सध्याच्या स्पर्धेच्या आणि तांत्रिक क्रांतीच्या युगात उत्पादन उद्योगाच्या क्षेत्रात प्रचंड बदल होत आहेत. उत्पादांच्या अपेक्षित आयुर्मानाबद्दल अपेक्षा मोठ्या प्रमाणात वाढलेल्या आहेत आणि वाढतच राहणार आहेत. तीव्र स्पर्धेमुळे किंमतसुद्धा मर्यादेतच ठेवावी लागते. उत्पादाच्या घटक भागांचे आयुष्य बऱ्याच अंशी पृष्ठभागाच्या गुणधर्मावर अवलंबून असते. पारंपरिक प्रक्रियांमुळे (टर्निंग, मिलिंग) मिळणाऱ्या पृष्ठभागाच्या मर्यादित गुणवत्तेमुळे अपेक्षित लाभ मिळत नाही. त्यातूनच काही खास पृष्ठभाग मिळविण्याचा प्रयत्न सुरू झाला. या प्रयत्नांची परिणती काही खास गुणधर्म असलेले पृष्ठभाग विकसित करण्यात झाली. हे खास गुणधर्म म्हणजे कठीण (हार्ड), गंजरोधक पृष्ठभाग, झीजरोधक पृष्ठभाग इत्यादी. यातूनच बर्निशिंग प्रक्रियेचा जन्म झाला.प्रथम अमेरिकेत 1930 साली ही प्रक्रिया विकसित झाली. परंतु याचा उपयोग फारच मर्यादित स्वरूपाचा होता. रेल्वेच्या डब्याच्या कण्याचे (अॅक्सल) आयुर्मान वाढविण्यासाठी याचा उपयोग करण्यात येत असे. याचा मोठ्या प्रमाणात उपयोग 1960 साली मुख्यत्वे जपानमधील वाहन उद्योगामध्ये सुरू झाला.
बर्निशिंग ही एक सुपर फिनिशिंग प्रक्रिया आहे. जेव्हा दोन वस्तू एकमेकांवर घासल्या जातात आणि त्या दोन पृष्ठभागांवर बल कार्यरत असते तेव्हा जी वस्तू कमी कठीण असते तिचे विरूपण (डिस्टॉर्शन) होते. विरूपण दोन प्रकारचे असते. एक म्हणजे जे विरूपण पूर्वस्थितीत परत येते त्याला इलॅस्टिक विरूपण असे म्हणतात. उदाहरणार्थ, स्प्रिंगवरचे बल काढून घेतल्यास ती पुन्हा पूर्वस्थितीत परत येते. यालाच आपण स्थितिस्थापकत्व असे म्हणतो.
विरूपणाचा दुसरा प्रकार म्हणजे, जे विरूपण पूर्वस्थितीत परत येत नाही, कायमस्वरूपी आकार बदलतो. याला आपण प्लॅस्टिक विरूपण म्हणतो. प्लॅस्टिक विरूपण कसे केले जाते ते आपण पाहू.
बर्निशिंग ही प्रक्रिया कार्यवस्तू सामान्य तापमानात असताना करावयाची प्रक्रिया आहे. चित्र क्र. 1 मध्ये बर्निशिंग कसे करतात याचे मूलतत्व दिलेले आहे. कार्यवस्तूवर बॉलच्यामार्फत बल कार्यरत आहे. जेव्हा हे बल यील्ड स्ट्रेसपेक्षा जास्त असते तेव्हा कार्यवस्तूच्या विरूपण झालेल्या मटेरियलचा पातळ थर पृष्ठभागावर तयार होतो. प्लॅस्टिक विरूपणामुळे हा कठीण थर तयार होतो. यालाच सरफेस प्लॅस्टिक डीफॉर्मेशन (SPD) असे म्हणतात. साधारणपणे पृष्ठभागावर असलेल्या पातळ थराची कठीणता 10 HRC ने वाढलेली असते. यामुळे कार्यवस्तूची झीजरोधकता वाढते.
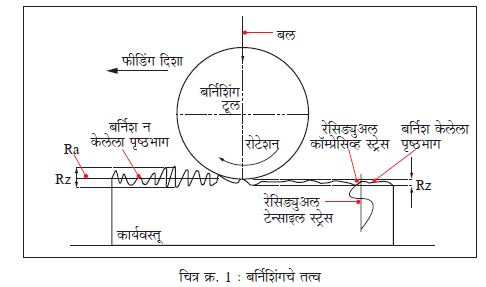
चित्र क्र. 2 मध्ये आपल्याला असे दिसते की, जो पृष्ठभाग आधीच्या प्रक्रियेमुळे तयार झाला आहे त्या पृष्ठभागावर असलेल्या वरच्या टोकांची (क्रेस्ट) उंची बलामुळे कमी झालेली आहे आणि हे मटेरियल खाली असलेल्या खड्ड्यांमध्ये दाबले गेले आहे. त्यामुळे वरती असलेली टोके आणि खड्ड्यांत असलेले बिंदू यातील अंतर कमी झाल्याने पृष्ठभागाचा खडबडीतपणा कमी होतो, म्हणजेच पृष्ठभाग जास्त गुळगुळीत होतो. त्यामुळे दोन पृष्ठभागांच्या एकमेकांच्या संपर्कात असलेल्या पृष्ठभागाचे क्षेत्रफळ वाढल्यामुळे त्या पृष्ठभागाचे आयुर्मान वाढते. बर्निशिंग प्रक्रियेत मटेरियल अजिबात काढले जात नाही पण पृष्ठभागाचे गुणधर्म मात्र बदलतात आणि पृष्ठभागाची उच्च गुणवत्ता प्राप्त होते.
बर्निशिंग प्रक्रियेचे वर्गीकरण बऱ्याचप्रकारे केले जाते. ते कुठल्या प्रकारचे टूल वापरले आहे, पृष्ठभागाचा भूमितीय आकार कसा आहे, यावर अवलंबून असते. टूलचा भूमितीय आकार कसा आहे यावर अवलंबून असलेले प्रकार पुढीलप्रमाणे आहेत.
1. बॉल बर्निशिंग
2. रोलर बर्निशिंग
1. बॉल बर्निशिंग
या प्रकारच्या बर्निशिंगमध्ये एक किंवा अनेक कठीण बॉल एका शँकमध्ये बसविलेले असतात. या शँकवर दाबयुक्त ऑइल कार्य करीत असते. हा दाब बॉलवर सतत कार्यरत असतो, म्हणजेच हे बॉल प्रक्रिया चालू असताना कार्यवस्तूवर सतत दाब देत देत स्वत:भोवती फिरत असतात. यामुळेच पृष्ठभागावर बर्निशिंग होते. बॉलचा कार्यवस्तूवर पडणारा दाब, ऑइलचा दाब कमी जास्त करून नियंत्रित करता येतो. ऑइलऐवजी स्प्रिंगचासुद्धा वापर करता येतो.
2. रोलर बर्निशिंगरोलर बर्निशिंगमध्ये नावाप्रमाणेच बॉलच्याऐवजी रोलरचा वापर केला जातो. चित्र क्र. 6 आणि 7 मध्ये या शँकवर एकच रोलर वापरला आहे. अनेक रोलरचासुद्धा वापर केला जातो. अशा प्रकारची टूल, मिलिंग/ड्रिलिंग मशीन किंवा अगदी लेथवरसुद्धा वापरली जातात.
जेव्हा एखाद्या भोकामध्ये बर्निशिंग करावयाचे असते तेव्हा अनेक रोलरचा वापर केला जातो. हे रोलर शँकबरोबर गोल फिरत असतात आणि त्याचप्रमाणे ते स्वतःभोवतीसुद्धा फिरत असतात, जशी पृथ्वी सूर्याभोवती फिरता फिरता ती स्वतःभोवतीसुद्धा फिरते. यालाच आपण प्लॅनेटरी मोशन असे म्हणतो. जिथे एकच रोलर वापरला जातो, त्याला 'युनिव्हर्सल बर्निशिंग टूल' (चित्र क्र. 7) असे म्हणतात. हे टूल सपाट पृष्ठभाग, तिरपा पृष्ठभाग तसेच दंडगोलाकार पृष्ठभाग यावर बर्निशिंग करण्यासाठी वापरले जाते.
बर्निशिंग टूलचे वर्गीकरण कुठल्या प्रकारच्या पृष्ठभागावर यंत्रण केले जाते त्यानुसारही केले जाते.
चित्र क्र. 8 मध्ये भोकाच्या अंतर्भागावर बर्निशिंग केले जात आहे.
चित्र क्र. 9 मध्ये तिरप्या (टेपर) पृष्ठभागावर बर्निशिंग केले जात आहे.
चित्र क्र. 10 मध्ये सपाट पृष्ठभागावर बर्निशिंग केले जात आहे, तर चित्र क्र. 11 मध्ये विशिष्ट आकार असलेल्या पृष्ठभागावर बर्निशिंग केले जात आहे.
कुठल्याही यंत्रण प्रक्रियेच्या बाबतीत काही मापदंड असतात की ज्यावर त्या यंत्रणाचा परिणाम अवलंबून असतो. बर्निशिंग करताना पुढील काही महत्त्वाच्या मापदंडांबद्दल आपण माहिती घेऊ.
1. बर्निशिंग बलबर्निशिंग टूल कार्यवस्तूवर ज्या बलाने दाबले जाते त्याला बर्निशिंग बल असे म्हणतात. या बलावरच बर्निशिंग टूल कार्यवस्तूमध्ये किती घुसते (पेनिट्रेशन) ते ठरते. हा अतिशय महत्त्वाचा मापदंड आहे. या बलावरच कार्यवस्तूच्या वरील पृष्ठभागाचे प्लॅस्टिक स्वरुपात विरूपण होणे अवलंबून आहे. पृष्ठभागाचा मिळणारा फिनिश या बलावरच अवलंबून असतो. हे बल किती ठेवावे हे कार्यवस्तूच्या धातूच्या यील्ड स्ट्रेंग्थवर अवलंबून असते.
2. गती (स्पीड)या ठिकाणी कार्यवस्तूची फिरण्याची गती अभिप्रेत आहे. सपाट पृष्ठभागावर बर्निशिंग करताना जर कार्यवस्तू स्थिर असेल तर बर्निशिंग टूल फिरत असते. या टूलच्या फिरण्याची गती म्हणजेच टूलची गती होय. ही गती फेरे प्रति मिनिटमध्ये (RPM) मोजतात. ही गती कार्यवस्तूच्या आकारावर आणि मजबूतीवर अवलंबून असते.
3. सरकवेग (फीड)टूलच्या एका फेऱ्यामध्ये टूल ज्या गतीने पुढे सरकते त्याला सरकवेग असे म्हणतात. हा सरकवेग आपल्याला कुठल्या प्रतीचा पृष्ठीय फिनिश पाहिजे त्यावर अवलंबून असतो. सरकवेग जेवढा कमी तेवढा पृष्ठीय फिनिश चांगला मिळतो.
4. एकाच पृष्ठभागावर पुन्हा पुन्हा बर्निशिंग करणेएकाच पृष्ठभागावर किती वेळा बर्निशिंग करावयाचे हे ठरवावे लागते. यासाठी कुठल्या धातूवर आपण बर्निशिंग करणार आहोत हे विचारात घ्यावे लागते. पृष्ठभागाचा फिनिश चांगल्या प्रतीचा मिळविण्यासाठी जास्त वेळा बर्निशिंग करावे लागते. जास्त लवचिक धातू असेल तर बर्निशिंग चांगले होते.
5. टूलचा व्यास आणि धातूबर्निशिंग टूलमध्ये बसविलेल्या बॉल किंवा रोलर याचा आकार आणि धातू यावर बर्निशिंगची गुणवत्ता अवलंबून असते. बर्निशिंग टूलचा कठीणपणा कार्यवस्तूपेक्षा जास्त असतो.
6. वंगण (लुब्रिकेशन)बर्निशिंग करताना कार्यवस्तूचे यंत्रण होत नसल्यामुळे कमी प्रमाणात उष्णता निर्मिती होते. त्यामुळे वंगणावर बर्निशिंगची गुणवत्ता फारशी अवलंबून नसते. त्यामुळे काही वेळेस वंगण न वापरतासुद्धा बर्निशिंग केले जाते. थोडेसे पातळ वंगणसुद्धा आपण वापरू शकतो. बेअरिंग, रोलर हे सहजपणे फिरावेत यासाठीच प्रामुख्याने वंगणाचा उपयोग होतो.
आजकाल बर्निशिंग या प्रक्रियेला जास्त महत्त्व मिळत आहे. यासाठी फक्त बर्निशिंगनंतर मिळणारी पृष्ठभागाची उच्च गुणवत्ता एवढेच कारण नसून, त्या कार्यवस्तूच्या तांत्रिक दृष्टीने उपयुक्त असलेल्या गुणधर्मात होणारी सुधारणा महत्त्वाची ठरते. बर्निशिंग केल्यामुळे पृष्ठभागावर आणि त्याच्या गुणधर्मांवर काय परिणाम होतो त्याची माहिती घेऊ.
1. पृष्ठभागाचा फिनिशबर्निशिंग ही एक सुपर फिनिशिंग करण्याची प्रक्रिया आहे, ज्यामुळे पृष्ठभागाची उच्च गुणवत्ता मिळते. पृष्ठभागाच्या उंचसखलपणात सुधारणा होते. म्हणजेच पृष्ठभागाचा खडबडीतपणा कमी होऊन तो जास्त गुळगुळीत होतो.
2. पृष्ठभागाचा कठीणपणाबर्निशिंग करताना कार्यरत असलेल्या बलामुळे कार्यवस्तूच्या पृष्ठभागावर असलेला थर प्लॅस्टिकदृष्ट्या प्रवाहित होतो. यामुळे कार्यवस्तूचे तापमान न वाढतासुद्धा कार्यवस्तूच्या पृष्ठभागाचे काठीण्य वाढते. त्यामुळे वेगळे केस हार्डनिंग करण्याची गरज रहात नाही. यालाच कोल्ड वर्किंग असे म्हणतात.
3. कॉम्प्रेसिव्ह स्ट्रेसबर्निशिंग करताना येणाऱ्या प्रचंड दाबामुळे कार्यवस्तूच्या पृष्ठभागामध्ये कॉम्प्रेसिव्ह स्ट्रेस निर्माण होतो. कॉम्प्रेसिव्ह स्ट्रेसमुळे कार्यवस्तूचे 'फटीगमुळे' कमी होणारे आयुष्य सुधारते. तडे (क्रॅक) निर्माण होण्याची शक्यता कमी होते. त्यामुळे पृष्ठभागावर कॉम्प्रेसिव्ह स्ट्रेस असणे नेहमीच हितावह ठरते. कॉम्प्रेसिव्ह स्ट्रेस सर्वसाधारण क्रिया करताना टिकून राहतो, परंतु जर कार्यवस्तूचे तापमान वाढले तर मात्र कॉम्प्रेसिव्ह स्ट्रेस नाहीसा होण्याची शक्यता असते. त्यामुळे बर्निशिंग केलेल्या वस्तूचे तापमान नियंत्रित ठेवल्यास वस्तूचे आयुर्मान वाढते.
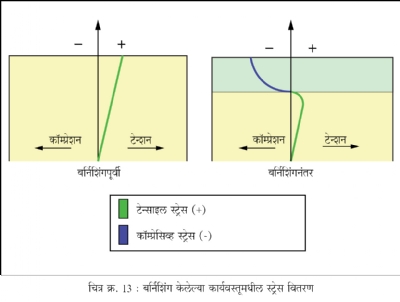
पारंपरिक पद्धतीच्या यंत्रणात म्हणजेच टर्निंग, मिलिंग, ड्रिलिंग इत्यादी प्रकारात टेन्साइल स्ट्रेस निर्माण होतो, ज्यामुळे वस्तूचे आयुर्मान कमी होते आणि तांत्रिक गुणधर्मदेखील कनिष्ठ दर्जाचे असतात. जेव्हा अशा कार्यवस्तू बर्निश केल्या जातात तेव्हा टेन्साइल स्ट्रेसची जागा कॉम्प्रेसिव्ह स्ट्रेस घेतो आणि त्यामुळे वस्तूच्या तांत्रिक गुणधर्म सुधारतात. चित्र क्र. 13 मध्ये कार्यवस्तूच्या पृष्ठभागावर बर्निशिंग करण्याच्या आधी आणि नंतर असणाऱ्या स्ट्रेसचे दृश्य दाखविले आहे.
4. धातूच्या कणांची संरचनाजेव्हा एखादी प्रक्रिया वातावरणीय तापमानात केली जाते तेव्हा अशा प्रक्रियेला कोल्ड वर्किंग प्रोसेस असे म्हणतात. बर्निशिंग ही अशीच एक कोल्ड वर्किंग प्रोसेस आहे. बर्निशिंग करताना येणाऱ्या प्रचंड दाबामुळे धातूचे सूक्ष्म कण आकाराने अधिक सूक्ष्म होतात (चित्र क्र. 14) आणि त्यामुळे या कणांचे गुणधर्मही बदलतात.
हे सर्व कण एका ठराविक दिशेने संरेखित (अलाईन) केले जातात. यामुळे धातूच्या पृष्ठभागाची ताकद, काठीण्य वाढते.
5. गंजरोधकतागंजणे म्हणजे काय हे आपल्याला माहिती आहेच. धातूच्या वस्तू वातावरणातील ऑक्सिजनमुळे गंजतात. वस्तू गंजल्यामुळे तिचे आयुर्मान कमी होते तसेच ती अचानक निकामी होते, ज्यामुळे मोठे नुकसान होऊ शकते. बर्निशिंग केल्याने गंजरोधकता वाढणे हासुद्धा फायदा मिळतो.
6. झीज रोधकताघर्षण आणि झीज या एकाच नाण्याच्या दोन बाजू आहेत. जिथे दोन वस्तूंमध्ये घर्षण आहे तिथे झीज होतेच आणि ज्या पृष्ठभागांमध्ये घर्षण आहे तिथे ते पृष्ठभाग कठीण असणे क्रमप्राप्त आहे.
7. फटीग लाइफचक्रीय बल किंवा पुनरावर्ती बल कार्यरत असल्यास कार्यवस्तू काही काळाने थकते. या थकव्यालाच आपण फटीग असे म्हणतो. फटीगमुळे कार्यवस्तूचे आयुर्मान कमी होते. उदाहरणार्थ, कनेक्टिंग रॉड सारखा वर/खाली, मागे/पुढे होत असल्याने सतत पुनरावर्ती बल कार्यरत असते. यामुळेच फटीग निर्माण होतो. बर्निशिंग प्रक्रियेने जो कॉम्प्रेसिव्ह स्ट्रेस निर्माण होतो त्यामुळे कार्यवस्तूचे फटीग लाइफ सुधारते.
8. विद्युत वाहकताप्रत्येक धातूच्या विद्युत वाहकतेचा गुणधर्म वेगवेगळा असतो. तांबे, अॅल्युमिनिअम या धातूंची विद्युत वाहकता फारच चांगली असते. त्याचप्रमाणे हा गुणधर्म काही विशिष्ट बाबींवरसुद्धा अवलंबून असतो. उदाहरणार्थ तापमान, अशुद्धता किंवा सच्छिद्रता यावरसुद्धा विद्युत वहनाची क्षमता अवलंबून असते. जर आपण धातूची सच्छिद्रता कमी केली तर विद्युत वहन सुधारते. बर्निशिंगमध्ये जे बल कार्य करते त्यामुळे वस्तूच्या पृष्ठभागावर असणाऱ्या थराची सच्छिद्रता कमी झाल्यामुळे विद्युत वाहकता सुधारते. पण जर वस्तू आकाराने मोठी असेल तर मात्र गाभ्याची सच्छिद्रता बदलत नसल्यामुळे विद्युत वाहकता सुधारत नाही.
कुठलेही यंत्रण करावयाचे झाले तर त्याचे काही फायदे आणि मर्यादा असतातच. वर उल्लेख केलेल्या मुद्यांवरून बर्निशिंग प्रक्रियेचे महत्त्व आपल्या लक्षात आलेच असेल. या प्रक्रियेमुळे मिळणाऱ्या फायद्यांविषयी आपण माहिती घेऊ.
⦁ पृष्ठभागाचा गुळगुळीतपणा खूपच उच्च दर्जाचा मिळतो, जो 0.05 ते 0.2 µm Ra या मर्यादेत मिळू शकतो. आरशाप्रमाणे चकचकीत पृष्ठभाग मिळतो.
⦁ बर्निशिंग प्रक्रिया लेथ, मिलिंग मशीन तसेच ड्रिलिंग मशीनवर करता येत असल्यामुळे ज्या कर्मचाऱ्याला ही मशीन चालविता येतात तो बर्निशिंग करू शकतो. आधीचे टूल काढून टाकून बर्निशिंग टूल वापरता येते. त्यामुळे त्याच सेटअपमध्ये बर्निशिंग करता येत असल्याने वेळेची बचत होते.
⦁ बर्निशिंग टूलमध्ये बॉल, रोलर असे झिजणारे भाग सहजपणे बदलता येत असल्याने देखभाल त्वरित करता येते आणि देखभालीचा खर्चही मर्यादित होतो.
बर्निशिंग करताना येणाऱ्या मर्यादा
⦁ बर्निशिंग टूलची किंमत जास्त असते.
⦁ छोट्या वस्तूंना बर्निशिंग करता येत नाही.
⦁ बर्निशिंग करताना येणाऱ्या प्रचंड बलामुळे नाजूक तसेच तकलादू वस्तूंचे बर्निशिंग करता येत नाही.
⦁ गुंतागुंतीच्या वस्तूंना आणि आकारांना बर्निशिंग करण्यासाठी खास टूल बनवावी लागतात. तसेच जास्त कौशल्य आणि अनुभवाची गरज असते. एखादा आकार बदलल्यास नवीन टूल बनवावे लागते.
बर्निशिंगचा उपयोग बऱ्याच ठिकाणी होतो. वाहन उद्योग, विमानात लागणारे भाग, वस्त्रोद्योग, हायड्रॉलिक भाग, रेल्वेसाठी लागणारे भाग अशा अनेक क्षेत्रात बर्निशिंग प्रक्रियेचा वापर केला जातो.
चित्र क्र 15 मध्ये दर्शविलेल्या आणि अशा प्रकारच्या बऱ्याच भागांसाठी बर्निशिंग या प्रक्रियेचा वापर केला जातो.
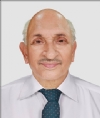
अजित देशपांडे
अतिथी प्राध्यापक,
ARAI, SAE
9011018388
ajitdeshpande21@gmail.com
अजित देशपांडे यांना जिग्ज आणि फिक्श्चर्स बनविण्याचा जवळपास 36 वर्षांचा अनुभव आहे. त्यांनी किर्लोस्कर, ग्रीव्हज् लोम्बार्डिनी लि., टाटा मोटर्स अशा विविध कंपन्यांत काम केले आहे. अभियांत्रिकी महाविद्यालयांमध्ये ते अतिथी प्राध्यापक आहेत.