कोणत्याही उद्योगामध्ये जेव्हा शीट मेटलच्या कामामध्ये अधिक अचूकतेची आवश्यकता असते, तेव्हा ते काम लेझर कर्तनाद्वारेच ( laser cutting )करणे श्रेयस्कर ठरते. लेझर ही एक उष्णता (थर्मल) आधारित प्रक्रिया असूनही मूळ मटेरियलचे कमीतकमी विरूपण आणि मापांची अचूकता मिळविणे या प्रक्रियेत सहज शक्य होते. लेझर तंत्रज्ञानाचा प्रवास, प्रक्रिया, वापर यासह विविध गोष्टींवर सविस्तर भाष्य करणारा लेख.
सुमारे 60 च्या दशकाच्या सुरुवातीला धातूसाठी लेझर कटिंग तंत्रज्ञान वापरण्यास सुरुवात झाली. सुरुवातीला हळूहळू युरोपमध्ये त्याचा वापर वाढत गेला. आपल्याकडे 1983-84 च्या सुमारास इंदोरमध्ये एक मशीन आले, तर टेल्कोने 1984-85 च्या सुमारास प्रोटोटायपिंग उत्पादनासाठी एक मशीन खरेदी केले. तेथून खऱ्या अर्थाने भारतीय उद्योग क्षेत्रामध्ये लेझर तंत्रज्ञानाच्या वापराला सुरुवात झाली.
त्याकाळी वाहन निर्मितीमध्ये शीट मेटल कापून त्याचे अपेक्षित कच्चे आकार (ब्लँक) तयार करावे लागत. त्यानंतर त्याला योग्य आकार देऊन (फॉर्मिंग) अतिरिक्त मटेरियल कापावे (ट्रिमिंग) लागत असे. याची डाय करण्यासाठी बराच वेळ लागायचा. नमुना उत्पादासाठी (प्रोटोटाइप) ते परवडत नसे. म्हणून ते सर्व पत्रे हाताने कापले जायचे. काही प्रमाणात सॉफ्ट टूल विकसित करून फॉर्मिंग केले जायचे, पण त्याच्यानंतर जास्तीचे मटेरियल कापावे लागण्याची समस्या होतीच. म्हणूनच टेल्कोने त्यावेळी इंग्लंडमधील एका कंपनीकडून 3D लेझर कटिंग मशीन विकत घेतले. त्या मशीनमध्ये ब्लँकिंग, ट्रिमिंग अशा सर्व प्रक्रिया व्हायच्या.
मी टेल्कोमधील नोकरी सोडून माझा स्वतःचा कारखाना सुरू करताना काळाप्रमाणे सर्व गोष्टी नव्या असाव्यात, तंत्रज्ञान नवे असावे असा विचार केला. 3D लेझर मशीन खूप महाग असल्याने सर्व अभ्यास करून आम्ही फ्लॅट बेड 2D मशीन आणण्याचा विचार केला आणि ते मशीन (चित्र क्र. 1) आम्ही आयात केले.
त्यावेळी एका मोठ्या कंपनीच्या नवीन वाहनाच्या भागांचे ब्लँकिंग करण्याचे काम आम्हाला मिळाले. त्यावेळी 6 महिने प्रचंड मेहनत करून ते तंत्रज्ञान आम्ही सिद्ध केले. प्रोटोटाइपसाठी वापरल्या जाणाऱ्या या मशीनवर आम्ही मास प्रॉडक्शन केले. त्यावेळी परिस्थिती अशी होती की दारात ट्रक उभे असायचे, शेजारी मटेरियल पडलेले असायचे आणि आमचे मशीन सतत 24 तास चालू असायचे. त्यावेळी या मशीनमध्ये आम्ही ग्राहकाच्या गाडीच्या एका मॉडेलचे 75 प्रकारचे विविध भाग तयार करीत होतो. उदाहरणार्थ, आउटर डोअर पॅनेल, इनर डोअर पॅनेल, B पिलर, C पिलर, टेल गेट इनर, टेल गेट आउटर, लोअर पॅनेल, हूडचे इनर आणि आउटर पार्ट इत्यादी. साधारणतः प्रति महिना आम्ही प्रत्येकाचे 100 सेट केले. जवळजवळ 5 महिने आम्ही असे काम केले.
हळूहळू पुण्यात, मुंबईत आणि नंतर संपूर्ण देशात हे तंत्रज्ञान कुठे कुठे कशा पद्धतीने उपयुक्त ठरेल याचा अभ्यास केला. बऱ्याच बहुराष्ट्रीय कंपन्यांना हे तंत्रज्ञान तोपर्यंत माहिती झाले होते. त्यामुळे त्यांच्याकडे हे तंत्रज्ञान वापरण्याची आम्हाला लवकर संधी मिळाली. इतर तंत्रज्ञानाच्या तुलनेत लेझर तंत्रज्ञान अतिशय वेगाने प्रस्थापित होत गेले. कमी काळात त्याला भरपूर प्रसिद्धी मिळाली. आकाराने लहान यंत्रभाग, प्रोटोटाइप याकरिता लेझर तंत्रज्ञानाची सुरुवात झाली होती.
लेझर प्रक्रिया
लेझर ही एक उष्णता आधारित (थर्मल) प्रक्रिया आहे. गॅस कटिंग असो किंवा प्लाझ्मा कटिंग असो, कोणताही भाग कापल्यावर त्याठिकाणी एक 'हीट अफेक्टेड झोन' तयार होतो, ज्याचा नंतर फॉर्मिंगमध्ये एखाद्या वेळेस त्रास होऊ शकतो. धातू थोडाफार कठीण (हार्ड) होऊ शकतो. पण लेझर प्रक्रियेचा फायदा असा आहे की, त्याचे हीट अफेक्टेड झोन इतके कमी (मिनिमल) आहेत की, त्यामुळे मटेरियलचे गुणधर्म (प्रॉपर्टी) अजिबात बदलत नाहीत. साधारणतः 4-5 मिमी. जाडीचे शीट असेल, तर लेझरने कापल्यावर मिळणारा हीट अफेक्टेड झोन 0.25 मिमी. रुंद असतो. प्लाझ्मा कटिंगने काम केल्यास हाच झोन सुमारे 5 ते 7 मिमी., तर गॅस कटिंगमध्ये तो 10 ते 15 मिमी. रुंद असतो. लेझर प्रक्रिया ही थंड कापाइतकीच उत्कृष्ट ठरते. लेझर प्रक्रियेदरम्यान बर निर्मिती होत नाही. ब्लँकिंग डाय वापरून तयार झालेल्या भागांची अचूकता आणि लेझरमधून मिळणारी अचूकता सारखीच असते. लेझरद्वारे 1 मीटरमध्ये ± 0.25 मिमी. इतकी अचूकता मिळते. गॅस कटिंग किंवा प्लाझ्मा कटिंग केले तर, 1 मीटरमध्ये ± 2 मिमी. इतकी अचूकता मिळते. लेझर झोत त्याचा ठरविलेला मार्ग सोडून जात नाही. त्यामुळे यंत्रभागाच्या मापांमध्ये सातत्य राखले जाते. प्लाझ्मा कटिंगमध्ये मटेरियल जास्त प्रमाणात जळते त्यामुळे लेझरच्या तुलनेत त्याची अचूकता कमी असते. प्लाझ्मा कटिंगमध्ये मटेरियल कापले जाताना त्याच्या कडेवर (एज) टेपर येतो. टेपरचे प्रमाण लेझरमध्ये कमी असते. 15 मिमी. जाडीचे मटेरियल लेझरने कापले तर टेपर 1 मिमी. मध्ये असतो. तेच जर प्लाझ्माद्वारे कर्तन केले, तर साधारणतः 4 मिमी. पर्यंत टेपर जाऊ शकतो. काही यंत्रभागांचे टॉलरन्स, गॅस आणि प्लाझ्मा कटिंगवरून साध्य होत नाहीत म्हणून ते लेझरनेच करावे लागतात.
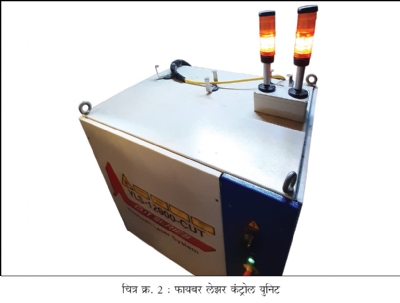
लेझर दोन प्रकारचे असतात. एक म्हणजे CO2 लेझर, जो गॅसमधून तयार होतो. दुसरा म्हणजे फायबर लेझर, जो सॉलिड मटेरियलमधून तयार होतो. CO2 लेझरच्या तुलनेत फायबर लेझर मशीन खूपच आटोपशीर (चित्र क्र. 2) असते.
मटेरियल
लेझर कर्तनासाठी वापरले जाणारे मटेरियल विशिष्ट दर्जाचे असणे गरजेचे असते. प्राथमिक गरज म्हणजे त्याच्यावर व्यवस्थित उष्णतोपचार (हीट ट्रीटमेंट) करून त्याच्यातील ताण (स्ट्रेस) पूर्णपणे काढून टाकले गेले असले पाहिजेत. अन्यथा मटेरियल कापल्यानंतर तेथील ताण निघून जाऊन तिथे विरूपण (डिस्टॉर्शन) येण्याची शक्यता असते. कमी जाडीच्या किंवा पातळ (थिन) मटेरियलला ही शक्यता अधिक असते. सगळ्या प्रकारच्या मटेरियलला ही समस्या येत नाही. साधारणतः कोल्ड रोल्ड (CR) मटेरियलला ट्रीटमेंट चांगली असल्यामुळे समस्या येत नाही. हॉट रोल्ड (HR) मटेरियलला समस्या येते. 5-12 मिमी. जाडीच्या मटेरियलला जास्त समस्या येते. स्टेनलेस स्टीलमध्ये कमी समस्या येते, कारण स्टेनलेस स्टील बनविण्याची प्रक्रियाच चांगली आहे. वाहन उद्योगातील बऱ्यापैकी यंत्रभाग किंवा बॉडी या 0.8, 1, 1.2 मिमी. जाडीच्या असतात. त्याला ही समस्या नसते. याच्यापेक्षा जाड मटेरियल असेल तर समस्या येतात.
सुरुवातीला अशा समस्या आल्यानंतर आम्ही जर्मनीतील एका कंपनीकडे विचारणा केली होती. त्यावेळी त्यांनी त्यांच्याकडे अशी विरूपणाची समस्या नसल्याचे सांगितले. त्यानंतर आमच्या असे लक्षात आले की, त्यांच्याकडील मटेरियल उच्च दर्जाचे उष्णतोपचार करून ताणरहित केलेले असते. या संदर्भात जिंदाल किंवा इतर स्टील उत्पादक बहुराष्ट्रीय कंपन्यांबरोबरदेखील आम्ही चर्चा करीत होतो. त्यांना आम्ही 'लेझरेबल' मटेरियल देण्याविषयी विचारणा केली. कारण युरोपमध्ये तशा तऱ्हेचे मटेरियल वापरले जात होते. काही काळ प्रयत्न केल्यानंतर आपल्याकडील स्टील उत्पादकांनी आवश्यक त्या सर्व प्रक्रिया विकसित करून 'लेझरेबल' मटेरियल पुरविण्यास सुरुवात केली.
आम्ही स्टीलचे कर्तन जास्तीतजास्त करतो. ब्रास, स्टेनलेस स्टील यासाठी लेझर वापरता येते. कॉपर, अॅल्युमिनिअमही कापता येते, परंतु अॅल्युमिनिअम कापायला लेझरला अवघड जाते. याची प्रमुख दोन कारणे आहेत. एक म्हणजे त्या मटेरियलची परावर्तनक्षमता (रिफ्लेक्टिव्हिटी). लेझर, प्रकाशकिरणांचा झोत असल्याने तो परावर्तित (रिफ्लेक्ट) होतो. दुसरी गोष्ट म्हणजे कॉपर आणि अॅल्युमिनिअममध्ये उष्णतावहन खूप वेगाने होते. त्यामुळे हे धातू कापताना अधिक उष्णता लागते. ज्या लेझर पॉवरने 20 मिमी. स्टेनलेस स्टील कापता येते तिथे फक्त 5 मिमी. अॅल्युमिनिअम कापणे शक्य होते. अधातूसुद्धा (नॉन मेटल) लेझरने कापता येतात, पण यामध्ये मोठी समस्या अशी असते की, हे अधातू कापताना त्यामध्ये घातक वाफा (टॉक्सिक फ्यूम) तयार होतात. अशा ठिकाणी चांगल्या दर्जाची एक्झॉस्ट यंत्रणा असणे गरजेचे असते. ती मोठ्या प्रमाणात वापरावी लागते.
मशीनच्या क्षमता
आम्ही 1994 मध्ये पहिले मशीन आणले तेव्हा, त्या मशीनद्वारे आम्ही 10 मिमी. पर्यंत धातू कापू शकत होतो. आज आमच्याकडे असलेल्या मशीनद्वारे आम्ही 25 मिमी. पर्यंत जाडीचा धातू कापू शकतो.
मशीनच्या क्षमतेनुसार त्यामध्ये 8 मिमी. पासून ते 20 मिमी. जाडीपर्यंत मटेरियल कापता येते, पण त्याची अचूकता मशीन उत्पादकाने दिलेल्या मर्यादांनुसार मिळू शकते. हल्ली उपलब्ध असलेल्या मशीन 1 मी. X 1 मी. पासून ते 2.5 मी. X 16 मी. पर्यंत कोणत्याही आकाराचे बेड असलेल्या असू शकतात. तसेच लेझरची पॉवर हाही पॅरामीटर महत्त्वाचा आहे. इंडस्ट्रीसाठी साधारणतः 1 kW पासून ते 12 kW पर्यंत शक्ती असलेल्या मशीन वापरतात. 1 kW चे मशीन, 5 मिमी. पर्यंत मटेरियल कापते, तर 12 kW चे मशीन 35 ते 40 मिमी. पर्यंतचे मटेरियल कापते. साधारणतः 1 मी. X 1 मी. हे मशीन जास्त अचूक असते. मशीन जितके मोठे, तेवढी त्याची अचूकता तुलनेने कमी होत जाते.
लेझर प्रक्रियेमध्ये 4 गोष्टी असतात. एक म्हणजे मापांची अचूकता, दुसरी म्हणजे कापाचा फिनिश आणि तिसरी गोष्ट म्हणजे टेपर आणि चौथी विरूपण. लेझर प्रक्रियेमध्ये हीट अफेक्टेड झोन कमी असल्यामुळे मटेरियलचे विरूपण कमीतकमी होते. लेझर प्रक्रियेमध्ये सहसा टेपर येत नाही, पण मटेरियल जर जास्त जाडीचे असेल, तर त्याला थोड्याफार प्रमाणात टेपर येतो. अतिशय सूक्ष्म झोत वापरून मटेरियल कापले जात असल्याने अचूकता आणि फिनिश उत्तम मिळतो.
विविध उपयोग
लेझर तंत्रज्ञान हे प्रामुख्याने प्रोटोटायपिंगसाठी उदयास आले होते. विविध क्षेत्रामधील विविध अॅप्लिकेशननुसार (चित्र क्र. 3, 4 आणि 5) त्याचा अवलंब केला गेला. आपल्याकडील उद्योग बऱ्यापैकी कस्टमायझेशनकडे वळला आहे. कमी बॅच साइझ क्वांटिटी उत्पादनाकडे आपले उद्योग झुकत चाललेले आहेत. प्रेसिंग कामामध्ये कस्टमायझेशन होत नसल्यामुळे लेझरचा वापर वाढण्याकडे कल आहे. कारण प्रत्येक लॉट हा वेगवेगळा पाहिजे. त्यासाठी मशीन फ्लेक्झिबल असणे आवश्यक आहे. त्यामध्ये कारखानदाराला असंख्य प्रकारचे प्रयोग करता येतात, केवळ यंत्रभागाचे डिझाइन व्यवस्थित होणे अपेक्षित असते. वाहन उद्योग सोडून इतर कोणत्याही उद्योगामध्ये जर शीट मेटलची आवश्यकता असेल, तर त्याच्यावरील काम लेझर कर्तनाद्वारेच केले जाते.
बरेच कारखानदार प्लाझ्मा कटिंग किंवा गॅस कटिंगऐवजी लेझरच्या उपयोगाकडे वळलेले दिसतात. त्याचे कारण असे आहे की, लेझर या प्रक्रियेचा खर्च काळानुसार बऱ्यापैकी कमी झालेला आहे. गॅस कटिंगपेक्षा हे आधी बऱ्याच पटीने महाग होते. जसजसे तंत्रज्ञान विकसित व्हायला लागले, तसतसा त्याच्या वापराचा खर्च कमी होत गेला.
प्रोटोटायपिंग आणि स्मॉल बॅच क्वांटिटीसाठी लेझर तंत्रज्ञानाची सुरुवात झाली. परंतु काळानुरूप लेझर तंत्रज्ञानात बदल झाले आणि आता आज लेझर हे प्रॉडक्शन टूल म्हणून प्रचलित होताना दिसत आहे.
गॅस कट ही खूप वेळखाऊ प्रक्रिया असल्याचे लक्षात आले आहे, कारण प्रत्यक्ष कर्तन झाल्यानंतर फिनिशिंगसाठी त्याच्यावर खूप प्रक्रिया कराव्या लागतात. मात्र लेझर प्रक्रियेनंतर त्याच्यावर कुठलीही प्रक्रिया केली जात नाही. हा लेझर प्रक्रियेचा मोठा फायदा आहे. त्याच्यावर नंतर डीबरिंग करायची गरज नसते. चित्र क्र. 5 मध्ये दाखविलेला भाग कापण्यासाठी लेझर वापरल्याने त्याला लागणारा वेळ आणि खर्च कमी झाला.
उदाहरण
आमच्याकडे आम्ही स्लायडर (चित्र क्र. 6) नावाचा एक यंत्रभाग तयार करतो. त्याचा उत्पादन खर्च ग्राहकाला कमी करावयाचा होता. त्यासाठी ग्राहकाने सुरुवातीपासूनच म्हणजे डिझाइनपासूनच आमच्याशी चर्चा केली होती. या स्लायडरची अॅसेम्ब्ली खूप किचकट असून पूर्वी त्याचे फॅब्रिकेशन झाल्यानंतर बरेचसे यंत्रण केले जात होते आणि हाच त्याचा खर्चिक भाग होता. चर्चा केल्यानंतर असे लक्षात आले की, आपण तेच काम कमी करू शकतो का किंवा फॅब्रिकेशननंतर जे यंत्रण केले जाते आहे ते टाळू शकतो का? त्यामध्ये सर्वात मोठी समस्या विरूपणाची असते. मटेरियल कापणे, मटेरियल वाकविणे (बेंड) आणि नंतर ते मटेरियल वेल्ड करणे या प्रत्येक ठिकाणी विरूपण येत असते. हे विरूपण कमी कसे करावयाचे हे आव्हान होते. यासाठी सर्वात प्रथम मटेरियल चांगल्या दर्जाचे असले पाहिजे, मटेरियलचा सपाटपणा उत्कृष्ट असला पाहिजे. पूर्वी गॅस कटिंग किंवा प्लाझ्मा कटिंग करून मटेरियल कापले जायचे. त्याच्याऐवजी आम्ही लेझर प्रक्रियेचा समावेश केला. त्यामुळे कमीतकमी हीट अॅफेक्टेड झोन होतात आणि अगदी कमीतकमी विरूपण होते.
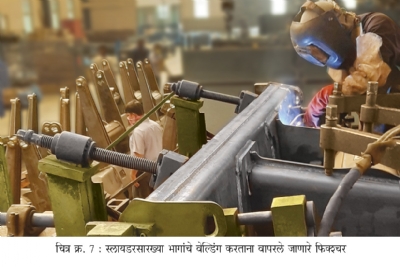
हा यंत्रभाग अरुंद आणि लांब आहे. यंत्रभाग जेवढा लांब आणि अरुंद, तेवढी त्यामध्ये विरूपणाची शक्यता अधिक असते. त्यामुळे लेझरद्वारे प्रक्रिया करून त्याचे पॅरामीटर अशा पद्धतीने स्थापित केले की, त्याचे कमीतकमी विरूपण होईल. सी.एन.सी. बेंडिंग मशीनवर बेंडिंग केले. यामुळे बेंडिंगनंतरच्या अचूकता अपेक्षेनुसार मिळतात. ± 30 मिनिट्स टॉलरन्समध्ये त्याचे बेंडिंग होते. या यंत्रभागामध्ये बरीच भोके आहेत आणि त्याला वेगवेगळ्या ठिकाणी बुश वेल्ड केलेले आहेत. लेझरमुळे प्रत्येक भोकाचे संदर्भ केंद्रांतर (सेंटर डिस्टन्स) अतिशय अचूकपणे नियंत्रित करता आले. बुशमधील अंतरे 0.5 मिमी. मध्ये नियंत्रित (फॅब्रिकेशननंतर) झाली. कमीतकमी विरूपण, अचूक केंद्रांतर आणि भोकाची अचूकता या तिन्ही गोष्टी नियंत्रित झाल्या. सी.एन.सी. बेंडिंग प्रक्रियेमुळे बेंडिंगच्या अचूकतेमध्ये सातत्य राखता आले. या यंत्रभागासाठी आम्ही काही फिक्श्चर (चित्र क्र. 7) तयार केले. त्यामुळे त्याच्यावर वेल्डिंग करताना कार्यवस्तू योग्य पोझिशनमध्ये घेणे साध्य झाले. वेल्डिंगनंतर होणारे विरूपण टाळण्यासाठी आम्ही वेल्डिंगचा क्रम निश्चित केला. एक भाग वेल्ड केल्यानंतर दुसरा भाग वेल्ड करण्यापूर्वी तो थंड होण्यासाठी त्याला मधून मधून ठराविक वेळ थांबावे लागते. अशाप्रकारे तो संपूर्ण यंत्रभाग करण्याची प्रक्रिया निश्चित केली आणि त्यानंतर हे सिद्ध झाले की, यंत्रणाशिवायसुद्धा हा यंत्रभाग तयार करता येऊ शकतो. या यंत्रभागाच्या आतमध्ये 2 फ्लॅट वेल्ड केलेले आहेत. त्यांच्यामध्ये एक तिसरा यंत्रभाग सरकत (स्लाइड) जातो. म्हणून त्याला स्लाइडर किंवा कॅरिअर असे नाव दिलेले आहे. या सर्व गोष्टी प्रक्रिया सुधारणेतून आणि डिझाइनमध्ये काही बदल करून केल्या. उदाहरणार्थ, काही ठिकाणी जाडी वाढवावी लागली, वेल्डिंग कुठे टाळता येईल याची काळजी घेतली, अशा सर्व सुधारणा करत त्या यंत्रभागामध्ये जवळपास 20% आर्थिक बचत झाली. ही प्रक्रिया आम्ही या यंत्रभागावर आधी स्थापित केली आणि त्यानंतर इतर अनेक यंत्रभागांसाठी ती वापरीत आहोत. या सर्व प्रक्रियेमध्ये कुठेही हीट ट्रीटमेंट किंवा स्ट्रेस रीलिव्हिंग या प्रक्रियांचा समावेश केलेला नाही. कोणतेही यंत्रण न करता लेझर प्रक्रिया आणि वेल्डिंग करून ती अॅसेम्ब्ली आम्ही तयार केली.
सुरक्षित वापर
लेझरची हाताळणी योग्य पद्धतीने न केल्यास ते अतिशय घातक टूल ठरू शकते. कारण लेझर डोळ्यांना दिसत नाहीत, त्यांची पॉवर खूप जास्त असते. जे लेझर आपल्या डोळ्यांना दिसतात त्याची पॉवर 1 किंवा 2 वॅट अशी असते. आज आमच्याकडील मशीन हे 12, 000 वॅटचे मशीन आहे. लेझरच्या बाबतीमध्ये आणखी एक बाब अशी असते की, लेझर नेहमी एका सरळ रेषेमध्ये कितीही अंतरापर्यंत जाऊ शकतात. त्यांची तीव्रता कमी होत नाही. लेझरचे गुणधर्म बदलत नाहीत. ते स्थिर राहतात. त्यामुळे ही प्रक्रिया खूप जास्त सातत्यपूर्ण मानली जाते. त्यामुळे लेझर मशीनमध्ये सुरक्षिततेसाठी सर्व आवश्यक वैशिष्ट्ये अंतर्भूत केलेली असतात. लेझर मशीनच्या बाहेरच्या बाजूला फ्लेक्सी ग्लास नावाची विशेष काच असलेल्या भिंती (चित्र क्र. 8) असतात. या काचेमुळे लेझर बीम अशा पद्धतीने विरूपित होतो की, त्यामध्ये तेवढी तीव्रता (इंटेन्सिटी) रहात नाही.
लेझर झोत कोणत्याही एका जागेवर स्थिर ठेवू शकत नाही. तो सातत्याने फिरता असावा लागतो. जर समजा लेझर झोत एका जागी स्थिर ठेवला तर त्या बिंदूच्या खालील कार्यवस्तूवरोबरच इतर सर्व मटेरियलदेखील खराब होते.
लेझरचा हेड आणि कार्यवस्तूमधील अंतर ही खूप महत्त्वाची बाब आहे. कर्तन होणार आहे किंवा नाही, होणार असेल तर त्याची गुणवत्ता कोणत्या दर्जाची असणार आहे, हे सर्व त्या अंतरावर अवलंबून असते. त्यामुळे ते अंतर सातत्याने कायम राखण्यासाठी मशीनमध्ये उच्च प्रतीचे इलेक्ट्रॉनिक संवेदक (सेन्सर) तंत्र अंतर्भूत केलेले असते. उदाहरणार्थ 2 मिमी. अंतर ठेवायचे असेल तर संपूर्ण प्रक्रियेदरम्यान तेवढेच अंतर राखले जाते.
मोठ्या शीटमधून विविध आकाराचे भाग कापावयाचे असतील तेव्हा नेस्टिंग तंत्र (चित्र क्र. 9) वापरले जाते. विविध आकारांचे भाग एकाच प्लेटमधून कापण्यासाठी त्याची विशिष्ट रचना करून आराखडा तयार केल्याने कमीतकमी मटेरियल वाया जाते. तिथे काही विशिष्ट टेस्टर असतात. दोन लगतच्या भागांमधील काप राखण्यासाठी ते वापरले जातात. दोन कापाच्यामध्ये एक विशिष्ट जागा सोडावी लागते. तेदेखील मटेरियलच्या जाडीवर अवलंबून असते. सर्व मोजमापे करून एक सीमारेषा आखली जाते. त्याच्याबाहेरील मटेरियल वाया जाते.
आर्थिक बाबी
खर्चाच्या दृष्टिकोणातून, गॅस कटिंग मशीन आणि लेझर कटिंग मशीन यामध्ये तुलना केली तर, लेझर कटिंग मशीन 8-10 पटीने महाग असतात. त्याचा प्रक्रिया खर्च 4 पट असतो. जिथे गॅस कटिंगने केलेले काम चालते, तिथे अर्थातच लेझर परवडू शकत नाही. जरी लेझरच्या किंमती कमी झाल्या असल्या, तरी ही प्रक्रिया तशी महाग ठरते. हे केवळ मशीनच्याच संदर्भात नाही तर त्याचे सर्व कन्ज्युमेबल वगैरे सर्व गोष्टीसुद्धा महाग असतात. परंतु एकंदर उत्पादकता आणि गुणवत्तेच्या दृष्टिकोनातून जर पाहिले तर या किंमती कमी ठरतात. तसेच लेझरमुळे कमी होणारा उत्पादन खर्च हा फरक भरून काढतो. तसेच कर्तनानंतर कराव्या लागणाऱ्या प्रक्रिया नसल्यामुळे त्यासाठी लागणारा खर्च वाचतो. त्यामुळेच लेझर कमी वेळात इतके प्रसिद्ध झाले आहे. कामाचा वेळ कमी करण्यासाठी ही प्रक्रिया खूपच प्रभावी आहे.
जेव्हा एखादा यंत्रभाग डिझाइन होत असतो तेव्हाच तो लेझर प्रक्रियेने करावयाचा आहे हे सुरुवातीलाच ठरवावे लागते आणि त्यानुसार डिझाइनमध्येच आवश्यक ती सर्व वैशिष्ट्ये अंतर्भूत करावी लागतात. एकूणच वेगवान आणि अचूक उत्पादनासाठी लेझर प्रक्रिया प्रभावी ठरते यात काही शंका नाही.