लघु मध्यम उद्योजकांना अपेक्षित दर्जाचे उत्पादन करण्यासाठी काही वेळेला विशिष्ट अत्याधुनिक सी.एन.सी. मशीनची गरज निर्माण होते. परंतु प्रत्येक वेळेला ती खरेदी आर्थिक दृष्ट्या परवडणारी नसते. अशीच समस्या आलेल्या एका उत्पादकाला रोल टर्निंग कामासाठी हेवी ड्युटी पारंपरिक लेथचे त्यांच्या गरजेनुसार सी.एन.सी. लेथमध्ये रूपांतर करून कसा फायदा झाला, याबाबत सखोल माहिती देणारा लेख.
सुमारे 3-4 वर्षांपूर्वी आमचे एक ग्राहक रोल टर्निंगच्या कामासंबंधात आम्हाला भेटायला आले होते. हे काम ते त्यांच्या पारंपरिक लेथ मशीनवर (चित्र क्र. 1) करीत होते. कार्यवस्तूचा व्यास सुमारे 500 मिमी. आणि लांबी सुमारे 3 मीटर असल्याने पारंपरिक लेथ मशीनवर त्यांना याचे यंत्रण करण्यासाठी सुमारे 50 ते 60 तास लागायचे. जास्त उत्पादनक्षमतेसाठी 30 HP पेक्षा जास्त स्पिंडल पॉवर आवश्यक होती, परंतु ग्राहकाकडील पारंपरिक लेथ 15 HP स्पिंडल पॉवरचा होता. रोल टर्निंगसाठी त्यांना जास्तीतजास्त स्पिंडल वेग 6-7 आर.पी.एम.च्या आसपास मिळत होता, जो खूपच कमी होता. हा वेग 30 आर.पी.एम.पेक्षा जास्त असायला हवा होता.
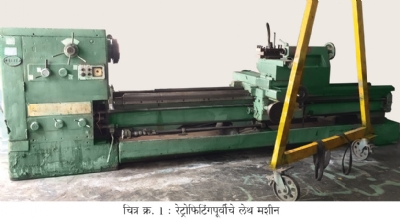
या कामासाठी सर्व दृष्टीने परिपूर्ण अशा सी.एन.सी. लेथ मशीनची किंमत सुमारे 80 लाख रुपये होती आणि ती त्यांना परवडणारी नव्हती. त्यामुळे आम्ही ग्राहकाची नेमकी निकड काय आहे याचा अभ्यास केला. त्यानंतर संबधित ग्राहकाला हेवी ड्यूटी पारंपरिक लेथचे सी.एन.सी. लेथमध्ये रेट्रोफिटिंग करून घेण्याची शिफारस केली. आम्ही त्यांना आश्वासन दिले की, त्यासाठी लागणारा खर्च नव्या मशीनच्या तुलनेत 50 टक्क्यांहून कमी असेल आणि मशीनची कामगिरी परिपूर्ण सी.एन.सी. मशीनशी 90 टक्क्यांपर्यंत जुळवून देण्यात येईल. ढोबळमानाने, सी.एन.सी. रेट्रोफिटिंगनंतर यंत्रणवेग आणि सरकवेग यासारखे यंत्रणाचे पॅरामीटर वाढवून कोणत्याही मॅन्युअल लेथची उत्पादकता सामान्यतः तिप्पट करता येते.
ग्राहकाकडे सध्या रोल टर्निंगसाठी जे लेथ मशीन वापरले जात होते, त्याचेच रेट्रोफिटिंग करणे हा पहिला पर्याय होता. परंतु त्या लेथ मशीनच्या डिझाइनचा अभ्यास केल्यानंतर त्याची अयोग्यता आमच्या लक्षात आली. रेट्रोफिटेड लेथची कामगिरी निश्चितपणे मशीनच्या मूलभूत प्रकारावर आधारित असते. रेट्रोफिटिंगसाठी पारंपरिक लेथ निवडताना त्याला गिअर असलेला हेडस्टॉक असणे, मशीनच्या मूलभूत संरचनेतील बेड आणि स्लाइड पुरेसे भक्कम असणे आणि टेलस्टॉकच्या क्विलचा व्यास 100 मिमी. पेक्षा अधिक असणे, या गोष्टी महत्त्वाच्या असतात.
गिअर असलेला हेडस्टॉक असला म्हणजे स्पिंडल मोटरची अधिकतम शक्ती स्पिंडलला मिळते. डायरेक्ट किंवा पुली/बेल्ट प्रकारच्या ड्राइव्हमध्ये शक्तीचे पारेषण कमी होते. त्यांच्या मशीनमध्ये हेडस्टॉकसाठी कोन पुली प्रकारची स्पिंडल ड्रायव्हिंग सिस्टिम होती आणि बेड आणि स्लाइड अत्यंत कमकुवत होते. त्यामुळे बाजारामध्ये हेवी ड्युटी लेथ मशीन शोधण्याचा निर्णय घेण्यात आला. आम्ही सगळ्यांनी मिळून गिअरसह हेडस्टॉक असलेला हेवी ड्यूटी लेथ शोधला आणि रेट्रोफिटिंगची प्रक्रिया सुरू केली.
रेट्रोफिटिंग प्रक्रिया
पारंपरिक लेथ, सी.एन.सी.मध्ये रूपांतरित करण्यात काही विशिष्ट प्रक्रिया असते आणि रेट्रोफिटिंगदरम्यान जुन्या किंवा वापरलेल्या मशीनच्या जवळजवळ प्रत्येक भागामध्ये सुधारणा (अपग्रेडेशन) केली जाते. उदाहरणार्थ, दोन्ही अक्षांचे लीड स्क्रू, दोन्ही अक्षांचे फीड गिअर बॉक्स, वायपर, शीतक प्रणाली, वंगण प्रणाली इत्यादी गोष्टी सुधारित घटकांसह बदलल्या जातात. ग्राहकाकडील लेथ आणि त्यावर जे काम करावयाचे ठरले होते, त्यासाठी आवश्यक असलेले नियंत्रक (चित्र क्र. 3) आणि सर्व्हो मोटर यांची निवड करणे, हे सर्वात प्रथम प्राधान्याचे काम होते. आम्ही शोधलेला लेथ खूपच अवजड होता आणि त्यात जे यंत्रण करावयाचे होते, त्यासाठी उच्च टॉर्क असलेल्या मोटरची आवश्यकता होती.
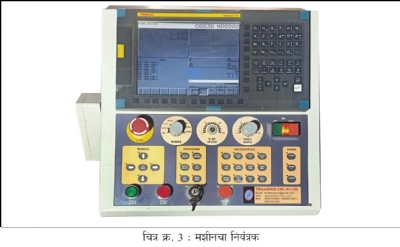
कोणत्याही सी.एन.सी. रेट्रोफिटेड लेथ मशीनसाठी X आणि Z अक्षांची पुनरावृत्तीक्षमता मशीन बेड आणि स्लाइड यांच्या स्थितीवर अवलंबून असते. जुन्या किंवा वापरल्या गेलेल्या लेथ मशीनसाठी बेड आणि स्लाइडचेही कंडिशनिंग करण्याची शिफारस केली जाते. ते अत्यावश्यकच आहे, कारण इतक्या वापरामुळे बेड तसेच स्लाइडची झीज झालेली असते. रीकंडिशनिंग करायचे म्हणजे एकतर बेडचे ग्राइंडिंग करायचे किंवा हाताने स्क्रॅपिंग करायचे. आम्ही शोधलेला लेथ खूपच वजनदार असल्याने बेड आणि स्लाइड यांच्यावर हाताने स्क्रॅपिंग आणि लॅपिंग प्रक्रिया करून त्यांचे रीकंडिशनिंग करण्याचा निर्णय घेण्यात आला.
स्लाइडची लवकर झीज होऊ नये आणि त्यांची हालचाल सफाईदारपणे व्हावी, म्हणून स्क्रॅपिंग/लॅपिंग प्रक्रियेनंतर त्यावर एक 'कुशनिंग' मटेरियल चिकटविण्यात आले. हे मटेरियल चिकटविल्यानंतर त्याचे ब्ल्यू मॅचिंग तपासणे जरूरी असते आणि थोडेफार स्क्रॅपिंग करून ते मॅच करावे लागते. रीकंडिशनिंग प्रक्रियेनंतर 10 मायक्रॉन सपाटपणा मिळाला आणि लेथसाठी असलेल्या IMTMA मानकांनुसार भौमितिक मापदंड होते. स्लाइड, बॉल स्क्रू, बेअरिंग यांच्यासारख्या फिरत्या भागांच्या वंगणासाठी, मशीनवर एक स्वयंचलित वंगण पंप बसविण्यात आला. वंगण करण्याचा वेळ आणि किती वेळाने वंगण करावयाचे, ते नियंत्रकाद्वारे सेट करता येऊ शकते. पंप करण्यासाठी तेल (ऑइल) उपलब्ध आहे की नाही, तसेच तेल पंप करताना वंगणासाठी योग्य दाब मिळतो की नाही, याची तपासणी करण्यासाठी वंगण प्रणालीमध्ये इंटरलॉक देण्यात आले होते. रेट्रोफिट केलेल्या सी.एन.सी.मध्ये वंगणीकरण व्यवस्थित होत आहे की नाही हे तपासणे महत्त्वाचे आहे कारण, मशीन आणि त्यातील वैशिष्ट्ये (फीचर्स) यांचे आयुर्मान त्यावर अवलंबून असते. यासाठी, ऑइल नंबर 68 वापरून, ते वंगण ठराविक प्रमाणात कमीतकमी दर अर्ध्या तासाने सोडावे, अशी शिफारस केली जाते.
मॅन्युअल कामे स्वयंचलित कार्यप्रणालीमध्ये रूपांतरित होणार असल्याने, जुन्या लेथमधील फीड गिअर बॉक्स आणि लीड स्क्रू बदलणे आवश्यक होते. तसेच लीड स्क्रू पुरेसा अचूकपणा देत नाहीत. त्यामुळे आम्ही त्यांच्या जागी अधिक अचूकता देणारे बॉल स्क्रू (चित्र क्र. 4 ) वापरले.
बॉल स्क्रूचे कठीणपणा आणि अचूकतेनुसार अनेक प्रकार आहेत. त्यानुसार या विशिष्ट कामासाठी आम्ही C3 श्रेणीचा अचूकपणा असलेला, कठीणीकरण केलेला, ग्राइंड केलेला आणि डबल नट असलेला बॉल स्क्रू निवडला. हे बॉल स्क्रू गिअरबॉक्सला जोडलेल्या सर्व्हो मोटरद्वारे चालविले जातात आणि ड्रायव्हिंग एंडला टॉर्क वाढविण्यासाठी गुणोत्तरात थोडी वाढ करतात. या ड्रायव्हिंग यंत्रणेसाठी बेअरिंगची निवडदेखील महत्त्वपूर्ण आहे.
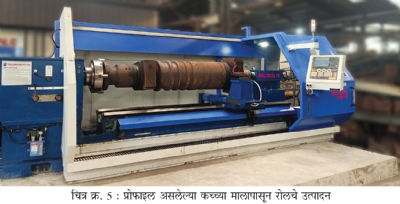
निवडलेल्या लेथच्या स्पिंडलची चाचणी (ड्राय रन) घेतल्यानंतर, गिअरच्या सर्व टप्प्यांवर ते सफाईने आणि समाधानकारकपणे चालत असल्याचे आढळले. तसेच स्पिंडलचा रनआउट इच्छित टॉलरन्समध्ये होता. लेथ मॅन्युअली चालविताना, स्पिंडलचा वेग बदलण्यासाठी ऑपरेटरला हेडस्टॉकचे गिअर बदलावे लागत होते. परंतु, आता मशीन स्वयंचलित बनविण्यात येत असल्याने, मशीन चालविताना पूर्वीप्रमाणे स्पिंडलचे गिअर बदलणे योग्य नव्हते. विद्यमान स्पिंडल मोटरसाठी एक ड्राइव्ह बसविण्याचा आणि जिथून ऑपरेटरला हवे असलेले सर्व वेग प्रोग्रॅमिंगद्वारे आणि अर्थात अधिकतम मोटर पॉवरसह मिळू शकतील, अशा एका स्थानी गिअर ट्रेनला लॉक करण्याचा निर्णय घेण्यात आला. X आणि Z अक्ष चालविण्यासाठी नियंत्रकाला स्पिंडलच्या गतीचा फीडबॅक आवश्यक असतो, म्हणजे स्पिंडलची गती आणि सरकवेग यांच्यातील समन्वयाने यंत्रणाचा दर्जा वाढू शकेल. स्पिंडलच्या गतीचा फीडबॅक मिळविण्यासाठी हेडस्टॉकजवळ स्पिंडल एन्कोडर बसविण्यात आले.
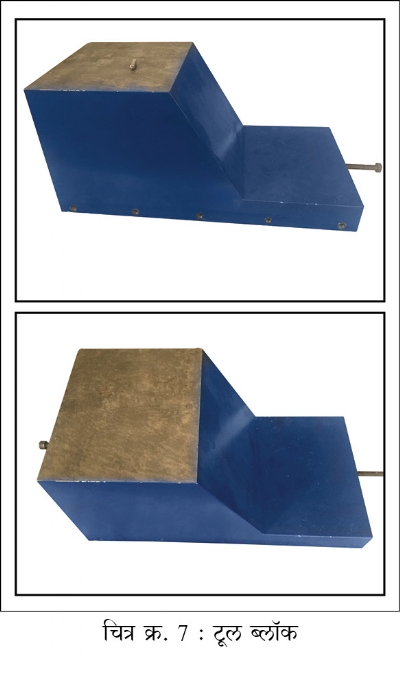
रोल टर्निंगमध्ये, कंपने टाळण्यासाठी, टर्निंग टूल दृढपणे पकडणे आवश्यक आहे. यासाठी जुन्या टूल पोस्टच्या जागी नव्याने कास्ट केलेला हेवी ड्यूटी ब्लॉक (चित्र क्र. 7) बसविण्याचा निर्णय घेण्यात आला. कारण, कंपने टाळण्यासाठी आणि रोल टर्निंग करताना उत्कृष्ट फिनिश मिळविण्यासाठी याची आवश्यकता होती.
स्वयंचलन (ऑटोमेशन) किंवा अपग्रेडेशननंतर यंत्रणाचे पॅरामीटर बदलतात आणि यंत्रण करताना शीतकाची आवश्यकता असते. मॅन्युअल मशीनच्या बाबतीत स्पिंडलची गती तसेच सरकवेग बहुतेकवेळा फारच कमी असतो. त्यामुळे शीतक वापरण्याची गरज असतेच असे नाही. परंतु त्या मशीनचे सी.एन.सी. रेट्रोफिटिंग केल्यानंतर वेग आणि सरकवेग वाढल्यामुळे शीतक वापरणे आवश्यक होते. चिप तोडण्यासाठी तसेच अपेक्षित फिनिश मिळविण्यासाठी शीतक साहाय्यक असल्याने मशीनवर एक स्वतंत्र शीतक टाकी आणि पंप बसविण्यात आले. शीतक चालू/बंद करण्याचे काम प्रोगॅमनुसार होते.
मशीनच्या आजूबाजूला चिप आणि शीतक पसरू नये यासाठी, यंत्रण प्रक्रियेदरम्यान मशीनवर काही आवरण (कव्हर) करणे गरजेचे होते. त्यासाठी अशी आवरणे डिझाइन करून बनविली आणि बसविली गेली, ज्यामुळे मशीन अधिक सुंदर आणि अगदी नव्या सी.एन.सी. सारखे दिसू लागले.
रेट्रोफिटिंग करताना मशीन रंगविणे फारच महत्त्वाचे असते. यामुळे मशीन गंजत नाही आणि त्याचे आयुर्मान वाढते. त्याशिवाय ग्राहकालाही नवीन मशीन घेतल्याचे समाधान मिळते. यासाठी आम्ही ग्राहकाने सुचविलेले रंग वापरून मुख्य मशीनवर स्प्रे पेंटिंग आणि आवरणांवर पावडर कोटिंग केले.
रेट्रोफिटेड सी.एन.सी. लेथ चालू केल्यावर असे दिसून आले की, कामाच्या बाबतीतल्या ग्राहकाच्या सर्व अपेक्षा पूर्ण झाल्या. त्याचबरोबर त्यांचे मशीन एखाद्या परिपूर्ण सी.एन.सी. लेथ मशीनची बरोबरी करू शकते आहे.
ग्राहकाला झालेले फायदे
कच्च्या मालापासून तयार रोल बनविण्यासाठी होणाऱ्या कामाचा तपशील तक्ता क्र. 1 मध्ये दिला आहे.
• पारंपरिक लेथ वापरीत असताना, त्याच यंत्रभागासाठी ते जास्तीतजास्त 5 आर.पी.एम. वर काम करीत होते. यासाठी जास्तीतजास्त 0.2 मिमी. कापाची खोली ठेवून, त्यांना जवळजवळ 48 तास यंत्रण करावे लागत होते.
• आता त्यांचा सुमारे 40 तास इतका यंत्रणास लागणारा वेळ वाचण्याबरोबरच विजेचा खर्च आणि इतर ओव्हरहेडदेखील कमी झाले आहेत.
• ग्राहकाचा खर्च कमी झाल्याने आणि त्यांना हवे तसे परिणाम मिळाल्याने ते समाधानी आहेत.