मागील अनेक वर्षांपासून आपण सी.एन.सी. मशिन्स वापरत आहोत. या मशिन्सशिवाय आपले काम होणारच नाही अशी भावना तयार होण्याइतके आपण त्याला स्थिरावलो आहोत. त्याचवेळी काही लोक पारंपरिक मशिन्स वापरून काम करत असताना सी एन सी मशिन घेतल्यावर , त्यांना असा अनुभव येतो की, सी.एन.सी. मशिनचा वापर तर आपण करतो पण काम किफायतशीर होत आहे की, नाही हे मात्र कळत नाही आणि जेव्हा कळते तेव्हा उशीर झालेला असतो.
यासाठी आपण एक उदाहरण पाहणार आहोत ज्यात अशा प्रकारची समस्या कशी सोडविली ते समजू शकेल.
एका लहान कारखान्यात चित्र क्र. 1 मध्ये दाखविलेली कार्यवस्तू तयार होत होती. पूर्वी जिग्ज वापरून या कार्यवस्तूचे रेडिअल ड्रिलिंग मशिनवर यंत्रण केले जात होते. जिग्जचे सातत्य, स्पिंडल रनआऊटमुळे होणारे ड्रिल/रिमरचे नुकसान आणि छिद्रांमध्ये अचूकता मिळत नव्हती. या यंत्रणात अशा अनेक अडचणींना सामोरे जावे लागत होते. त्याचबरोबर वेळेत अपेक्षित उत्पादन मिळत नव्हते. त्यामुळे व्ही. एम. सी. मशिनवरच कार्यवस्तू केली जावी अशी मागणी ग्राहकाने केली. त्यामुळे उत्पादकाने नवीन व्ही.एम.सी. मशिन विकत घेतले.
आता तीच कार्यवस्तू व्ही.एम.सी. मशिनवर केली जात होती. रेडिअल ड्रिलिंग मशिनच्या तुलनेत ही व्ही.एम.सी. मशिन जवळजवळ 4 पटीने महाग होती. व्ही.एम.सी.च्या वापरानंतर कार्यवस्तूची गुणवत्ता सुधारली, मात्र तयार होणाऱ्या कार्यवस्तूंच्या संख्येचे गणित जुळत नव्हते. पूर्वीपेक्षा गुणवत्तेमध्ये निश्चितच फरक पडला होता, मात्र महिन्याकाठी दोन शिफ्टमधून केवळ 1500 कार्यवस्तूंचेच उत्पादन होत होते. त्यामुळे मशिनच्या खरेदीसाठी घेतलेल्या कर्जाचे हप्ते देणे अवघड बनले होते. जेमतेम कामगाराचा पगार आणि इतर खर्च भागत होता. त्यामुळे मशिन घेण्यात आपण चूक केली की काय असा प्रश्न या कारखान्याच्या मालकासमोर उभा राहिला. या कारखान्यातील काही लोक त्यांची ही समस्या घेऊन आम्हाला भेटले. यावर आम्ही सर्वांगीण अभ्यास करायचे ठरवले. मशिन देणार्यांनी फक्त गुणवत्तेचा विचार करत ती मशिन विकली असल्याचे त्यावेळी लक्षात आले. या मशिनवर एकावेळी एकच कार्यवस्तू लावली जात होती आणि 2 सेटिंगमध्ये कार्यवस्तूच्या दोन बाजू केल्या जात होत्या. (चित्र क्र. 2 पहा.) चित्रावरून असे लक्षात येते की, 110 पीसीडी वरील 12 Ø चे भोक हे वरच्या कॉलरमध्येच फुटत होते. त्यामुळे मशिन देणाऱ्यांनी दोन सेट-अप वापरले होते.
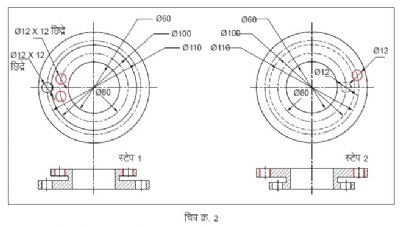
सर्वप्रथम आम्ही एका लहान प्लेटवर 2 कार्यवस्तू उलट-सुलट बसवल्या आणि कार्यवस्तूच्या दोन्ही बाजूचे ड्रिलिंग एकाच सेटिंगमध्ये करण्यास सुरुवात केली. ड्रिलसाठी कार्यवस्तूच्या अगदी जवळून सुरुवात करून कर्तनाचा वेळ कमी केला. मायक्रोफाईंड ग्रेडची कार्बाईड ड्रिल लेपन करून वापरली. त्यामुळे उत्पादकतेमध्ये भरघोस सुधारणा होऊन महिन्याकाठी 5000 कार्यवस्तू तयार होऊ लागल्या. (तक्ता क्र. 1)
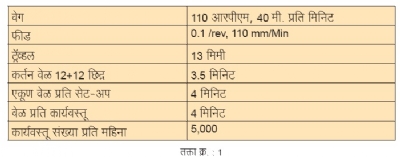
यानंतर आम्ही 6 कार्यवस्तू एका सेटिंगमध्ये करता येतील असे फिक्श्चर (चित्र क्र. 3) तयार केले. या 6 कार्यवस्तू एका प्लेटमध्ये बसविल्या आणि या असेम्ब्लीचे वजन त्याला उचलून टेबलवर ठेवता येईल अशा मर्यादेत ठेवले. ती प्लेट मशिन टेबलवर एका फिक्श्चर प्लेटमध्ये लोकेट केली. (चित्र क्र. 4) त्यामुळे 6 कार्यवस्तूचा लोडिंग आणि अन-लोडिंग वेळ एका कार्यवस्तूइतकाच झाला. 3 कार्यवस्तू वरच्या पाळीची छिद्रे आणि 3 कार्यवस्तू खालच्या पाळीची छिद्रे असा सेट-अप करताना कार्यवस्तू बाजूला हलवून लावल्यामुळे मशिनच्या ट्रॅव्हलमध्ये सर्व छिद्रे येतील अशी खबरदारी घेतली. एका सेट-अपमधून 9.6 मिनिटांमध्ये 3 पूर्ण (वरची-खालची सगळी छिद्रे) कार्यवस्तू तयार होऊ लागल्या. म्हणजेच प्रति कार्यवस्तू केवळ 3.2 मिनिटे एवढा वेळ लागला. यामुळे एका महिन्यात 7000 कार्यवस्तूचे उत्पादन मिळू लागले.
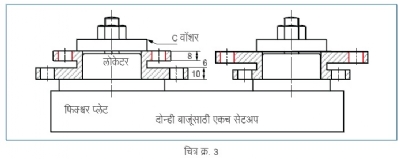
जिथे मशिनचे हप्ते देणेही अवघड झाले होते तिथे या नवीन पद्धतीमुळे महिन्याकाठी 44,000 रुपये नफा होऊ लागला. पूर्वी अपेक्षित उत्पादन मिळत नसल्यामुळे इतरांकडे ज्या काही कार्यवस्तू गेल्या होत्या, त्या प्रति कार्यवस्तू 2 रुपये ग्राहकाला कमी करून दिल्यामुळे ग्राहकाने वाढीव काम दिले आणि त्याच प्रकारच्या इतर कार्यवस्तू देण्याची तयारी दाखवल्यामुळे नवी मशिन देण्यास हाच उद्योजक तयार झाला.
सूचना - वरील सर्व बाबी या एक मशिन वापरून मांडलेल्या आहेत. तसेच सी.एन.सी. क्षेत्रात प्रथम प्रवेश करणाऱ्या बाबतीतल्या आहेत. ज्यांच्याकडे एकापेक्षा जास्त मशिन्सचा सेट-अप असेल तिथे वेगळी समीकरणे मांडावी लागतील. मूळ मशिनची किंमत वाढल्यावर त्या अनुषंगाने उत्पादन प्रक्रियेमध्ये बदल घडवून काम किफायतशीर करण्यावर भर दिला पाहिजे. तरच आपल्या गुंतवणुकीवर रास्त परतावा मिळण्यास तंत्रज्ञानाचा उपयोग होईल एवढेच या लेखाच्या निमित्ताने मुद्दा अधोरेखित करायचा आहे.)
दत्ता घोलबा ‘मानस इंजिनिअरिंग’ कंपनीचे संस्थापक संचालक असून, 44 वर्षांपासून कटिंग टूल्स या विषयाशी निगडित कार्य करत आहेत.
dattagholba@gmail.com