काही तपासण्या स्कॅनिंग प्रोबशिवाय करणे सहजपणे शक्य असते. याबाबत आपण धातुकामच्या जानेवारी 2021 मध्ये प्रकाशित झालेल्या लेखात समजून घेतले होते. या लेखात स्ट्रेन गेज प्रोब, त्याचे फायदे आदींबाबत सखोल माहिती वाचावयास मिळेल.
काही तपासण्या स्कॅनिंग प्रोबशिवाय करणे सहजपणे शक्य असते. याबाबत आपण धातुकामच्या जानेवारी 2021 मध्ये प्रकाशित झालेल्या लेखात समजून घेतले होते. तसेच टच ट्रिगर प्रोबपेक्षा स्कॅनिंग प्रोब कुठे अधिक चांगले कार्य करेल, याबाबतही सविस्तरपणे जाणून घेतले होते. त्याशिवाय, रेझिस्टिव्ह फोर्स आणि स्ट्रेन गेज ही तंत्रज्ञाने वापरल्याने ट्रिगर प्रोबचे दोन प्रकार होतात हे पाहिले होते. त्यापैकी रेझिस्टिव्ह प्रोबबद्दल आपण मागील लेखात तपशीलवार माहिती घेतली होती. या लेखात आपण स्ट्रेन गेज प्रोबबद्दल (चित्र क्र. 1) चर्चा करणार आहोत.
स्ट्रेन गेज प्रकारचे टच प्रोब
स्टायलसच्या अग्रामध्ये होणारी छोटी विक्षेपणे (डिफ्लेक्शन) शोधण्यासाठी नवीन प्रकारची स्ट्रेन गेज संरचना वापरून उच्च अचूकता असलेली पुनरावृत्तीक्षमता मिळते आणि लांब स्टायलसद्वारा 3D फॉर्मचे मापन करता येते. मानक प्रोबमध्ये एक यांत्रिकी कळ (स्विच) स्पर्श झाल्याचे संकेत (सिग्नल) निर्माण करते. यात प्रोबचे काम सुरू करण्यासाठी (ट्रिगर) स्टायलसच्या अग्रावर आवश्यक असणारे बल प्रोबिंगच्या दिशेनुसार बदलते. यामुळे फॉर्मच्या मापनामध्ये छोट्या त्रुटी निर्माण होतात, ज्यांना 'लोबिंग' असे म्हणतात. नवीन प्रकारच्या प्रोबमध्ये, स्टायलसच्या अग्राच्या सूक्ष्म विक्षेपणांद्वारे निर्माण होणारे बल अचूकपणे शोधण्यासाठी इलेक्ट्रॉनिक स्ट्रेन संवेदनाचा (सेन्सिंग) वापर करून या त्रुटीवर मात केली जाते.
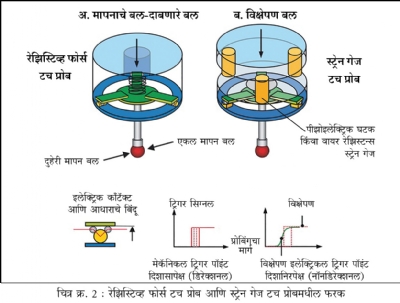
प्राथमिक टच ट्रिगर प्रोबिंग सिस्टिम 'तीन पायांच्या तत्त्वा'नुसार (चित्र क्र. 2) कार्य करतात. जेव्हा स्टायलसचा बॉल कार्यवस्तूशी संपर्क साधतो, तेव्हा CMM च्या स्केल प्रणालीद्वारा वाचता येण्यासाठी एक काम सुरू करण्याचा संकेत निर्माण होतो. मोजला जाणारा बिंदू मापन मशीनच्या सहनिर्देशकांच्या परिभाषेत मिळतो आणि त्याचा संदर्भ स्टायलस बॉलच्या केंद्रस्थानातून घेतला जातो. एका भक्कम शाफ्टद्वारे, स्टायलसचा बॉल एका तीन बिंदू बेअरिंगला जोडलेला असतो. या बेअरिंगच्या तीन बिंदूंवर प्रत्येकी एक कळ असते. जर स्टायलस दिलेल्या दिशेपासून कोणत्याही दिशेत हलला, तर यापैकी किमान एक कळ उघडली जाते. तीच पुढे काम सुरू करण्याचा संकेत म्हणून वापरली जाते. प्रोबिंग बलात प्रोबिंगच्या दिशेनुसार फरक पडतो, हा या प्रणालीतील मुख्य दोष आहे आणि त्यामुळे वेगवेगळ्या लवचिकपणामध्ये (इलॅस्टिसिटी) स्टायलसचे विक्षेपण होते. त्यामुळे निर्माण होणारे दिशात्मक प्रोबिंग वर्तन (तीन कोपऱ्यांचे वैशिष्ट्य) दुरुस्त करणे कठीण असते.
यांत्रिकी संकेताला विद्युत संकेतामध्ये रूपांतरित करण्यासाठी उच्च दर्जाच्या प्रोबिंग प्रणालीमध्ये विविध रूपांतरण घटकांचा, उदाहरणार्थ पीझोइलेक्ट्रिक घटक किंवा वायर रेझिस्टन्स स्ट्रेन गेज
(चित्र क्र. 2), उपयोग होतो. या घटकांचा वापर करून दिशानिरपेक्ष प्रोबिंग मिळविता येऊ शकते. नंतरच्या टप्प्यावरील इलेक्ट्रॉनिक्स हे सुनिश्चित करते की, अतिशय कमी प्रोबिंग बल वापरून मोजमाप केले जाऊ शकते. मोजमापांच्या अनिश्चिततेवर संवेदकाचा (सेन्सर) प्रभाव कमीतकमी असतो. प्रोबिंग बिंदू सापडल्यानंतरच तीन बिंदू बेअरिंगमध्ये विक्षेपण होते. त्यामुळे सहनिर्देशक अक्षांमध्ये बऱ्यापैकी लांब विना मोजमाप मार्ग (ब्रेक पाथ) असले तरी चालतात.
सर्व टच ट्रिगर संवेदक प्रणालींमध्ये एक दोष असतो की, कोणत्याही बिंदूचे मापन करण्यासाठी सहनिर्देशक मापन मशीनचा स्पर्श करणारा घटक (स्टायलस) आधी त्याच्या संपर्कात आणावा लागतो आणि नंतर तो कार्यवस्तूपासून दूर न्यावा लागतो. त्यामुळे अशाप्रकारे प्रत्येक मोजल्या जाणाऱ्या बिंदूसाठी तपासणीस लागणारा वेळ सेकंदांच्या श्रेणीतील असावा लागतो.
मुख्य फायदे
• ज्या कार्यवस्तूंचे टॉलरन्स अतिशय कमी असतात (± 0.01 मिमी.) आणि ज्यांच्यासाठी कमी जागेत पुष्कळ बिंदूंवर मापन करावे लागते, अशा कामांसाठी याचा वापर करण्याची शिफारस केली जाते. ज्या वैशिष्ट्यांच्या (फीचर) मापनासाठी लांब किंवा क्लिष्ट स्टायलसची व्यवस्था (चित्र क्र. 3) आवश्यक असते, त्यासाठीदेखील हे अनुकूल असते.
• वेगवान, स्वयंचलित स्टायलस बदल आणि 10 दशलक्षाहून अधिक ट्रिगर इतके स्टायलस मोड्यूलचे सामान्य आयुर्मान असते. उत्पादकतेत वाढ होते आणि वेळ आणि खर्चात बचत होते.
• वैशिष्ट्य संपर्क, पृष्ठीय फिनिश आणि अचूकता यासारख्या परस्परविरोधी गरजा पूर्ण करण्यासाठी स्टायलस व्यवस्थेचे इष्टतमीकरण शक्य असते.
• स्ट्रेन गेज तंत्रज्ञान मायक्रॉनपेक्षाही कमी स्तरावरची ट्रिगरिंग कामगिरी देते आणि मानक 'कायनेटिक टच प्रोब'मध्ये अनुभवाला येणारी लोबिंग समस्या (चित्र क्र. 4) दूर करते.
• प्रोबमधील सॉलिड स्टेट इलेक्ट्रॉनिक्स लाखो ट्रिगर पॉइंटवर विश्वासार्ह ऑपरेशनची खात्री देतात.
• मानक बल आणि कमी बलाचे स्टायलस मोड्यूल उपलब्ध असून, कमी बलाच्या मोड्यूलमध्ये स्टायलसचा बॉल लहान असतो किंवा ते नाजूक मटेरियलवर वापरण्यासाठी डिझाइन केलेले असतात. याव्यतिरिक्त, विस्तारित ओव्हरट्रॅव्हल मोड्यूल CMM मोशन ओव्हररन विरूद्ध अधिक संरक्षण प्रदान करते. स्टायलस चेंज रॅक (चित्र क्र. 5) वापरून मोड्यूल बदलता येतात.
निष्कर्ष
प्रोबिंग प्रणालीची निवड पूर्णपणे अॅप्लिकेशनवर किंवा केल्या जाणाऱ्या मोजमापावर अवलंबून असते. प्रणालीची निवड करण्यासाठी पुढील मुद्दे विचारात घेणे आवश्यक आहे.
1. तपासणी करण्याचा यंत्रभाग (प्रिझमॅटिक, शीट मेटल, प्लॅस्टिक, ग्लास इत्यादी)
2. टॉलरन्स बँड ( 0.005 मिमी., 0.020 मिमी. इत्यादी)
3. मोजण्याचा पॅरामीटर (रेखीय परिमाण, आकार, GD&T, प्रोफाइल)
4. तपासणी प्रकार (सॅम्पलिंग बेस, 100% तपासणी)
5. संपर्क वेळ
6. प्रक्रिया क्षमता
प्रोबचा प्रकार निवडण्याबाबतचा निर्णय घेताना व्यावहारिक बाबींकडे लक्ष दिले पाहिजे. पूर्वी सांगितल्यानुसार, आदर्श तपासणी पद्धत निश्चित करण्यात, दिलेल्या डेटमवर आवश्यक असणाऱ्या टॉलरन्सची मोठी भूमिका असते.
टच प्रोबिंगद्वारा उच्च अचूकता मिळते, परंतु अॅनालॉग स्कॅनिंग प्रोबच्या तुलनेत त्याची पुनरावृत्तीक्षमता कमी असते. अॅनालॉग स्कॅनिंग ही एखाद्या यंत्रभागाची तपासणी करण्याची सर्वात अचूक पद्धत मानली जाते आणि त्याद्वारे ±0.005 मिमी. किंवा त्याहून कमी टॉलरन्समध्ये तपासणी करणे शक्य असते. विशिष्ट यंत्रभागांच्या बाबतीत, स्कॅनिंग हा एक योग्य पर्याय असतो, कारण त्यांच्यामध्ये उच्चस्तरीय अचूकतेने प्रोफाइलची तपासणी करणे आवश्यक असते. काही यंत्रभागात सुट्या सुट्या बिंदूंवर प्रोबिंग केले तरी चालू शकते. स्टँप केलेला, ढिले टॉलरन्स असलेला, ज्यात फॉर्मला महत्त्व नाही आणि फक्त भोकांच्या स्थानांचे प्रोफाइल आवश्यक आहे, असा यंत्रभाग अशा तपासणीसाठी योग्य आहे. जरी त्या भागामध्ये एकाधिक वैशिष्ट्ये असतील, तरीही स्कॅनिंग करणे अनावश्यक आणि व्यर्थ खर्चाचे आहे.
वेगवेगळ्या प्रोबिंग पर्यायांचे मूल्यांकन करताना उपलब्ध बजेट हा एक महत्त्वपूर्ण घटक असतो. हा घटक सुरुवातीला विचारात न घेता सर्वात शेवटी विचार करण्यामागे कारण आहे. एखाद्या संस्थेने त्यांच्या कामामध्ये प्रथम सर्वोत्कृष्ट तंत्रज्ञानावर संशोधन केले पाहिजे. त्यानंतर त्यातून मिळणारा फायदा आणि खर्चातील बचत यांच्याकडे लक्ष दिले पाहिजे आणि गुंतवणुकीवरील अंदाजित परताव्याची गणना केली पाहिजे आणि त्यानंतर सगळ्यात शेवटी उपलब्ध बजेटचा विचार केला पाहिजे. कंपन्या नेहमीच खर्चामध्ये कपात करणे, उत्पादनाला चालना देणे किंवा विक्री वाढविणे, यासाठी प्रयत्नशील असतात. यामुळे काहीजण उद्योगातील ट्रेंडनुसार नव्याने आलेल्या प्रत्येक तंत्रज्ञानाचा वापर करण्याच्या मागे लागतात. तथापि, प्रतिस्पर्धी जे करीत असतील, तेच आपणही करणे प्रत्येक कंपनीसाठी योग्य असेलच असे नाही. काहीही करणे आणि ते चांगल्या प्रकारे करणे, यात फरक आहे. सर्वोत्तम पर्याय शोधण्यासाठी वेळ लागतो, परंतु दूरदृष्टीचा वापर करून योग्य चौकशी केली तर, लवकरच उत्कृष्ट उपाययोजना हाती येते.
उद्योगक्षेत्राच्या स्कॅनिंग पर्यायाच्या दिशेने होणाऱ्या वाटचालीमागे सुधारित 'थ्रूपूट' हे कारण आहेच, परंतु ज्याप्रकारे यंत्रभागांचे प्रिंट तयार केले जातात, ते त्याहून अधिक महत्त्वाचे कारण आहे. पूर्वी, यंत्रभागांचा संदर्भ रुंदी आणि लांबीच्या परिमाणांद्वारे दिला जात असे. उत्पादनांचे जीवनचक्र दिवसेंदिवस लहान होत चालले आहे. फक्त रुंदी आणि लांबी वापरून सध्या बनवित असलेल्या यंत्रभागाची पुनरावृत्ती करणे फारच क्लिष्ट आहे आणि त्यात बदल करण्यास खूप वेळ लागतो. जेव्हा यंत्रभागाचा संपूर्ण आकार प्रोफाइलद्वारे नियंत्रित केला जातो, तेव्हा CAD मॉडेल बदलण्यासाठी लागणारा वेळ खूपच कमी होतो. प्रोफाइलद्वारे नियंत्रित केलेला यंत्रभाग त्यामध्ये अंतर्भूत असलेल्या GD&T प्रोफाइल नियंत्रणासाठी अनुकूल असतो. जेव्हा त्या यंत्रभागाच्या प्रोफाइलमध्ये वैशिष्ट्यांचे स्थान समाविष्ट असते, तेव्हा त्याचे स्कॅनिंग करणे विशेषतः उपयुक्त ठरते.
टच प्रोबिंग वापरून थ्रूपुटमध्ये वाढ
CMM चा स्कॅनिंग करण्याचा वेग मशीनच्या गतीशीलतेनुसार (डायनॅमिक्स) साधारणपणे 80 मिमी./सेकंद आणि 150 मिमी./सेकंद यांच्यादरम्यान मर्यादित असतो. तथापि, या मर्यादेपर्यंत पोहोचण्याच्या खूप आधी, मोजमापांची अचूकता कमी होते. बहुतेक वेळेस मोजण्याची परिणामकारक अधिकतम गती 10 मिमी./सेकंद आणि 25 मिमी./सेकंद यांच्यादरम्यान मर्यादित असते.
कसे?
कार्टेशियन CMM मधील बिन-रेखीय गतीमुळे सतत त्वरण (अॅक्सिलरेशन) आणि अवत्वरण (डेसिलरेशन) होते. त्यामुळे मशीनच्या रचनेवर (स्ट्रक्चर) पीळ देणारी आणि विक्षेपण आणणारी बले निर्माण होतात. या गतिशील विक्षेपणांमुळे (डायनॅमिक डिफ्लेक्शन्स) मापनाच्या गतीनुसार मापनातील त्रुटी वाढतात. गतिशील विक्षेपणे टाळण्यासाठी, यंत्रभागाच्या पृष्ठभागावर स्टायलस वेगाने हलत असताना, 5 अक्षीय मापन मशीनचे त्वरण कमी करते.
सोप्या शब्दात सांगायचे तर CMM च्या ब्रिजची हालचाल करून माहिती बिंदू गोळा करण्याऐवजी प्रोब हेडलाच पाचवा अक्ष दिल्याने, प्रोब हेड त्याच्या असंख्य हेड स्थितीसह वेगाने फिरते. असे केल्याने तपासणी नित्यक्रमाचे एक अधिक कार्यक्षम वातावरण तयार होते आणि पारंपरिक 3 अक्षीय टच प्रोब प्रणालीपेक्षा तिप्पट थ्रूपुट मिळतो. आज बाजारात उपलब्ध असलेल्या कोणत्याही पारंपरिक 3 अक्षीय टच प्रोब सोल्यूशनच्या किंमतीशी हे स्पर्धात्मक आहे.
निष्कर्ष
एक प्रोबिंग धोरण (स्ट्रॅटेजी) विकसित करण्याच्या दृष्टिकोनातून थ्रूपुट आणि अचूकता यांचा तुलनात्मक विचार महत्त्वपूर्ण आहे. प्रक्रिया नियंत्रणाच्या हेतूने मोठ्या प्रमाणात माहिती गोळा करणे महत्त्वाचे असते. परंतु तशी माहिती गोळा करताना तपासणीचा आवर्तन काळ वाढू शकतो, ज्याचा शेवटी थ्रूपुटवर परिणाम होतो. यंत्रभागातील वैशिष्ट्याचे (फीचर) स्थान आणि स्थिती निश्चित करण्यासारख्या इतर हेतूने तपासणी करताना, कमी माहिती बिंदू असले तरी आवश्यक प्रमाणात मितीय माहिती मिळू शकते.
आपल्या स्वत:चे समाधान होईपर्यंत तपशीलवार संशोधन करण्यास वेळ दिल्याने नक्कीच मोठा फायदा होऊ शकतो. CMM आणि प्रोबिंगच्या क्षेत्रामध्ये आज उत्पादकांना उपलब्ध असलेले सर्व पर्याय पाहता, एका गोष्टीची खात्री आहे. ती म्हणजे, जर आपण पुरेसा वेळ दिला, तर आपल्या विशिष्ट गरजा आणि खर्चाला अनुकूल अशी उपाययोजना शोधण्यात आपण नक्कीच यशस्वी होऊ!
(प्रोबच्या सर्व चित्रांसाठी सौजन्य : रेनिशॉ)