बहुतांश महत्त्वाच्या उद्योगातील वर्कशॉपमध्ये उत्पादनाचे मोजमापन करणारी निरनिराळी गेज त्यांच्या मध्यवर्ती गेज लॅबोरेटरीमध्ये ठराविक कालमर्यादेमध्ये कॅलिब्रेट केली जातात. विविध मोजमापांच्या गेज तपासणीसाठी विविध आकाराची स्लिप गेज वापरली जातात. या स्लिप गेजलाच ‘गेज ब्लॉक’ असेही नाव आहे. हार्डन टूल स्टील, टंग्स्टन कार्बाइड आणि सिरॅमिक वापरून गेज ब्लॉक बनविलेले असतात.
0.5 मिमी. ते 100 मिमी.पर्यंतच्या निरनिराळ्या आकाराच्या गेज ब्लॉकचे काही ठराविक सेट वापरले जातात. उदाहरणार्थ 122, 112 किंवा 87 गेज ब्लॉकचा एक सेट (चित्र क्र. 1) असतो. हे गेज ब्लॉक मेट्रिक (M) किंवा इंपिरीयल (I) या दोन्ही मापन पद्धतीत वापरले जातात. त्यामुळे त्यांना I87, M122 आदी पद्धतीने संबोधले जाते. गेज लॅबमधील गेज ब्लॉक शॉप मास्टरचे काम करतात. परंतु, गुणवत्तेतील उच्च पातळीची काळजी घेण्यासाठी शॉप मास्टर असलेले गेज ब्लॉकदेखील ठराविक काळाने तपासून घेण्याची गरज असते. ISO ने यासाठी काही दंडक (तक्ता क्र. 1) घालून दिलेले आहेत. त्याचे पालन काटेकोरपणे होणे आवश्यक असते. अशा गेज ब्लॉकच्या अचूक मोजमापनाचे कार्य ज्या मशिनमुळे शक्य होते, ते गेज ब्लॉक कंपॅरेटर मशिन (चित्र क्र. 2)
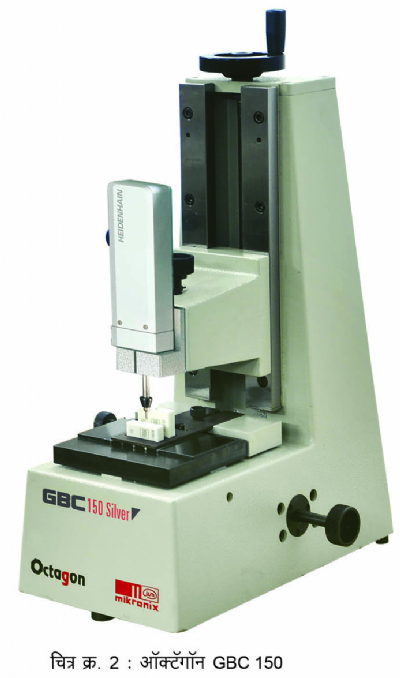
आमच्या ‘ऑक्टॅगॉन’मध्ये तयार होते. गेली वीस वर्षे आम्ही अचूकतेच्या क्षेत्रातील एक अग्रगण्य कंपनी असा लौकिक प्राप्त केला आहे. अचूकतेच्या क्षेत्रामधील जगप्रसिद्ध अशा MAHR आणि TESA अशा परकीय उद्योगसमूहांच्या उत्पादनाच्या तोडीचे उत्पादन आम्ही भारतामध्ये यशस्वीपणे करीत आहोत. भारतातील नॅशनल फिजिकल लॅबोरेटरीपासून (NPL) स्वित्झर्लंडमधील मेटास अशा नामांकित प्रयोगशाळांनी आमच्या उत्पादनांचा दर्जा तपासून त्याची ग्वाही दिलेली आहे.
ISO 3650 प्रमाणे 10 मिमी. आकारापर्यंतच्या गेज ब्लॉकचा क्रॉस सेक्शन 30 X 9 मिमी. असतो. 10 मिमी.पेक्षा मोठे गेज ब्लॉक 35 X 9 मिमी. या क्रॉस सेक्शनचे असतात. त्यांचे मोजमापन करताना त्याच आकाराच्या स्टॅँडर्ड गेज ब्लॉकबरोबर त्यांची तुलना केली जाते. त्यामुळे रेफरन्स ब्लॉकदेखील 30 X 9 मिमी. आणि 35 X 9 मिमी. या पृष्ठीय आकाराचे असतात. एकाचवेळी रेफरन्स ब्लॉक आणि तपासणीचा ब्लॉक हे दोन्ही कंपॅरेटरमध्ये ठेवले जातात आणि ते वर आणि खाली असलेल्या दोन प्रोबने तपासले जातात. त्यामुळे याला 2 प्रोब पद्धती असे म्हटले जाते. हे ब्लॉक दंडगोलाकार पिनांवर ठेवून मोजले जातात.
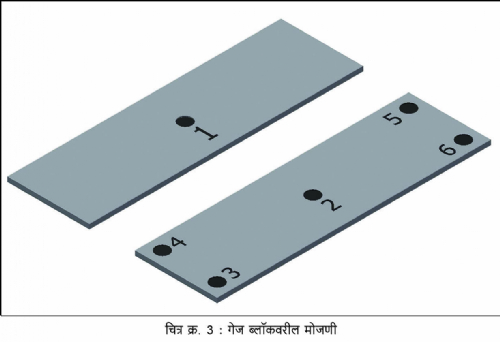
चित्र क्र. 3 मध्ये दर्शविल्याप्रमाणे रेफरन्स ब्लॉकवर मध्यभागी एक आणि प्रत्येक तपासणीच्या ब्लॉकवर मध्यभागी एक आणि चार कोपर्यात चार अशी एकूण पाच ठिकाणी मापे घेतली जातात. परंतु, संदर्भ (रेफरन्सिंग) घेताना 1, 2, 3, 4, 5, 6, 2, 1 या पद्धतीने झालेल्या 8 मापनांचे विश्लेषण केले जाते. सर्वसाधारण पद्धतीमध्ये ही प्रक्रिया प्रत्येक ब्लॉकचे तीन वेळा मापन आणि विश्लेषण करून पूर्ण केली जाते. निकाल देताना या तीन मापनांची सरासरी विचारात घेतली जाते. यातील नंबर 2 चे रीडिंग मध्य लांबीतील फरक (सेंटर लेंग्थ डेव्हिएशन) ठरविण्यासाठी वापरले जाते. 3, 4, 5, 6 रीडिंगवरून ब्लॉकची समांतरता ठरते. रेफरन्स ब्लॉकच्या मापनातील आणि तपासणी होणार्या ब्लॉकच्या मापनातील साधारण आकारातील फरकावरून ब्लॉकची श्रेणी (ग्रेड) ठरते. गेज ब्लॉकच्या आकारातील अचूकपणावर त्याची श्रेणी अवलंबून असते. सर्वोत्कृष्ट अचूकता असणारा ब्लॉक K श्रेणीचा मानला जातो.
काही विशिष्ट परिस्थितीत 3 ऐवजी 10 वेळा मापे घेतली जातात. यावरून आपल्या लक्षात येईल की, 3 मापनांच्या प्रक्रियेमध्ये प्रत्येक ब्लॉकची 8 मापे घेतली जातात आणि त्यांचे विश्लेषण होते. एकूण 24 मापे घेतली जातात. हेच 10 मापनांच्या प्रक्रियेमध्ये प्रत्येक ब्लॉकची 80 मापे आणि विश्लेषण असे प्रमाण होते. बहुसंख्य सेट 122 गेज ब्लॉकचे असल्याने या संपूर्ण मापन प्रक्रियेला अर्थातच खूप वेळ आणि चिकाटीची आवश्यकता असते.
वर उल्लेखलेले गेज ब्लॉक कॅलिब्रेशनचे कार्य प्रामुख्याने दोन पद्धतीने होते. एक म्हणजे लेझर इंटरफेरोमीटर आणि दुसरी कंपॅरेटर प्रणाली. लेझर इंटरफेरोमीटर प्रणालीमध्ये लेझर तंत्र वापरून प्रत्यक्ष मोजमापन केले जाते. परदेशी लेझर इंटरफेरोमीटर प्रणालीमध्ये एका ब्लॉकचे मोजमापन करायला सुमारे तीस हजार रुपये एवढा खर्च येतो. ही प्रणाली भारतात दोन ठिकाणी आहे, परंतु ती खर्चिक असून सहसा सामान्य औद्योगिक वापरासाठी ती सोयीची नाही.
दुसरी पर्यायी पद्धत असलेल्या दोन प्रोब वापरणार्या कंपॅरेटर प्रणालीमध्ये गेले 50 वर्षे इंडक्टिव्ह प्रोब वापरले जात. यामध्ये ‘Voltage Inductance Displacement’ हे तत्त्व वापरले जाते. त्यात 0.01 मायक्रॉनपर्यंत (10 नॅनोमीटर) मापन करता येते. परंतु या पद्धतीमध्ये एक महत्त्वाची बाब म्हणजे, तुलना मर्यादा (कंपॅरिझन रेंज) फक्त 20 मायक्रॉन एवढीच असते. याचा अर्थ जर 122 ब्लॉकचा सेट तपासावयाचा असेल, तर 122 रेफरन्स दर्जाचे ब्लॉक ठेवणे आवश्यक असते. (या रेफरन्स दर्जाच्या ब्लॉकचे कॅलिब्रेशन अतिशय महागडे असते.)
गेल्या काही वर्षांमध्ये हायडेनहाइन या जर्मन कंपनीने पल्स काउंटर अंतर्भूत असलेली ‘इन्क्रिमेंटल एन्कोडर’ सिस्टिम तयार केली. मशिन टूल तपासणीसाठी प्रामुख्याने वापरात येणार्या या पद्धतीमध्ये 10 नॅनोमीटर इतक्या अचूकतेने मापन करता येते.
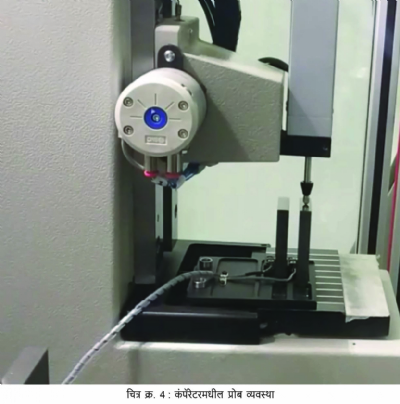
आम्ही निर्माण केलेले कंपॅरेटर भक्कम बांधणीच्या कास्ट आयर्न स्टँडमध्ये बसविलेले असतात. उत्कृष्ट बनावटीच्या स्लाइड आणि इतर भाग वापरून, गेज ब्लॉकचे मोजमापन करण्यासाठी ‘2 प्रोब सिस्टिम’प्रमाणे (चित्र क्र. 4) वरच्या आणि खालच्या बाजूस इन्क्रिमेंटल एन्कोडर प्रोब बसविले आहेत. याचे रिझॉल्युशन 10 नॅनोमीटर असून तुलना मर्यादा मात्र 20 मायक्रॉनऐवजी 20 मिमी. एवढी विशाल होते. या यंत्रणेमुळे संपूर्ण मोजमापन क्षेत्रामध्ये क्रांती झाली. याचे दोन महत्त्वाचे फायदे आहेत. एक म्हणजे तुलनात्मक मर्यादा 20 मिमी. असल्यामुळे 122 गेज ब्लॉकची तपासणी करण्यासाठी वेगळे 122 रेफरन्स ब्लॉक न लागता केवळ 10 ब्लॉकच्या साहाय्याने ही तपासणी पूर्ण करता येते. दुसरी महत्त्वाची गोष्ट म्हणजे त्या मर्यादेमध्ये कोणतेही मापन सहज करता येत असल्यामुळे मेट्रिक अथवा इंपिरीयल (इंचातील) ब्लॉकसाठी वेगवेगळे रेफरन्स ब्लॉक लागत नाहीत. एकाच रेफरन्स सेटवर संपूर्ण तपासणी करता येते. त्यामुळे एकंदर सेटअप आणि तपासणीच्या खर्चामध्ये लक्षणीय बचत होते.
हायडेनहाइन स्केल आणि प्रोबद्वारा दोन मायक्रॉनपेक्षाही सूक्ष्म अंतर अचूकपणे मोजले जाते. संपूर्ण यंत्रणेचे रिझॉल्युशन 1 नॅनोमीटर इतके आहे आणि अनिश्चितता (अन्सर्टिनिटी) 30 नॅनोमीटर इतकी राखली जाते. (काही अतिविशिष्ट कार्यासाठी लेझर प्रोबदेखील वापरता येतात, परंतु ही यंत्रणा जास्त खर्चिक आहे. अत्यंतिक आवश्यकता असेल अशाच ठिकाणी ग्राहक ही यंत्रणा वापरतात.) प्रोबची हालचाल आणि गेज ब्लॉकची हालचाल मोटराइज्ड् कंट्रोलद्वारा नियंत्रित केली जाते. हल्ली ही संपूर्ण यंत्रणा सी.एन.सी. प्रणाली वापरून लवकर पूर्ण करता येते.
गेज ब्लॉकची तपासणी ही एक क्लिष्ट प्रक्रिया आहे. गेज ब्लॉक अत्यंत काळजीपूर्वक हाताळावे लागतात. उचलताना किंवा ठेवताना ते खाली पडता कामा नयेत. त्याच्यावर कुठलेही चरे पडता कामा नयेत.
गेज ब्लॉकची तपासणी करताना तापमान नियंत्रित करावे लागते. आंतरराष्ट्रीय मानांकनानुसार तापमान 20° से.च्या जवळ म्हणजे ±2° से. अथवा ±1° से. मध्ये नियंत्रित करून प्रयोगशाळेमध्ये गेज ब्लॉकची तपासणी केली जाते, अन्यथा तापमानाचा विपरीत परिणाम रिडींगवरती होतो. शक्यतो हा रिडींगवरती होणारा तापमानाचा परिणाम कमी करण्यासाठी आणि अचूक रिडींग मिळण्यासाठी प्रिसिजन तापमान सेन्सर (प्रोब) वापरून रिअल टाइम थर्मल एरर करेक्शन केले जाते. तसेच आपल्या श्वासोच्छवासामुळे, हाताच्या स्पर्शामुळे त्यांचे तापमान बदलू शकते आणि रीडिंग चुकीचे येऊ शकते. यासाठी शक्यतो गेज ब्लॉक हाताळताना लाकडी चिमट्याचा (फोरसेप) वापर केला जातो.
रेफरन्स ब्लॉक आणि तपासणीचा ब्लॉक कंपॅरेटरवर ठेवून पायात असलेला स्विच सुरू केल्यावर प्रोब पुढे येतात आणि रीडिंग घेऊन परत मागे जातात, असे दोन्ही ब्लॉकचे मापन होते. प्रत्येकवेळी मापन करताना मध्यावर एक आणि चारही कोपर्यांची चार अशी एकूण पाच मापे घेतली जातात आणि ही क्रिया तीनवेळा केली जाते. मापन पूर्ण झाल्यावर प्रत्येकवेळी गेज ब्लॉक आपापल्या जागी नीट ठेवणे आवश्यक असते. या संपूर्ण प्रक्रियेमुळे एक गेज ब्लॉक सेट तपासणी करण्यास सुमारे दोन दिवसांचा वेळ जातो. ही संपूर्ण प्रक्रिया करणारा ऑपरेटर प्रशिक्षित तज्ज्ञ असावा लागतो. ही प्रक्रिया किचकट आहे आणि पूर्वी सर्व मापे हाताने लिहिली जात असल्यामुळे चुकांचे प्रमाण जास्त असे. आता मापन, विश्लेषण आणि निकाल हे काम सॉफ्टवेअरमार्फत होत असले तरी मानवी हस्तक्षेपाचा परिणाम होण्याची शक्यता राहतेच.
आपण वर पाहिलेच आहे की, गेज ब्लॉकची हाताळणी हे कौशल्याचे काम आहे. सतत काळजी घेऊन कॅलिब्रेशन करताना ऑपरेटरला कंटाळवाणे वाटू शकते. त्यामुळे त्याचा कामाच्या वेळेवर परिणाम होतो. या विषयातील तज्ज्ञ ऑपरेटर आता दुर्मीळ आहेत. विशेषतः परदेशामध्ये अशा ऑपरेटरचा खर्च हासुद्धा महत्त्वाचा मुद्दा आहे. हे सर्व मुद्दे लक्षात घेता काही कंपन्या या कामाचे स्वयंचलन करण्याच्या प्रयत्नात आहेत. यामुळे सलग 24 तास काम होऊ शकत असल्यामुळे संपूर्ण सेटचा तपासणी अहवाल एका दिवसात मिळू शकतो.
सिंगापूर येथील या क्षेत्रातील नॅशनल मेट्रॉलॉजी सेंटर या सरकारी कंपनीने स्वयंचलनासह कंपॅरेटर पुरविण्यासाठी एक आंतरराष्ट्रीय निविदा (टेंडर) काढली होती. त्यामध्ये 122 ब्लॉकचा सेट प्रत्येकी पाच मापने आणि तीन आवर्तने करून 10 तासांमध्ये पूर्ण तपासणी करण्याचे आव्हान होते. त्यांना संध्याकाळी मशिनला लोड देऊन गेले की सकाळी परिणाम हातात असतील अशी यंत्रणा निर्माण करायची होती. ही व्यवस्था विकसित करण्याचे काम एका वर्षात पूर्ण करावे लागणार होते. आंतरराष्ट्रीय टेसा, मिटुटोयो अशा जगप्रसिद्ध कंपन्यांच्या स्पर्धेमध्ये हे विशेष काम आम्हाला मिळाले.
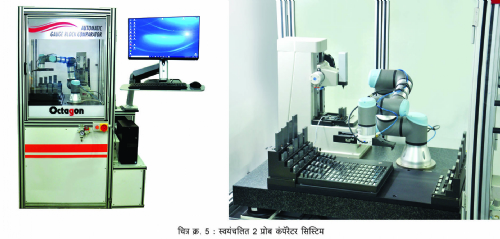
आतापर्यंत कोणीही न केलेले हे विकसन करताना आम्ही बर्याच पर्यायांचा विचार केला. यासाठी औरंगाबादच्या ‘मायक्रोनिक्स’ कंपनीची मोलाची साथ आम्हाला मिळाली. यात सर्वात किचकट आव्हान होते ते म्हणजे 122 गेज ब्लॉकचा सेट एका जागी ठेवल्यावर त्यातील प्रत्येक ब्लॉक उचलून कंपॅरेटरवर योग्य जागी ठेवणे आणि मोजमापन झाल्यावर पुन्हा गेज ब्लॉक बॉक्समध्ये परत त्याच जागी योग्य रीतीने ठेवणे. यासाठी आधी आम्ही गॅँट्री पद्धत वापरण्याचा विचार केला. पण पॅलेट आणि गॅँट्री अचूक वापरणे कठीण होते. एका जर्मन तपासणी यंत्रणेमध्ये युनिव्हर्सल कंपनीचे रोबो वापरलेले आम्ही पाहिले आणि त्यावर अधिक अभ्यास करण्याचे ठरविले. आपल्या बाजारपेठेमध्ये एकसुरी काम करण्यासाठी अनेक रोबोचे पर्याय उपलब्ध आहेत. परंतु, त्यामध्ये एक मोठी अडचण होती ती म्हणजे रोबो पुनरावर्ती काम करतो. मात्र, त्यातील अचूकतेमध्ये फरक पडू शकतो. रोबोला काही पोझिशन कायम करून योग्य काम करता येते. पण 122 जागांवर असलेले ब्लॉक एक एक करून मशिनला पुरविणे आणि काम झाल्यावर परत त्याच जागेवर तसाच, कोणतेही अपघात न होता परत ठेवणे यासाठी 122 प्रोग्रॅम फीड करावे लागले असते. त्यामुळे वारंवारिता आणि अचूकता यातील फरक हा एक मोठा प्रश्न होता. रोबोला काम करण्यासाठी CAD कोऑर्डिनेट देणे आवश्यक असते. यामध्ये आम्हाला खूप प्रयत्न करावे लागले.
अखेर अभ्यासांती चांगला रोबो मिळविला, पण त्यामध्येही अचूकतेच्या अनेक अडचणी होत्या. त्यामुळे आम्ही अनेक नवीन प्रोग्रॅम केले. रोबोचे कॅलिब्रेशन करणे हादेखील मोठा प्रश्न होता. हाताळणीमध्ये (हॅँडलिंग)काही बदल करावे लागले. गेज ब्लॉक तपासण्यास ठेवण्यासाठी आम्ही एक टेम्प्लेट तयार केली. मशिन आणि या फिक्श्चरचे कोऑर्डिनेट स्थिर करून कॅलिब्रेट करावे लागले. चाचण्या घेताना झालेल्या चुकांचे ‘एरर मॅपिंग’ करून ते प्रोग्रॅम आम्ही पुन्हा दुरुस्त केले. आम्ही या प्रोजेक्ट डेव्हलपमेंटमध्ये कोणतीही कसर ठेवली नाही. ऑर्डरमधील 10 रेफरन्स ब्लॉकचे कॅलिब्रेशन चांगले होणे आवश्यक होते, ते स्वित्झर्लंडमधील मेटास प्रयोगशाळेमधून करून घेतले.
आमची सर्व सिस्टिम (चित्र क्र. 5) तयार झाल्यावर प्री डिस्पॅच इन्स्पेक्शन करण्यापूर्वी आम्ही खूप चाचण्या घेतल्या. ग्राहक कंपनीचा प्रतिनिधी भारतात येऊन तपासणी करण्याऐवजी त्या सिस्टिमचा व्हिडिओ आणि अहवाल तयार करून पाठविला. मंजुरी मिळाल्यावर सिंगापूरमध्ये इन्स्टॉलेशन करून पुन्हा चाचण्या झाल्या. 122 गेज ब्लॉकच्या सेटचे संपूर्ण कॅलिब्रेशन रोबोद्वारा आमच्या मशिनवर कोणतेही नुकसान न होता केवळ 8.5 तासांत पूर्ण झाले. आम्हाला सांगण्यास अभिमान वाटतो की, आम्ही अशा प्रकारची सिस्टिम तयार करणारी एकमेव कंपनी आहोत. या संपूर्ण प्रकल्पाच्या यशात ऑक्टॅगॉन पुणे आणि मायक्रोनिक्स औरंगाबाद कंपनीतील R & D विभागासह मोहन काळे, के. व्ही. कुलकर्णी, श्रेयांस बुबने यांचा सहभाग होता.
ही सिस्टिम कशी चालते हे दाखविणारा व्हिडिओ पाहण्यासाठी शेजारी दिलेला QR कोड स्कॅन करावा.
आजवर युरोप किंवा इतर देशातील उत्पादनांची भारतात कॉपी होत असे. परंतु आता इतर देश आमच्या उत्पादनांची कॉपी करतील असे वाटते!
विवेक घोडके
संस्थापक, व्यवस्थापकीय संचालक
ऑक्टॅगॉन प्रिसिजन इंडिया प्रा. लि.
9325084622
ghodke@octagon.co.in
विवेक घोडके यांत्रिकी अभियंते असून ऑक्टॅगॉन प्रिसिजन इंडिया प्रा. लि. कंपनीचे ते संस्थापक, व्यवस्थापकीय संचालक आहेत. औद्योगिक मोजमापन क्षेत्रातील कामाचा त्यांना 30 वर्षांचा अनुभव आहे.