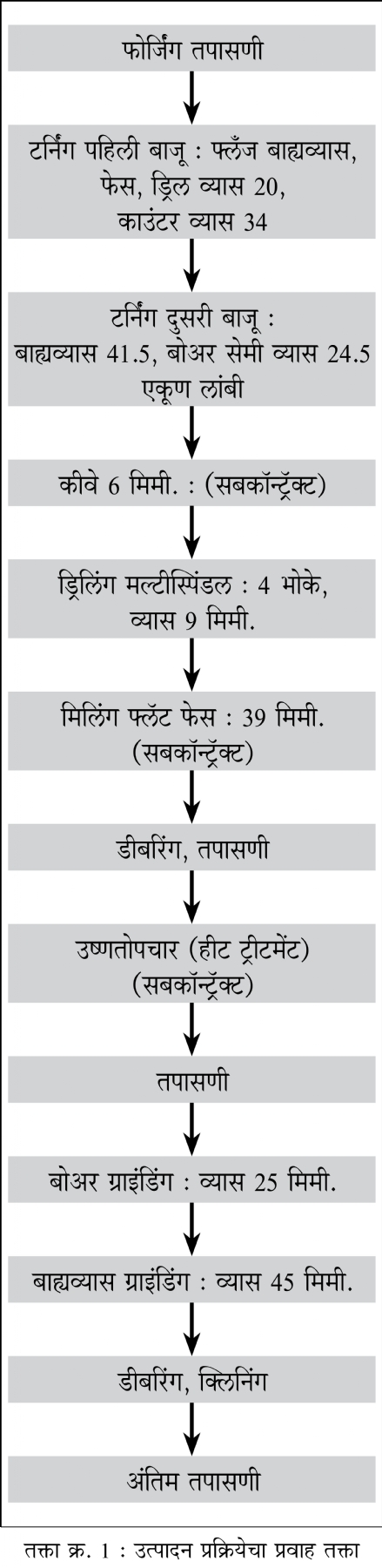
आता आमचे काम अधिक सोपे झाले. त्यातलाच एक साडे पाच फुटी लेथ उत्पादनाच्या दृष्टीने त्याचे आवश्यक रीकंडिशनिंग, देखभाल करून तयार केला. त्यावर टर्निंग ऑपरेशन करण्याचे ठरविले. त्याप्रमाणे एकावेळी 8 कार्यवस्तू होऊ शकतील असे फिक्श्चर तयार केले आणि त्यावर सुरुवातीला 25-30 यंत्रभाग ट्रायल म्हणून केले. फिक्श्चरमध्ये काही आवश्यक सुधारणा (चित्र क्र. 4 आणि 5) केल्या. कारण आम्हाला प्रति महिना 7000 यंत्रभाग म्हणजे प्रतिदिन 275-280 यंत्रभाग करणे आवश्यक होते. त्यामुळे टर्निंगचे हे काम प्रति यंत्रभाग 2 ते 2.25 मिनिटांतच संपवायचे होते. नवीन पर्यायी यंत्रभागाच्या रेडियल टर्निंगसाठी केलेल्या फिक्श्चरमध्ये मल्टी लोडिंग तत्त्वाप्रमाणे एकाचवेळी 8 यंत्रभाग Ø42 बाह्यव्यासामध्ये (OD) बसवून Ø 9 मिमी.च्या भोकामध्ये पिन टाकून त्याचे पोझिशनिंग केले आणि सेंटर क्लॅम्पिंग केले. तसेच ड्रॉइंगवरील त्रिज्येनुसार एका बाजूचे टर्निंग केले. एक बाजू झाल्यावर सेंटर क्लॅम्प सैल करून C क्लॅम्प बाजूला काढून सर्व यंत्रभाग बाजूला काढून परत दुसऱ्या बाजूच्या टर्निंगसाठी पूर्वीप्रमाणेच प्रत्येक यंत्रभाग लोकेट, पोझिशनिंग आणि सेंटर क्लॅम्पिंग करून रेडियस टर्निंग पूर्ण केले. अशाप्रकारे 8 यंत्रभागांसाठी अंदाजे 17 मिनिटे वेळ लागल्याने प्रत्येक तासाला 25-26 यंत्रभाग याप्रमाणे 12 तासाच्या शिफ्टमध्ये 275-280 यंत्रभाग व्यवस्थित, सुरळीतपणे होऊ लागले आणि महत्त्वाची मिलिंगची अडचण दूर झाली.
चित्र क्र. 4 : मूळ ड्रॉइंगप्रमाणे दोन्ही फ्लॅट फेस मिलिंगसाठी फिक्श्चर
इतर कामांचे नियोजन करताना सी.एन.सी. टर्निंगची दोन्ही कामे काटेकोर मापांची अपेक्षा असल्याने वेळखाऊ होती. पण आणखी एका सी.एन.सी.वर व्यवस्था करून उत्पादन वाढविले. ड्रिलिंगसाठी मल्टीस्पिंडल जिग असल्याने प्रति यंत्रभाग वेळ खूप कमी म्हणजे 1.5 मिनिटे इतका असल्याने तिथे उत्पादन वाढवायला सोपे गेले. सर्वात शेवटच्या बाह्यव्यासाच्या ग्राइंडिंग आणि बोअर ग्राइंडिंगसाठी आधी बाहेरून येणाऱ्या यंत्रभागाची प्रतीक्षा करावी लागे. त्यामुळे त्यात वाया जाणारा वेळ, पाठपुरावा यामुळे उद्दिष्टपूर्तीवर परिणाम व्हायचा. पण आता बरीचशी कामे कारखान्यातच होऊ लागल्याने उत्पादनात सुरळीतपणा आला.
केवळ कारखान्यातील एका अडगळीत पडलेल्या लेथचा उपयोग करून मिलिंगच्या समस्येवर मार्ग काढून परावलंबित्व कमी झाल्याने नंतर 1-2 महिन्यांत प्रति महिना 7000 यंत्रभागांचा नियमित पुरवठा होऊ लागला.
चित्र क्र. 5 : पर्यायी ड्रॉइंगप्रमाणे दोन्ही बाजू रेडियस टर्निंगसाठी फिक्श्चर
निष्कर्ष आणि फायदे
1. परावलंबन टाळून स्वावलंबन
साध्य झाले.
2. बाहेरून येणाऱ्या यंत्रभागांच्या प्रतिक्षेचा वेळ वाचला.
3. ग्राहकाला वेळेत मालाचा पुरवठा करणे शक्य झाले.
4. मिलिंगऐवजी टर्निंग कंपनीमध्येच केल्याने प्रति यंत्रभाग 2 रूपये
प्रमाणे प्रति महिना 14,000 रूपये बचत झाली.
5. बाहेरून येणाऱ्या मालाची रोजची वाहतूक वाचल्याने प्रति महिना 3000 रूपये बचत झाली.
तात्पर्य : बरीच उत्पादने, त्यांचे भाग, त्यांचे डिझाइन बऱ्याच वर्षांपूर्वी झाल्याने, कंपनीतील नवनवीन वाढत्या कामाच्या व्यापामुळे त्याच्यावर संशोधन आणि विकसन करायला वेळ मिळत नाही आणि उत्पादन तर चालूच असते. त्यामुळे डिझाइनमधील अशा किरकोळ सुधारणा करून प्रक्रियेत पर्याय निर्माण करून स्वावलंबन आणि बचत करणे शक्य झाले.
9922152466
[email protected]
अशोक कुलकर्णी यांत्रिकी अभियंते असून, त्यांना डिझाइन, विकसन, जिग्ज आणि फिक्श्चर्स, एस.पी.एम. तसेच, यंत्रण क्षेत्रातील 40 वर्षांचा प्रदीर्घ अनुभव आहे. गेली 10-12 वर्षे विविध कंपन्यांसाठी आणि इंजिनिअर समूहासाठी ते सल्लागार म्हणून काम करीत आहेत.