औरंगाबादमधील मायक्रो फॉर्म टूल्स ही आमची
ISO 9001:2008 प्रमाणित कंपनी आमच्या जगभरातील ग्राहकांच्या गरजा भागविण्याचे काम करते. मोठ्या संख्येने बनविल्या जाणाऱ्या उत्पादनासाठी कमी खर्चात जास्त उत्पादन काढण्याचे पर्याय आम्ही विकसित करतो. आमच्याकडील विशेष प्रोफाईल ग्राइंडर वापरून अचूक भौमितिक आकार बनविता येतात. त्यामुळे उत्तम सातत्य देणारे इन्सर्ट फॉर्म टूलिंगचे पर्याय ग्राहकांना उपलब्ध होतात.
आमच्याकडे प्रामुख्याने ऑप्टिकल प्रोफाईल ग्राइंडर (ओ.पी.जी.) आणि त्याबरोबर इतर संलग्न यंत्रसामग्री आणि तपासणीच्या सुविधा उपलब्ध असून, आमच्याकडील तज्ज्ञांकडून त्या चालविण्यात येतात. आमच्या उत्पादनांमध्ये प्रामुख्याने इन्वोल्युट प्रोफाईल टेस्टिंग प्रोब स्टायलस, स्प्लाइन गेज, स्टँडर्ड कार्बाईड ब्रेझ्ड टिप्ड टूल, हाय प्रिसिजन ब्रोच, एंड मिल आणि रीमर इत्यादी ग्राहकांच्या मागणीनुसार विशिष्ट आकारातील टूलचा (कस्टमाईज्ड फॉर्म टूल) समावेश आहे.
फॉर्म टूल म्हणजे एक किंवा त्याहून अधिक कडा असलेले, कार्यवस्तूवर अपेक्षित असलेल्या आकाराशी मिळते जुळते असणारे प्रोफाईल अथवा कंटूर असणारे टूल होय. फॉर्म टूलचा वापर करून कार्यवस्तुच्या पृष्ठभागावर क्लिष्ट आकार देणारे यंत्रण करता येते. फॉर्म टूलच्या कर्तन कडेचा (कटिंग एज) आकार कार्यवस्तूवर अपेक्षित असलेल्या आकाराच्या आरशातील प्रतिमेसारखा असतो. सर्वसाधारणपणे फॉर्म टूल साध्या मशिनवर वापरली जातात. मात्र, काहीवेळा ती आधुनिक सी.एन.सी. मशिनवर वापरणे योग्य ठरते. फॉर्म टूलचे काही महत्त्वाचे फायदे आहेत, ज्यामुळे योग्य कामासाठी त्यांचा वापर, सी.एन.सी. मशिनवर स्टँडर्ड टर्निंग इन्सर्टच्या वापरापेक्षा अधिक किफायतशीर ठरतो. फॉर्म टूलचा वापर केल्यामुळे उत्पादकता वाढण्याबरोबरच उत्पादांचा आकार आणि मापे यात सातत्य मिळते. या टूलचा वापर मुख्यतः एखाद्या कार्यवस्तूचे अधिक प्रमाणात उत्पादन करताना केला जातो.
फॉर्म टूलच्या रचनेची वैशिष्ट्येफॉर्म टूल बहुतांशी हाय स्पीड स्टील (एच.एस.एस.) मटेरियलपासून बनविलेली असतात. परंतु, आता फॉर्म टूलसाठी सिमेंटेड कार्बाईडचा वापर वाढू लागला आहे. 66 HRC कठीणता असलेली फॉर्म टूल बनविण्यासाठी टंग्स्टनचा वापर केला जात आहे. विशिष्ट आकाराच्या सिमेंटेड कार्बाईड टिपचा वापर फॉर्म टूलसाठी केल्यास एच.एस.एस. वापरून बनविलेल्या फॉर्म टूलपेक्षा 30 ते 40% उत्पादकता वाढते. फॉर्म टूलला योग्य रेक आणि रिलीफ कोन असल्यास धातू यंत्रणाचे काम चांगल्या पद्धतीने करता येते. फॉर्म टूलच्या प्रकारावर त्यावरील रिलीफ कोन अवलंबून असून, वर्तुळाकार फॉर्म टूलचा रिलीफ कोन 100 ते 120, सपाट फॉर्म टूलचा रिलीफ कोन 120 ते 150 असतो, तर मिलिंग कटरकडून रिलीव्हिंग मिळण्यासाठी फॉर्म टूलचा रिलीफ कोन 250 ते 300 इतका असतो.
वेगवेगळ्या गरजांसाठी आणि गुणवत्तेसाठी आम्ही नवनवीन फॉर्म टूल विकसित करीत असतो. अशा विकसित केलेल्या फॉर्म टूलची काही उदाहरणे पुढे दिली आहेत.
बेअरिंगच्या पोकळीच्या आकाराचे यंत्रण (आतील व्यास)चित्र क्र. 1 मध्ये बेअरिंगच्या पोकळीतील आतील व्यासाच्या प्रोफाईलचे यंत्रण करण्याचे उदाहरण दिले आहे. या आकाराची भौमितिक रचना जरी सोपी वाटत असेल तरी बेअरिंगच्या कामागीरीचा विचार केला तर ती गुंतागुंतीची होऊ शकते. याचे प्रामुख्याने असे कारण आहे की, संपूर्ण प्रोफाईलमध्ये वंगणाचा (ल्युब्रिकंट) प्रवाह एक सारख्या जाडीचा असणे आवश्यक आहे. बेअरिंगची
सर्वोत्तम कामगिरी मिळण्यासाठी पोकळीच्या भौमितिक आकाराच्या यंत्रणाची अचूकता, रिस्ट्रिक्टरचा आकार आणि बेअरिंग क्लिअरन्स या गोष्टी फार महत्त्वाच्या असतात.
डिझाईन केलेला आकार ऑप्टिकल प्रोफाईल ग्राइंडरवर तयार करून, प्रोफाईल प्रोजेक्टरवर तपासला जातो. या डिझाईनची वैधता उत्पादन प्रक्रियेमध्ये तपासली जाते, तसेच त्यावर चाचण्या करून ते ग्राहकाला दाखविले जाते. हे फॉर्म टूल चित्र क्र.
2 आणि
3 मध्ये दाखविले आहे.
विशिष्ट आकार तयार करण्यासाठी ऑप्टिकल प्रोफाईल ग्राइंडर आणि प्रोफाईल प्रोजेक्टरचा
(चित्र क्र. 4) वापर केला जातो. बाजारातून आणलेल्या ऑप्टिकल प्रोफाईल ग्राइंडरमध्ये योग्य ते बदल करून, याचा वापर आम्ही 600 मिमी. X 600 मिमी. आकाराच्या प्रोजेक्शनसाठी करून प्रतिमेचा आकार 20 पटीने मोठा केला.
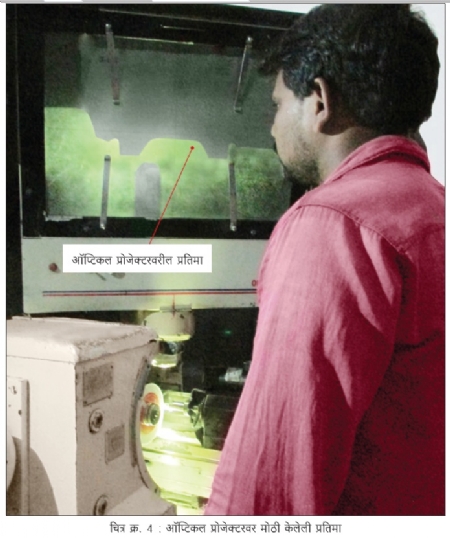
ऑप्टिकल प्रोफाईल ग्राइंडरवर अपेक्षित कंटूरची मोठी केलेली प्रतिमा, ग्राईंडिंग व्हीलची दिशा आणि मार्ग (पाथ) नियंत्रित करण्यासाठी वापरली जाते. काहीवेळा कॅडमधून मिळविलेली डिजिटल प्रोफाईलही ऑप्टिकल प्रोफाईल ग्राइंडरमध्ये वापरली जाते. यानंतर डाऊनलोड केलेल्या डिजिटल फाईलच्या आधारे मूळ भागाच्या प्रोफाईलमध्ये विंडोज इंटरफेसच्या साहाय्याने योग्य रिलीफ आणि इतर भौमितिक बदल करून घेतो. यानंतर कॅम यंत्रणा वापरून टूलचा योग्य तो मार्ग निर्माण केला जातो. ग्राईंडिंग व्हीलवर बहुअक्षीय (मल्टी ॲक्सिस) नियंत्रण असल्यामुळे टूलवर अपेक्षित कंटूर तयार केला जातो. टूलच्या कडेवर स्विव्हेलिंग व्हील सेट केल्यानंतर ग्राईंडिंग होत असताना टूलवर निर्माण होणाऱ्या आकारावर सॉफ्टवेअर लक्ष ठेवते आणि त्याची कॅड मॉडेलशी तुलना करीत राहते. मशिनवर बसविलेल्या व्हिजन यंत्रणेमुळे आधी निश्चित केलेल्या प्रोफाईलपेक्षा होणारे फरक ओळखले जातात आणि हा फरक भरून काढण्यासाठी योग्य ते ऑफसेट दिले जातात. यामुळे, व्हीलची झीज झाल्यामुळे किंवा इतर बदलांमुळे निर्माण होणारे दोष आपोआप काढून टाकले जातात.
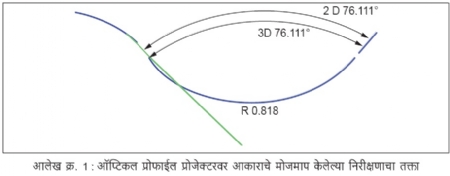
प्रोफाईल प्रोजेक्टरचा वापर करून अचूकरीत्या बनविलेल्या नमुना कंटूरचे द्विमिती
(2D) मोजमापन (आलेख क्र. 1) केले जाते. तसेच ऑप्टिकल यंत्रणेद्वारे त्या नमुन्याची मोठी प्रतिमा मशिनवरील पडद्यावर दाखविली जाते. प्रोजेक्टरने मोठा करून दाखविलेला नमुन्याचा आकार DROच्या मदतीने स्क्रीनवर लांबी रुंदीचे मोजमाप करण्यास सोपा पडतो.
फॉर्म टूल अधिक चांगल्या पद्धतीने करण्यासाठी इन्सर्टवर अपेक्षित फॉर्म तयार करता येतो. उदाहरणार्थ, चित्र क्र. 5 मध्ये दाखविल्याप्रमाणे वापरलेल्या इन्सर्टची भूमिती बदलून अपेक्षित भूमितीचे (कंटूरचे फॉर्म) टूल करता येते. आमच्या ग्राहकांसाठी कमी खर्चात केलेली ही सुधारणा आहे.
वापरलेल्या कार्बाईड इन्सर्टला पुन्हा धार लावणेवापरलेल्या इन्सर्टला धार लावून
(चित्र क्र. 6) मूळ भौमितिक आकार देण्याचे तंत्रज्ञान आम्ही विकसित केले आहे. या इन्सर्टना पुन्हा लेपन (कोटिंग) करून ते ग्राहकाला उपलब्ध करून दिल्यामुळे पुढील फायदे मिळण्यास मदत झाली.
फायदे • TiN लेपन.
• टूलची उच्च दर्जाची भौमितिक अचूकता आणि पृष्ठभागाचा उत्कृष्ट फिनिश.
• अगदी कमी किंमत.
• या इन्सर्टचे आयुष्य नव्या इन्सर्टच्या 90%
थ्रेड मिलिंग कटरसिंटर्ड ब्लँक वापरून पाहिजे तो फॉर्म मिळविता येतो आणि इंडेक्सेबल इन्सर्टचे उत्पादन करता येते. चित्र क्र. 7 मध्ये दाखविलेला थ्रेड मिलिंग कटर, आयात केल्या जाणाऱ्या थ्रेड मिलिंग कटरला पर्याय असणारा कटर भारतात विकसित केला आहे. आम्ही भारतात सिंटर्ड ब्लँकचा फुलफॉर्म थ्रेड मिलिंग कटर विकसित केला असून, ऑप्टिकल प्रोफाईल ग्राइंडरच्या मदतीने पाहिजे तो फॉर्म मिळविता येतो. यानंतर डिझाईन केलेल्या आकाराची वैधता प्रोजेक्टरवर तपासली आणि महत्त्वाची मापे, तसेच अचूकता यांची खात्री केली. तक्ता क्र. 1 मध्ये ग्राहकांना मिळणारे फायदे दाखविले आहेत.
फॉर्म टूलचे फायदे1. आवर्तन काळ : वेळेची बचत होते. एकच आकार फॉर्म टूलने केला, तर फॉर्म टूलच्या आत बाहेर होणाऱ्या एकाच हालचालीमध्ये, तो आकार सिंगल पॉईंट कटरने लागणाऱ्या वेळाच्या 1/3 वेळात पूर्ण करता येतो. जेव्हा उत्पादनाची संख्या जास्त असते, तेव्हा ही बचत या खास टूलमध्ये केलेली गुंतवणूक वसूल करते.
2. अचूकता : या टूलच्या वापरामुळे अचूकता मिळते, कारण यामध्ये बदल होणारे घटक कमी होतात. नेहमीचे कटिंग टूल वापरले तर त्याच्या हालचालींचा मार्ग दोन अक्षांनी ठरविला जातो, पण फॉर्म टूलच्या हालचालीसाठी मशिनचा एकच अक्ष वापरला जातो. प्रक्रियेत चुका घडवू शकतील असे हालचाल करणारे घटक कमी झाल्यामुळे फॉर्म टूल वापरून अतिशय काटेकोर आणि सातत्यपूर्ण अचूकता मिळविणे सहज शक्य होते.
3. पृष्ठीय फिनिश : सिंगल पॉईंट टूल वापरताना कटिंग टूल कार्यवस्तुच्या पृष्ठभागावरून फिरताना कार्यवस्तुच्या पाठोपाठच्या दोन फेऱ्यांच्या दरम्यान पृष्ठभागावर सूक्ष्म खड्डे येतात. फॉर्म टूल वापरल्यामुळे हे खड्डे येत नाहीत, कारण त्या कार्यवस्तुचा एक संपूर्ण भाग फॉर्म टूलमुळे एकाच प्लंजमध्ये कापला जातो. यामुळे चांगला फिनिश मिळतो.
प्रत्येक फॉर्म टूल वेगळे असते. ग्राहकाने दिलेल्या भूमितीप्रमाणे टूलचे आरेखन केले जाते. त्यामुळे फॉर्म टूलचा पुरवठा करताना स्टँडर्ड टूलपेक्षा बराच जास्त खर्च येतो. परंतु, वर दिलेल्या आवर्तन वेळ, अचूकता किंवा फिनिश अशा अनेक फायद्यांमुळे हा अतिरिक्त खर्च समर्थनीय ठरतो.
स्टँडर्ड आणि गरजेनुसार बनविलेल्या टूलच्या किंमतीची तुलना केली तरी खर्चातील फरक अचूकपणे लक्षात येत नाही. टूलचे आयुष्य हे त्यामागील एक कारण आहे. जेव्हा सिंगल पॉईंट काँटॅक्ट टूल कार्यवस्तूवरील एका आकाराचे यंत्रण करीत असते, तेव्हा टूलची झीज करणारी यंत्रणाची सर्व शक्ती एका इन्सर्टच्या लहान स्पर्शबिंदूवर केंद्रित होते. पण फॉर्म टूलचे यंत्रण (कटिंग) एका स्पर्शरेषेवर केले जात असल्यामुळे सर्व शक्ती त्या संपूर्ण रेषेच्या आकारावर विकेंद्रित केली जाते. त्यामुळे फॉर्म टूलची झीज कमी प्रमाणात होते. त्यामुळे इन्सर्टच्या खरेदीची गरज कमी निर्माण होते. तसेच टूल बदलण्यात जाणारा वेळही वाचतो. वापरलेली फॉर्म टूल पुन्हा धार लावून काही मर्यादित वेळा पुन्हा वापरता येतात.