औद्योगिक क्षेत्रातील विविध यंत्रभाग बनविताना वेगवेगळया धातूंवर आणि मशिनवर निरनिराळ्या कटिंग टूलच्या साहाय्याने वेगवेगळ्या कार्यपद्धतीचा वापर केला जातो. परंतु जोपर्यंत बनविलेला यंत्रभाग योग्य त्या तपासणीच्या स्वीकृती चाचण्यांमधून तावून सुलाखून निघत नाही, तोपर्यंत तो पूर्णत्वाला जात नाही. अनेकदा असे आढळून येते की, अपेक्षित पॅरामीटर मोजण्यासाठी योग्य ते उपकरण वा कार्यपद्धती निवडली गेली नाही, तर कदाचित त्या चाचणीत तो पॅरामीटर स्वीकारला जाऊ शकतो, परंतु प्रत्यक्ष त्या यंत्रभागाच्या जोडणीच्या वेळी त्याला नाकारले जाऊ शकते. त्यामुळे मोजमापन उपकरण आणि मोजमापन कार्यपद्धती यादेखील यंत्रण कार्यपद्धती इतक्याच काटेकोरपणे निवडल्या तरच व्यवसायात गुणवत्ता आणि किफायतशीरपणा या निकषांवर टिकून राहता येते.
आमच्या ’ॲक्युरेट’ कंपनीमार्फत मागील सुमारे 5 दशकांच्या वाटचालीत, मोजमापनाच्या क्षेत्रात भारतीय उद्योगांमध्ये अनेक आधुनिक उपकरणे विकसित करून, नव्याने बाजारपेठेत आणून ती यशस्वीपणे कार्यरत केली आहेत. या काळात आमच्या समोर आलेल्या आव्हानांचा सामना करताना आम्हाला आलेले अनुभव आणि त्यातून झालेल्या वेगवेगळ्या उपकरणांची निर्मिती आणि विकास वाचकांसमोर लेखाच्या माध्यमातून मांडण्याचा आमचा प्रयत्न आहे. या अंकात आपण आजच्या काळाला अनुरुप अशा को-ऑर्डिनेट मेजरिंग मशिनबद्दल (सी.एम.एम.) माहिती घेणार आहोत. त्यापूर्वी सी.एम.एम.चा उगम होण्यापूर्वीच्या काळातील यंत्रभाग तपासणीच्या काही पद्धतींवर आपण एक नजर टाकूया.
आपणा सर्वांना स्टीलची पट्टी (स्केल) किंवा त्यापेक्षा अचूक मोजमापन करणारे व्हर्निअर कॅलिपर/डेप्थ डायल यांसारखी उपकरणे बऱ्यापैकी परिचित आहेत. ही उपकरणे एका अक्षातील सरळ रेषेतील मापे मोजतात. (चित्र क्र.1) जर X, Y आणि Z या तीनही अक्षातील मोजमापन करणाऱ्या उपकरणाची कल्पना आपल्या मनामध्ये रेखाटली, तर जवळपास त्याप्रमाणेच सी.एम.एम. असेल.
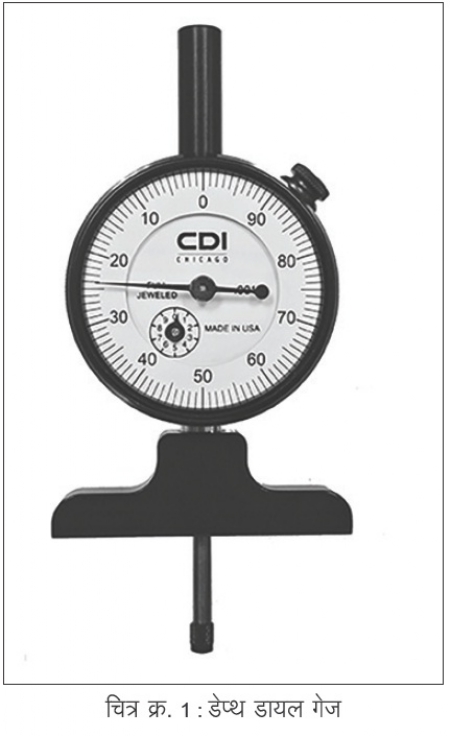
बहुतांशी उपकरणांमध्ये मोजमापन करताना उपकरणांचा विशिष्ट पृष्ठभाग यंत्रभागाला स्पर्श करतो. अशा पद्धतीला ‘कॉन्टॅक्ट टाईप मोजमापन पद्धती’ म्हणतात. कधीकधी अशा पद्धतीने मोजमापन करताना मिळालेले निष्कर्ष म्हणावे तितके अचूक किंवा सातत्यपूर्ण मिळतातच असे नाही, त्याला मऱ्यादा येऊ शकतात. याचे मुख्य कारण म्हणजे, अशा कार्यपद्धतीत अंतर्भूत असलेला मानवी कृतींचा सहभाग. मग तो उपकरणांच्या डायलवर दिलेल्या दाबाच्या फरकामुळे असेल किंवा तो यंत्रभागाचा संदर्भ घेताना (रेफरन्स घेणे किंवा ट्रू करणे) असेल. शिवाय अशा उपकरणांमध्ये जोडलेले भाग एकमेकांत स्लाईड होत असतात किंवा दात्यांमध्ये फिरत असतात. अशा जोडणीमध्ये असलेला रिलेटिव्ह बॅकलॅश हादेखील रिडिंगमध्ये फरक पडायला कारणीभूत होऊ शकतो. हा फरक पॉईंटरने रिडिंग दाखविणाऱ्या उपकरणात (ॲनालॉग टाईप) जास्त प्रमाणात दिसून येतो. हा फरक काढून टाकण्याच्या दृष्टीने डिजिटल प्रकारची उपकरणे विकसित झाली.
काही यंत्रभाग जर क्लिष्ट किंवा गुंतागुंतीचे असतील, तर मात्र काही मापे तो यंत्रभाग मशिनवरून खाली उतरवून ग्रॅनाईटच्यासरफेस प्लेटवर ठेवून इतर उपकरणांच्या मदतीने मोजावी लागतात. (चित्र क्र. 2) उदाहरणार्थ, अक्षांचा समकेंद्रीपणा (कॉन्सेंट्रिसिटी), अक्षांची कोनीय स्थिती (अँग्युलर पोझिशन), पृष्ठभागांचा गोलपणा (राउंडनेस) किंवा सपाटपणा (फ्लॅटनेस) इत्यादी. अशाप्रकारे तपासणी करण्याच्या पद्धतीला ’फर्स्ट प्रिन्सिपल’ने तपासणी करणे असे म्हणतात.
सरफेस प्लेटवरील मोजमापन पद्धतीमध्ये दोन प्रकारच्या मऱ्यादा प्रकर्षाने जाणवायच्या. एक म्हणजे तपासणी करायच्या यंत्रभागाचा रेफरन्स घ्यायला किंवा तो यंत्रभाग ट्रू करायला खूप वेळ जायचा. त्यामुळे एखादे सेटिंग बदलल्यानंतरचा यंत्रभाग तपासणी करून, तो ड्रॉईंगप्रमाणे आहे याची खात्री पटायला बराच वेळ जायचा. सी.एन.सी. सारखी महाग मशिन, यंत्रण झाल्यानंतर केवळ यंत्रभाग तपासून ’ओके’ आहे याची खात्री पटेपर्यंत बंद ठेवणे हे नक्कीच परवडण्यासारखे नव्हते. शिवाय मानवी चुकांमुळे तपासणीतील सातत्यदेखील मिळत नसायचे.
यावर सुरुवातीला असा तोडगा काढला गेला की, सी.एन.सी. मशिनवर एखाद्या यंत्रभागाचे यंत्रण पूर्ण झाल्यावर त्याच मशिनवर त्याची तपासणी करणे. त्याप्रमाणे काही ठराविक प्रकारच्या आज्ञावलीदेखील बनविल्या गेल्या. परंतु या तोडग्यातदेखील सी.एन.सी. मशिनवर यंत्रण थांबवून तपासणी करण्याची तरतूद केलेली असल्याने अपेक्षित उत्पादकता मिळायची नाही. शिवाय काही वर्षांनी मशिनच्या वापरानंतर तपासणीच्या अचूकतेचा दर्जादेखील खालावला जायचा.
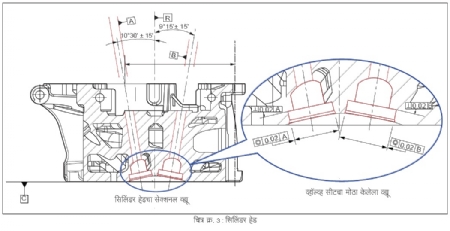
सी.एम.एम.ची गरज नेमकी कशी निर्माण झाली, हे समजून घेण्यासाठी आपण एका यंत्रभागाचे उदाहरण थोड्या विस्तृतपणे पाहू. आमच्या एका ग्राहकाकडून आलेले इंजिनच्या सिलिंडर हेड या यंत्रभागाच्या ड्रॉईंगचे काही भाग चित्र क्र. 3 मध्ये दाखविले आहेत. चित्रात दाखविल्याप्रमाणे काही महत्त्वाच्या निकषांवर त्यांना आमच्याकडून तपासणी करण्यासाठी योग्य असे उपकरण पाहिजे होते. चित्रात दाखविलेले व्हॉल्व्ह गाईड बोअर आणि व्हॉल्व्ह सीटचे यंत्रण हा या यंत्रभागाचा गाभा आहे. या दोन्हींचे इतर पृष्ठभागांबरोबरचे नातेदेखील (रिलेशन) तेवढेच अचूक आणि काटेकोर असणे हे इंजिनच्या कामगिरीच्या दृष्टीने महत्त्वाचे असते. त्यादृष्टीने काही महत्त्वाचे असलेले पॅरामीटर पुढे दिले आहेत शिवाय ते चित्र क्र. 3 मध्ये वेगळ्या रंगात दाखविले आहेत.
सिलिंडर हेडवरील मोजावयाचे काही महत्त्वाचे पॅरामीटर
1. रेस्टिंग पृष्ठभागाचा सपाटपणा-C
2. व्हॉल्व्ह गाईड बोअर आणि व्हॉल्व्ह सीट बोअरची स्वतंत्रपणे सिलिंड्रिसिटी, ओव्हॅलिटी
3. व्हॉल्व्ह गाईड बोअर आणि व्हॉल्व्ह सीट बोअरच्या अक्षांची रेस्टिंग पृष्ठभागाशी असलेली कोनीय स्थिती (अँग्युलर पोझिशन)
4. व्हॉल्व्ह गाईड बोअर आणि व्हॉल्व्ह सीट बोअरचा एकमेकांशी असलेला समकेंद्रीपणा (कॉन्सेन्ट्रिसिटी) - हा पॅरामीटर इतका महत्त्वाचा आहे की, सिलिंडरवर व्हॉल्व्हची जुळणी केल्यावर काही सेकंदांसाठी डिझेल वापरून लिकेज टेस्टिंग केले जाते.
हे पॅरामीटर सरफेस प्लेटवर फर्स्ट प्रिन्सिपलने तपासणे हे वेळखाऊ तर निश्चित होतेच, पण त्या तपासणीत होणाऱ्या संभाव्य मानवी चुकांमुळे खात्रीशीर अहवाल येण्याची शक्यता कमी होती. या मऱ्यादेमुळेच सी.एम.एम.सारख्या तपासणी मशिनचा टप्प्याटप्प्याने विकास होत गेला.
सी.एम.एम.च्या सध्याच्या रचनेतील वैशिष्ट्ये
चित्र क्र. 4 मध्ये सर्वसाधारणपणे 500 ते 800 मिमी लांबी, रुंदी, उंची या आकारात असलेल्या यंत्रभागाच्या तपासणीसाठी वापरात येणाऱ्या सी.एम.एम.ची रचना दाखविली आहे. यामध्ये तपासणीसाठी आलेला यंत्रभाग संतुलित आणि स्थिर ठेवण्यासाठी ग्रॅनाईटची सरफेस प्लेट भक्कम बेसवर बसवलेली असते. त्यावर अतिशय सुलभ आणि कंपनविरहीत X अक्षामधील हालचालीसाठी एअर बेअरिंगवर एक ब्रिज बसवलेला असतो. मशिनमधील हलणाऱ्या भागांची झीज होऊन त्याच्या अचूकतेवर परिणाम होऊ नये यासाठी मशिनचे हलणारे भाग आणि ग्रॅनाइटचे गाईड वे यामध्ये विशिष्ट दाबाची हवा सतत सोडली जाते. यामुळे मशिनचे आयुर्मान वाढते. ब्रिजवर Y अक्षाच्या हालचालीसाठी एक कॅरेज बसविलेले असते. उभ्या अक्षाच्या वर-खाली होणाऱ्या हालचाली या एका कॉलमवर दिलेल्या असतात. कॉन्टॅक्ट टाईप मोजमापनाच्या दृष्टीने एक प्रोब कॉलमच्या रॅमवर बसविलेला असतो. हा प्रोब X, Y आणि Z या तीनही अक्षांमध्ये पाहिजे तसा पुढे-मागे हालचाल करतो. ही हालचाल जॉयस्टीकच्या साहाय्याने हाताने करता येते किंवा स्वयंचलनानेदेखील होऊ शकते. वारंवार एकसारखे भाग जर तपासायचे असतील, तर एखादी आज्ञावली मशिनमध्ये आधी तयार करून ठेवून हे काम स्वयंचलनाद्वारे करता येते.
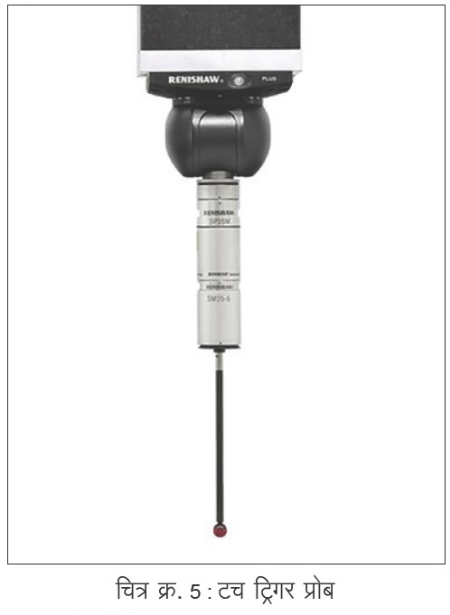
बहुतांशी प्रोब हे टच ट्रिगर प्रकारचे असतात. हे प्रोब (चित्र क्र. 5) जेव्हा यंत्रभागाच्या अपेक्षित पृष्ठभागाला स्पर्श करतात त्यावेळी निश्चित केलेल्या दाबानुसार एका सेन्सरमार्फत ते माप प्रोसेसरमध्ये नोंदले जाते. परंतु ज्यावेळी यंत्रभागांच्या काही पृष्ठभागांचा आकार मोजायचा असतो, (उदाहरणार्थ, इंपेलरच्या व्हेनची प्रोफाईल) अशावेळी स्कॅनिंग प्रोब वापरले जातात. (चित्र क्र. 6 आणि 7) हे प्रोब दिलेल्या आज्ञेप्रमाणे त्या दिशेने यंत्रभागाच्या संपर्कात राहून असंख्य निरीक्षणे नोंदवून घेतात आणि त्या प्रोफाईलचा नेमका आकार कसा आहे, ते अचूक सांगतात.
तपासणी करतेवेळी प्रोबचा स्पर्शबिंदू यंत्रभागाच्या नेमक्या कोणत्या जागी टेकणे गरजेचे आहे, हे त्या यंत्रभागाच्या रचनेवर अवलंबून असते. त्यामुळे वेगवेगळ्या आकाराचे आणि वेगवेगळ्या लांबीचे प्रोब मशिनबरोबर उपलब्ध करून दिलेले असतात. (चित्र क्र. 8) प्रोब हेडवर प्रोब बदलण्याची क्रिया हाताने किंवा स्वयंचलनाने करता येते.
प्रोब अतिशय नाजूक असल्याने तो काळजीपूर्वक हाताळावा लागतो, म्हणून ग्रॅनाईट प्लेटवर गरजेनुसार प्रोब पार्किंगची सोयदेखील केलेली असते. ही सोय स्वयंचलनाने प्रोब बदलताना उपयुक्त ठरते. (चित्र क्र. 9)
सी.एम.एम. वर प्रथम तपासावयाचा यंत्रभाग ग्रॅनाईट प्लेटवर X किंवा Y अक्षाला समांतर करून ठेवला जातो. तो व्यवस्थित स्थिरावला आहे याचीदेखील खात्री केली जाते. सी.एम.एम.मध्ये वेगवेगळे पॅरामीटर मोजण्यासाठी वेगवेगळे पऱ्याय (प्रोग्रॅम) उपलब्ध असतात. जो पॅरामीटर मोजावयाचा आहे त्याची आज्ञावली निवडून त्याला साजेसा प्रोब निवडावा लागतो. सुरुवातीला हाताच्या नियंत्रणाने प्रोब यंत्रभागाच्या पृष्ठभागाजवळ आणून आज्ञावलीप्रमाणे काळजीपूर्वक स्पर्श करून थोडासा दाब (प्रेशर) दिला जातो. ठराविक दाबानंतर ते निरीक्षण सेन्स करून प्रोसेसरमध्ये पाठवले जाते. अशा अनेक अपेक्षित निरीक्षणांचा संच झाला की, त्याआधारे त्या पॅरामीटरचे नेमके माप (व्हॅल्यू) आपल्याला मिळते. शिवाय ते ड्रॉईंगवर दिलेल्या टॉलरन्सच्या तुलनेत कसे आहे (स्वीकृत किंवा अस्वीकृत) तेदेखील सांगितले जाते. या अहवालाची छापील प्रत (प्रिंटआऊट) घेऊन तो अहवाल संग्रहित केला जातो. नमुन्यादाखल सिलिंडर हेडचा अहवाल चित्र क्र.10 मध्ये दिला आहे.
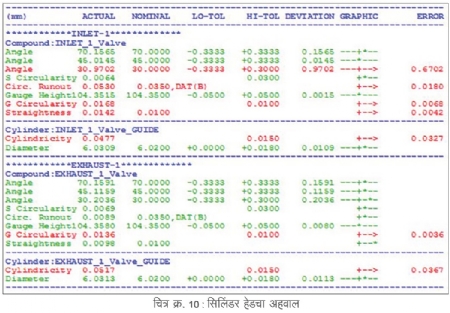
तपासावयाच्या यंत्रभागाचा आकार, त्याचे माप आणि त्यावर तपासणी करावयाचे पॅरामीटर आणि त्यांची क्लिष्टता यावरून आम्ही आमची सी.एम.एम.ची उत्पादने वरचेवर विकसित करत गेलो. या कामी प्रोबच्या विकासात ’रेनिशॉ’ कंपनीने आमच्याबरोबरीने मोलाचे योगदान दिले आहे. क्लिष्ट आणि अचूक यंत्रभागांचे यंत्रण करणाऱ्या लघु आणि मध्यम आकाराच्या उद्योजकांकडेही आता सी.एम.एम. असणे ही गरजेची बाब झालेली आहे. सी.एम.एम.च्या मालिकेत आमची अनेक मॉडेल बाजारात उपलब्ध आहेत. त्यातील काही मॉडेल चित्र क्र. 11, 12, 13 मध्ये दिली आहेत.
तसे पाहता सी.एम.एम.चे तंत्रज्ञान प्रथम 1965 च्या सुमारास युरोपमध्ये विकसित झाले. पुढे युनायटेड किंग्डम, इटली, जर्मनीसारख्या देशांनी त्यामध्ये नैपुण्य मिळवले. आमच्याकडे अशाप्रकारचे सी.एम.एम. बनविण्याचा विचार 1985 च्या सुमारास झाला. प्रत्यक्ष उत्पादन 1991 च्या सुमारास झाले. मशिन तयार होण्याच्या काळात अशी मशिन महाग असल्याने त्यांची संख्या तुरळकच असायची. अशा परिस्थितीत मशिनचे कव्हर काढून आतील भाग बारकाईने पहायचे अवघडच होते. त्यामुळे असे सी.एम.एम. आमच्या कंपनीत बनविण्यासाठी बऱ्याचशा भागांची कल्पना करणे किंवा एअर बेअरिंगसारख्या भागांसाठी, त्यांचे निकामी झालेल्या भागांचे रिव्हर्स इंजिनिअरिंग करणे याशिवाय दुसरा पर्याय नव्हता.
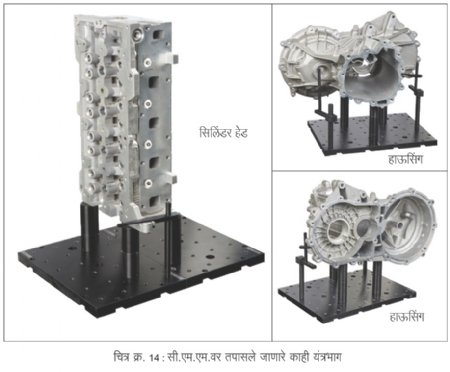
दुसरी आव्हानात्मक परिस्थिती म्हणजे इलेक्ट्रॉनिक सेन्सरसारख्या भागांचा विकास करणे. त्याकाळी अशा भागांवर 100 टक्के आयात शुल्क (इम्पोर्ट ड्युटी) असल्याने त्या काळात आम्हाला पहिले एक मशिन तयार करण्यासाठी सुमारे 10 लाख रुपये खर्च करावे लागले. या मशिनची अचूकता तपासण्यासाठी आवश्यक असणारे लेझर मशिनही खूप महागडे असल्याने आम्ही काही मशिन टूल उत्पादकांकडे असलेले मशिन वापरून ही गरज भागवली. भारतात संगणकाचा विस्तार त्याकाळात नुकताच सुरू झाला होता. आम्ही मशिनमधील गणिताची समीकरणे मांडण्यासाठी पहिला प्रोग्रॅम संगणक आधारित मायक्रोप्रोसेसर वापरून हे आव्हान समर्थपणे पेलले. सुमारे 3 वर्षांच्या अथक परिश्रमातून पहिले नमुना मशिन आम्ही तयार केले. बंगळुरूच्या ‘धातू निर्माण’ या कंपनीने आमच्यावर विेशास ठेऊन पहिले मशिन विकत घेतले आणि आमचा सी.एम.एम. मशिन उत्पादनाचा प्रवास 1991-92 पासून सुरू झाला.
सी.एम.एम.सारख्या अत्याधुनिक आणि किंमती मशिनच्या देखभालीचा खर्च परवडण्याजोगा असेल का? अशा प्रकारची एक भीती काही उद्योजकांच्या मनात असण्याची शक्यता असते. मशिनचीच किंमत एवढी जास्त, तर त्याला वरचेवर लागणारे भागदेखील (स्पेअर) महाग असणार आणि त्यामुळे हे मशिन कारखान्यात बसवून वापरणे आपल्या आवाक्याबाहेर जाईल अशी भावनाही अनेकांनी आमच्याकडे व्यक्त केली होती. परंतु हा एक भ्रम आहे. हे मशिन प्रामुख्याने एअर बेअरिंगवर काम करत असल्यामुळे यामध्ये एकमेकांत घासून झीज होणारे असे कुठलेच भाग नाहीत. त्यामुळे भाग सहसा बदलावे लागत नाहीत. परंतु ठराविक काळानंतर मशिनचे कॅलिब्रेशन करून अचूकतेची खात्री करणे गरजेचे असते. जर ग्राहकाने आमच्याबरोबर ए.एम.सी. (ॲन्युअल मेंटेनन्स कॉन्ट्रॅक्ट) केले तर आम्ही या कॅलिब्रेशनची संपूर्ण जबाबदारी स्वीकारतो.
यावेळी बदलाव्या लागणाऱ्या इलेक्ट्रॉनिक भागांचा (पार्ट) खर्च मात्र काही प्रमाणात असतो. पण तो परिस्थितीनुसार बदलत राहतो. तसेच इलेक्ट्रॉनिक्स प्रोबवर बसविलेले स्टायलस काहीवेळा बदलावे लागण्याची शक्यता असते. परंतु त्याचा खर्च दोन ते पाच हजार रुपयांच्या आसपास असतो.
अनेक आव्हानांचा सामना करत विदेशी उत्पादनाच्या तोडीस तोड उपकरणे आम्ही उपलब्ध करून देत आहोत. तसेच आमची उत्पादने विदेशी उत्पादनांच्या किंमतीच्या तुलनेत सुमारे 25 ते 40% स्वस्त आहेत. या दोन्ही गोष्टी आमच्या दृष्टीने अभिमानाच्या आहेत.
cmmapplication@accurategauging.com
यांत्रिकी अभियंते असलेले मोमिन ए. वाय.सध्या अक्युरेट गेजिंग अँड इन्स्ट्रुमेंट्स प्रा. लि.मध्ये अप्लिकेशन अँड ट्रेनिंग विभागाचे प्रमुख आहेत. त्यांना या क्षेत्रामधील 25 वर्षांचा अनुभव आहे.