GD&T मापन टॉलरन्स संदर्भातील सविस्तर माहिती देणाऱ्या लेखमालेतील हा शेवटचा लेख. लोकेशन टॉलरन्स कोणत्याही संदर्भाच्या संबंधात वैशिष्ट्याचे अपेक्षित स्थान (ट्रू पोझिशन) निर्धारित करतो. लोकेशन नियंत्रण आणि रनआउट टॉलरन्स कसे तपासावे याबाबत या लेखात सखोल माहिती दिली आहे.
GD&T चा पुढचा प्रकार म्हणजे लोकेशन (स्थान) टॉलरन्स याविषयी आपण या लेखात जाणून घेणार आहोत.
लोकेशन टॉलरन्स : लोकेशन टॉलरन्स कोणत्याही संदर्भाच्या संबंधात वैशिष्ट्याचे अपेक्षित स्थान (ट्रू पोझिशन) निर्धारित करतो. लोकेशन टॉलरन्स दर्शविण्यासाठी संदर्भ (डेटम) नेहमीच आवश्यक असतो आणि संदर्भाशी संबंधित वैशिष्ट्यासाठी असलेला, हा एक भौमितिक टॉलरन्स आहे.
हे नेहमी वापरले जाणारे GD&T टॅग आहेत. ते समजण्यास तुलनेने सोपे असतात आणि त्याने वैशिष्ट्याचे स्थान (फीचर लोकेशन) नियंत्रित केले जात असल्यामुळे, कोणताही बदल करण्यासाठी ते अतिशय उपयुक्त असतात. लोकेशन टॉलरन्सच्या सामान्य उदाहरणांमध्ये प्रोफाइल आणि स्थिती टॉलरन्स टॅग यांचा समावेश असून लोकेशन नियंत्रण पुढील तीन प्रकारांमध्ये वर्गीकृत केले गेले आहे.
अ. पोझिशन टॉलरन्स
ब. समकेंद्रियता (कॉन्सेन्ट्रिसिटी)
क. सममिती (सिमेट्री)
अ. पोझिशन टॉलरन्स
एखाद्या वैशिष्ट्याचे त्याच्या अपेक्षित स्थानापासून असणारे एकंदर अनुमत विचलन (अलाउड डेव्हिएशन) अशी पोझिशन टॉलरन्सची व्याख्या केली जाते. अपेक्षित (ट्रू) पोझिशन म्हणजे तंतोतंत सहनिर्देशक किंवा मूळ परिमाणे अथवा नॉमिनल मूल्य दर्शविणारी अन्य साधने यांच्याद्वारे परिभाषित केलेले स्थान. दुसऱ्या शब्दांत, पोझिशन टॉलरन्स म्हणजे आपल्या वैशिष्ट्याचे स्थान त्याच्या अपेक्षित स्थानापासून किती भिन्न असू शकते त्याचे माप. पोझिशन टॉलरन्स सामान्यत: छिद्र किंवा स्लॉट यासारख्या अॅसेम्ब्लीसाठी महत्त्वाच्या वैशिष्ट्यावर लागू होते.
पोझिशन टॉलरन्सचा अर्थ कसा लावायचा?
चित्र क्र. 1 मध्ये Ø10.0 ± 0.1 मिमी. च्या चार छिद्रांचे स्थान संदर्भ A, B आणि C च्या संदर्भात 0.2 मिमी. च्या आत असले पाहिजे. सतत संपर्क रहावा आणि चारही छिद्रे विशिष्ट पोझिशनच्या आत रहावीत, हे सुनिश्चित करण्यासाठी त्यांना एका ब्लॉकवर लोकेट केलेले आहे. त्याच्याशी जोडल्या जाणाऱ्या (मेटिंग) यंत्रभागामधील आटे असलेल्या कनेक्टरला ही छिद्रे जुळणे आवश्यक आहे.
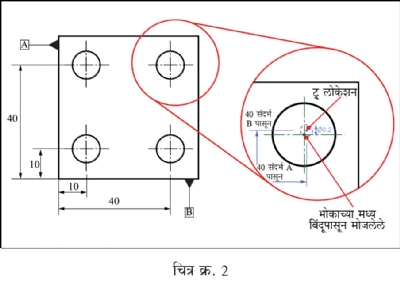
अपेक्षित स्थान निश्चित केल्यावर, छिद्रे चित्र क्र. 2 मध्ये दाखविल्याप्रमाणे तंतोतंत त्याच स्थानावर असण्याची गरज नसते, परंतु त्यांची केंद्रे टॉलरन्सद्वारे निर्दिष्ट (स्पेसिफाइड) केलेल्या प्रमाणात म्हणजेच 0.2 मिमी. च्या आत कोठेही असू शकतात. मूलभूत परिमाणे (चौरसातील परिमाणे) विना टॉलरन्स आहेत आणि छिद्र परिपूर्ण असल्यास त्यांच्याद्वारे अपेक्षित स्थान समजते. वरच्या बाजूच्या उजवीकडच्या छिद्राच्या 2D तपासणीत, अपेक्षित स्थान संदर्भ A पासून 40 मिमी. आणि संदर्भ B पासून 40 मिमी. असेल. छिद्रांचे केंद्र सामान्यत: CMM द्वारे मोजले जाते आणि अपेक्षित स्थानाबरोबर त्याची तुलना केली जाते. जोपर्यंत छिद्रांचे केंद्र फीचर नियंत्रण फ्रेमद्वारे निर्दिष्ट केलेल्या 0.2 मिमी.च्या टॉलरन्स झोनमध्ये आहे, तोपर्यंत यंत्रभाग टॉलरन्समध्ये आहे.
पृष्ठभागाचा पोझिशन टॉलरन्स कसा तपासावयाचा?
गेज वापरणे
मापन गेज किंवा तपासणी गेज (चित्र क्र. 3) वापरून पास/फेल निर्णय केला जातो. यात ऑपरेटरच्या कौशल्याच्या पातळीनुसार होणारा, कामाची गती आणि तपासणीची गुणवत्ता यांच्यातील फरक अजिबात नसतो, हा एक फायदा आहे. तसेच यातील सोपेपणामुळे स्वयंचलन साधता येते.
पोझिशनल गेज वापरण्याचे तोटे
प्रत्येक यंत्रभागासाठी गेज तयार करावे लागते. आवश्यकतेनुसार बनविलेल्या गेजची किंमत जास्त असते, ज्यामुळे प्रोटोटाइप बनविण्याच्या टप्प्यात त्यांचा समावेश करणे कठीण होते.
सहनिर्देशक मापन मशीन (CMM) वापरणे
संदर्भ प्लेन सेट करावी आणि यंत्रभागावरील मापन बिंदूवर स्टायलस (चित्र क्र. 4) ठेवावा. मापन परिणाम त्वरित स्क्रीनवर दिसून येतो. कार्टेशियन सहनिर्देशांकदेखील मोजले जाऊ शकतात आणि एका मापनात संयुक्त अपेक्षित स्थान मिळू शकते. बोअर मोजण्यासाठी, वेगवेगळ्या खोलीवर मापन करावे आणि दंडगोलाकारिता, लंबत्व आणि सरळपणा यांची पडताळणी करावी.
ब. समकेंद्रियता (कॉन्सेन्ट्रिसिटी)
समकेंद्रियता हा स्थान नियंत्रणातला दुसरा प्रकार आहे. समकेंद्रियतेमध्ये अशा स्थितीचे वर्णन केले जाते, ज्यात कोणत्याही संयोजनातील दोन किंवा अधिक वैशिष्ट्ये एकाच अक्षात असतात. संदर्भित वैशिष्ट्याच्या केंद्रिय अक्षाला संदर्भ अक्षाबरोबर नियंत्रणात ठेवणारा समकेंद्रियता/समअक्षीयता हा एक टॉलरन्स आहे. समकेंद्रियतेचे मापन करताना, आपण दोन दंडगोलांच्या अक्षांची समअक्षीयता किती अचूक आहे, ते त्यांचे केंद्रबिंदू जुळतात की नाही त्यावरून तपासतो. समकेंद्रियता वर्तुळाकार वैशिष्ट्यावर लागू केली जाते. ट्रान्स्मिशन गिअरमध्ये कंपने आणि झीज टाळण्यासाठी नेहमीच समअक्षीयता असणे आवश्यक आहे. सर्व अक्ष योग्यपणे एका रेषेत असण्याची खात्री करण्यासाठी समकेंद्रियतेची आवश्यकता असू शकते.
समकेंद्रियतेचा अर्थ कसा लावायचा?
चित्र क्र. 5 मध्ये संदर्भ A च्या संदर्भात व्यासाच्या Ø20 ± 0.05 मिमी.ची समकेंद्रियता 0.03 मिमी.मध्ये आहे. याचा अर्थ समकेंद्रियतेचा टॉलरन्स 0.03 मिमी आहे.
हे ही वाचा : GD & T ची मुलभूत माहिती
समकेंद्रियता कशी तपासावयाची?
डायल गेज वापरून
यंत्रभागास एका जागी पकडून आणि ज्या अक्षासाठी टॉलरन्स दिला आहे, त्याच्या परिघाच्या शीर्षस्थानावर डायल गेज (चित्र क्र. 6) ठेवावा. यंत्रभाग फिरवून आणि डायल गेजचा वापर करून कमाल आणि किमान रनआउट मूल्ये मोजावीत. निर्दिष्ट परिघाच्या सभोवतालचे मापन करावे. निर्दिष्ट अक्षांवर पुन्हा मापन करावे. कमाल-किमान यांच्यातील सर्वाधिक फरक समकेंद्रियता म्हणून वापरला जातो. जर आपण संदर्भ A च्या संदर्भात Ø20 ची समकेंद्रियता तपासत असाल तर, Ø20 ला 'V' ब्लॉकवर ठेवणे आवश्यक आहे.
डायल गेज वापरण्याचे तोटे
डायल गेजचा यंत्रभागावरील कोन आणि दबाव यासारखे घटक मापन मूल्यावर परिणाम करतात, म्हणजेच ऑपरेटरनुसार मापन बदलू शकते. डायल गेजचे अग्र (टिप) आणि यंत्रभागाचा पृष्ठभाग यांच्यातील घर्षणामुळे ओरखडा पडू शकतो. यामुळे तो यंत्रभाग अस्वीकृतही होऊ शकतो.
सहनिर्देशक मापन मशीन (CMM) वापरणे
प्रथम संदर्भाच्या मापन बिंदूवर स्टायलस (चित्र क्र. 7) ठेवून आणि नंतर समअक्षीयता मोजण्यासाठी यंत्रभागाच्या (दंडगोल) मापन बिंदूवर स्टायलस ठेवावा. मापन मूल्य मापनयंत्रात नोंद (रेकॉर्ड) केले जाते. पृष्ठभागावर स्टायलस ठेवण्याच्या दोन पद्धती आहेत. बिंदू मापन, ज्यात प्रत्येक मापनासाठी स्टायलस पृष्ठभागावर ठेवून मापन केले जाते आणि ऑटो ट्रिगर (स्कॅनिंग) मापन, ज्यात पृष्ठभागाशी संपर्क टिकवून ठेवत स्टायलस हलवून बिंदूंचे अखंड मापन केले जाते. यात स्टायलसच्या संपर्कात येणे अवघड असणाऱ्या दंडगोलाच्या परीघावर स्टायलस फिरवून मापन करता येते.
क. सममिती (सिमेट्री)
सममिती हा एक त्रिमितीय (3D) टॉलरन्स आहे, जो एका संदर्भ प्रतलामध्ये दोन वैशिष्ट्ये एकसारखी असल्याचे सुनिश्चित करण्यासाठी वापरला जातो. हे एक क्लिष्ट नियंत्रण आहे, जे सामान्यत: CMM वापरून मोजले जाते. सममिती मोजताना आपण यंत्रभाग संदर्भाच्या (रेफरन्स प्लेन) संदर्भात किती अचूकपणे सममितीय आहेत हे तपासत असतो. सममिती वर्तुळाकार तसेच वर्तुळाकार नसलेल्या वैशिष्ट्यावरदेखील लागू केली जाते. अॅसेम्ब्लीमध्ये सममिती वापरली जाते. यात सेट स्क्रू, चावी गाळे (की स्लॉट), वेल्ड किंवा अॅसेम्ब्लीनंतर ज्यांचे संतुलन (बॅलन्सिंग) करावे लागते, अशा अन्य संलग्न गोष्टींचा समावेश असतो.
सममितीचा अर्थ कसा लावायचा?
चित्र क्र. 8 मध्ये 18 ± 0.08 मिमी. रुंदी असलेल्या खाचेची सममिती संदर्भ A च्या संदर्भात 0.05 मिमी.च्या आत असली पाहिजे. b हे सैद्धांतिक केंद्रीय प्रतल आहे आणि a हे 0.05 मिमी.चा टॉलरन्स बँड आहे. खाचेची रूंदी केंद्रीय अक्षापासून 0.05 मिमी.च्या टॉलरन्समध्ये सममितीय असली पाहिजे.
सममिती कशी तपासावयाची?
सममिती तपासण्यासाठी अॅनालॉग कॅलिपर किंवा मायक्रोमीटर (चित्र क्र. 9) वापरून यंत्रभागाचे मापन करावे.
हे वापरण्यास सोपे आणि शीघ्र असल्यामुळे एकाच जागेवर पुन्हा पुन्हा मापन करण्यासाठी उपयुक्त आहे. कॅलिपर आणि मायक्रोमीटर दोन्ही विविध प्रकारांत उपलब्ध असतात. लोकेशन आणि मोजण्याच्या फॉर्मनुसार (आकार) त्यांची निवड केली जाते.
मॅन्युअल पद्धत वापरण्याचे तोटे
मोजल्या गेलेल्या मूल्यांची अचूकता आणि मापनाची गती हे वैयक्तिक उपकरणाच्या मापन त्रुटीव्यतिरिक्त ऑपरेटरच्या कौशल्याच्या पातळीवरही अवलंबून असते. हे वापरून आकार मोजला जाऊ शकत नाही, कारण ही उपकरणे दोन बिंदूंमधील लांबी मोजतात. त्याशिवाय, मापन मूल्यांची माहिती हाताने लिहून नोंद करावी लागते.
सहनिर्देशक मापन मशीन (CMM) वापरणे
संदर्भ घटक (प्रतल) आणि यंत्रभाग (प्रतल) यांच्या सेटअपमधील विचलन प्रत्येक मापन बिंदूवर स्टायलस (चित्र क्र. 10) ठेवून कोणीही शीघ्रपणे आणि अचूकपणे मोजू शकतो. मापन मूल्ये मापन यंत्रात नोंदविली जातात.
थोडक्यात सांगायचे तर, आतापर्यंत आपण GD&T विषयीच्या मूलभूत गोष्टी, टॉलरन्स, संदर्भ, फिट्स आणि त्यांचे प्रकार आणि फॉर्म नियंत्रण, ओरिएंटेशन, प्रोफाइल नियंत्रण आणि लोकेशन नियंत्रण या प्रकारांबद्दल शिकलो आहोत. आपण GD&T च्या रनआउट नियंत्रण या शेवटच्या प्रकाराच्या अभ्यास करू.
5. रनआउट नियंत्रण
रनआउट म्हणजे यंत्रभाग संदर्भ अक्षाभोवती 360° मध्ये फिरविल्यावर, दिलेल्या संदर्भ वैशिष्ट्य किंवा वैशिष्ट्यामध्ये दुसऱ्या डेटमच्या संदर्भात किती विचलन होते, त्याचे मूल्य. ड्रिल, गिअर, शाफ्ट, अॅक्सल यासारख्या मशीन टूलमधील फिरणाऱ्या यंत्रभागांचे वैशिष्ट्य नियंत्रित करण्यासाठी रनआउट टॉलरन्स वापरला जातो. रनआउट दर्शविण्यासाठी संदर्भ नेहमीच आवश्यक असतो.
प्रिसिजन अॅसेम्ब्लीमध्ये रनआउटमुळे चुकीचे संरेखन (अलाइनमेंट) होते आणि/अथवा संतुलनाच्या समस्या उद्भवतात. जो मोटर शाफ्ट, बेअरिंग जर्नल्सच्या तुलनेत आउट फिरतो, तो मोटरला असंतुलित करतो आणि तिचे आयुर्मान कमी करतो. एक डिझाइनर रनआउटचा टॉलरन्स निर्दिष्ट करून अशा वॉबल आणि असंतुलित फिरण्याच्या समस्येपासून मोटरचा बचाव करू शकतो.
रनआउट दोन प्रकारचे असतात. एक म्हणजे वर्तुळाकार रनआउट आणि एकंदर रनआउट.
अ. वर्तुळाकार रनआउट
परिभ्रमणाच्या अक्षाच्या लंबातील कोणत्याही सेक्शनवर मोजले असता मिळणारी इंडिकेटरची एकंदर हालचाल म्हणजे वर्तुळाकार रनआउट. 'O' रिंग ग्रूव्हच्या व्यासांकरिता वर्तुळाकार रनआउट टॉलरन्स बऱ्याचदा आवश्यक असतो.
वर्तुळाकार रनआउटचा अर्थ कसा लावायचा?
दंडगोलाकार पृष्ठभागाचा अरीय (रेडियल) दिशेतील, निर्देशक (इंडिकेटर) बाणाने दाखविलेला रनआउट, जेव्हा यंत्रभाग संदर्भ अक्षाच्या रेषेवर (चित्र क्र. 11) एकदा फिरविला जातो, तेव्हा संदर्भ अक्षाच्या लंबात असलेल्या कोणत्याही मापन प्रतलावर तो 0.03 मिमी.पेक्षा जास्त पुढे जाऊ नये. समकेंद्रियता तपासतात त्याच पद्धतीने रनआउट तपासतात. रनआउट म्हणजे केंद्ररेषेच्या अवतीभवती नॉमिनल फॉर्मचे विचलन, जे फॉर्म आणि स्थान दोन्ही नियंत्रित करते. समकेंद्रियता हा एकच केंद्र सामायिक करणाऱ्या दोन वस्तूंमधील व्युत्पन्न (डिराइव्हड) केंद्रबिंदू किंवा केंद्ररेषा आहे. यावर फॉर्म नियंत्रण नसते.
रनआउट कसा तपासावयाचा?
संदर्भ पृष्ठभागावर साध्या हाइट गेजचा वापर करून रनआउट मोजला जातो. सर्व संदर्भ बिंदू निश्चित करून आणि केंद्रीय संदर्भ अक्ष फिरवून संदर्भ अक्ष नियंत्रित केला जातो. ज्या संदर्भावर रनआउट नियंत्रित केला जाणे आवश्यक आहे, त्या प्रत्येक संदर्भावर यंत्रभाग सामान्यत: V ब्लॉक किंवा एका स्पिंडलद्वारे प्रतिबंधित केला जातो. नंतर यंत्रभाग त्या अक्षाभोवती फिरविला जातो आणि यंत्रभागाच्या पृष्ठभागाच्या लंबात ठेवलेल्या हाइट गेजचा वापर करून विचलन (चित्र क्र. 12) मोजले जाते. जोपर्यंत गेजवरील मूल्य रनआउट टॉलरन्सपेक्षा अधिक नसते, तोपर्यंत यंत्रभाग स्पेसिफिकेशनमध्ये असतो.
ब. एकंदर रनआउट
एकंदर रनआउट म्हणजे जेव्हा यंत्रभाग संदर्भ अक्षाभोवती 360° फिरविला जातो, तेव्हा संपूर्ण फीचर किंवा पृष्ठभाग यांच्यात डेटमच्या संदर्भात होणारे विचलन. एकंदर रनआउट, यंत्रभाग फिरविल्यामुळे होणारे पृष्ठभागातील आणि अक्षीय परिमाणातील विचलनाचे प्रमाण हे दोन्ही नियंत्रित करतो. अरीय आणि अक्षीय दोन्ही विचलने मोजली जातात आणि टॉलरन्समध्ये ठेवली जातात. अक्षांभोवती फिरत असताना संपूर्ण पृष्ठभाग स्पेसिफिकेशनमध्ये असणे ज्यात आवश्यक असते, अशा यंत्रभागांसाठी एकंदर रनआउट सहसा मोजला जातो. दंडगोलाच्या पृष्ठभागाचे टेपर रोखण्यासाठी हा खूप परिणामकारक असतो. जेव्हा एखादा यंत्रभाग फिरतो आणि त्याचा पृष्ठीय संपर्क मोठ्या प्रमाणात असतो, तेव्हा एकंदर रनआउट महत्त्वपूर्ण असू शकतो. एकंदर रनआउटमुळे वर्तुळाकार रनआउटच्या आवश्यकतांमध्ये अधिक सूक्ष्मता येते. मोठे पंप शाफ्ट, ट्रान्स्मिशन शाफ्ट आणि क्लिष्ट गिअर यासारख्या यंत्रभागांमध्ये एकंदर रनआउट वापरला जातो.
एकंदर रनआउटचा अर्थ कसा लावायचा?
जेव्हा यंत्रभाग संदर्भ अक्ष रेषेवर फिरविला जाईल, तेव्हा चित्र क्र. 13 मध्ये, निर्देशक बाणाने दाखविलेला, दंडगोलाकार पृष्ठभागाचा अरीय दिशेतील एकंदर रनआउट, दंडगोलाकार पृष्ठभागाच्या कोणत्याही बिंदूवर 0.03 मिमी.च्या पुढे जाऊ नये.
एकंदर रनआउट कसा तपासावयाचा?
तपासणीची पद्धत रनआउटप्रमाणेच आहे, परंतु येथे रनआउट अरीय आणि अक्षीय दोन्ही दिशांमध्ये तपासणे आवश्यक आहे. हे CMM वरदेखील तपासले जाऊ शकते.
वरील मूलभूत गोष्टी समजून घेतल्यावर आपल्याला GD&T च्या पुढील फायद्यांची जाणीव झाली असेल, अशी मला खात्री आहे.
· भौमितिक टॉलरन्सचा फायदा असा आहे की, त्याद्वारे डिझाइनरच्या मनातले डिझाइन अचूक आणि कार्यक्षमतेने व्यक्त केले जाते, जे नुसता आकार (साइझ) टॉलरन्स वापरून व्यक्त केले जाऊ शकत नाही.
· GD&T पद्धत वापरल्याने खर्च कमी होतो आणि गुणवत्ता, विश्वासार्हता आणि सुरक्षितता सुधारते, अॅसेम्ब्ली करण्यात सुलभता येते आणि अॅसेम्ब्ली सुरळीत चालते, हे सिद्ध झाले आहे.
· GD&T वापरल्याने अधिक विस्तृत टॉलरन्स श्रेणी लागू करता येते आणि फंक्शनल (कार्यशील) यंत्रभाग अस्वीकृत होण्याचे प्रमाण कमी होते.
बोनस टॉलरन्स हा आकाराच्या फीचरशी संलग्न भौमितिक नियंत्रणासाठी उपलब्ध असलेला अतिरिक्त टॉलरन्स आहे, ज्यात महत्तम मटेरियल कंडिशन (MMC) आणि लघुत्तम मटेरियल कंडिशन (LMC) सुधारक (मॉडीफायर) असतात. बोनस टॉलरन्सच्या मदतीने उत्पादनात आणखी बरेच फायदे होऊ शकतात, परंतु GD&T च्या मूलभूत गोष्टी वाचकांपर्यंत पोहोचविणे हा हेतू असल्यामुळे, आम्ही या लेखामध्ये त्यांचा समावेश केलेला नाही.
· GD&T ची चांगली अंमलबजावणी केल्यावर सांख्यिकी प्रक्रिया नियंत्रणसुद्धा (SPC) करता येते, ज्यामुळे उत्पाद अस्वीकृतीचा दर, अॅसेम्ब्ली अपयश आणि गुणवत्ता नियंत्रणासाठी लागणारे प्रयत्न कमी होतात आणि संस्थांच्या संसाधनांची भरपूर बचत होते. परिणामी, निरनिराळे विभाग समांतर कार्य करण्यास अधिक सक्षम होतात, कारण जे काही साध्य करावयाचे आहे, त्यासाठी त्यांच्याकडे एकच लक्ष्य आणि भाषा असते.
अशा प्रकारे, GD&T जटिल यंत्रणामध्ये महत्त्वाची भूमिका बजावते, उत्पादनात योग्य प्रमाणात टॉलरन्स ठेवण्याची परवानगी देऊन डिझाइनची अचूकता वाढविते. जे व्यवसाय GD&T चा शब्दशः आणि अर्थशः अवलंब करतील, त्यांना उत्पादनातील समस्या, रीवर्क आणि स्क्रॅप कमी केल्याने मोठा फायदा होईल.
खरे पाहता, GD&T च्या उत्क्रांतीचे वर्णन साधेपणापासून लवचिकतेच्या दिशेने हळूहळू झालेला बदल असे केले जाऊ शकते.