मिलिंग ऑप्टिमायझेशनचे काही घटक आपण मागील अंकात (ऑक्टोबर 2017) बघितले. त्याच लेखाचा दुसरा भाग या अंकात वाचकांसाठी देत आहोत.
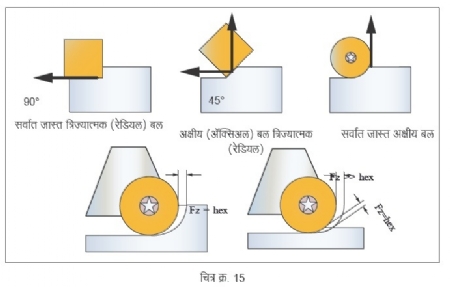
मिलिंगमधील संज्ञा
• Vc-कर्तन वेग (कटिंग स्पीड)-मी/मिनिट
• N-RPM (प्रति मिनिट फेरे)
N =Vc X 1000 / Dc X π
• Dc - कटरचा व्यास-मिमी
• Fz - सरकवेग (फीड) मिमी/दंत (टूथ)
• Vf - सरकवेग (फीड) मिमी/मिनिट
• Ae - संपर्क कमान (आर्क ऑफ एंगेजमेंट) -मिमी
• Ap - कापाची खोली - मिमी
• Hex - छिलक्याची जाडी - मिमी
मिलिंग प्रक्रिया सुधारण्यासाठी घटकांचे इष्टतमीकरण (ऑप्टिमायझेशन)
कोणत्याही प्रक्रियेचे इष्टतमीकरण (ऑप्टिमायझेशन) करण्यासाठी शून्यातून सुरुवात करणे चांगले. नवीन कार्यवस्तूवर काम करण्यासाठी त्या प्रक्रियेचे पुनर्गठन (रीइंजिनिअरिंग) करणे वेळखाऊ प्रक्रिया असते. त्यामुळे पूर्ण प्रक्रिया समजावून घेतल्यानंतरच त्यातील घटकांचा अधिकाधिक चांगला वापर कसा करता येईल, ते निश्चित करणे आवश्यक असते. मिलिंग प्रक्रियेत वर दिलेल्या काही घटकांचा अभ्यास करून, त्याचा सर्वोत्तम वापर कसा करता येईल आणि प्रक्रिया जास्त फायदेशीर कशी होईल याची माहिती लेखात आपण घेऊ.
1. मिलिंग करायच्या कार्यवस्तूची वैशिष्ट्ये लक्षात घेऊन कटरची जागा (पोझिशन) आणि त्याचा मार्ग (पाथ) याची योग्य निवड.
2. कार्यवस्तू, तिचे मटेरिअल आणि मशिनिंग सेंटरचा विचार करून निवडलेली सर्वोत्तम पद्धत आणि प्रोग्रॅमिंग.
3. उत्पादकता वाढविण्यासाठी ॲप्रोच अँगल आणि छिलक्याची जाडी यांच्या परस्पर संबंधाचा फायदा घेऊन वाढवता येणारा सरकवेग.
4. परिणामकारक व्यास (इफेक्टिव्ह डायमीटर) या संकल्पनेचा वापर करून, बॉल नोझ आणि टोरॉईड कटर्सच्या (केंद्रस्थानी कर्तन कडा एकमेकांवर आच्छादित होणारे कटर्स) मदतीने केलेले प्रोफाईल मिलिंग.
5. पोकळयांचे मिलिंग करताना जास्त अक्षीय खोली (हाय ॲक्शिअल डेप्थ) आणि कमी त्रिज्यात्मक काप (रेडिअल कटस्) वापरून केलेले प्रोग्रॅमिंग.
मागील लेखातील संदर्भ - वरीलपैकी पहिल्या मुद्द्याचे तपशीलवार विवेचन मागील अंकात दिले होते. त्याचाच हा पुढील भाग
2.3 कार्यवस्तूमध्ये कोपर्यांचे मिलिंग करताना टूलची दिशा अचानक बदलणे टाळावे.
वर उल्लेख केल्याप्रमाणे, ज्यामध्ये मिलिंग कटरचा प्रवास आवश्यक इतकाच होईल, कार्यवस्तूशी संपर्क Ae = 70% प्रमाणे होईल आणि कार्यवस्तूमध्ये प्रवेश करताना फिरता संपर्क (रोलिंग काँटॅक्ट) होईल. अशा पद्धतीने प्रोग्रॅम करून, वेगवेगळ्या धातूंच्या कार्यवस्तूंवर चित्र क्र. 9 मध्ये दाखवल्याप्रमाणे प्रयोग केले असता मिळालेले निकाल तक्ता क्र. 1 मध्ये दिले आहेत.
तक्ता क्र. 1 मधील आकडेवारीवरून स्पष्ट दिसते की, टूलचे मार्ग नीट विचारपूर्वक निवडून, प्रोग्रॅमिंग केले तर फेस मिलिंगसारखी साधी प्रक्रिया खूपच कार्यक्षम होऊन उत्पादकता वाढते.
3 आतील कोपर्यांचे मिलिंग करताना येणारी कंपने टाळणे.
कार्यवस्तूमधील खाचा अथवा पोकळ्यांचे कोपरे मिलिंग करताना कंपने निर्माण होण्याची शक्यता अधिक असते. अशावेळी टूलची संपर्क कमान (Ae) आणि सरकवेग फार काळजीपूर्वक निवडावे लागतात. संपर्क कमान आणि त्रिज्यात्मक कापाची खोली (रेडिअल कट) कमी केली, तर कंपने कमी होतात आणि जास्त खोलीचे काप घेता येऊन सरकवेगही वाढविता येतो.
सुरुवातीचे रफ मिलिंग करताना प्रोग्रॅममध्ये Dc च्या 50% त्रिज्या ठेवली तर फायदेशीर ठरते, पण फिनिशिंग करताना इतकी जास्त त्रिज्या ठेवणे शक्य नसते. तेव्हा चकत्या काढणे (स्लायसिंग) यासारख्या वेगळ्या मार्गांचा अवलंब करावा लागतो.
(चित्र क्र. 14a, 14b, 14c)
मिलिंगमध्ये सरकवेग (Fz) आणि छिलक्याची जाडी (Hex) यांवर ॲप्रोच कोनाचा परिणाम
कार्यवस्तूचा धातू आणि भूमिती यावरून ॲप्रोच कोनाची निवड करताना योग्य निर्णय घ्यावा लागतो. सरकवेग एकच असूनही ॲप्रोच कोनाच्या प्रमाणात छिलक्याची जाडी बदलते. (चित्र क्र. 15)
उदाहणार्थ,
ॲप्रोच कोन 900 असताना,
Hex = Fz = 0.2 असेल तर,
ॲप्रोच कोन 450 असताना,
Hex = 0.2 / 1.414 = 0.14
त्यामुळे सरकवेग 1.414 या पटीत वाढविता येईल. म्हणजे, 450 ॲप्रोच कोन असताना
Fz = 1.414 x 0.2 = 0.28.
यामुळे कोणत्याही प्रोसेस पॅरामीटरला धक्का न लावता उत्पादकता वाढते.
इन्सर्ट वर्तुळाकार असताना कापाच्या खोलीप्रमाणे ॲप्रोच कोन बदलतो आणि कापाची खोली कमी केली की, छिलक्याची जाडी कमी होते. त्यामुळे सरकवेग वाढविता येतो. त्यामुळे एस एस इन्कोनेलसारख्या कठीण धातूवर वर्तुळाकार इन्सर्ट वापरणे किफायतशीर ठरते.
ravinaik1951@gmail.com
रवी नाईक यांना टूलिंग क्षेत्रातील 40 हून अधिक वर्षाचा अनुभव असून ते टूलिंग विषयक सल्लागार आहेत.