उद्यम प्रकाशन’च्या ‘धातुकाम’ मासिकाचे नोव्हेंबर 2017 आिडिसेंबर 2017 या महिन्याचे अंक माझ्या वाचनात आले होते. यामध्ये प्रामुख्याने इंडस्ट्री 4.0 आणि क्लाऊडच्या साहाय्याने उत्पादन कार्यक्षमतेचा मागोवा घेणारे एकमेकांशी संलग्न असलेले लेख होते.
आजकाल या अनुषंगाने औद्योगिक जगतात बरेच शब्द वरचेवर कानावर पडतात. उदाहरणार्थ, ऑटोमेशन, रोबोटिक्स, आर्टिफिशियल इंटेलिजन्स, क्लाऊड कॉम्प्युटिंग, मशिन लर्निंग, एम.टू एम., IIoT, स्मार्ट मॅन्युफॅक्चरिंग, डिजिटल नेटवर्किंग, डिजिटल ट्रान्सफॉर्मेशन इत्यादी. पण अजूनही या शब्दांबद्दलचे नेमके आकलन आणि या विषयाचा व्यवसायात जास्तीत जास्त फायदा नेमका कसा करून घ्यायचा या गोष्टींबद्दल कारखान्यात काम करणाऱ्या बऱ्याच लोकांमध्ये पुरेशी जागरूकता नाही असे चित्र बऱ्याचदा पहायला मिळते.
आम्ही, ‘इंजेनिअस’ आणि ‘ॲसेंट इंटेलीमेशन प्रा. लि.’ या दोन्ही कंपन्यातर्फे संयुक्तपणे काम करून भारतात आणि भारताबाहेरच्या ग्राहकांना त्यांच्या गरजेनुसार सेवा पुरवतो. ‘इंजेनिअस’ ही आधुनिक तंत्रज्ञानाचा उपयोग करून अनोखी लर्निंग सोल्युशन देणारी कंपनी आहे, तर ‘ॲसेंट इंटेलीमेशन प्रा. लि.’ ही औद्योगिक स्वयंचलन, खासकरून IoT आणि IIoT या माध्यमाचा वापर करून मशिनसामग्री किंवा मालमत्तेचे दूरवरून व्यवस्थापन (रिमोट ॲसेट मॅनेजमेंट) यामध्ये नैपुण्य असणारी कंपनी आहे.
कित्येकदा असे जाणवते की, बरेचसे लघु किंवा मध्यम उद्योजक आणि त्यांचे सहकारी आपल्या उद्योगांची कार्यक्षमता पातळी उंचावण्याच्या दृष्टीने बरेच जागरूकझालेले आहेत. ही कार्यक्षमता उंचावताना तेथील प्रत्येक गोष्टीत होणारा अपव्यय शोधून काढून, त्याची कारणमीमांसा करून आणि त्यावर योग्य उपाय अंमलात आणून त्याला प्रतिबंध करणे हा एक सरधोपट मार्ग अवलंबलेला दिसतो. ओ.ई.ई. या तंत्राचा वापर करून हेच काम शास्त्रशुध्द पद्धतीने केले जाते.
ओ.ई.ई.च्या माध्यमातून काम करताना होणारे नुकसान किंवा अपव्यय यांची खालील तीन प्रकारात वर्गवारी केली जाते.
अ) कार्यक्षमता अपव्यय - शास्त्रोक्त पद्धतीने मांडलेल्या अपेक्षित पातळीशी प्रत्यक्ष वापरलेल्या स्पीड, फीडमधील तफावत आणि कामगाराच्या कार्यक्षमतेतील तफावत यामुळे येणारी उत्पादनामधील घट.
आ) उपलब्धता अपव्यय - मशिन, मटेरियल, टूल किंवा कामगार उपलब्ध नसल्यामुळे होणारा किंवा सेटअप बदलताना होणारा वेळेचा अपव्यय आणि त्यामुळे येणारी घट.
इ) गुणवत्ता अपव्यय - सेटअप बदलल्यावर होणाऱ्या पहिल्या कार्यवस्तूवरील नमुना (ट्रायल)उत्पादन किंवा उत्पादन प्रक्रियेत होणारे रिजेक्शन यामुळे होणारा अपव्यय आणि त्यामुळे होणारी घट.
या लेखाच्या अनुषंगाने आपण मशिनसामग्रीच्या उपलब्धतेच्या बाबतीत होणाऱ्या अपव्ययावर लक्ष केंद्रित करू. कित्येकवेळा असे आढळून येते की, अशा अपव्ययाची कारणे शोधताना महत्त्वाच्या अशा ठराविक कारणातच (ए क्लास)वर्गवारी केली जाते, किंबहुना ती तशी करणे सोपेही जाते. परंतु काही बारीकसारीककारणांमुळे होणारा अपव्यय नेमका शोधणे आणि सातत्याने त्याची नोंद करणे हे खूप जिकिरीचे होऊन बसते. अशा बारीकसारीक कारणांमुळे होणारा अपव्यय हा ‘इतर’ या ढोबळ वर्गवारीत नोंदला जातो. त्यामुळे त्याकडे दुर्लक्ष होते. त्याची पुरेशी नोंद नसल्यामुळे शास्त्रोक्त पद्धतीने त्यावर उपाययोजना होत नाहीत. पर्यायाने कार्यक्षमता उंचावण्याच्या प्रक्रियेला येथे खीळ बसण्याची शक्यता असते.
हाच मुद्दा घेऊन आमच्या एका भारतीय ग्राहकाने आमच्याकडे विचारणा केली. त्यांच्या उद्योगामध्ये अशा प्रकारे होणाऱ्या अपव्ययाची त्याचवेळी (रियल टाईम) नोंद करणे, योग्य कारणात त्याची वर्गवारी करून ठराविक कालावधीचा संक्षिप्त अहवाल देणे आणि संबंधितांकडे तो अहवाल पोहोचवून त्यावर तातडीने उपाययोजना करण्याबद्दल वरचेवर जागरूक करणे हे काम त्यांना संगणकीय आज्ञावलीमार्फत करून पाहिजे होते. शिवाय ही आज्ञावली त्यांच्या ई.आर.पी. यंत्रणेला सहज जोडली जाणारी असावी अशी त्यांची अपेक्षा होती. या लेखात ‘प्लँट कनेक्ट - एस फॅक्टरी’ ही प्रणाली वापरून प्रत्यक्षात अंमलात आणलेल्या उदाहरणावरून, इंडस्ट्री 4.0 चे बारकावे, त्यातील नेमकेपणा आणि त्याची उपयुक्तता वाचकापुढे मांडण्याचा प्रयत्न केला आहे.
या ग्राहकाकडे असलेल्या उद्योगामध्ये विविध प्रकारच्या, लहानमोठ्या आकाराच्या कार्यवस्तू अधिकतम संख्येने (बल्क क्वांटिटी) बनविल्या जातात. यासाठी वापरलेली मशिनसामग्री ही मल्टीस्टेशन आणि जास्तीत जास्त स्वयंचलनाचा अवलंब करून बनविलेली आहे. या कार्यवस्तू बनविण्याचा आवर्तन काळ (सायकल टाईम) काही सेकंदांमध्ये आहे. यातील एक प्रातिनिधिक मशिन चित्र क्र. 1 मध्ये दाखविले आहे. या मशिनवरील आवर्तन काळ हा 4.65 सेकंद एवढा कमी आहे.
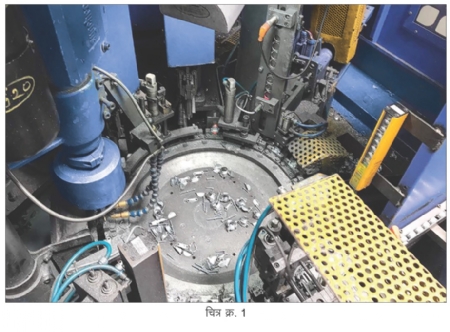
कधी कधी स्वयंचलनाने काम चालू असताना काही कारणाने त्यामध्ये खंड पडायचा. ही कारणे बऱ्याचदा त्या स्वयंचलनामध्ये पुरविलेल्या इंटरलॉकमुळेसुद्धा असायची. पण उत्पादनामध्ये हा पडलेला खंड निदर्शनास येऊन संबंधित कामगाराने त्याचे नेमकेकारण शोधून ते नियंत्रणात आणेपर्यंत बराच वेळ वाया जायचा. या वाया जाणाऱ्या वेळाची नेमक्या कारणासह नोंद व्हायची नाही. साहजिकच नोंद नसल्यामुळे अशा गोष्टींचे विश्लेषण करून त्यावर रास्त उपाययोजना करणे कठीण होऊन बसायचे. अशारीतीने कार्यक्षमता उंचावण्याच्या उपक्रमांना काही प्रमाणात खीळ बसायची. या सर्व परिस्थितीचे अवलोकन केल्यावर आमचे लक्ष पुढील गोष्टींवर केंद्रित करावे लागणार होते. माहिती (डेटा) त्या त्या वेळी गोळा करण्यासाठीची तरतूद करणे, ती नेटवर्किंगमार्फत पुढे पाठवून त्याचे सुयोग्य विश्लेषण करणे, त्याचे अहवाल तयार करणे, याबरोबरच नुकसानीची नेमकी कारणे शोधायला मदत करून, योग्य तो निर्णय घेण्याच्या प्रक्रियेला चालना देणे इत्यादी.
‘ॲसेंट इंटेलीमेशन प्रा. लि.’ च्या अध्यक्षा सुजाता टिळक यांनी तयार केलेले मॉडेल आराखड्याच्या रुपात चित्र क्र. 2 मध्ये दाखविले आहे. या चित्रात दाखविलेला आराखडा थोडक्यात खाली क्रमवार होणाऱ्या घडामोडींमार्फत सांगायचा प्रयत्न केला आहे.
1) लाल रंगातील तुटक वर्तुळात दाखवलेली उपकरणे म्हणजे कारखान्यातील वेगवेगळी मशिन किंवा साधने आहेत, ज्यावर संवेदकाच्या (सेन्सर) माध्यमातून त्यांचे दिवसभरातले होणारे काम याची नोंद केली जाते.
2) वर गोळा केलेली माहिती जांभळ्या रंगाच्या तुटक वर्तुळात दाखविलेल्या वेगवेगळ्या राऊटरमार्फत पुढे क्लाऊड किंवा सर्व्हरकडे पाठविली जाते.
3) आकाशी रंगाच्या तुटक वर्तुळात दाखविलेल्या सर्व्हरमध्ये राऊटरकडून आलेली माहिती एकत्रित आणि ठराविक पद्धतीने साठवून ठेवून त्याचे वेगवेगळ्या निकषांवर विश्लेषण केले जाते. यामध्ये कृत्रिम बुद्धिमत्ता (आर्टिफिशियल इंटेलिजन्स) किंवा काही प्रगत सॉफ्टवेअर वापरलेली असतात. अशी सॉफ्टवेअर कल्पकतेने बनविणे हेच खरे या विषयाचे गमक आहे.
4) निरनिराळ्या विश्लेषणानंतर निळ्या तुटक वर्तुळात दाखविल्याप्रमाणे त्यातून मिळालेले अहवाल हे निरनिराळ्या फॉरमॅटमध्ये तयार होतात. हे अहवाल पुढे संबंधितांकडे पुढील कार्यवाहीसाठी पाठविले जातात किंवा ठराविक ठिकाणी ते सर्वांच्या माहितीसाठी प्रदर्शित केले जातात.
5) काळ्या तुटक वर्तुळात दाखविल्याप्रमाणे हे अहवाल कारखान्यातील वेगवेगळ्या श्रेणीतील पदक्रमानुसार (हायरार्की) संबंधितांकडे पाठवून त्यांना योग्य ते निर्णय घ्यायला आणि राबवायल साहाय्यभूत ठरतात.
वर उल्लेख केलेल्या बारीकसारीककारणांनी उत्पादनात खंड पडून होणाऱ्या अपव्ययाची तत्परतेने नोंद होण्यासाठी आम्ही आमच्या प्रणालीमध्ये काही आज्ञावली तयार केल्या. उदाहरणार्थ, खंड पडल्यानंतरच्या ठराविक आवर्तनापर्यंतजर ते मशिन ठीक करून (रिसेट करून) त्याच्यावर पूर्ववत उत्पादन सुरू झाले नाही तर त्याची त्वरित दखल घेऊन योग्य त्या कारणापुढे त्याची नोंद करणे आणि त्याचा संदेश मशिनच्या पडद्यावर देऊन संबंधिताचे लक्ष खेचून घेणे. यामुळे आलेली अडचण कमीतकमी वेळात दूर करून खंडित उत्पादन सुरू करणे शक्य होते. शिवाय अशा येणाऱ्या अडचणींची वारंवारिता आणि प्रत्येक वर्गवारीत एकूण वाया गेलेला कालावधी याचे दर आठवड्याचे किंवा दर महिन्याचे सारांश अहवाल या स्वरुपात उपलब्ध होऊ शकतात. वरील प्रातिनिधिक मशिनवर आम्ही दोन आवर्तनाचे सेटिंग केले आहे. म्हणजेच उत्पादनात (2 x 4.65) 10 सेकंदापेक्षा जास्त काळ खंड पडला तर या प्रणालीमार्फत त्याची आपोआप नोंद घेणे आणि पुढे संदेश देणे हे कार्य चालू होते.
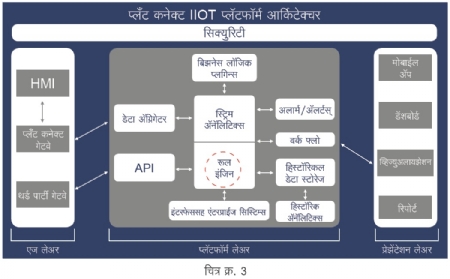
आमच्या प्रणालीचे हे वैशिष्ट्य चित्र क्र. 3 मधून जास्त समर्पकपणे समजावून सांगता येते. चित्र क्र. 3 मध्ये लाल रंगाच्या तुटक वर्तुळात दाखविल्याप्रमाणे ‘रुल इंजिन’ हा भाग गोळा केलेल्या माहितीचे योग्य ते विश्लेषण करून आलेल्या अडचणीच्या मुळाशी जायचे काम करण्याबरोबरच त्यावर योग्य उपाययोजना पण सुचवितो.
वस्त्रोद्योगातील एका ग्राहकाकडे बसविलेल्या ’प्लँट कनेक्ट एस-फॅक्टरी’ आज्ञावलीमार्फत गेल्या 3 महिन्यातील अपव्यय झालेल्या वेळेची नोंद केलेले एप्रिल 2018, मे 2018 आणि जून 2018 चे स्क्रीनशॉट चित्र क्र. 4, 5, 6 मध्ये आणि त्याचा संकलित केलेला सारांश स्वरुपातील आलेख, चित्र क्र. 7 मध्ये दिला आहे.
या आज्ञावलीचे अजून एक वैशिष्ट्य म्हणजे या आज्ञावलीच्या मेंटेनन्स मॉड्युलमध्ये याचा होणारा किफायतशीर वापर. सर्वसाधारणपणे कुठल्याही मशिनचे मोटर, बेअरिंग, ब्रश, ऑईल इत्यादीसारखे काही मुख्य भाग बदलतानाचे वेळापत्रक हे त्याचे ठरवून दिलेले आयुर्मान किती काळ आहे यावर आधारित असते. (शेड्युल बेस्ड मेंटेनन्स). परंतु प्रत्यक्ष या भागांचा कार्यकाळ नेमका किती वापरून झालाय आणि त्याचे आयुर्मान किती शिल्लक आहे याचे गणित तिथे काम करणाऱ्या मानवी हस्तक्षेपाचा (ह्युमन एलिमेंट) वापर करून सातत्याने आणि अचूकतेने मांडणे हे केवळ राबवायला अवघड तसेच ग्राह्य धरायला कठीण जाते. त्यामुळे या प्रकारच्या कार्यपद्धतीमध्ये हे बदलले जाणारे भाग वेळेत बदलले न जाता उशिरा बदलले जाण्याची शक्यता असते, ज्यामध्ये उत्पादनाचा गुणवत्ता दर्जा खालावण्याची शक्यता असते किंवा हे भाग त्यांचे आयुर्मान संपायच्या आत बदलले जाऊन उत्पादन अकारण खर्चिक होते. या आज्ञावलीतून प्रत्येक भागाचा वापर नेमका किती झाला आहे हे सातत्याने नोंदले जात असल्याने (रियल टाईम डेटा) त्या भागाचे ठरवून दिलेले आयुष्य वापरले गेले की, संबंधित व्यक्तीला त्याच्या संगणकावर संदेश पोहोचवला जातो आणि त्याची दखल घेऊन निर्णयाची प्रत्यक्ष अंमलबजावणी करेपर्यंत तो संदेश वारंवार झळकत राहतो. याला ’कंडिशन बेस्ड मेंटेनन्स’ म्हणतात. अशारीतीने योग्यवेळी कृती केल्यामुळे संभाव्य रिजेक्शनमुळे होणारे नुकसान आि आयुर्मान संपण्याआधी बदलल्या गेलेल्या भागांमुळे अकारण होणारा खर्च हे दोन्ही टाळले जाते.
आमचे हे ‘प्लँट कनेक्ट - एस फॅक्टरी सॉफ्टवेअर’ सध्या सातारा जिल्ह्यातील वाई औद्योगिक वसाहतीतील ’गरवारे वॉल रोप्स लि.’ तसेच अहमदनगर औद्योगिक वसाहतीतील ’एल. अँड टी. स्विचगिअर’ या कंपनीतदेखील यशस्वीपणे कार्यरत आहे.
भविष्यामध्ये आमच्या या आज्ञावलीमध्ये नवीन तंत्रज्ञान वापरून सुधारणा करताना बिझनेस ॲनालिसिस मॉड्युल, टूलिंग मॅनेजमेंट, टूलरूम वर्क फ्लो, एस.पी. सी. टेक्निक, बेंच मार्किंग या मुद्द्यांवर भर देण्याचा विचार आहे.
sudhir@santechnomentors.com
यांत्रिकी अभियंते असलेले सुधीर पंडितराव हे सॅन टेक्नो मेन्टॉर्स प्रा. लि. कंपनीचे संचालक आहेत. इन्स्ट्रुमेंटेशन आणि ऑटोमेशन इंडस्ट्रीचा त्यांना जवळपास 32 वर्षांचा अनुभव आहे.