फॉर्मेंट कंपनीमधील 1975 चा तो काळ मला अजून आठवतो. मी त्याच वर्षी तिथे रुजू झालो होतो आणि आमच्याकडे CVRDE ची ट्रॅक शू ड्रिलिंगची मोठी ऑर्डर होती. त्या कामासाठी डीप होल ड्रिलिंगची गरज होती. भारतात ते यंत्र तयार करणारे तसेच, त्याची हत्यारे बनवणारे कोणीही नव्हते. त्यामुळे अशा प्रकारचे मशिन आयात करणे हा एकच पर्याय होता.
’प्रेसिहोल’ कंपनीची स्थापना
मशिन आयात करणे ही सोपी गोष्ट नव्हती. सर्वजण पारंपरिक ड्रिलिंगचाच वापर करत होते. मात्र, पारंपरिक ड्रिलिंगला खूप वेळ लागायचा. तसेच अचूकता नसायची. त्यावेळी आम्ही हे मशिन स्वत:च बनविण्याचे ठरविले आणि हत्यारांसाठी आम्ही ’सँडविक’ कंपनीकडे मदत मागितली. त्यांच्यासोबत सुरुवात करण्यासाठी आम्ही ट्यूबची निर्मिती केली, पण नंतर त्यांच्याकडून आवश्यक ती गन ड्रिल बनवून मिळाली आणि आम्ही भारतातल्या पहिल्या डीप होल ड्रिलिंग मशिनची निर्मिती केली.
त्यानंतर आम्हाला NFC कंपनीकडूनही एक मोठी ऑर्डर मिळाली. त्यांच्याकडे ’युटिटा’ यंत्र होते. त्यांना अजून काही यंत्रांचा समावेश करायचा होता. आमच्या यंत्राची किंमत ही ’युटिटा’ मशिनच्या एक तृतीयांश इतकी असूनही ऑर्डर मिळायला 2 वर्षे लागली होती, कारण बाजारपेठेत आमची तितकीशी प्रसिद्धी झालेली नव्हती. ’युटिटा’ यंत्रावर बिलेटला 20 मिमीचे छिद्र पाडण्यासाठी, बिलेट चकमध्ये पकडून ते 800-1000 rpm ला फिरवत असत. आम्ही त्यांना सांगितले, ’आम्ही बिलेट स्थिर ठेऊन त्याला हवे ते ड्रिल करू शकतो, तसेच तुम्ही आता जे ड्रिलिंग पॅरामीटर वापरत आहात, त्यापेक्षा चांगल्या दर्जाचे पॅरामीटर वापरून आम्ही चांगले ड्रिलिंग करून देऊ. तुम्ही आमच्याकडे बिलेट पाठवून तपासणी करा आणि मग आमच्याकडून मशिन घ्या’. दोन वर्षांच्या अथक प्रयत्नांनंतर ऑर्डर मिळाली आणि मग आम्ही मागे वळून पाहिलेच नाही. आम्ही त्या मशिन्स बनवल्या आणि दोन्ही मशिन्स ’इम्टेक्स’मध्ये प्रदर्शित केल्या. त्याबद्दल आम्हाला ’फाय फाऊंडेशन’ पारितोषिकही मिळाले. त्यानंतर आम्हाला बऱ्याच ऑर्डर्स मिळायला सुरुवात झाली. अशा तर्हेने भारतामध्ये डीप होल ड्रिलिंगची सुरुवात 1987 मध्ये मी, अनिल कुलकर्णी आणि अयाज काझी अशा तिघांनी मिळून 450 चौरस फूट जागेत ’प्रेसिहोल मशिन टूल’ या कंपनीची स्थापना केली. स्वतः च्या दोन गन ड्रिलिंग मशिन्स बनवून त्यावर जॉबवर्क करून देण्यास सुरुवात केली.
यापूर्वी भारतामधील पहिले गन ड्रिलिंग मशिन मी स्वतः डिझाईन करून तयार केले होतेच. सुरुवातीला आम्ही डझच तयार केल्या. त्यानंतर व्यवसाय वाढवण्यासाठी आणि आर्थिक स्थैर्यासाठी डीप होल ड्रिलिंग - गन ड्रिलिंग, BTA ड्रिलिंग, स्कायव्हिंग अँड बर्निशिंग, होनिंग, इजेक्टर ड्रिलिंग मशिनचे उत्पादन सुरू केले. ’प्रेसिहोल मशिन टूल्स’ ही नावाप्रमाणे होल मेकिंग मशिन्स बनवते. आम्ही तयार करत असलेल्या मशिनविषयी थोडक्यात जाणून घेऊ.
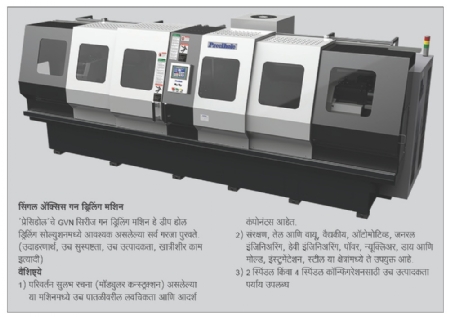
गन ड्रिलिंगची प्रक्रिया दाखवणाऱ्या चित्र क्र. 1 मध्ये जी पिवळी रेषा दिसते आहे, ती शीतकाची (कुलंट) आत जाणारी लाईन आहे. लाल रेषा ही शीतक आणि चिप बाहेर पडताना दाखवणारी लाईन आहे. चित्र क्र.1 अ मध्ये हत्यारावर जी दोन छिद्रे दिसतात त्यामधून शीतक बाहेर येते. ड्रिलिंग पॉईंटवरती दाबयुक्त (प्रेशराइज्ड) शीतकाचा पुरवठा होतो आणि परतीच्या मार्गामध्ये (रिटर्न पाथ) चिप आणि शीतक हे चित्र क्र. 1 (अ) मध्ये दाखविल्याप्रमाणे बाहेर पडतात. बाहेर पडल्यानंतर बुशबॉक्स नावाची एक ॲसेम्ब्ली असते, त्यात चिप आणि शीतक जमा केले जातात. BTA मध्ये टूल पुढे जात असताना शीतकाचा पुरवठा हत्याराच्या बाहेरून होतो. शीतक आणि चिप, हत्यार बसविलेल्या नळीतून बाहेर जातात.
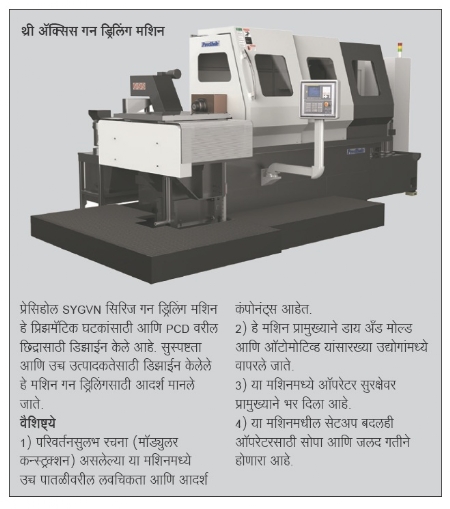
डीप होल ड्रिलिंग प्रक्रियेमध्ये जी प्राथमिक गरज असते ती म्हणजे ड्रिलिंग होण्यापूर्वी हत्याराला योग्य मार्ग दाखविणाऱ्या गाईडबुशची. तो हत्याराला कार्यवस्तूवरील हव्या त्या जागी अचूकपणे पोहोचविण्याचे काम करतो. ड्रिल या बुशमधून फिरत फिरत जेव्हा कंपोनंटमध्ये शिरते, तेव्हा त्याच्यासोबत शीतकसुद्धा आतमध्ये जाते. नंतर ड्रिल पूर्णतः कंपोनंटमध्ये आल्यानंतर जे छिद्र तयार होते, तेच हत्याराचे गाईड बनते. आता यामध्ये दाबयुक्त (प्रेशराइज्ड) शीतकाचा पुरवठा सतत जात असल्याने ड्रिलिंगमुळे तयार झालेली चिप लगेच बाहेरपडत असते. त्यामुळे चिप अडकून ड्रिल तुटण्याची भीती नसते. तसेच ड्रिलिंग होताना, जी उष्णता निर्माण होते ती पण शीतकामार्फत कमी केली जाते. ड्रिलिंग करत असताना अपेक्षित छिद्राचा टॉलरन्स मिळवण्यासाठी बर्निशिंग पॅड्स (चित्र क्र.3) असतात. ते छिद्राला फिनिशिंग आणण्याचे काम करतात.
ड्रिलिंगची प्रक्रिया निवडताना त्यातील L/D म्हणजे ड्रिलिंगची लांबी/व्यास याचे गुणोत्तर आणि अपेक्षित व्यास या गोष्टी महत्त्वाच्या असतात, हे आपल्याला माहितच आहे. L/D गुणोत्तर 7-8 पर्यंत आपण नेहमीच्या ड्रिलिंग यंत्रावर ’वुड पेकिंग’ पद्धत वापरून करू शकतो, मात्र त्यापुढे डीप होल ड्रिलिंग यंत्र वापरावे लागते. साधारणपणे 0.8 ते 30 मिमीपर्यंत व्यासाचे छिद्र गन ड्रिलिंग पद्धतीने करतात तर 15 मिमी ते 300 मिमीपर्यंत व्यासाची छिद्रेकरताना BTA ड्रिलिंगचे यंत्र वापरावे लागते. सामान्यपणे L/D गुणोत्तर 125 पर्यंत आपल्याला डीप होलची पद्धत वापरता येते. आम्ही आमच्याकडे 10 मिमी व्यासाचे ड्रिल 3 मीटरपर्यंत म्हणजे L/D = 300 पर्यंत डीप होल ड्रिलिंग करू शकतो. हे कठीण काम असते. विशेषत: एवढ्या लांब छिद्राची कॉन्सेन्ट्रिसिटी अचूक राखण्यासाठी विशेष काळजी घ्यावी लागते. त्यासाठी अर्थातच जॉब मटेरिअलचे सातत्य फार महत्त्वाचे असते. कंपोनंटच्या कोणत्याही क्रॉस सेक्शनमध्ये एकसमान कठीणता (युनिफॉर्म हार्डनेस) लागतो. जर तसे नसेल आणि त्या कठीणतेमध्ये फरक असेल, तर ड्रिल कमी कठीणता असलेल्या दिशेने वळू शकते. यावेळी जॉबच्या बाहेरून बसविलेले संवेदक (सेन्सर्स) कामाला येतात. ते जाडी (वॉल थिकनेस) मोजतात आणि जाडीमधील फरक दाखवतात. त्यावरून छिद्राचा मध्यबिंदू (सेंटर) कोणत्या भागामध्ये (क्वाड्रंट) गेला आहे ते समजते आणि शीतकाच्या दाबाचे नियंत्रण वापरून ड्रिल पुन्हा मूळ दिशेने वळवता येते.
केस स्टडी
आतापर्यंतच्या प्रवासात खूप अवघड मशिन्स बनवण्यात आल्या, त्यामध्ये जी पहिली मशिन बनवण्यात आली ती एका डीझेल इंजिन बनविणाऱ्या कंपनीसाठी. जनरेटर इंजिनच्या इंजिन ब्लॉकमध्ये ल्युब्रिकेशनसाठी ऑईल गॅलरी होल्स असतात. त्या ऑईल गॅलरी होल्स ड्रिलिंगसाठी, आम्ही हे (चित्र क्र. 2) मल्टीअॅक्सिस कॉलम मशिन तयार केले होते. यामध्ये दोन प्रकारचे इंजिन ब्लॉक होते. दोघांचीही लांबी-वजन वेगळे होते. तसेच दोघांमध्ये ड्रिलिंग छिद्रामध्येही थोडासा फरक होता. या सगळ्याचा विचार करून त्यांना एक 8 स्पिंडल, 5 अक्षीय डीप होल ड्रिलिंग मशिन देण्यात आले आणि 12 सिलिंडर ते 16 सिलिंडरमध्ये जो सेटअप बदलत होता, तोही आम्ही यात एक बटण दाबून करता येईल असा केला.
त्यांच्याकडे असलेले पारंपरिक मशिन जुने झाले होते. त्यामुळे ते वारंवार बंद पडत असे. कामगाराला त्या मशिनवर काम म्हणजे काळ्या पाण्याची शिक्षा वाटत असे. ’कुलंट फिल्ट्रेशन सिस्टिम’मध्ये त्यांना काही अडचणी होत्या. ते मशिन चालवण्यात सुलभता नव्हती. म्हणजे कंपोनंट लो केल्यानंतर, ऑपरेटर सतत कुठे ना कुठे त्या मशिनमध्ये व्यग्र राहायचा. आम्ही हे मशिन तयार केले, तेव्हा ते बनवताना काही गोष्टींचे भान ठेवावे लागले. उदाहरणार्थ, जुने मशिन ज्या जागेत होते त्याच जागेत हे मशिन ठेवायचे होते. या मशिनमध्ये दोन्ही प्रकारचे कंपोनंट झाले पाहिजेत. ’कंपोनंट चेंजिंग’ म्हणजे एका सेटअपमधून दुसऱ्या सेटअपमध्ये जाताना फारसा त्रास पडू नये, तसेच याचे फिक्श्चरिंग करताना दोन्ही कंपोनंट ठेवता येतील असे फिक्श्चर बनवले. परंतु एक सेटअप चालू असताना अनावधानाने दुसऱ्या सेटअपचा कंपोनंट लावला, तर ते मशिन ’अलार्म’ देईल, अशी व्यवस्था करण्यात आली होती. या मशिनमुळे एक कंपोनंट तयार करण्यासाठी लागणारा वेळ (सायकल टाईम) 96 मिनिटांवरून 28 मिनिटांवर आला आणि ऑपरेटरच्या कौशल्यावर अवलंबून राहणे वाचले. ऑपरेटरचे सतत गुंतून राहणेही टळले. हा कंपोनंट कास्ट आयर्नचा असल्याने मशिनिंग होताना कास्ट आयर्न, पावडरसारखी चिप तयार करते आणि त्याच्यात जे ग्रॅफाईट असते ते फिल्टर (अशा मशिनला फिल्ट्रेशन लेव्हल ही 10 मायक्रॉनपर्यंत असते) करणे हे थोडे अवघड असते. त्यासाठी वेगवेगळी तंत्रे वापरावी लागतात. या मशिनमध्ये आम्ही हत्यार देखरेख यंत्रणादेखील (टूल मॉनिटरिंग सिस्टिम) दिली आहे, ज्यामुळे समजा हत्यार बोथट (ब्लंट) झाले, तर कोणत्या स्पिंडलवरील कोणते हत्यार बोथट झाले आहे, याचाही संदेश हे मशिन देते.
ग्राहकाचे समाधान
कंपनीच्या इतिहासात अनेक कठी प्रसंग आले. उदाहरणार्थ, 2004 साली आम्ही ऑस्ट्रियामधील एका कंपनीसाठी एक खास मशिन बनवले. आधी त्यांच्याकडे एक स्विस मशिन होते, जे सातही दिवस 3 शिफ्टमध्ये चालायचे, मात्र समाधानकारक उत्पादन मिळत नव्हते. त्यामुळे त्यासाठी आम्ही दोन स्पिंडलचे स्वयंचलित डीप होल ड्रिलिंग मशिन तयार केले. (हे आमचे निर्यात होणारे पहिले मशिन होते.) मशिन तयार झाल्यानंतर तिकडच्या ग्राहकाकडून भारतात त्याची तपासणी आणि ट्रायलही झाली. नंतर मशिनचे व्यवस्थित पॅकिंग करून मशिन तिकडे पाठवले गेले. तिकडे उघडून पाहिल्यावर त्या मशिनची खूप मोडतोड झाल्याचे लक्षात आले. कंपनीच्या आणि देशाच्याही प्रतिष्ठेचा प्रश्न होता. मी आमची 3 माणसे तिकडे घेऊन गेलो. पॅकिंगच्या वेळी आवश्यक ती काळजी न घेतल्याने मशिनची अवस्था अगदीच कठीण झाली होती. काही भाग तुटले होते, वायर उंदरांनी कुरतडल्या होत्या इत्यादी. आम्ही ते मशिन तपासले आणि भारतातून विमानाने सुटे भाग मागवले आणि काम सुरू करून 10 दिवसांत मशिन चालू करून दिले. ग्राहकाने मशिनची ट्रायल घेतली. त्या मशिनचे सर्व कार्य पाहिले. त्या मशिनवर 3-4 कंपोनंट ड्रिलिंग करून देखील पाहिले. ते मशिन पूर्ववत झाल्याची त्यांची खात्री पटली. पहिल्या दिवशी आम्हाला बाहेरचा रस्ता दाखवणारा ग्राहक (कस्टमर) त्या दिवसानंतर आमचा मित्र बनला आणि पुढे तशा 3 मशिन्स आमच्याकडून घेतल्या.
आमच्याच मशिनवर जॉबवर्क करून आणि स्वतःच्या मशिन्स बनवण्याने आम्ही आमची सुरुवात केली. जॉबशॉप ठेवण्याचा हाच हेतू होता की, ग्राहकासाठी आम्ही मशिनमध्ये जे काही बदल करू, ते आधी इथल्या जॉबशॉपवर करून बघता येतील, तसेच आम्ही स्वतः अनेक प्रयोग इथल्या जॉबशॉपमध्ये करीत असतो.
नमूद करण्यास अभिमान वाटतो की, ’प्रेसिहोल’च्या अथक परिश्रमानंतर डीप होल ड्रिलिंग मशिनची युरोप, अमेरिका, कॅनडा, गल्फ कंट्रीज आणि साऊथ इस्ट आशियातील बाजारपेठ काबीज केली आहे. आता परदेशातील डीप होल ड्रिलिंग मशिन्स बनविणाऱ्यांबरोबर’प्रेसिहोल’ यशस्वीपणे प्रतिस्पर्धा करत आहे. याचाच भाग म्हणजे,
• युरोपिअन ऑर्डिनन्स फॅक्टरीजचा गन बॅरल बनविण्यासाठी लागणारी पूर्ण मशिन रेंज ’प्रेसिहोल’ने दिल्या.
• ’मेडिकल इमप्लांट मशिनरीजच्या’ क्षेत्रात ’प्रेसिहोल’चे योगदान लक्षणीय आहे. या क्षेत्रात वापरल्या जाणाऱ्या धातूत 1.0 मिमी पासून छिद्र करणाऱ्या मशिन्सचे नियमित उत्पादन सुरू केले आहे.
• याचबरोबर ’प्रेसिहोल’ आपल्या जॉब शॉपमध्ये न्युक्लिअर रिॲक्टरला लागणाऱ्या कंपोनंट्सचे डीप होल ड्रिलिंग सातत्याने करून देत आहे.
भारतामधील गन ड्रिलिंग मशिनची एकूण बाजारपेठ ही साधारण 50 कोटी रुपयांची आहे. त्यापैकी आमचा वाटा सुमारे 65-70% आहे. ’प्रेसिहोल’ वर्षाला जवळजवळ 45-48 मशिन्स बनवते. किंमतीच्या बाबतीत या मशिन्स कमीत कमी 20 लाखांपासून ते जास्तीत जास्त 8.5 कोटी रुपयांपर्यंत आहे. तर ’प्रेसिहोल’चा मशिन टूलचा व्यवसाय हा वर्षाला 35 ते 40 कोटी रुपयांचा आहे.
vrnayak@precihole.com40 वर्षांपासून यंत्र निर्मितीत मग्न असलेले व्ही. आर. नायक यांत्रिकी अभियंता असून प्रेसिहोल कंपनीचे संचालक आहेत.