विद्युत निर्मिती केंद्र, सिमेंट कारखाने, पोलाद आणि लोखंड उत्पादन करणारे कारखाने इत्यादी अवजड यांत्रिकी उद्योगांमध्ये तांत्रिकदृष्ट्या अवाढव्य, अत्याधुनिक, अतिशय काटेकोर मोजमापांमध्ये बनविलेली उपकरणे आणि यंत्रसामग्री वापरली जाते. अशा यंत्रसामग्रीचे संचालन, देखभाल आणि दुरुस्तीची कामे अतिशय आव्हानात्मक असून, त्यासाठी विशिष्ट प्रकारच्या वेगवेगळ्या मशिन, नियोजन, तांत्रिक कौशल्य, तसेच अतिकुशल मनुष्यबळ आणि गुणवत्ता नियंत्रण यांची गरज असते.
साहजिकच अशी महागडी मशिन, दुरुस्तीसाठी लागणारी आधुनिक उपकरणे, कुशल मनुष्यबळ आणि गुणवत्ता नियंत्रण उपलब्ध करणे सर्वसाधारण लघु उद्योजकाच्या आवाक्यात नसल्याने अशा मोठमोठाल्या आकाराच्या क्लिष्ट यंत्रभागांची देखभाल आणि दुरुस्तीची कामे करणे ही केवळ मोठा सेटअप असलेल्या कंपन्यांचीच मक्तेदारी असते. हा प्रचलित समज खोडून काढत कल्पनाशक्ती, संशोधन, जिद्द आणि चिकाटी ठेवून एखादा लघु उद्योग आकाराने मोठ्या, अवजड आणि क्लिष्ट यंत्रभागांचे यंत्रण करू शकतो हे दाखवून देणाऱ्या नागपूर येथील न्युमॅक कंपनीने केलेल्या काही अवघड प्रक्रिया सुधारणा आपण या लेखात पाहणार आहोत.
1983 मध्ये छोट्या जागेवर सुरू केलेल्या न्युमॅक कंपनीचा सुरुवातीचा प्रवास अतिशय खडतर होता, मात्र अनुभवातून शिकत आम्ही आव्हानात्मक यंत्रभागांचे परीक्षण आणि दुरुस्ती करण्यामध्ये नाव कमावले आहे. कमीतकमी वेळेत आणि माफक खर्चात काम करणे हे आमच्या कंपनीचे उद्दिष्ट आहे. आम्ही आजपर्यंत 50 हून अधिक विशिष्ट उपयोगिता मशिन (एस.पी.एम.), उपकरणे आणि उत्पादांची निर्मिती केली असून, त्यापैकी 7 मशिनला पेटंट मिळाले आहे, तर काही पेटंट मिळण्याच्या मार्गावर आहेत.
संघर्ष, कठोर परिश्रम घेण्याची तयारी, काळानुसार तंत्रज्ञान आत्मसात करणे यानुसार गेली 35 वर्षे आम्ही काम करत आहोत. 25 वर्षांपासून आम्ही ग्राहकाकडे आलेल्या समस्या त्यांच्या कारखान्यांमध्ये जाऊन जागेवरच यंत्रण संदर्भातील सेवा पुरविण्यास सुरुवात केली आहे. यामुळे साहजिकच उद्योगांचा बहुमूल्य वेळ आणि पैशांची बचत होऊन नादुरुस्त मशिन लवकरात लवकर कार्यरत करण्यात यश आले आहे.
महानिर्मिती आणि इतर सार्वजनिक तसेच खाजगी क्षेत्रातील विद्युत निर्मिती केंद्रांचे आव्हानात्मक आणि अवघड दुरुस्तीची कामे आम्ही नेहमीच करीत असतो. परंतु कोराडी आणि खापरखेडा या दोन औष्णिक विद्युत निर्मिती केंद्रामधील (थर्मल पॉवर स्टेशन) आव्हानात्मक यंत्रणाचे काम कसे केले याचे तपशील आपण या लेखात पाहणार आहोत.
केस स्टडी 1कोराडी थर्मल पॉवर स्टेशन
(KTPS), (युनिट 3 - 120 MW आणि युनिट 5 - 210MW)कोराडी थर्मल पॉवर स्टेशन येथील काम अतिशय किचकट आणि कठीण होते. कामाचा आणि उपलब्ध परिस्थितीचा विचार करता, अशाप्रकारचे काम 1998 सालापर्यंत भारतामध्ये करण्यात आलेले नव्हते. या यंत्रभागाचा आवाका लक्षात घेता, जगभरामध्येदेखील क्वचितच त्यावर योग्य उपाय सुचविला जातो.
KTPS येथील 120MW चा विद्युत निर्मिती संच 1972 साली पोलंड देशामध्ये बनलेला आहे. या संचातील बेअरिंग एरियामधील ग्लँडच्या परिसरात केसिंग पूर्णपणे समकेंद्री (कॉन्सेन्ट्रिक) असणे अत्यंत आवश्यक असते. परंतु केसिंगचे तापमान वाढून या जागी विरूपण (डिफॉर्मेशन) झाल्याने ग्लँड एरियात केसिंगचा आकार अंडाकृती झाला होता. अंडाकृती विरूपण झालेल्या जागी यंत्रण करून त्याला परिपूर्ण समकेंद्री करायचे होते. या केसिंगचा बाहेरील व्यास अंदाजे 4 मीटर असून, वजन
35 ते 40 मेट्रिक टन आहे. आम्ही बनविलेल्या एस.पी.एम.ने बोअरिंग बारद्वारा तंतोतंत समकेंद्री यंत्रण केलेल्या जागेच्या ठिकाणी
1 ते 1.2 मीटर व्यास आहे.
केसिंगच्या अंतर्गत यंत्रणासाठी सपाट पृष्ठभागाचे पार्टिंग करून त्याचे यंत्रण केले जाते. यामुळे पार्टिंग प्रतलातूनच वाफेची होणारी गळती शोधता येते. या नेहमीच्या पद्धतीने आम्ही यंत्रण करण्याचा प्रयत्न केला. परंतु ग्लँड परिसरातील लंबगोलाकारिता (ओव्हॅलिटी) वाढत असल्यामुळे केसिंगच्या वरच्या आणि खालच्या अशा दोन्ही भागांत विविध प्रकारचे विरूपण येत होते.
या समस्येवर मात करण्यासाठी,
KTPS ने मूळ टर्बाईनची निर्मिती केलेल्या परदेशी कंपनीकडे (इलेक्ट्रिम, पोलंड) तसेच
BHEL कंपनीकडे विचारणा केली असता त्यांच्याकडून असमर्थता दर्शविण्यात आली. या केसिंगची दुरुस्ती शक्य नसल्याने विरूपण झालेले केसिंग बदलण्याचा (रिप्लेसमेंट) सल्ला
BHEL ने दिला. केसिंग बदलण्याचा खर्च
1.93 कोटी + कर (टॅक्स) वेगळाच भरावा लागणार असल्याचे निदर्शनास आले. प्रत्येक केसिंग बदलासाठी कमीतकमी
90 दिवस लागणार होते. या कालावधीमध्ये कमीतकमी
6 महिन्यांसाठी टर्बाईन बंद ठेवावे लागणार असल्यामुळे
KTPS ला ते कोणत्याच दृष्टीने परवडणारे नव्हते. त्यामुळे KTPSने वेगळा मार्ग शोधण्याचे ठरविले.
KTPS ने या कामासाठी न्युमॅकसह अनेक कंपन्यांकडे विचारणा केल्यानंतर सर्वांकडून यासंदर्भातील पर्याय समोर आले. त्या सर्वांमध्ये न्युमॅक कंपनीने दिलेला पर्याय KTPS ने संमत केला. संपूर्ण डिझाईन, त्याचा विकास आणि त्याचे प्रत्यक्षातील यंत्रण हे सर्व काम
KTPS ने न्युमॅककडे सोपविले होते. अतिशय कुशलतेने परंतु साधेपणाने विकसित करण्यात आलेल्या न्युमॅकच्या
3 पर्यायांपैकी एक पर्याय निवडण्यात आला.
टर्बाईन बेअरिंग एरियामध्ये दोन्ही बाजूने आधार असलेले बोअरिंग आणि यंत्रण करणारे विशिष्ट उपयोगिता मशिन
(चित्र क्र.1) बनविले. अशा विशेष व्यवस्थेमुळे मशिन तंतोतंत मध्यभागी राहून दोन्ही बाजूंचे सारखेच यंत्रण करणे शक्य होऊ शकले. या कामाचे तपशील थोडक्यात पुढे दिले आहेत.
1. केसिंगमध्ये दोन्ही बाजूला आधार असणारे आणि यंत्रणाचे काम तंतोतंत मोजमापात करणारे विशिष्ट प्रकारचे एस.पी.एम. विकसित केले.
2. हे एस.पी.एम. मध्यभागी स्थिर राहून दोन्ही बाजूला सारखेच समकेंद्री यंत्रण होईल यासाठी याला स्थिर पायाची योजना केली. या यंत्रणाच्या कामांसाठी विशेष बोअरिंग बार बनवून त्याला स्थिरता येण्यासाठी आधार (सपोर्ट) देण्यात आले.
3. प्रत्यक्ष यंत्रण करताना बोअरिंग बार स्थिर राहून कंपने येऊ नयेत म्हणून विशेष काळजी घेतली. यासाठी योग्य आधार बनविण्यात आले
.
4. संपूर्ण कार्यवस्तूचे माप घेणे, त्याचे डिझाईन, विशिष्ट उपयोगिता मशिन विकसित करणे, मशिन जागेवर स्थापित करणे, प्रत्यक्ष यंत्रण करणे, यावेळी मशिन स्थिर राहून कंपने येणार नाहीत याची दक्षता घेणे, तसेच योग्य प्रकारे समकेंद्री यंत्रण करून तंतोतंत मोजमापामध्ये यंत्रण करणे हे संपूर्ण काम आव्हानात्मक होते. आम्ही योग्य नियोजन, तांत्रिक कौशल्य, आमचा पूर्वानुभव आणि कुशल मनुष्यबळ यांच्या भरवशावर आधी अंदाज केलेल्या 51 दिवसांऐवजी केवळ 19 दिवसांत हे काम यशस्वीरीत्या पूर्ण करू शकलो.
5. प्रत्यक्ष काम करतांना काही कामे साखळी पद्धतीने एका पाठोपाठ एक (सिरीजमध्ये) करण्याचे नियोजन केले होते. परंतु योग्य समन्वय आणि नियोजन करून समांतर पद्धतीने काम करण्याची आखणी केली आणि त्यामुळे वेळेची मोठी बचत करता आली.
6. आधी रोज अंदाजे 10 ते 12 तास काम करण्याचे ठरविले, परंतु जास्तीचे कुशल मनुष्यबळ वापरून 2 समूहामध्ये वेगवेगळी कामे करून रोज अंदाजे 20 तास काम करू शकलो. यामुळे एकूण कालावधी बराच कमी झाला.
7. संभाव्य अडचणी आणि अडथळे यांवर आधीच चर्चा करून त्यावर योग्य उपाययोजना केली.
8. योग्य देखरेख आणि तज्ज्ञ व्यक्तींशी चर्चा करून, प्रत्यक्ष कामाचे परिस्थितीनुरूप योग्य निर्णय घेऊन, काम कोठेही थांबू नये याची काळजी घेतली.
अशाप्रकारे 19 दिवसांच्या अतिशय कमी वेळात आम्ही हे आव्हानात्मक काम पूर्ण करू शकलो. यंत्रण सुरू असताना पोलंडमधील इलेक्ट्रिमच्या 2 अभियंत्यांनी KTPS ला भेट दिली असता, त्यांनी कामाची प्रशंसा केली. त्यांनी असे नमूद केले की, ‘पोलंडमध्येसुद्धा या समस्येवर अशाप्रकारचा पर्याय दिला गेला नसता. अशाप्रकारचे काम अद्यापतरी आमच्याकडे आलेले नाही. अशी समस्या आमच्याकडे आली असती, तरी त्यासाठी केसिंग बदलणेच आम्ही अधिक पसंत केले असते.’
फायदे • जवळपास 2 कोटी रुपये प्रति युनिट एवढे मोठे आर्थिक नुकसान होण्यापासून वाचले.
• मशिन डाऊन टाईम
(25-30 दिवस) आणि त्यामुळे होणारे इतर नुकसान आणि आर्थिक नुकसान यात पकडलेले नाही. ते पकडल्यास हा आकडा 2 कोटी रुपयांच्या पुढे जाणारा आहे.
• साधारणपणे एकूण 9 कोटी रुपये वाचले. जेव्हा देखभालीसाठी इतर युनिट बंद केले जातात, त्यावेळी होणारे विद्युत निर्मितीचे नुकसान यामध्ये पकडलेले नाही.
केस स्टडी 2आता आपण खापरखेडा पॉवर स्टेशन येथे
2011 साली केलेल्या कामाचे तपशील पाहणार आहोत.
समस्याखापरखेडा थर्मल पॉवर स्टेशन येथील
210 MW च्या युनिट
4 मधील जनरेशन बंद पडल्याचे तेथील अधिकाऱ्यांच्या लक्षात आले. प्रथम कंपनीअंतर्गत अभियंत्यांकडून या समस्येचा शोध घेण्यात आला. तेव्हा जनरेटर रोटर
(चित्र क्र. 2) खराब झाल्यामुळे विद्युत निर्मिती थांबल्याचे लक्षात आले. तो पूर्ववत होण्यासाठी योग्य मटेरियलची बांधणी करून, जनरेटरच्या आकारानुसार अचूक यंत्रण करावे लागणार होते.
ही ॲसेम्ब्ली
250 टन वजनाची होती. एवढी मोठी ॲसेम्ब्ली सोडवून त्याचे भाग वेगळे करणे हे अतिशय वेळखाऊ काम होते. त्यातील भाग वेगळे केल्यानंतर यंत्रणासाठी ते वेगवेगळ्या ठिकाणी नेऊन, यंत्रण झाल्यानंतर ते परत पॉवर स्टेशनवर आणून त्यांची पूर्ववत व्यवस्थित ॲसेम्ब्ली करावी लागणार होती.
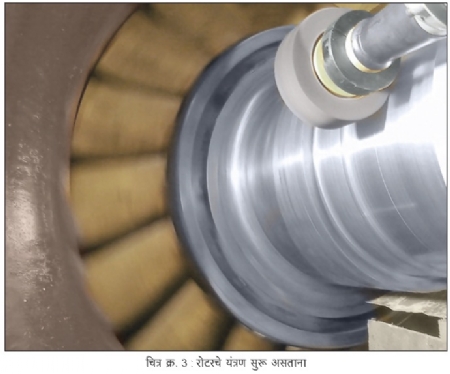
ज्या ज्या कंपन्यांकडे रोटर दुरुस्ती करण्याची मागणी केली होती त्या कंपन्यांचा सेटअप मोठा होता. हा यंत्रभाग करण्यासाठी सर्वजण समर्थ होते, परंतु त्यासाठी येणारा खर्च काही कोटी रुपयांमध्ये होता आणि लागणारा वेळही अधिक होता. यासाठी कमीतकमी 6 महिन्यांचा वेळ वाया जाणार होता, कामाच्या दृष्टीने परवडणारे नव्हते. बाकीच्या कंपन्यांच्या तुलनेत आमचा सेटअप अतिशय लहान होता. परंतु आम्ही हे आव्हान स्वीकारले. प्लँटमधील अभियंते आणि वरिष्ठ अधिकाऱ्यांशी चर्चा केली. आम्ही प्रत्यक्षात साईटवर जाऊन खराब झालेल्या यंत्रभागाची तपासणी केली आणि त्या यंत्रभागाजवळ उपलब्ध असलेली जागादेखील पाहिली. उपलब्ध परिस्थितीचा विचार करता आम्ही पॉवर स्टेशन प्लँटमध्येच हे यंत्रण करण्याचा निर्णय घेतला. आम्ही ती ॲसेम्ब्ली मोकळी (डिसमेंटल) न करता जागेवरच त्याचे यंत्रण करावे असे निश्चित केले. यामुळे वाहतूक, यंत्रभाग सुटे करणे आणि त्याची परत जुळणी करणे या सर्वांमध्ये वाया जाणारा वेळ आणि होणारा खर्च यामध्ये परिणामकारक बचत होणार होती. आम्ही यासाठी एक विशिष्ट उपयोगिता मशिन विकसित केले.
रोटरचा खराब झालेला भाग योग्य त्या मूळ मटेरियलने मेटलाईज्ड केला आणि साईटवरच रोटरचे यंत्रण आणि ग्राईंडिंग केले. असे विशिष्ट उपयोगिता मशिन विकसित करताना रोटर यंत्रण करण्याच्या जागी प्रत्यक्ष यंत्रण आणि फिनिशिंगच्या वेळी मशिनचा वेग आणि सरकवेग (स्पीड आणि फीड) याचे उत्तम संतुलन राखणे हे खरे आव्हान होते. त्यावरच यंत्रणाचे मोजमाप, अचूकता आणि गुणवत्ता ठरणार होती. या कार्याकरिता सलग 8 दिवस 6 ऑपरेटरचा कार्यगट साईटवर काम करत होता. वरिष्ठ अधिकारीदेखील कामाची प्रगती आणि गुणवत्ता यावर सातत्याने लक्ष ठेवून होते. या यंत्रभागाच्या यंत्रणातील अचूकता मिळविण्यात आम्ही यशस्वी ठरलो. हे यंत्रण पूर्ण केल्यापासून जनरेटर रोटरकडून आजपर्यंत कोणतीही तक्रार आलेली नाही. याशिवाय महानिर्मिती आणि इतर विद्युत कंपन्यांच्या निर्मिती केंद्रांमध्ये उद्भवलेल्या कित्येक गंभीर समस्यांवर आम्ही नियमित देखभाल आणि दुरुस्तीच्या कामांसाठी आमच्या सेवा उपलब्ध करून दिल्या आहेत. बंद पडलेली उपकरणे तातडीने दुरुस्त करून दिल्याने विद्युत निर्मितीचे संभाव्य नुकसान कमीतकमी ठेवण्यात आम्हाला यश मिळू शकले.
अलीकडच्या काळात आम्ही काही अभिनव कल्पना वापरून आमचे तांत्रिक कौशल्य, अनुभव, योग्य संकल्पना आणि नियोजनाद्वारे काही गंभीर स्वरुपाच्या समस्या आणि निर्माण झालेले तांत्रिक बिघाड यावर उपाय शोधून अशी नादुरुस्त मशिन लवकरात लवकर वापरात आणू शकलो.
केस स्टडी 3कोराडी थर्मल पॉवर स्टेशन (KTPS),
(युनिट 9 - 660 MW). आय.डी. फॅनमधील अपघाती बिघाड
येथील 660 MW क्षमतेचा निर्मिती संच चालू असताना, निर्माण झालेली अतिवेगवान कंपने आणि ओव्हरलोडिंगमुळे आय.डी. फॅन 9 ब संपूर्णरीत्या तुटला जाऊन त्यात गंभीर स्वरुपाचा बिघाड झाला. या बिघाडामुळे आय.डी. फॅन बेअरिंग सपोर्ट फाऊंडेशन, इंपेलर गाइड व्हेन, फिक्स्ड गाइड व्हेन आणि इतर संबंधित सामग्रीचे गंभीर नुकसान होऊन ही तुटलेली सामग्री बदलण्याचा एकमेव उपाय प्रथमदर्शनी तरी दिसत होता. 660 MW च्या अतिशय गंभीररीत्या तुटलेल्या आय.डी. फॅनचा बाहेरील व्यास 3.5 ते 4 मीटर असून, एकूण लांबी जवळपास 13 ते 14 मीटर आणि वजन 15 टनापर्यंत होते. दुरुस्तीचे काम साईटवर करणे अतिशय अवघड आणि आव्हानात्मक होते.
महानिर्मितीच्या वरिष्ठ अधिकाऱ्यांनी अनेक कंपन्यांच्या अभियंत्यांशी चर्चा केल्यानंतर सर्वांनीच हा तुटलेला फॅन दुरुस्तीकरिता मूळ निर्मिती केलेल्या कंपनीकडे पाठविण्याचा सल्ला दिला होता. एवढेच नव्हे, तर फॅन तयार केलेल्या हॉलंडमधील हौडण कंपनीच्या अभियंत्यांनीसुद्धा या फॅनची दुरुस्ती साईटवर शक्य नसून, त्यासाठी फॅन कंपनीकडे पाठविण्याचाच उपाय सुचविला. या प्रक्रियेमध्ये बराच खर्च होता आणि दुरुस्तीसाठी अंदाजे 4 महिन्यांचा कालावधी लागणार होता. महानिर्मिती कंपनीने आमच्याशी या संदर्भात चर्चा केली. त्यानंतर आम्ही हे संपूर्ण दुरुस्तीचे काम साईटवरच करून देण्याचे अवघड आव्हान स्वीकारले. योग्य नियोजन आणि तांत्रिक कल्पकता यांचा सुरेख मेळ घालून आम्ही हे आव्हानात्मक काम अतिशय अल्प खर्चात केवळ 20 ते 22 दिवसांच्या कमी काळात पूर्ण केले. बिघडलेला फॅन दुरुस्त केल्यानंतर पूर्ण क्षमतेने कार्यरत झाला. अशा प्रकारे या दुरुस्तीच्या कामामध्ये कंपनीचा बहुमूल्य असा 3 महिन्यांचा कालावधी आणि लाखो रुपयांची बचत झाली.
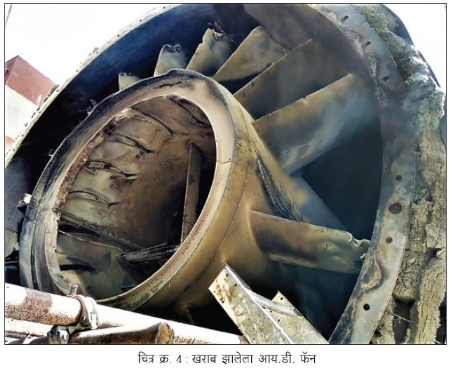
महानिर्मिती केंद्रामध्ये देखभाल आणि दुरुस्तीची कामे करीत असताना कित्येकदा मूळ कंपनीद्वारे बनविलेले महत्त्वाच्या उपकरणांचे सुटे भाग, तसेच आयात केलेल्या उपकरणांचे सुटे भाग उपलब्ध नसल्याने केवळ या सुट्या भागांसाठी अशी महत्त्वाची उपकरणे बंद ठेवायची वेळ येत असे. अशा वेळी मूळ कंपनीच्या आयात कराव्या लागणाऱ्या सुट्या भागांच्या जागी आम्ही असे सुटे भाग स्वत: विकसित केले. अशी महत्त्वाची मशिन लवकरात लवकर दुरुस्त करून वापरात आणण्यात आम्ही यशस्वी झालो.
अशाप्रकारची अनेक आव्हानात्मक कामे आपल्यासमोर येत असतात. बऱ्याचवेळा ते खूप मोठे काम आहे, आपल्याला झेपेल का, अशी शंका येऊन आपण त्यापासून लांब राहतो. मात्र, आपण लघु उद्योजक असलो तरी कल्पकतेत आणि कौशल्यामध्ये कुठेही कमी पडत नाही अशी जिद्द ठेवल्यास यश नक्की मिळते.